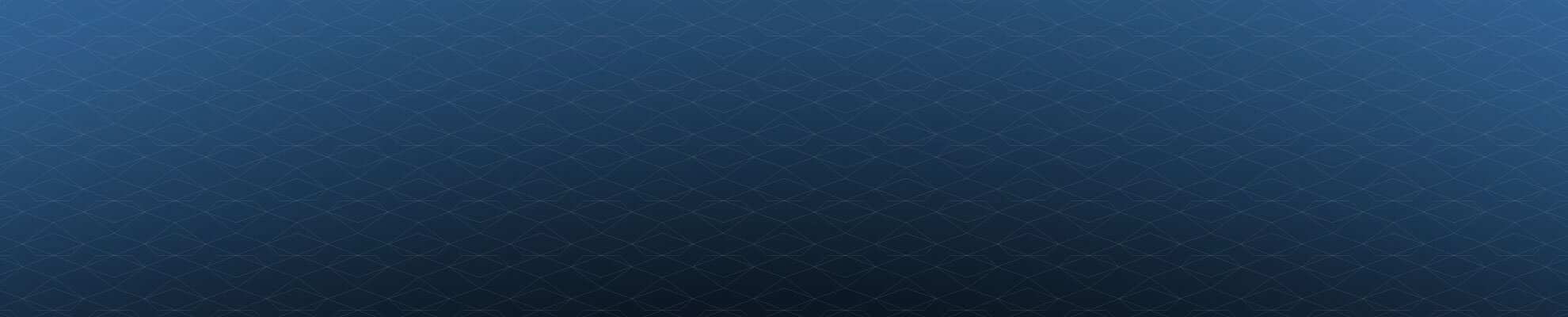
News and Resources
Browse by Category
Browse by Product
- All Dressing Products
- All Grinding Products
- CBN-Diamond Superabrasives
- Conventional Abrasives
- Diamond Lapping Compounds
- Diamond Rotary Dressers
- Diamond Stationary Dressers
- Hybrid Bond Grinding Tools
- Metal Bond Grinding Tools
- Plated Grinding Tools
- Resin Bond Grinding Tools
- Vitrified Bond Grinding Tools
True Blue Performance in Conventional Grinding
CDT demonstrated Blue Moon TZ wheels from Krebs & Riedel on the Studer S33. Learn how these grinding wheels improve form retention, power use, and grind quality.
When you’re looking for ways to improve grinding performance, the ultimate factor comes down to value: how can you get the precision and efficiency you need while managing costs? That’s where advanced conventional abrasives often excel.
With certain applications, classic abrasives like silicon carbide and aluminum oxide deliver strong results at a lower upfront investment compared to superabrasives. For shops that don’t require the extreme speeds or precision of diamond and CBN, conventional wheels remain a smart, cost-effective choice.
While these wheels haven’t changed much in a hundred years, a few innovators are pushing the boundaries with scientifically engineered abrasive grains. One next-generation solution is the Blue Moon™ TZ high-performance grinding wheel from Krebs & Riedel, designed to bring greater efficiency, precision, and consistency to your process. Watch this video or read the following article to learn more.
Features and Benefits of Blue Moon™ TZ
Continental Diamond Tool is proud to bring to its customers the Blue Moon™ TZ, which represents the next evolution in the Blue Moon product line developed by the R&D team at Krebs & Riedel. This conventional grinding wheel incorporates a precision-shaped trapezoid abrasive grain that delivers maximum performance through high cutting efficiency, low thermal load, and outstanding profile retention.
Designed to perform under long contact lengths and demanding applications, the Blue Moon TZ offers:
Very low risk of overheating while grinding
High removal rates leading to short grinding times
Self-sharpening abrasive grain for consistent performance
Extended dressing intervals for improved wheel life
Reduced cost per unit through higher efficiency
Applications range from deep pass and centerless grinding to raceway and profile grinding of large gear modules. It is a versatile solution across aerospace, automotive, agricultural engineering, wind energy, hydraulics, and bearing production.
Blue Moon TZ’s Proven Performance
At the United Grinding Precision Summit in July 2025, Continental Diamond Tool was happy to bring this innovative wheel technology to the North American market. During a live demonstration on the Studer S33 cylindrical grinder, the Blue Moon™ TZ wheel was put to the test on steel specimens commonly used for tensile strength testing. This setup allowed attendees to see first-hand how the wheel handles demanding applications such as thread grinding where precise form and surface finish are critical. As the S33 shaped these test specimens, the Blue Moon™ TZ delivered stable performance with reduced heat build-up, extended form retention, and consistent results over long grinding passes.
At the event, CDT Senior Application Engineer Paul Christy shared his perspective on why this technology stands out:
“The Precision Summit has been exciting. Many people have been asking questions, and we’ve had some great customer engagement,” says Paul. “We’re running Blue Moon technology. It has a ceramic-shaped grain, specifically formulated for the steel grinding that they were doing here.”
During his presentation, Paul emphasized that the benefits translate directly to shop-floor productivity:
“The Blue Moon technology gives us lower power consumption and better form retention. In this application, where we’re holding thread forms, the wheel provides excellent life and the consistent form retention required to grind threads.”
The Practical Advantage of conventional abrasive grinding wheels
For many manufacturers, conventional abrasives like the Blue Moon™ TZ offer a cost-effective solution with impressive productivity gains. Grinding shops benefit from high removal rates, reduced thermal load, and extended dressing intervals, all of which help shorten cycle times and improve efficiency.
At CDT, we work with customers to match the right wheel to the right process. While superabrasive wheels made of diamond or CBN deliver the highest levels of performance and longevity, there are certain applications where the cost-per-part savings of superabrasives don’t fully materialize. In these cases, conventional options like the Blue Moon™ TZ strike the right balance between performance and upfront investment.
With lower power consumption, reliable form retention, and strong economic efficiency, the Blue Moon™ TZ demonstrates just how far conventional abrasives have advanced. For applications from raceway grinding to large gear profiles, it’s a proven solution that helps manufacturers achieve results while managing costs.
See us Live at Motion + Power 2025
Manufacturers looking to explore the benefits of advanced conventional abrasives will have the opportunity to see CDT’s solutions first-hand at Motion + Power Technology Expo 2025. This event marks our first major showcase of Krebs & Riedel products since becoming their exclusive North American partner, as well as our public debut in the gear grinding market. On display will be the Blue Moon™ TZ alongside other Krebs & Riedel products and CDT’s Vitrified CBN wheels and Diamond Rotary Dressers, giving attendees a chance to see the full range of solutions we provide for gear and precision grinding applications.
Join us at Motion + Power 2025 to talk with our engineering team, see how our investment in the Burri PM550T enables precise custom profiling, and learn how CDT is helping manufacturers achieve faster turnaround, consistent results, and better overall grinding performance.
our Commitment to Excellence
At Continental Diamond Tool, we’re committed to helping customers choose the best abrasive solution—whether it’s conventional wheels like the Blue Moon™ TZ or our world-leading superabrasives—so you get the right balance of performance, precision, and long-term value.
We take pride in delivering not only advanced products but also outstanding customer service. Reach out by phone, email, or web form to learn how Blue Moon™ TZ can support your process. Contact us today.
CDT’s £4 million move in Wales sparks jobs boom and global growth
Continental Diamond Tool’s Kinmel Bay team moves into a new facility triple the size, boosting capacity for plated products.
Continental Diamond Tool in North Wales is celebrating a major transformation after moving to a purpose-built facility — unlocking massive growth potential and creating dozens of new jobs.
CDT has successfully relocated to a new 30,000 sq ft factory in Kinmel Bay after what managers described as a “logistical challenge on par with a military operation.”
The operation involved transporting more than 100 metric tonnes of machinery and equipment to the new base that’s nearly three times the size of its old premises less than half a mile away on the Tir Llwyd Industrial Estate.
The move is part of a £4 million expansion by the company which custom engineers ultra-precise industrial tooling for the aerospace, automotive and oil and gas sectors. Blue chip customers include Rolls Royce, Airbus and Tenneco.
Originally established as Consort Precision Diamond in 1984, the company was acquired and rebranded by American-owned Continental Diamond Tool in 2018.
Production Manager Justin Hughes, whose father, Peter, was a founding member of the business, said the move marks the beginning of an exciting new chapter for the company.
“There is a new ambition along with the investment,” said Justin, who has worked at CDT for 18 years. “The future is bright.”
The relocation was carried out with precise planning to minimise disruption, with some production lines back in operation in less than a week.
“In three days they had transported pretty much all the machinery out of the old factory into the new one,” he said. “Production was down for a maximum of two weeks for certain products, but for others the down time was less than a week.”
The company brought in help from key suppliers, including Mills CNC, and received support from CDT’s American owners, who have overseen multiple factory expansions in the United States.
“We had help from one of our American colleagues, facility manager Mike Moehring, who even brought forward his exit flight because it had gone so smoothly,” said Justin.
“This isn’t the company’s first rodeo. They’ve helped us get things right the first time — and that’s been absolutely invaluable.”
With 46 staff currently on site, the company now plans to grow the workforce to around 80 employees over the next two years, with a major recruitment and investment push underway — particularly in the electro-plating department.
“We could only fit 14 electro-plating tanks in our old premises,” Justin explained. “Here we can accommodate up to 200. It’s the perfect environment – less humid, well-ventilated, and much more comfortable for staff.”
CDT is investing £500,000 in new equipment, and the improved capacity is already paying off.
International orders are growing and the company now has the ability to manufacture five times as many large parts per day and thousands of small parts per week, many destined for the oil and gas industry.
“We used to have to turn away orders because we just didn’t have the capacity,” said Justin. “Now we can meet that demand — and electro-plated products are on course to become the biggest part of our business.”
The company is also expanding into Poland, which Justin describes as a “manufacturing powerhouse.”
The new facility has been designed with staff welfare in mind, with a new canteen and bright, modern working conditions aimed at both retaining current staff and attracting new recruits.
“It feels like we’ve moved out of the dark ages into the 21st century,” he added. “We’ve always been capable — now we have the tools and the space to reach our full potential.”
Among the longest-serving staff is Joe Bowles, 35, from Rhyl, who began his career as an apprentice and is now CDT’s Grinding Supervisor.
“The company has grown bigger but it still feels like a family,” said Joe. “The American owners have put real money into the business and upgraded our machines – it’s a huge vote of confidence in the Kinmel Bay operation.”
Joe, a third-generation engineer, takes pride in the firm’s commitment to quality.
“Everything is inspected two or three times. Our tolerances are normally within 10 microns – a red blood cell is five microns – and sometimes we work to just a single micron. That’s how precise we are.”
For newer members of the team, the relocation was seamless. Nori Aknai, 38, originally from Hungary and now living in Rhyl, joined CDT three months ago as a finance assistant.
“I really do like it here,” she said. “The move was huge but it went incredibly smoothly. Literally, we were working in the old place one day and the following morning we came here and everything was working. The fact that it’s a growing company means it’s an exciting place to work.”
Now firmly settled in their new home, CDT is looking to the future with optimism.
“I’m very proud of what we have achieved,” said Justin. “We’ve laid the foundations to do something really special here in Kinmel Bay.”
Continental Diamond Tool Limited (CDT Ltd.), based in Kinmel Bay, Rhyl, U.K., is the European subsidiary of Continental Diamond Tool Corporation, headquartered in New Haven, Indiana, U.S.A. For more than 40 years, CDT Ltd. has been a leader in diamond rotary dresser technology, originally operating as Consort Precision Diamond. Since joining CDT, the company has expanded its product line, delivering high-performance diamond plated grinding wheels and other premium superabrasive products to customers worldwide.
Precision Grinding for the Semiconductor Industry
CDT’s custom wheels help grinding shops meet tight specs, reduce downtime, and machine tough materials for the components needed to make semiconductors.
From smartphones to satellites, semiconductors power modern life. But behind every microchip are precision equipment, advanced materials, and skilled technicians that make high-volume chip production possible.
For machining shops that support the semiconductor industry, quality is non-negotiable. These manufacturers play a key role in producing wafer chucks, dicing tool components, and structural parts that keep chip production running at scale. These components must hold tight tolerances and perform in high-heat, high-vacuum, and chemically aggressive environments.
At Continental Diamond Tool (CDT), our role is simple: support the grinding operations that keep this work moving. We manufacture superabrasive grinding wheels that hold spec, reduce downtime, and deliver consistent quality.
Pandemic Pressures on Semiconductor Production
The global chip shortage that began in 2020 wasn’t just a blip—it was a wake-up call. When demand for electronics surged and supply chains fell behind, everything from automotive production to medical device manufacturing slowed down.
What caused it?
Demand for electronics and cloud infrastructure spiked
Fabs, packaging plants, and ports were shut down
Capacity for advanced chips was limited and concentrated in a few regions
Some sectors canceled orders early and were left scrambling when demand came back
This perfect storm exposed just how fragile the semiconductor supply chain had become.
Semiconductors, Five Years Later: What’s Changed?
Since then, major investments have poured into rebuilding and expanding semiconductor capacity:
The CHIPS and Science Act is supporting new fabs in the United States, including Ohio, Arizona, and New York
Foundries like TSMC and Samsung are expanding beyond Asia to reduce geopolitical risk
Automakers have jumped into chip development and procurement to secure their own supply
Meanwhile, demand keeps rising—especially with the growth of AI and cloud computing. AI workloads from machine learning, real-time analytics, and generative models require advanced chips, high-bandwidth memory, and complex packaging. That demand has cascaded across industries—from data centers and robotics to autonomous vehicles and healthcare.
Meeting that demand isn’t just about making more chips. It also means meeting tighter tolerances, ensuring reliability, and reducing variation across the supply chain. While new fabs are coming online, other parts of the process—like grinding and machining—are just as critical.
Grinding shops produce the wafers, tooling, and support components that make high-performance chipmaking possible. At CDT, we manufacture grinding wheels that are built for the job.
Precision Grinding: The Quiet Backbone of Semiconductor Manufacturing
Semiconductor fabs require tools made from tough materials like tool steels, ceramics, carbides, and coated alloys. Materials are selected for their strength, stability, and ability to handle heat and wear, but that also makes them challenging to machine.
Our customers specialize in grinding tight-tolerance components using surface, OD, and ID grinding. In the semiconductor industry, this often means working at the micro level—holding tolerances within ±0.0001” and achieving mirror-like finishes with no room for error. We support this detailed work with custom-engineered wheels that are:
Built for consistency – holding form over long production runs
Aggressive yet cool-cutting – to reduce heat distortion and burn
Tailored to the material – with bond and grit combinations suited for everything from hardened steels to fragile ceramics
Tackling Tough Materials with Superabrasive Precision
Semiconductor manufacturing is performed in clean rooms under extreme conditions with high heat, vacuum environments, reactive chemicals, and intense electric fields. Tools like etchers, deposition systems, and ion implanters must operate with micron-level accuracy that stays stable under pressure.
That’s why these tools are made of materials that offer:
Thermal stability to handle high processing temperatures
Mechanical strength to hold shape
Chemical resistance to survive plasma and gas exposure
For this work, grinding wheels must be capable of shaping and controlling difficult materials like plasma-resistant ceramics, hardened tool steels, and carbide-based coatings. On top of that, shops regularly face new materials engineered to improve thermal performance, erosion resistance, and particle control.
To machine these materials effectively, you need grinding tools that stay sharp, cut clean, and hold spec. Conventional abrasives can load up, overheat, and require constant dressing in these conditions, making them ill-suited for the task. On the other hand, CDT’s diamond and CBN wheels — made with resin, vitrified, hybrid, or metal bonds — are designed to handle these jobs with ease.
And what if a customer is working with a material that’s unfamiliar? That’s when we turn to the CDT grinding lab.
Custom Superabrasive Solutions Tested In-House
CDT’s in-house grinding lab is built to help customers test materials and validate wheel performance. Whether you’re running a new material or facing a recurring problem, we can help develop the right solution.
If you’re dealing with edge burn, profile loss, or surface finish issues on brittle materials, we’ll work with you to sort it out. We regularly work with advanced ceramics, silicon carbide, coated tool steels, and other materials that are now standard in semiconductor production. We use custom wheels and a controlled testing environment with the goal to help you dial in your process faster and avoid tying up valuable time and equipment on the shop floor.
Precision That Powers Progress
From wafer chuck carriers to dicing tool components, precision grinding shops keep semiconductor chip production running at scale. It’s not the work that happens inside the cleanroom—but it’s every bit as important.
At CDT, we know what’s at stake. As the industry moves toward thinner wafers, harder materials, and tighter specs, we’re here to help grinding teams produce parts that are consistent, efficient, and competitive. Our wheels are built for performance, long life, and lower cost per part.
Ready to Tackle Your Toughest Grinding Challenge?
From plasma-resistant ceramics to hard-coated steels, we know how tough these materials can be. We work directly with grinding shops to develop the right tool for the job.
Whether you’re qualifying a new material, scaling a high-volume part, or solving a surface finish issue, CDT delivers custom-engineered grinding solutions that help you move forward. Our in-house lab takes the guesswork out of testing and speeds up production.
Reach out to see how CDT can help with your next grinding challenge.
Profile vs. Surface Finish: Identifying the Limiting Factor in Your Grinding Process
Learn how to identify whether profile or surface finish is limiting your grinding process—and how to use that insight to reduce scrap and optimize performance.
Scrap is costly—both in time and materials. If you’re looking to improve quality and reduce waste, it’s essential to identify what’s holding your process back. In Episode 12 of The Grinding Chronicles, CDT Application Engineer Blu Conrad shares how measuring profile and surface finish can help pinpoint the root cause of your quality issues. Watch the video or read on to learn how to address these limiting factors and run a more efficient grinding operation.
The Grinding Chronicles - Episode 12
Why Your Parts Are Going Out of Spec — And How to Fix It: Part 1
Efficient grinding operations—especially at scale—depend on consistency to stay competitive. When parts start falling out of spec, the impact is immediate: lost time, wasted material, and rising costs. Two of the most common culprits are profile deterioration and surface finish breakdown. But how can you tell which one is actually limiting your process?
A targeted approach to tracking part quality can reveal the answer—and help you set the ideal dressing interval for your wheel.
Profile and Surface Finish: Understanding the Distinction
In grinding, profile refers to the macro geometry your wheel produces—the shape and dimensional accuracy of the part. Surface finish, on the other hand, captures the micro-level texture or roughness on the surface. Both play a critical role in quality, but they degrade differently and can indicate different underlying problems.
Track the Right Data
One of the most effective ways to diagnose which factor is causing your parts to fail is to measure both profile and finish at regular intervals. For example, take a measurement every five or ten parts and record that data alongside the volume of material removed.
Plotting those measurements on a graph—with volume ground on the horizontal axis and profile or finish on the vertical axis—will give you a clear picture of which element goes out of tolerance first.
“Whichever set of data crosses out of tolerance first—that’s your constraint,” says Blu Conrad, Application Engineer at CDT. “That tells you where your process is breaking down and where to focus your efforts.”
If profile is causing you to fall out of spec first, your dressing interval should be set based on that. If surface finish is the issue, your remedies need to shift toward surface-related variables.
If Profile is the Problem
When profile is the limiting factor, excessive force per grit is often to blame. This can occur when the wheel-work contact length is short, meaning fewer cutting edges are engaged and each grit is doing more work. Over time, this accelerates wear and throws the wheel out of shape.
In cases like this, upgrading to a more robust grinding wheel can help. A harder abrasive or more durable bond may provide better resistance to wear and extend the life of the wheel between dressing cycles.
But before you swap out tooling, it’s important to rule out other contributors—especially coolant. Inadequate coolant flow or misaligned nozzles can rapidly accelerate wheel wear and distort profile accuracy.
“It’s not always the wheel’s fault,” Blu explains. “Sometimes just optimizing your coolant delivery can make a huge difference in how long your profile holds.”
To learn more about effective coolant application, check out The Grinding Chronicles Episode 3, where Blu breaks down four key factors—velocity, flow, line placement, and temperature—and how each one affects wheel performance and part quality.
If Surface Finish is the Issue
In some processes, the surface finish goes out of spec before the profile ever does. This points to different limitations—often related to speed, feed, wheel dressing parameters, or wheel condition.
In an upcoming video later this year, we will walk through how to predict surface finish with a simple calculation and explain what changes you can make to improve results. Subscribe to our YouTube Channel to catch the release.
Make Your Dressing Interval Work for You
Scrap is always costly—but it’s also avoidable with the right analysis. By identifying whether profile or finish is the first to fail, you gain control over your process. You can set a purposeful dressing schedule that reduces unnecessary wheel wear, increases uptime, and keeps parts in spec for longer. After all, both profile and finish will eventually degrade—it’s not a matter of if, but when—so knowing which factor breaks down first lets you plan more strategically.
Need help dialing in your own dressing interval? Contact CDT’s Application Engineering team at TheGrindingChronicles@cdtusa.net or visit cdtusa.net/the-grinding-chronicles for more grinding insights.
Check out more videos from The Grinding Chronicles and follow CDT on Linked In for the latest news in grinding technology.
Breaking from the Conventional: How Vitrified CBN Wheels Excel on Studer Equipment
Vitrified CBN wheels improve performance, reduce downtime, and enable lights-out grinding on Studer machines. Learn more in CDT’s latest blog.
At Continental Diamond Tool, we frequently manufacture Vitrified CBN wheels for widely used grinding platforms such as the Studer S33, FavoritCNC, and S131r. While many operations still rely on conventional abrasives, Vitrified Bond CBN is increasingly the go-to solution for high-precision, high-volume grinding applications—and for good reason.
If your shop is pushing for tighter tolerances, longer tool life, or lights-out production, here's why this technology may be the right move.
Why Choose Vitrified CBN?
When grinding hardened steels and other ferrous materials, Vitrified CBN (Cubic Boron Nitride) wheels offer significant advantages over traditional abrasives like aluminum oxide, which are commonly used for similar applications:
100–300× Longer Wheel Life
Vitrified CBN outlasts conventional wheels by a wide margin, reducing the frequency of wheel changes and downtime.Tighter Tolerance Control
These wheels maintain form exceptionally well, ensuring consistent part geometry even across extended production runs.Cooler, Cleaner Cutting
The vitrified bond provides superior chip clearance and heat dissipation, minimizing the risk of thermal damage and improving surface finish.Ideal for Lights-Out Operation
Extended wheel life, consistent performance, and reduced need for manual intervention make Vitrified CBN wheels a great match for automated and lights-out environments.
“If you are dressing properly with a diamond rotary dresser, your vitrified CBN wheel will last a very long time—and you’ll produce high-quality parts at a great pace with little to no variation,” says Troy Giacherio, CDT’s Product Line Manager for Rotary Dressers.
Rotary Dressing Techniques for Vitrified CBN
Dressing is essential for maintaining wheel shape and exposing fresh cutting edges—but how often and how efficiently you can dress the wheel makes a big difference in productivity.
Conventional Abrasive Wheels
These wear down quickly and require frequent dressing to restore geometry and surface integrity.Vitrified CBN Wheels
Thanks to their exceptional wear resistance, these wheels require dressing far less frequently. When dressing is needed, rotary diamond dressers are the tool of choice.
At CDT, we manufacture rotary diamond dressers tailored to your process, whether using conventional or Vitrified CBN wheels. For vitrified applications, these dressers enable precise, programmable dressing that fits seamlessly into automated processes—reducing operator time and increasing repeatability.
“If you’re transitioning from conventional abrasives to CBN—or if you’re seeing issues like burn or finish patterns—you might not be dressing your wheel correctly,” says Troy. “If your power draw starts creeping up or you see changes in surface finish, that’s your cue—it’s time to dress the wheel.”
Want to learn more about dressing Vitrified Bond CBN wheels with a rotary diamond dresser? Watch Episode 5 of The Grinding Chronicles, where Troy breaks down key dressing parameters like velocity ratio, overlap ratio, and depth of dress.
Top Signs You Should Be Using Vitrified CBN Wheels Instead of Conventional Abrasives
If your current process is held back by:
Frequent dressing and wheel changes
Inconsistent size or surface finish
Excessive heat generation
Limited machine uptime or operator availability
…it may be time to evaluate a Vitrified CBN solution. Especially when paired with capable machines like the Studer S33, FavoritCNC, and S131r, CBN technology can unlock new levels of efficiency and reliability.
“When switching from conventional wheels to vitrified CBN wheels, we’ve seen dress intervals go from a few parts to hundreds,” says Troy. “The key is balancing efficiency with consistency to get the most life out of your wheel and performance from your process.”
Whether you’re looking to reduce cost per part, improve part quality, or enable lights-out production, switching to Vitrified CBN may be the upgrade your process needs.
See CDT Wheels in Action: United Grinding Precision Summit
Curious how Vitrified CBN performs in a real-world environment?
Join us July 29–30 at the United Grinding Precision Summit, where CDT has supplied wheels on these three Studer machines: the S33, FavoritCNC, and S131r.
You’ll have the opportunity to meet our engineers, discuss dressing techniques and process parameters, and explore how customized Vitrified CBN wheels can enhance your operations.
👉 RSVP now at united.grinding.com/theprecisionsummit2025
Making the Switch from Conventional Abrasives to CBN
Ready to explore Vitrified CBN Wheels and Diamond Rotary Dressers? At CDT, our sales team includes dedicated process engineers who work directly with customers to assess grinding setups, identify improvement opportunities, and develop optimized solutions tailored to today’s most advanced platforms.
Whether you're running a Studer S33, FavoritCNC, or S131r, or comparable machines from Kellenberger, Bryant, or Okuma, CDT has the tools and technical expertise to support your production goals. We help manufacturers across industries transition from conventional abrasives to high-performance vitrified CBN—delivering better form retention, reduced dressing, and longer wheel life.
📞 Call us at 1-800-443-6629 or contact us online to get in touch with a CDT expert and find the right grinding solution for your application.
A Novel Solution to a Conventional Problem
For manufacturers struggling with long lead times and lack of support for their conventional abrasive grinding wheels, CDT offers a faster, more reliable solution.
Many manufacturers today are struggling to find a supplier with the right technical support for their grinding applications. Current wheel suppliers have been pulling back on technical service for years, and long lead times add another layer of frustration for manufacturers who need reliable custom solutions fast. When every delay impacts production schedules and delivery commitments, fast answers and reliable delivery is critical.
Compounding these supply challenges, the skilled workforce is retiring, leaving newer workers without the same level of technical experience. This makes expert guidance and reliable support more important than ever—manufacturers not only need high-quality grinding wheels but also the knowledge to use them effectively. That’s where CDT steps in.
At CDT, we believe in providing the best tools to help industries thrive. If we don’t make it, we find it—and make it better. That’s why we’ve partnered with Krebs & Riedel, a century-old global leader to bring their high-quality conventional abrasive grinding wheels to North America—now stocked and custom-profiled at our manufacturing center in New Haven, Indiana. By expanding our offerings, we’re giving North American manufacturers faster access to premium grinding solutions with inventory ready to be customized—all backed by CDT’s commitment to exceptional service.
While CDT is an established engineering powerhouse when it comes to superabrasive solutions and grinding application know-how, we have not applied our expertise to the conventional abrasives market, until now. Through our partnership with Krebs & Riedel, we are here to solve the problems that conventional abrasive customers are facing by offering local inventory, in-house custom finishing, and expert engineering support of Krebs & Riedel's world-class products. Watch the video and read the article below to learn how CDT is filling the gaps to ensure faster turnaround and better performance for both superabrasive and conventional abrasive grinding wheels.
A Trusted Source for Conventional Abrasive Grinding Wheels:
Finding a new supplier for your conventional abrasive grinding wheels can be daunting, but you shouldn’t have to settle for slow delivery or compromise on precision. Continental Diamond Tool is filling the gap with a new line of custom-profiled conventional abrasive wheels supported by our dedicated team of application engineers. As the exclusive North American supplier of Krebs & Riedel’s world-class conventional abrasive grinding wheels, we ensure our customers get the best technology with faster lead times and expert guidance. Our application engineers can step in to assist your team in troubleshooting grinding issues like wheel loading, excessive wear, workpiece burn or chatter, and inaccurate dimensions. With half a century in the grinding industry, we understand the challenges manufacturers face and are committed to delivering solutions that will keep operations running at peak performance.
Where Conventional Abrasives Are Commonly Used
Conventional abrasive grinding wheels help produce the critical parts that keep the world moving—from gears and bearings to internal combustion engines. These wheels are widely used across cost-conscious industries that require reliable material removal. In gear manufacturing, they play a critical role in shaping and finishing gears to exact specifications. Disc grinding is commonly employed for achieving flat, parallel surfaces in automotive and industrial components. Cutting and rough grinding applications rely on conventional abrasives for heavy stock removal and material shaping in fabrication and foundry operations. In the automotive sector, grinding wheels are essential for machining internal combustion engine components, such as crankshafts and camshafts. Additionally, bearing rings and linear technology applications require high-precision grinding to ensure smooth operation and longevity in mechanical systems.
With CDT's lineup of conventional abrasive options from Krebs & Riedel, we support all of these major industries with high-quality solutions designed for performance and reliability.
Technology That Drives Performance
Krebs & Riedel has been perfecting bonded abrasives for over 125 years, and their expertise now powers CDT’s conventional grinding wheel offerings. With a focus on performance, longevity, and efficiency, their wheels stand out for their:
Customization – At Krebs & Riedel, they offer optimized grain structures, bond systems, and pore space composition to push the limits of grinding in ways specific to your application.
Precise Finishing – Advanced custom profiling on CDT’s Burri PM550T makes fine-tuned precision and smooth finishes possible.
Quality Materials – The integrity and longevity of your grinding wheel depends on premium abrasives and carefully engineered bonding systems like those used by Krebs & Riedel.
“At CDT, we are committed to providing our customers with not only the best wheels but also the expertise to optimize their performance,” says Erik Van Meter, CDT’s Product Line Manager of Conventional Abrasives. “We partnered with Krebs & Riedel because their dedication to quality and innovation aligns with our own high standards. Their world-class wheels, combined with our investment in the Burri PM550T, allow us to deliver precise, fine-tuned profiles that allow our customers to achieve better grinding results.”
More Than Just Conventional Abrasives: A Complete Grinding Solution
For applications requiring even greater performance and durability, CDT also offers a full range of custom-engineered superabrasive products, including diamond and CBN grinding wheels and diamond rotary dressers. These advanced grinding products are perfect for applications where conventional abrasives fall short.
Superabrasive grinding wheels deliver:
Higher grinding efficiency and performance
Longer lifespan and durability
Better precision and surface quality
CDT has assembled a team of industry-leading application engineers—many featured in "The Grinding Chronicles" series—who use the latest technology to make data-driven decisions for product innovation. Their process improvements have helped hundreds of customers save millions of dollars. Whether troubleshooting grinding issues, optimizing machine performance, or ensuring proper coolant delivery, our team can help you achieve the best possible grinding results.
With our ability to source high-quality conventional grinding wheels and manufacture superabrasive solutions, CDT serves all the leading manufacturing industries, having produced more than 70,000 unique products for a multitude of applications. Starting with the right abrasive material plays a critical role in product development, impacting grinding efficiency, surface quality, and overall tool life. Whether it's silicon carbide, aluminum oxide, diamond, or cBN, our portable and in-house grinding lab technology allows us to analyze performance data and recommend the optimal solution to help customers achieve the best possible grinding results.
Why Partner with CDT?
At CDT, we go beyond delivering grinding wheels—we help you find the right solution for your company’s success. Here’s why customers are turning to CDT’s advanced grinding products:
Expert Guidance & Support – Our team works with you to specify the optimal abrasive wheel for your application requirements.
Reliable U.S.-Based Inventory – With Krebs & Riedel wheels stocked in our New Haven facility, you benefit from shorter lead times and reduced downtime.
Custom Profiling Services – Custom profiling on our state-of-the-art Burri PM550T ensures your grinding wheel arrives ready to perform at its best.
Seamless Integration with Superabrasives – If your application demands more than conventional abrasives, we offer diamond and CBN solutions to take your grinding performance to the next level.
“We don’t just supply wheels—we get results,” says Van Meter. “Our team works closely with customers to understand their needs and deliver the best possible grinding wheel configurations, including profiling services to ensure maximum performance right out of the box.”
It Starts with a Quote
With decades of experience and a commitment to performance, CDT provides the right tools for your grinding needs. Whether you need conventional abrasives or high-performance superabrasives, we’re here to help you achieve the best possible results. Plus, we offer competitive pricing to ensure you get the best solution at the right value. Put us to the test with a free, no-obligation quote.
For more information on silicon carbide or aluminum oxide grinding wheels from Krebs & Riedel, visit our conventional abrasives product page or contact our team today at 1-800-443-6629
Improving Part Quality and Reducing Costs in Medical Grinding
Discover how CDT helps medical manufacturers improve part quality, reduce scrap, and cut costs with custom-engineered grinding wheel solutions.
In medical manufacturing, even small inconsistencies in components like implants, surgical tools, or drill bits can lead to costly failures and compromised safety. Precision and reliability aren't just goals—they're required for industry standards and FDA approval. Yet it’s common for manufacturers to struggle with persistent issues like inconsistent surface finishes, excessive burr formation, and unpredictable wheel performance that increase scrap and labor costs.
At Continental Diamond Tool (CDT), we understand the root causes behind these challenges and help medical manufacturers overcome them through targeted, reliable, custom engineered grinding solutions.
One of CDT’s biggest strengths is how closely our sales and engineering teams work together—often as the same people. Many of our team members serve dual roles, combining application expertise with customer-facing support, so the person helping you select your wheel also understands how to fine-tune it for maximum performance.
“The most important factor for medical suppliers is part quality,” says Blu Conrad, CDT Application Engineer who specializes in medical manufacturing support. ”When we see issues like burrs, poor finishes, or short wheel life, it’s usually a sign that there is a problem with the wheel or process set up. We can help you fix that.”
CDT’s vitrified CBN wheels provide reliable, repeatable performance when grinding complex medical components like surgical drill bits.
Is Your Grinding Process Hurting Your Productivity?
Do you face problems like:
Inconsistent surface finishes and part quality?
Excessive manual deburring labor due to excessive burr formation?
Short wheel life and frequent dressing?
Difficulties maintaining tight tolerances and precise geometries?
These problems often come down to using a grinding wheel or machine settings that are not optimized for your application. At CDT, we take a hands-on, data-driven approach to help you pick the right wheel and adjust your set up — so you can count on consistent, reliable performance that fits the way you work.
Specialized Grinding Wheels Designed for the Medical Industry
CDT specializes in designing, developing, and delivering custom-engineered diamond and cBN grinding wheels for all types of medical manufacturing. While we have seven unique product lines, there are three distinct grinding wheel types that we commonly specify for medical manufacturers:
Plated Wheels: Perfect for roughing operations, plated wheels maintain precise profiles — like those required on complex medical implants and surgical cutting tools — for the entire life of the wheel with no dressing required. We also offer a strip and replate program that reuses your wheel core and reapplies the abrasive—restoring it to like-new condition at a fraction of the cost.
Vitrified CBN Wheels: Often found in finishing operations, these wheels minimize burr formation and ensure consistent, high-quality results. Best used with machines featuring onboard wheel dressers, vitrified cBN wheels are particularly cost effective for manufacturers who are taking advantage of lights out operation. CDT also manufactures the onboard Diamond Rotary Dressers that keep these wheels efficiently grinding at peak performance.
Hybrid Bond Wheels: A variation of CDT's resin bond grinding wheels, our EVO Hybrid Bond formula provides excellent shape retention, consistent free cutting, and reduced heat buildup. We often recommend this product line for finishing medical parts on machines where operators manually dress the wheel.
“We’ve helped customers reduce cycle times by up to 20%,” recalls Blu. “And just as important, we’ve been able to significantly cut down on manual deburring labor—especially when they switch to vitrified CBN wheels paired with onboard wheel dressers that run cleaner and cooler with less downtime than manual dressing.”
Proven Solutions Across Leading Machines and Materials
CDT grinding wheels are designed to perform on leading medical manufacturing machines, including platforms from Walter, Rollomatic, Schütte, Starr, and Strausak. Whether you're a large OEM or a contract manufacturer, we tailor each wheel to your production requirements.
“Medical components are often made from stainless steels like 17-4 or 455, which can be tricky,” Blu explains. “They’re gummy and prone to burrs. That’s why we pay close attention to both the material and the machine setup when we spec a wheel.”
Our team takes material properties—such as ductility and hardness—into account when developing wheels. Stainless steels are particularly prone to heat buildup and burrs. With the right wheel and setup, we can significantly reduce these effects, helping customers reduce scrap and minimize secondary deburring processes.
Your Trusted Guide for Long-Term Success
CDT isn't just a wheel supplier; we're your strategic partner in precision grinding. Our team proactively collaborates with you from new product prototyping to established production optimization, ensuring your processes are finely tuned and continuously efficient.
We can also help you evaluate machine options—well before it's time to order your grinding wheel. “It’s more common than it should be for us to get called in after a machine is already purchased,” says Blu. “We love to be part of the conversation earlier because features like onboard dressers make a huge difference. We’ve had customers retrofit onboard dresser technology just to unlock the full performance of a vitrified CBN wheel.”
In addition, our grinding lab is a valuable resource for customers. They can safely explore the performance limits of their wheels and identify opportunities for improvement without interrupting production or incurring the cost of scrap and downtime. We also offer a portable lab to diagnose system inefficiencies directly at the production site.”
From implants to surgical tools, CDT Application Engineer Blu Conrad specializes in helping medical manufacturers improve precision, reduce scrap, and save time. Reach out today.
Why Medical Manufacturers Trust CDT
Medical manufacturers consistently choose CDT because we deliver:
Rapid turnaround and reliable lead times
Dependable quality, performance, and cost-efficiency
Hands-on technical support, troubleshooting, and training for your operators
Expert R&D engineering services focused on helping you succeed
Don’t let grinding wheel issues compromise the quality or productivity of your medical manufacturing operations. Take control of your process and partner with CDT to confidently meet your critical manufacturing goals.
Ready to transform your grinding process? Contact Blu Conrad and others on the CDT sales team today for a free consultation and quote. Call 1-800-443-6629 or visit our webform to get started.
Grind Talk: How CDT Improves Grinding Performance for Customers
Discover how CDT engineers partner with manufacturers to cut scrap, improve performance, and deliver custom superabrasive grinding solutions.
At Continental Diamond Tool, we’re passionate about crafting custom superabrasive grinding solutions—and turning that passion into a competitive edge for our customers. Last month, we sat down with several of our engineers to capture their real-world experiences: how CDT teams up with customers to solve tough grinding issues fast and deliver results that truly move the needle. Watch the video or keep reading below.
Real Stories of CDT Problem-Solving
In a series of interviews, our engineers discussed what true partnership and problem-solving look like at CDT—whether it’s answering a midnight call or collaborating on a process fix that slashes scrap. These are the highlights.
Driving Scrap Reduction Through Collaboration
CDT Vice President of Research and Development Jack Shindle has known Continental Diamond Tool not just as a workplace, but as a trusted partner.
“Every place I’ve worked, I’ve been part of the innovation team,” begins Jack. “My previous employer was actually a customer of Continental Diamond Tool. I used CDT resin bond, metal bond, and plated wheels to grind ceramic components—both in the green state and after firing. At that time, I collaborated with CDT engineers on a grinding process. Through our work — and some innovative fixture design — we were able to drop the scrap rate by 25%.”
Our engineering team still works closely with customers to fine-tune wheel specs and process changes, avoiding off-the-shelf fixes in favor of custom collaboration for their unique problem.
Going the Extra Mile for Customers
Andrew Olvera knows what it’s like to be on the other end of that late-night support line. Before joining CDT, he relied on our team whenever his own production hit a snag.
“When I worked for an OEM machine manufacturer, CDT stood out because they were always there for me,” remembers Andrew. “If I had a call in the middle of the night, my application engineer would answer the phone. My salesperson was there the next day. They were always there to help me through thick and thin.”
Today, Andrew pays that forward—fielding customer calls around the clock and coordinating rapid-response solutions so our partners never miss a beat.
Building Trusted Connections
Zeb Domer first experienced CDT’s commitment long before he joined our team. Working for a customer, he saw firsthand how our people and products stood up under pressure.
“In my previous job, we actually used Continental Diamond Tool’s grinding wheels, and that's where I became familiar with the company's integrity and the quality of their product,” recalls Zeb Domer, Resin Bond Product Line Manager at CDT. “Anytime we ran into a situation, Continental Diamond Tool was just a phone call away. You really felt that personal connection, knowing they had your back if any issue arose.”
Now as our Resin Bond Product Line Manager, Zeb brings that level of trust to every conversation—treating customers as true partners, not just orders to be filled.
Commitment to Performance, Delivery, and Innovation
Across every interaction, CDT’s engineers live by the simple truths that customers expect: on-time delivery and uncompromised performance. As Jack Shindle puts it,
“The two things customers want is they want you to be on time and they want you to have equal or better performance. We talk about on-time performance or on-time delivery every day.”
It’s not just about meeting today’s challenges—it’s about the genuine passion of our people to invest time, resources, and energy into what’s important. As Andrew Olvera reminds us,
“Everyone here is very passionate about their product line and the namesake of CDT—from the owner expanding our facility to the engineering department being at your call to help you develop new tooling.”
And the best part? We’re only getting started. In Jack’s words,
“I think we’re just starting to scratch the surface on what we’ll be able to achieve in the markets that we’re either currently serving or looking to serve.”
That passion and drive ensure every solution we deliver is backed by both expertise and a genuine commitment to long-term partnership and success. Our engineers—Jack, Andrew, and Zeb—have been in your shoes as customers themselves, so we know exactly what it takes to keep production running. Ready for our team to help you with your grinding process improvements?
📞 Contact us today to see how CDT can help push your production capabilities further.
Call us at 800-443-6629 or visit cdtusa.net to get started.
CDT Targets Growth in Eastern Europe with Sales Presence in Poland
Continental Diamond Tool expands into Poland, bringing high-performance grinding wheels and diamond dressers to the region’s growing aerospace and automotive industries.
Continental Diamond Tool is targeting major sales growth in Eastern Europe after launching our first sales force in Poland.
Leading the team is Mariusz Kowalski, our new Sales Manager for Poland, who is spearheading a drive for new orders on behalf of Continental Diamond Tool (CDT).
CDT supplies precision tooling for Tier 1 aerospace and automotive companies, specialising in designing and producing high‑spec grinding wheels for advanced manufacturing processes. Our product range includes diamond‑encrusted rotary dressers, accurate to within one‑thousandth of a millimetre.
We have also ramped up the manufacture of new electroplated grinding wheels and tools thanks to a £250,000 investment in cutting‑edge equipment at our Kinmel Bay location.
CDT sees huge opportunities to supply new customers in the rapidly developing engineering sector in Poland and other Eastern European countries.
The move is part of a £4 million expansion that will triple production and double our workforce in Kinmel Bay to 80.
As part of the strategy, we will move later this year to a new 30,000 sq ft factory—three times the size of our current premises—less than half a mile away on the Tir Llwyd Industrial Estate.
Mr Kowalski graduated with a Master of Science from Warsaw University of Technology, specialising in Mechatronics Engineering, which combines mechanical, electrical, computer engineering and robotics to create innovative and complex systems.
Before joining CDT he spent most of his career at Fanar, a Polish leader in machining‑tool manufacturing, where he rose through the ranks and developed new grinding and welding processes.
Now representing CDT from Łomianki—about 20 miles west of Warsaw—he said:
“The new plant in Kinmel Bay will generate more products and a larger production volume, putting us in a perfect spot to support what’s happening here in Poland.
“The Polish market in terms of advanced manufacturing in particular is the fastest-growing in Europe with aerospace companies like Pratt and Whitney and General Electric already in Poland and the country has its own rapidly growing engineering sector which we can service.
“Poland is also attractive to European Union countries like Germany and France because it has a well-educated and skilled workforce, lower costs and is more flexible.
“It also has between 30 and 40 tool-making companies and that’s a market we are also focusing on along with the automotive sector.
“Poland has a lot of engineering companies popping up every day and they’re growing fast.
“I believe that in 10 years’ time Poland could be a world leader in high tech for aerospace, automotive and the medical science industries and CDT can be part of that.
“With our modern factory in Kinmel Bay due to come on line later this year and our operation in the USA in five years’ time we could be looking at a market worth £80 million to the company.
“It is early days for us here in Poland but every day we learn more and make new contacts.
“It’s a fast developing country. Twenty years ago we had 20 per cent unemployment but now it’s below five per cent and the economy is booming.”
CDT’s European division is also seeing business boom, with sales of our new electroplated grinding products rocketing by 960 per cent over the past two years.
We expect electroplated products to outsell rotary dressers within a few years as orders continue to increase, and the move into Poland should only boost demand.
We already export 50 per cent of our turnover from the U.K., with electroplated grinding products reaching beyond Europe into the Middle East, Thailand and Indonesia, and sales forecast to overtake rotary dressers in two to three years.
The Kinmel Bay operation was founded as Consort Precision Diamond in 1984, specialising in diamond‑encrusted rotary dressers and grinding wheels.
CDT acquired and rebranded the business in 2018; our global headquarters are in New Haven, Indiana.
We are one of only two similar companies in the U.K., supplying sectors that include aerospace, automotive, medical and semiconductors.
Our products are used in Boeing 777 and 787 Dreamliner aircraft, as well as the Airbus A330–A380 range, whose wings are made at the Airbus factory in Broughton, Flintshire.
Managing Director Jeff Wirth said:
“Strategically, appointing the team in Poland was a very important move because it’s the next step in our expansion in Europe.
“Poland’s economy has been transformed in recent years and it’s now a manufacturing powerhouse so this is perfect timing.
“For many years Germany was the engine of Europe and now Poland has taken that mantle.
“Poland is booming and growing. They have a great workforce and a great work ethic and the investment they have made over the past 20 to 30 years has paid off.
“Our operation there is being integrated into the company at a time when we are going to be moving into the new factory which will enable us to triple our production capacity, with new products coming on stream.
“Mariusz will be at the forefront, ensuring that our clients in Poland receive top-notch service and support. His expertise and dedication are key to navigating this phase of growth.
“It’s a really exciting time for CDT – watch this space.”
Continental Diamond Tool Limited (CDT Ltd.), based in Kinmel Bay, Rhyl, U.K., is the European subsidiary of Continental Diamond Tool Corporation, headquartered in New Haven, Indiana, U.S.A. For more than 40 years, CDT Ltd. has been a leader in diamond rotary dresser technology, originally operating as Consort Precision Diamond. Since joining CDT, the company has expanded its product line, delivering high-performance diamond plated grinding wheels and other premium superabrasive products to customers worldwide.
Related links:
https://www.business-live.co.uk/enterprise/north-wales-precision-engineering-firm-31694121
https://www.rhyljournal.co.uk/news/25181361.north-wales-firm-eyes-huge-growth-eastern-europe/
https://www.wales247.co.uk/high-flying-north-wales-engineering-firm-targets-growth-in-eastern-europe
https://businessnewswales.com/north-wales-engineering-firm-targets-growth-in-eastern-europe/
Solving Grinding Challenges in Advanced Ceramics with Superabrasive Solutions
Discover how custom-engineered superabrasive grinding wheels improve precision, reduce scrap, and boost efficiency in advanced ceramic manufacturing.
Working with advanced ceramics? Then you know the challenges: parts that chip under pressure, tools that wear out fast, and long cycle times that slow you down.
Whether you’re machining zirconia for aerospace, silicon carbide for electronics, alumina for medical components, or glass for food and beverage applications, the goal is the same—hit tight tolerances without sacrificing efficiency.
At Continental Diamond Tool (CDT), we understand the pressure—balancing precision and productivity, maintaining a competitive edge, and ensuring employee safety and customer satisfaction through an unwavering commitment to quality and best practices.
That’s why our superabrasive grinding wheels are engineered not just to meet specs, but to solve real manufacturing challenges. Our role is to support you with tools that cut downtime, reduce scrap, and maximize productivity—because in your business, reliability is everything.
The Problem: Time, Tool Life, and Surface Integrity
Ceramic materials are notoriously hard and brittle. With the wrong grinding setup, you risk:
Microcracks and subsurface damage
Excessive wheel wear
Long grinding cycles that reduce throughput
If your process isn’t delivering the results you need, there are many variables to check out—feeds and speeds, coolant delivery, dressing frequency. But among these, one of the most powerful levers is your grinding wheel.
Not all grinding wheels are created equal. Traditional wheels that were designed for grinding metal—even some diamond and CBN options—often fall short when used on ceramics.
Metals have distinct properties that react to heat and stress very differently than ceramics, so designing a grinding wheel that is optimized specifically for the ceramic material you are grinding will set you up for the best results.
The Solution: Tackling Challenges with Advanced Bond Technologies
That’s why CDT develops advanced vitrified and hybrid bonds—engineered specifically for ceramics—to handle extreme hardness, reduce power consumption, and maintain consistent performance over time. Our engineering team has worked with leading global industries to:
Reduce grinding forces by up to 30%—less heat, less damage
Cut cycle times in half—to exceed production targets
Increase tool life up to 20x—because every wheel change costs time and money
Whether you're grinding alumina, zirconia, silicon nitride, or another ceramic, our custom bond systems help you maintain surface integrity while keeping production moving
Purpose-Built Tools for Your Machines
There are countless combinations of wheel types and machine settings that can technically get the job done—but only a wheel engineered for your application and material in mind will truly maximize output, consistency, and profitability.
CDT product engineers design custom wheels for the leading machines in your facility, including:
Round Tool grinding (e.g., Anca, Rollomatic, Star)
Surface and Blanchard grinding (e.g., Okamoto, ELB, DCM)
Cylindrical & ID grinding (e.g., Studer, Toyoda, Landis)
Double disk and fine grinding (e.g., SpeedFam, Supfina)
Need unique geometries? We engineer wheels with fluting, coolant holes, cross-cutters, and flat-bottom drills to meet your exact requirements. We’re here to help you move beyond trial-and-error to get dialed-in results from the first part to the last
Tools Built for High-Performance Lines
Your production line is fast, automated, and precise—your tooling should be too. CDT supports modern machining environments with:
Multi-axis CNC compatibility
Rotary dressers for automated operations
Through-spindle and high-pressure coolant systems
High-speed spindle compatibility for ID grinding
We don’t just supply grinding wheels—we engineer solutions that integrate seamlessly into your process. Our application engineers can work with you—on-site or remotely—using data-driven analysis to fine-tune your settings for improved performance. Click here to learn more about our portable grinding lab, designed to collect real-time data directly from your machine—right at your facility.
Risk-Free Innovation: Partner with CDT
Switching tooling vendors is a big decision—and we don’t take that lightly. That’s why CDT makes the process transparent, collaborative, and low-risk. Our engineers work closely with your team to define clear success metrics and test parameters up front, so you know exactly what to expect before making any changes.
With over 50 years of experience and more than 70,000 unique tools engineered for over 5,000 customers, we’ve seen—and solved—a wide range of grinding challenges. Whether you're facing issues with surface finish, throughput, or wheel wear, our team brings proven expertise to help you move forward with confidence.
Let’s talk about your process—and how we can help you get more from it.
Call us at 800-443-6629 or visit cdtusa.net to get started.
Ceramic Grinding: Myth vs. Reality
CDT tests the grindability of ceramic vs. metal materials. Discover how ceramics like Silicon Carbide and Quartz really perform—and why the process matters.
Metals have historically dominated manufacturing, but ceramic materials are quickly gaining traction. While many machinists are comfortable grinding metals, ceramics can be intimidating due to their reputation for being difficult to work with. But is grinding ceramics really as challenging as it's made out to be?
In Episode 11 of The Grinding Chronicles, Application Engineer Harrison Sheldon tackles this misconception head-on. Watch the video or continue reading below to discover the realities of grinding ceramics and how their performance compares to metals.
The Grinding Chronicles - Episode 11
Debunking the Myth: How Difficult is it to Grind Ceramics?
Grinding ceramics often gets labeled as difficult partly due to perception. Manufacturing operations typically have more experience with grinding metals, making ceramics seem inherently more challenging. Machinists unfamiliar with ceramics may develop misconceptions and overlook the subtle nuances involved in grinding these materials.
Ceramics possess unique properties that contribute to their perceived difficulty. Technical ceramics generally fall into three main categories: oxides (like alumina and quartz), non-oxides (like silicon carbide and boron carbide), and composites. Composites combine metals and ceramics with particulate or fiber reinforcement to create a hybrid material. Zirconia Toughened Alumina (ZTA) is a type of Ceramic Matrix Composite (CMC).
Ceramics are typically strong and hard, yet brittle, due to their strong ionic or covalent bonds. These strong bonds create a rigid atomic structure, making ceramics resistant to deformation. However, this rigidity also means ceramics cannot easily absorb impacts or distribute stresses evenly, causing them to fracture or chip under stress instead of deforming as metals typically do. This brittleness makes them more challenging to grind, as the process must carefully control forces and temperatures to prevent microscopic cracks or breakage.
The Rise of Ceramics in Manufacturing
Ceramic materials have been used by humans for thousands of years, initially for pottery, construction, and decorative purposes. However, the modern adoption of ceramics in industrial applications took off significantly during the late-20th century, particularly with advancements in superabrasive grinding wheels that can process these extra hard materials. Ceramics began to replace metals in applications demanding high-temperature stability, corrosion resistance, low weight, and excellent wear characteristics. For example, ceramic bearings in automotive turbochargers and ceramic turbine blades in aerospace engines showcase their growing importance in mission-critical, high-precision applications.
Despite their impressive capabilities, ceramics have historically seen slower adoption rates due to difficulties surrounding their machining and grinding processes. Traditional operations have hesitated to make the investment into superabrasive technology that supports ceramic grinding. However, adoption of these advanced grinding methods have greatly improved the ease and efficiency of processing ceramics has led to their expanded use within practical applications across various industries.
A Controlled Trial: Ceramics vs. Metals
To better understand ceramic grinding, CDT conducted a detailed trial comparing the grinding difficulty of various advanced ceramic materials. Four distinct ceramics were selected—Boron Carbide, Quartz, Silicon Carbide, and ZTA—and each was surface-ground using the same 240 grit vitrified diamond wheel. Sensors captured critical metrics, including power draw and cutting forces, at different feed rates to generate a series of three different material removal rates. We then aligned our findings with a similar historical study conducted on metals, allowing us to directly assess how ceramic materials measure up to metals in terms of grinding difficulty.
Understanding the Metrics
The two critical measurements taken during grinding were power draw and force. Why focus on these?
1. Power Draw: This metric directly relates to the grinding zone temperature. Elevated temperatures accelerate diamond wear, causing wheel degradation.
For example, in a practical scenario, higher temperatures can significantly shorten the life of a grinding wheel, increasing operational downtime and costs. Therefore, optimizing power draw directly contributes to maintaining productivity and profitability.
2. Cutting Forces: Excessive cutting forces can lead to machine deflection, vibrations, increased wheel wear, stress on machinery, and quality issues like cracking.
Consider a manufacturer grinding precision ceramic components for aerospace applications; excessive cutting forces could lead to subtle defects or inconsistencies that might compromise safety and performance. Managing and controlling these forces through proper grinding parameters is crucial for maintaining product integrity and consistency.
Results of the Experiment
The experiment conducted by The Grinding Chronicles team provided valuable insights into the relative difficulty of grinding ceramics compared to metals:
Specific Power: Among the ceramics tested, Boron Carbide required the most power, indicating it can be more challenging to grind, whereas Quartz needed the least.
Force: The ranking of ceramic materials was the same when evaluating the cutting force required, reaffirming the results from the specific power analysis.
Cutting Performance: In a third analysis, we combined power and force data to evaluate the overall grindability of each ceramic material. This provided a clear picture of how easy—or difficult—each one was to grind. In this cutting performance evaluation, Quartz was notably easy to grind—so much so that it hardly registered on the standard graph. This illustrates that ceramics can range from very challenging (Boron Carbide) to exceptionally easy (Quartz).
To provide additional perspective, we referenced a notable 1970s study by Dr. Richard Lindsay, which examined the relative difficulty of grinding various metals using conventional abrasives. By using a similar methodology for our experiment, we were able to overlay our ceramic grinding data onto Dr. Lindsay’s original findings to evaluate the results.
In the direct comparison, it clearly illustrates how ceramics stack up against metals in grinding difficulty. The results showed that grinding Boron Carbide with a vitrified diamond wheel was only slightly more challenging than grinding 52100 steel using conventional abrasives. Meanwhile, Zirconia Toughened Alumina (ZTA) with a vitrified diamond wheel ground as easily as cast iron with conventional abrasives.
The Key Takeaway
Not all ceramics are created equal. Similar to metals, ceramic materials vary significantly in their grindability. Misconceptions about ceramics arise mainly because machinists are generally more familiar with metals and their properties, processes, and challenges.
However, from a power and force perspective, ceramics exhibit grinding characteristics comparable to metals. Success in grinding ceramics depends heavily on understanding the optimal grinding processes, machine setups, and wheel selections tailored to each specific ceramic material.
If you're new to ceramics or struggling with grinding ceramic materials, CDT’s engineering experts are here to help. Contact us today at TheGrindingChronicles@CDTUSA.net for expert guidance.
Check out more videos from The Grinding Chronicles and follow CDT on Linked In for the latest news in grinding technology.
CDT Does It Again with Custom Electroplated Solution for the Energy Sector
Learn how CDT delivered a custom aluminum-core, large-diameter electroplated wheel for a demanding energy application with tight tolerances.
What makes CDT stand out in the world of superabrasive solutions? It’s not just our products—it’s our people and our values. At Continental Diamond Tool, we live by GRIT: being a Global, Responsive, Innovative Team. And just like the team behind them, our tools are built with GRIT—engineered to perform with precision, durability, and purpose. Once again, our team delivered a standout example of what that means in practice.
This time, the challenge came from a company in the alternate energy sector—an organization pushing the boundaries of energy technology to build a more secure, efficient, and resilient infrastructure for tomorrow. They needed a large-diameter electroplated grinding wheel capable of meeting unique operational demands. Our Plated Department engineered a custom solution with a complex geometry and aluminum core to get the job done.
A Specialized Tool for a Demanding Application
This customer needed a grinding solution that could take on a particularly difficult challenge: shaping silicon carbide into a complex form with a wheel that would be nearly impossible to dress using conventional methods. It was a new application for a newer customer working in a rapidly evolving field driven by breakthrough technology—where precision and reliability were critical, but few proven solutions existed.
Plated grinding wheels proved to be the ideal choice. The application required significant stock removal from a large workpiece while maintaining a highly intricate form and holding tight tolerances. Because the form couldn’t be redressed, the wheel needed to maintain its geometry throughout the process—something CDT’s electroplated tools are engineered to do exceptionally well.
The application also required a grinding wheel much larger than what’s typical for plated products—no problem for CDT, thanks to our oversized plating tanks that can accommodate large diameters up to 38 inches without the need for segmentation. To reduce the overall weight while maintaining structural integrity, our engineers custom-designed the wheel with an aluminum core—an uncommon material for electroplating that few plating manufacturers are skilled at handling. Backed by our team’s expertise and manufacturing capabilities, the entire process—from order to delivery—was completed in under our standard lead time of 5 weeks. (For customers with even tighter deadlines, we also offer a RUSH program that can cut lead times in half for an additional fee—contact our sales team for more information.)
Precision Engineering Backed by Quality Assurance
What added to the complexity of this project was the combination of a highly detailed design and exceptionally tight tolerances. The customer required tolerances as precise as ±0.0010" across critical features, with the bore needing to meet a strict +0.0016" / -0.0000" specification (H7). Adding to the challenge, the wheel featured a custom aluminum core—an uncommon choice for electroplated products. Because aluminum oxidizes quickly, it demands a specialized pretreatment process that not all plating manufacturers are experienced or equipped to handle.
This is where CDT’s commitment to quality makes all the difference. Thanks to CDT’s in-house expertise, we ensure strong, consistent adhesion while meeting all performance and quality requirements.
Our CNC department machines the core with robotic precision for consistent, repeatable results, while our skilled technicians apply masking by hand to ensure abrasive is placed exactly where it’s needed. Plating specialists carefully control timing and chemistry for optimal bond performance—but the real proof comes during inspection.
Every custom plated product at CDT undergoes rigorous quality checks using advanced metrology equipment, including:
Keyence IM-8000 for fast, high-accuracy dimensional measurement
Keyence VHX-960 digital microscope for surface structure and grit analysis
Zoller Venturion for presetting and edge geometry verification
Mitutoyo CMM for precise 3D inspection of critical tolerances
These tools—and the trained experts who use them—ensure that every wheel we deliver meets exacting performance standards before it ever reaches the customer.
Why CDT Plating?
Since launching our plating line four decades ago, CDT has custom-engineered more than 25,000 unique plated SKUs across a wide range of industries and applications.
We offer:
Proven Experience – Deep expertise in solving complex, nonstandard grinding challenges, paired with the efficiency to deliver simple, standard forms with speed
High-Capacity Infrastructure – More than 500 plating tanks in the U.S., with additional capacity expanding in Europe
Innovation – R&D engineering expertise and application support to optimize wheel life and grinding performance
Precision – In-house inspection tools for coupon measurement by expert technicians ensure every product meets exacting standards
Versatility – Ability to handle extremely large diameters, unusual substrates, complex geometries, and more
Sustainability – Strip and replate services to extend tool life, reduce waste, and support your long-term success
If other manufacturers say it can’t be done, chances are we already have.
Projects like this one for the energy sector are a clear example of CDT’s GRIT in action. With a global mindset, a responsive team, and an innovative custom-engineered approach, our Plated Department delivered a solution where others could not.
Do you have a challenging application that could benefit from CDT’s plated solutions? Let’s talk. Our team is here to help.
Tailoring Grinding Solutions for the Unique Challenges of Aerospace
From titanium to CMCs, see how Continental Diamond Tool’s grinding and dressing solutions are engineered to meet the toughest manufacturing challenges in aerospace.
In aerospace manufacturing, precision grinding is essential for producing components that must reliably perform under extreme conditions. Whether it’s turbine blades, vanes, or structural parts, these components require tight tolerances, exceptional surface finishes, and consistent performance—all while being made from some of the most challenging materials to grind, such as nickel-based superalloys, titanium, and ceramic matrix composites (CMCs).
The grinding process must balance aggressive material removal, heat management, and tool wear resistance to achieve the required part quality and efficiency. This is where electroplated grinding wheels and diamond rotary dressers provide significant advantages, offering solutions to some of the most persistent challenges in aerospace grinding.
Evolving Challenges in Aerospace Manufacturing
Aerospace manufacturers are continuously refining their production processes to meet increasing performance demands. Several industry trends are shaping the way grinding solutions must adapt:
Advanced Materials Require New Machining Strategies
The use of lightweight, high-strength materials such as carbon fiber composites, aluminum-lithium alloys, and CMCs is growing. These materials improve fuel efficiency without sacrificing structural integrity. However, their brittleness, heat sensitivity, and abrasiveness present machining challenges that require specialized grinding technology to shape them.
Additive Manufacturing Is Changing Component Design
3D-printed aerospace parts often require post-processing to achieve dimensional accuracy and surface integrity. Superabrasive grinding wheels are particularly well-suited for refining these components without inducing stress or altering their properties.
Rising Demand for High-Precision Parts
Increasing global defense spending and increased commercial air travel require manufacturers to produce high-performance components at scale, making efficient and repeatable grinding solutions more critical than ever.
Space Exploration Is Pushing Material Science Forward
New materials developed for satellite technology and space vehicles require grinding solutions that can maintain precision while working with ultra-hard alloys and ceramics, materials designed to withstand the extreme conditions of space.
With these challenges in mind, engineering the right grinding wheel is more critical than ever for ensuring part quality, process efficiency, and long-term performance in aerospace applications.
The Role of Electroplated Grinding Wheels in Aerospace
Electroplated grinding wheels offer a unique advantage in aerospace manufacturing due to their single-layer abrasive structure, aggressive cutting action, and ability to maintain form without dressing. Unlike bonded grinding wheels, where abrasive grains are embedded within a matrix, electroplated wheels expose a full layer of diamond or cBN material, ensuring sharp cutting edges and consistent performance.
How Electroplated Grinding Wheels Address Aerospace Challenges
✔ Maintaining Profile Accuracy: Electroplated wheels hold complex geometries without needing dressing, making them ideal for intricate aerospace components.
✔ High Stock Removal with Minimal Heat Generation: The open structure of electroplated wheels allows for aggressive material removal while features like coolant slots and through the wheel coolant delivery can be added to reduce heat buildup—critical when working with heat-sensitive materials like titanium.
✔ Custom-Engineered for the Application and Material: Abrasive size and type, core accuracy, and uniform plating are all critical to match unique aerospace grinding requirements.
✔ Longer Tool Life, Less Downtime: Electroplated wheels maintain their shape throughout their lifespan, eliminating the need for dressing and reducing machine downtime.
✔ Cost Savings with Strip and Replate Services: CDT offers a customized strip and replate program that allow customers to reuse the same core, reducing costs and lead times while delivering the same high-level performance. Our strip technology safely removes remaining abrasive without damaging the core and returns the tool to “like new” condition after replating. This makes it a more cost-effective and sustainable solution for aerospace manufacturers running frequent grinding operations.
"Electroplated grinding wheels are a great fit for aerospace because they are both precise and efficient. They hold intricate profiles, handle high speeds, and stand up against tough materials like nickel alloys, titanium, and ceramics — plus, with our strip and replate services, customers can extend the life of their tools and keep costs down without sacrificing performance," says Jordan Donnelly, CDT Product Line Manager for Electroplated Products.
Optimizing Grinding Performance with Diamond Rotary Dressers
Precision grinding requires continuous wheel maintenance to ensure optimal cutting efficiency and part consistency. Diamond rotary dressers are essential in aerospace manufacturing for truing and conditioning grinding wheels, ensuring the reliability and accuracy of the grinding process.
Key Benefits of Diamond Rotary Dressers in Aerospace
✔ Consistency Across High-Volume Production: Rotary dressers keep grinding wheels performing uniformly, ensuring part consistency and accuracy from the first to the last component.
✔ Reducing Cycle Times & Increasing Efficiency: Keeping wheels properly conditioned and sharp, minimizes grinding forces and allows for optimum cycle times while maintaining part quality.
✔ Application-Specific Design: Whether the application requires traverse or plunge-style dressing, CDT custom-designs each rotary dresser to specific customer needs and applications.
✔ Manufacturing Customization: Every application is different, thus requiring different solutions. CDT solves this issue by offering sintered, reverseplated, and metal bonded rotary dressers.
"Consistency is everything in aerospace manufacturing. Even the smallest deviation can throw off performance, which is why rotary dressing is so important. Our custom-engineered dressers keep grinding wheels precise and reliable, helping manufacturers get accurate, repeatable results every time," explains Troy Giacherio, CDT Product Line Manager for Diamond Rotary Dressers.
The Advantage of a Multi-Disciplinary Grinding Expertise
While electroplated grinding wheels and diamond rotary dressers provide high-performance solutions, CDT’s expertise extends beyond these technologies—allowing us to approach aerospace grinding challenges from multiple angles.
We have extensive experience working with a variety of:
Bond Types: Plated, resin bond, metal bond, vitrified bond, hybrid bond
Core Materials: Carbon fiber, ceramic, high-tensile strength steel, and many more
Diamond Patterns: Handset, random set, reverse plated, CVD-reinforced
Abrasives: Diamond, cBN, and conventional abrasive grinding solutions
This broad expertise enables CDT to study materials, test performance, and develop tailored grinding solutions that push the boundaries of what’s possible. Our dedicated grinding lab allows us to simulate real-world aerospace applications, testing how new materials react during grinding and refining wheel designs to optimize performance.
This cross-industry experience from both the product and application side fosters innovation, ensuring that we don’t just provide grinding wheels—we provide solutions tailored to the specific needs of aerospace manufacturers.
Expanding Capabilities to Better SERVE the Aerospace Industry
To address increasing global demand for aerospace products, CDT is expanding its electroplated grinding wheel production capacity with a new building that will grow its second plating line in Europe. This expansion will increase production efficiency, reduce lead times, and allow CDT to serve aerospace manufacturers at a larger scale.
"Expanding our plating facility is a big step forward. With the new electroplating line, we can speed up production and handle more capacity, getting products delivered faster. It’s all part of CDT’s commitment to innovation and supporting the growing needs of our aerospace customers," says Justin Hughes, Production Manager at CDT Ltd.
Finding the Right Grinding SolutionS for Aerospace Manufacturing
The challenges of aerospace manufacturing—tough materials, tight tolerances, and growing demand—require advanced grinding solutions that can maintain precision, minimize downtime, and innovate at speed and scale.
With specialized knowledge in electroplated diamond and cBN grinding wheels, advanced diamond rotary dresser technology, and expertise across many other grinding product types, CDT is uniquely positioned to help aerospace manufacturers optimize production processes and innovate for the future.
Contact us today to discuss how CDT’s precision grinding solutions can help optimize your aerospace manufacturing process.
Sales Skyrocket by 960% on Plated Products at CDT's Engineering Center in North Wales
Learn how CDT’s North Wales facility achieved 960% growth in Electroplated grinding products in just one year.
Sales of new Electroplated grinding wheels launched by a precision engineering company in North Wales have rocketed by 960 per cent.
The success of the Electroplated line has put Continental Diamond Tool (CDT) in Kinmel Bay – which supplies blue chip companies like Rolls Royce and Tenneco – on course for considerable growth in sales volume over the next three years.
The niche company is best known for the design, development, and delivery of diamond-encrusted rotary dressers, with tolerances of down to 1,000th of a millimetre in terms of accuracy.
The team in Kinmel Bay began making Electroplated grinding wheels and other electroplated products in a small way in the third quarter of 2023. By last summer, soaring demand led the company to invest £250,000 in new, cutting-edge equipment.
Conwy County Borough Council helped make the upgrades possible by securing £100,000 in funding from the UK Shared Prosperity Fund for CDT.
Production capacity will be increasing again later this year when the American-owned company moves to a new production site less than half a mile away on the Tir Llwyd Industrial Estate.
At 30,000 sq ft, the new building is three times the size of CDT’s current home and will see the workforce doubling from 40 to 80 over the next few years.
The company expects Electroplated products to outsell rotary dressers within a few years as orders continue to increase.
This surge has already created two new full-time jobs, with recruitment underway for two more positions.
Finance Manager Michaela Lawton said: “We always had high hopes for the Electroplated products, but no one really expected to hit 960 per cent growth year on year from when we launched the new line.
“The fact that we have been able to buy this new equipment means we can respond to the demand which is fantastic.
“We have been able to adapt quickly and increase our capacity. The funding that came via Conwy County Borough Council helped massively. We’re incredibly grateful they facilitated this grant.
“We export 50 per cent of our turnover, with Electroplated grinding wheel deliveries reaching as far as Europe, the Middle East, Thailand, and Indonesia.
“Going forward we see enormous potential for this product line. We expect our Electroplated grinding products to overtake our Rotary dressers in sales in two to three years.
“The interest is there, and we can respond to that. The market is huge, and we are well-placed to take a big share.
“Our parent company in America have put rocket boosters under CDT with their investment in technology and talent. The fact that we’re moving to the new premises makes all this possible— it’s going to escalate our growth on a huge scale.
“The leadership at CDT is very ambitious, and we have the perfect synergy and a great working relationship,” Michaela remarked. “The entire team is focused on growing our capacity to deliver the best superabrasive solutions for advanced manufacturing across the world.”
Cllr Nigel Smith, Conwy County Borough Council’s cabinet member for Sustainable Economy, who is one of three councillors who represent Kinmel Bay on the authority, said: “Having a company of this calibre in Conwy, particularly in my own town of Kinmel Bay is fantastic.
“I’m really pleased that the funding we’ve been able to source for the company from the Shared Prosperity Fund has enabled them to buy this new equipment and grow the company so spectacularly, with the opportunity for 40 further jobs.
“Among the recruits will be apprentices, so there will be opportunities for our young people to find high skill, well paid jobs on their doorstep. It’s brilliant.
“It’s a real feather in Conwy’s cap that we have a company that supplies high-end, blue-chip companies like Rolls Royce, Tenneco and others across the world.
“CDT’s continued investment is a big vote of confidence in Kinmel Bay and Conwy and the dedicated workforce we have in the local area.
“They are going to grow the economy here in Conwy and in Wales generally. It’s something we need to be proud of.”
Equally delighted is Justin Hughes, CDT’s production manager, who worked for the original company before it became part of Indiana-based Continental Diamond Tool Corporation six years ago.
Our CDT team in Wales has been upgrading and expanding its plating technology to mirror the cutting-edge, 500-tank plating lab at our U.S. headquarters—delivering the same level of precision and innovation worldwide.
Justin said: “Seeing those orders coming in gives you a real buzz and where we are going to be in 12 months is phenomenal. It’s very exciting.
“The potential is huge and the more people we can give jobs to, the better. These are jobs that are at a premium in an area like Conwy.
“That’s one of the reasons we’ve done our best to keep things as local as we can – a lot of the staff can walk or cycle to work.
“We have an experienced and highly skilled team here in Kinmel Bay and in the United States, which has made the transition to Electroplated grinding products a lot easier.
“The partnership with our American owners has been a seamless blend of two well-matched teams with complementary skills.
“They have taken as much knowledge from us as we have taken from them. They are very supportive, and we get lots of transatlantic cooperation.
“I am incredibly excited for the future here. It’s very busy, there’s lots of work to do and I like it like that, and all our employees are equally excited.”
Continental Diamond Tool Limited (CDT Ltd.), based in Kinmel Bay, Rhyl, U.K., is the European subsidiary of Continental Diamond Tool Corporation, headquartered in New Haven, Indiana, U.S.A. For more than 40 years, CDT Ltd. has been a leader in diamond rotary dresser technology, originally operating as Consort Precision Diamond. Since joining CDT, the company has expanded its product line, delivering high-performance diamond plated grinding wheels and other premium superabrasive products to customers worldwide.
Core Matters: How Different Wheel Body Materials Impact Grinding
Learn how grinding wheel core materials like steel, aluminum, and carbon fiber impact performance, precision, and cost to optimize your grinding applications.
When using superabrasive grinding wheels in precision manufacturing, selecting the right abrasive, bond type, and wheel core material is critical for optimal grinding performance and wheel life. While abrasives and bond types often take center stage, the wheel core can be equally important. The core material is the foundation that provides structural support and stability. The right core material ensures high performance while preventing machine strain, excessive grinding wheel wear, and unnecessary cost. But how do you determine the best core material for your specific needs?
In Episode 10 of The Grinding Chronicles, CDT Engineering Manager Jeff Wirth breaks down the essential properties of core materials and how they influence grinding applications. Watch the video or read the article below to learn how to choose the best option for your application.
The Grinding Chronicles - Episode 10
Selecting the Right Core Material for Grinding Wheels
The core of a superabrasive grinding wheel does more than just hold the abrasive—it directly impacts machine efficiency, grinding precision, and tool longevity. Choosing the right core material not only optimizes performance but also helps prevent unnecessary damage to the wheel, machine, and workpiece while enhancing operator safety.
Common core materials for superabrasive grinding wheels include metals—such as steel, aluminum, and copper—as well as non-metals like ceramics and resin composites. Ceramic or vitrified cores are commonly found in conventional abrasive grinding wheels and are also used in some superabrasive grinding wheels. Resin composite cores may be made from materials like bakelite, abrasive composites, or carbon fiber. Each of these materials has unique properties that affect grinding performance, and understanding their characteristics helps manufacturers make more informed decisions.
Understanding Core Material Properties
Density – Defined as mass per unit volume, density directly affects the weight of a grinding wheel. Heavier cores put added stress on machines and spindle bearings, which is why large-diameter grinding wheels are often designed with lighter core materials like carbon fiber, bakelite, or ceramic. An overly heavy wheel can reduce machine longevity, increase energy consumption, and pose handling risks for operators, making weight an important consideration for both performance and safety.
Expansion – Core materials expand due to heat and mechanical forces, which can impact grinding accuracy. Minimizing expansion is crucial for applications with tight tolerances, as it helps prevent wheel distortion and ensures consistent precision. Expansion occurs in two forms:
Mechanical Expansion: At high speeds, some core materials naturally expand due to centrifugal forces. Materials with high tensile strength resist this growth, maintaining stability and accuracy over time.
Thermal Expansion: Heat generated during grinding can cause materials to expand, leading to dimensional changes and reduced precision. Materials with low thermal expansion coefficients are essential for consistently achieving tight tolerances.
For high-speed and high-precision grinding applications, grinding wheels with cores made from high-tensile steel, carbon fiber, or vitrified ceramic often perform better. These materials minimize mechanical and/or thermal expansion, ensuring consistent performance, reduced deformation, and greater accuracy under extreme conditions.
Thermal Conductivity – This property determines how well a core material dissipates heat. Efficient heat transfer prevents thermal damage (burning) to the workpiece, improves surface quality, and extends tool life. Metal materials like Copper and Aluminum with high thermal conductivity remove heat, leading to lower wear and improved performance in high heat applications such as fluting drills.
Modulus of Elasticity (MOE) – This measurement indicates a material’s ability to resist deformation under stress. A higher MOE means the material is stiffer and less likely to flex or deform. Steel has a very high MOE. This can be beneficial for applications with high grinding forces that require tight tolerances, as a flexible core can introduce inconsistencies in grinding performance.
Comparing Core Materials: Strengths and Weaknesses
Each core material offers specific advantages and drawbacks. Here’s how some of the most common materials compare:
Steel is strong, durable, and resistant to mechanical expansion. However, its heavy weight can strain machinery.
Aluminum is lighter and often more affordable than steel, with higher thermal conductivity and resistance to corrosion. However, it has significantly higher thermal expansion compared to steel and other materials.
Copper offers excellent thermal conductivity and a high modulus of elasticity (MOE), but its weight and cost make it less suitable for large grinding wheels.
Ceramic is lightweight, cost-effective, and resistant to expansion, but low thermal conductivity and high stiffness or brittleness can be a drawback.
Resin composites, including bakelite, are affordable and lightweight. However, they lack stiffness and high thermal conductivity, making them more susceptible to expansion and heat buildup in high-force grinding applications.
Carbon fiber is ideal for demanding applications due to its high stiffness and low weight. However, it tends to trap heat and is more expensive than other materials.
Choosing the Right Core Material for Your Application
Selecting the best core material depends on several factors, including the type of grinding being performed, the machine’s limitations, and cost considerations. For example:
Flute grinding and medical drill bits operate at traditional speeds with lower grinding forces. This means that a wide variety of core materials can be used without significant performance issues. In these cases, ceramic cores are often recommended because they provide an excellent balance of cost and functionality.
High-speed applications like camshaft grinding generate significant heat and grinding forces. This makes high-stiffness materials like carbon fiber or high-tensile steel essential to be able to perform effectively and safely.
Hybrid or combination cores are an innovative solution for balancing weight, stiffness, and cost. This approach involves layering or combining different materials to optimize performance while keeping costs manageable. For instance, a steel core can be reinforced with carbon fiber to reduce weight without sacrificing strength.
Practical Considerations in Core Material Selection
Beyond material properties, cost plays a major role in selecting the right core material for grinding wheels. While core materials like carbon fiber and vitrified ceramic are both resistant to mechanical and thermal expansion and lighter weight, they come at very different price points. Once all process requirements are met, cost is usually the deciding factor, as manufacturers balance performance needs with material costs to avoid unnecessary expenses.
Budget-Friendly Options – Ceramic and resin composites provide cost-effective solutions for applications with lower grinding forces and minimal heat generation. These materials perform well in traditional grinding operations without adding unnecessary expense.
Mid-Range Solutions – Aluminum and standard steel cores offer a balance between affordability and durability. These materials are commonly used in medium-duty grinding applications where moderate strength and thermal properties are required, optimizing cost per part without sacrificing performance.
Premium Core Materials – High-tensile steel and carbon fiber provide top-tier performance, making them ideal for high-speed and high-force applications. While their higher price point increases the initial cost of the grinding wheel, their longevity and reliability often justify the investment by reducing long-term cost per part through extended tool life and efficiency gains.
When selecting a core material, it is essential to consider not just the upfront cost but also long-term savings from reduced machine wear, improved grinding efficiency, and longer tool life. CDT’s engineering team can help assess cost-effectiveness based on your specific grinding application, ensuring the best balance between performance and cost per part.
Optimize Your Grinding Wheel Performance with CDT
Choosing the right core material is critical for achieving consistent, high-performance grinding results. Whether you're working with grinding applications for heavy-duty industrial engine components or high-precision medical tool manufacturing, the engineering team at Continental Diamond Tool is ready to assist in customizing a grinding wheel with the materials that are best for your needs.
If you have questions about selecting the best core material for your specific application, CDT’s engineers are here to help. Reach out to TheGrindingChronicles@cdtusa.net for expert advice.
Check out more videos from The Grinding Chronicles and follow CDT on Linked In for the latest news in grinding technology.
The Essential Role of Diamond Grinding Wheels in Manufacturing with Composite Materials
Learn how diamond grinding wheels optimize composite material manufacturing, tackling fiber pullout, heat sensitivity, and tool longevity.
Manufacturing with composite materials presents unique challenges: differences in hardness, fiber pullout, and heat sensitivity require grinding wheels with specialized engineering to prevent defects and ensure tool longevity. Superabrasive grinding wheels, particularly those utilizing diamond abrasives, have become indispensable tools in achieving the desired quality and efficient grinding of parts made from composites.
Understanding Composites
Composites are engineered materials made by combining two or more constituent materials with distinct physical or chemical properties. The result is a material that exhibits characteristics different from the individual components, often offering enhanced strength and reduced weight. Common types of composites include:
Fiberglass: Comprising glass fibers embedded in a resin matrix, fiberglass is renowned for its versatility and is used across many sectors, from automotive components to sporting goods to garage doors.
Ceramic Matrix Composites (CMCs): These consist of ceramic fibers within a ceramic matrix, providing high-temperature stability and strength. CMCs are ideal for many aerospace applications.
Fiber Matrix Composites (FMCs): Combining fibers such as carbon or aramid with a polymer matrix, FMCs are commonly used in wind turbines and marine vessels due to their excellent strength-to-weight ratios.
The Role of Superabrasive Grinding Wheels
Manufacturing with composites presents unique challenges, primarily due to their heterogeneous nature and the abrasive characteristics of reinforcing fibers. Superabrasive grinding wheels, especially those with diamond abrasives, can be custom engineered to address these challenges effectively.
Fiberglass and FMCs: For these materials, electroplated diamond grinding wheels are an excellent choice. Plated diamond grinding wheels are widely used because they can be designed with an open structure that helps prevent issues like "loading," where softer materials can clog the wheel and lead to inefficiencies. These wheels are often employed with aggressive grit sizes ranging from 40 to 120 to ensure efficient material removal and desired surface finishes.
"Each composite material presents unique machining challenges. For example, Fiberglass and Fiber Matrix Composites can be tricky because they tend to ‘string’ if not cut properly. That’s why we often recommend a plated grinding wheel with aggressive grit—it keeps the material from gumming up and ensures a clean finish,” says Matt Harnish, CDT Sales Rep for Diamond and CBN Plated Products.
CMCs: Given their hardness and brittleness, CMCs require a more nuanced approach. While plated grinding wheels are suitable for the majority of composite grinding applications, approximately 75% of those we see at CDT, certain scenarios may benefit from metal bond or hybrid bond grinding wheels.
"Plated wheels are ideal for most composite applications because they maintain their profile and cut aggressively without excessive wear. But for Ceramic Matrix Composites, we sometimes refer customers to our metal bond or hybrid bond product lines when deeper diamond layers are needed for longevity and performance,” says Jordan Donnelly, Plated Product Line Manager.
Maintenance and Performance Considerations
Due to the variable composition in composite materials, it is common for grinding wheels to experience "loading," where debris accumulates on the wheel's surface and diminishes cutting efficiency. While plated grinding wheels typically do not require dressing, in these applications some dressing can help to restore their optimal performance and prolong their lifespan. Proper coolant application can also help to reduce the amount of debris.
"One of the biggest factors in machining composites is managing tool wear. If a wheel starts loading up, it’s not cutting efficiently. Regular dressing keeps the wheel sharp and extends its life, ensuring our customers get consistent performance,” Matt explains.
Comparative Advantages
When evaluating grinding solutions for composites, several factors come into play:
Performance: Superabrasive grinding wheels, particularly diamond-based plated wheels, offer superior cutting efficiency and precision compared to alternatives like carbide-tipped wheels.
Durability: The inherent hardness of diamond ensures a longer tool life, reducing the frequency of replacements and downtime.
Cost-Effectiveness: While the initial investment in superabrasive wheels is high, their extended lifespan and enhanced performance lead to cost savings over time, often making them more cost effective when considering cost per part.
“We switched from carbide to diamond-plated wheels over 30 years ago and have seen great results. They last much longer and aren’t that much more expensive. The savings in tool life and less downtime easily make up for the cost. Diamond’s extreme hardness, durability, and efficiency make it the best choice for grinding composites, especially with the precision we need for large-scale building construction and remodel projects,” says a longtime CDT customer.
Emerging Technologies and Industry Outlook for Composite Machining
The composite industry is continually evolving, with advancements aimed at improving manufacturing efficiency and material performance. Notable emerging technologies include:
Automated Fiber Placement (AFP): This advanced method involves the precise placement of fiber tapes onto molds, enhancing production rates and consistency in composite part fabrication.
Additive Manufacturing with Composites: The integration of 3D printing technologies allows for the creation of complex composite structures, offering design flexibility and potential material savings.
The composites industry is experiencing robust growth, with a market valuation of $99.52 billion in 2023. This trend underscores the increasing adoption of composite materials across various sectors, driven by their advantageous properties and the continuous advancements in manufacturing technologies.
CDT is well-positioned to meet the rising demand with its state-of-the-art 500-tank plating lab in the United States. We can deliver high-capacity production of high-quality, reliable superabrasive tools. Additionally, with a larger plating facility currently being built in the United Kingdom, CDT is expanding its reach to better serve the global composites market with cutting-edge grinding solutions.
In conclusion, superabrasive grinding wheels play a pivotal role in the machining and fabrication of composite materials. Their ability to deliver precision, efficiency, and longevity makes them indispensable in the ever-evolving landscape of composite manufacturing. The use of composite materials is growing, and CDT is ready. Call us today to discuss how our precision grinding solutions can enhance your production process.
Celebrating Our Apprentices
Apprenticeships at CDT offer hands-on experience, critical skills, and leadership opportunities—more than training, they’re a launchpad for a lifelong career.
CDT Ltd.'s current and former interns (left to right): Corey Lloyd-Jones, Joe Bowles, Stephanie Hughes-Jones, Daniel Hughes-Jones, and Rhys Butler.
Investing in the Future: Celebrating Our Apprentices for National Apprenticeship Week
At Continental Diamond Tool (CDT), we take great pride in nurturing the next generation of engineers through our apprenticeship programs. In celebration of National Apprenticeship Week in the U.K., we’re highlighting the inspiring journeys of five apprentices at our manufacturing center in Wales. Read on to see how these talented individuals have developed their skills, grown within the company, and are shaping the future of engineering.e.”
From Apprentice to Supervisor – Joe Bowles’ Journey
Joe Bowles began his career with Continental Diamond Tool Ltd. in September 2007 as an engineering apprentice. Over the years, his dedication and willingness to learn saw him progress into new roles, gaining invaluable experience along the way. Today, he is the Supervisor of the Grinding Department, where he leads a skilled team and ensures high standards of quality and precision.
Reflecting on his journey, Joe shares:
"From an apprentice 17 years ago to a supervisor, my path has been driven by hard work and the support of a company that values growth, innovation, and investment in people. I look forward to furthering my career with CDT and being part of its bright future."
Joe’s success is a testament to the long-term benefits of apprenticeships, illustrating how they can open doors to leadership and career progression.
Daniel Hughes-Jones – A Key Player in CNC Machining
Daniel joined CDT Ltd. in March 2021, quickly making an impact in the CNC Machining Department. He successfully completed his HNC in Engineering, further strengthening his knowledge and technical expertise. Now, as a key team member, he operates multiple CNC machines and plays an important role in training new apprentices.
"My apprenticeship at CDT provided me with vital knowledge and a developed skill set, and I’m grateful to pass on my knowledge and experiences to the next generation of apprentices." – Daniel Hughes-Jones
Daniel’s ability to mentor new apprentices showcases the value of experienced employees sharing their knowledge, ensuring a strong and skilled workforce for the future.
Corey Lloyd Jones – Building a Strong Foundation
Corey started his apprenticeship with CDT Ltd. in September 2023 and is currently in his second year, working towards his HNC in General Engineering while also completing a Level 3 NVQ. With a strong ambition to learn, Corey is eager to develop his expertise across multiple machines and broaden his engineering knowledge.
"After finishing my apprenticeship, I would like to progress further within the company and learn more skills on more machines. I chose this career path as it looked like a good challenge. I am doing the general engineering HNC course because it opens up a lot of opportunities for me in the future, rather than having just mechanical or electrical HNC." – Corey Lloyd Jones
Corey’s enthusiasm for engineering showcases how apprenticeships provide a solid foundation for career growth, allowing young professionals to tailor their learning to suit their ambitions.
Rhys Butler & Stephanie Hughes-Jones – The Next Generation of Engineers
Rhys Butler and Stephanie Hughes-Jones, Daniel’s younger sister, are the newest members of CDT Ltd.’s apprenticeship program, having joined in September 2024. Though early in their careers, both are already embracing the challenges and opportunities that come with learning on the job.
Rhys shares his thoughts on his apprenticeship so far:
"I've been on my apprenticeship for around seven months now, and I've thoroughly enjoyed it because it has provided hands-on experience, and a deeper understanding of how complex systems come together. The opportunity to apply theoretical knowledge in real-world settings has been both challenging and rewarding. I've gained valuable skills in problem-solving, teamwork, and technical expertise, which have made me more confident in my abilities. Looking ahead, I would love to further develop my expertise in engineering and continue to grow in a role where I can contribute to impactful projects." – Rhys Butler
Stephanie, who was drawn to engineering for its balance of hands-on work and intellectual challenge, shares her experience:
"I chose engineering because I like jobs that are both physically challenging and mentally interesting. My apprenticeship helps me improve my skills as a machinist while giving me chances to keep learning and growing." – Stephanie Hughes-Jones
Their journeys emphasize how apprenticeships provide real-world experience, technical expertise, and career-building opportunities from day one.
Apprenticeships are more than just training—they’re a launchpad for a successful career. They provide a solid foundation for career progression, hands-on experience, and the opportunity to develop vital skills in a fast-paced, innovative environment.
The apprentices above are prime examples of what can be achieved through dedication, hard work, and the right support. From those just starting out to those who have grown into leadership roles, their journeys highlight the value of apprenticeships and the opportunities they create.
👉 Interested in an apprenticeship or know someone who is? CDT Ltd. works closely with Coleg Llandrillo to identify promising candidates for our highly competitive engineering apprenticeship programme. Each year, we offer placements to 2 to 3 students. The next apprenticeships will begin in September 2025. If you’re interested, we encourage you to explore Coleg Llandrillo’s Engineering Programme as the best route to be considered for a future opportunity with us. Learn more about Coleg Llandrillo here: https://www.gllm.ac.uk/
Continental Diamond Tool Limited (CDT Ltd.), based in Kinmel Bay, Rhyl, U.K., is the European subsidiary of Continental Diamond Tool Corporation, headquartered in New Haven, Indiana, U.S.A. For more than 40 years, CDT Ltd. has been a leader in diamond rotary dresser technology, originally operating as Consort Precision Diamond. Since joining CDT, the company has expanded its product line, delivering high-performance diamond plated grinding wheels and other premium superabrasive products to customers worldwide.
2025 President's Message: Reflecting on Growth and the Future
Discover how Continental Diamond Tool's 2024 investments in people, processes, technology, and infrastructure are paving the way for enhanced customer solutions in 2025.
As we usher in 2025, Continental Diamond Tool is proud to reflect on an incredible year of progress and innovation. In this video update, CDT’s President, Nick Viggiano, shares his gratitude and insights, highlighting the milestones and lessons from the past year.
Strong Partnerships: Driven by GRIT
Thanks to the unwavering support of our customers and suppliers, CDT has thrived since 1973. We are grateful to our loyal partners who have been instrumental in making CDT an American manufacturing success story. Guided by our GRIT: Global, Responsive, Innovative Team, being a committed partner remains central to our mission as we deliver superior superabrasive solutions for advanced applications across the world.
2024 Highlights: Advancing to Better Serve You
In 2024, our focus was on making internal improvements to better serve you — our customers. By investing in people, infrastructure, and technology, we strengthened our ability to deliver the precision and quality you expect from us. Here are a few key achievements:
Strategic Leadership: Under the leadership of our new CEO, Brian VanHall, we are strengthening our strategy, structure, and systems to ensure your needs are met with efficiency and excellence.
People-Centered Investments: Our strongest competitive advantage is our people. By attracting and cultivating top talent, we have assembled a team that is committed to making every interaction and product surpass your expectations.
State-of-the-Art Expansion: Our newly expanded 72,000-square-foot Technology Center in New Haven, Indiana, will be a platform for the latest advancements in machining, inspection, and quality control for unmatched product reliability.
Global Growth: With a move underway in Wales to a larger 30,000-square-foot building, we are further increasing our capacity to provide timely support and advanced solutions to a global market.
Lessons Learned: Elevating the Customer Experience
In 2024, we put our focus on what truly matters:
People: By placing the right people in the right roles, our team is equipped and empowered to meet your needs with expertise and responsiveness.
Development: Continuously investing in our people, processes, and products delivers better, more innovative solutions for you.
Quality: Enhancing processes that assess, analyze, and assure product quality, performance reliability, and customer satisfaction.
Looking Ahead to 2025: Focused on You
As we step into the new year, we are energized by the opportunities ahead. We remain deeply committed to our mission of delivering unparalleled solutions while fostering strong partnerships with our customers and suppliers. Our gratitude extends to every individual who contributes to our success, from the dedicated CDT team to our trusted partners.
From all of us at Continental Diamond Tool, we wish you in this dynamic world of manufacturing a prosperous and fulfilling 2025.
You can find CDT’s latest product innovations, expert grinding tips, and company news by visiting our blog, watching our videos, or connecting with us on LinkedIn. Together, let’s make this another year of partnership and success!
How CDT Works Together to Serve Customers Better
Behind every precision tool is a team—and surprising fun facts! Guess who are neighbors, or how many interviews we conducted last year. Read the article to learn more.
Staying competitive in precision manufacturing is about more than customizing the most advanced grinding tools and cutting-edge dressing technology—it’s also about the people and processes that ensure everything runs smoothly. At Continental Diamond Tool, many departments work together to deliver exceptional products and service to our customers. In this blog, we’re highlighting the key players whose efforts behind the scenes uphold our standards of reliability and customer satisfaction.
Let’s explore how our departments—from Executive Leadership to Human Resources, Purchasing, Marketing, IT, Finance, and Administration—play a crucial role in better serving our customers.
Executive Leadership: Setting the Vision
Leadership is the compass that guides a company toward success. Our Executive Leadership team sets strategic direction, defines goals, and ensures alignment of our department initiatives with market demand. From expanding facilities for electroplating with diamonds to encouraging development of custom hybrid bonds, our leadership fosters a culture of innovation, reliability, and customer focus.
Fun Facts:
Continental Diamond Tool is a second-generation family-owned company. CDT President Nick Viggiano succeeded his father, Ray, who founded the company in 1973. Under Nick’s leadership, the company has become the fastest growing superabrasives company in North America.
Did you know CDT President Nick Viggiano and CEO Brian VanHall are neighbors? The family ties and neighborly spirit run deep in our organization.
Human Resources: Building a World-Class Team
The foundation of any successful company are people. Human Resources Director, Jenni Long, ensures we hire top talent, provide continuous training, and foster a positive workplace culture. By focusing on employee engagement and growth, HR builds a motivated, skilled team dedicated to excellence.
Fun Facts:
This month, Jenni single-handedly processed the open enrollment benefit selections for more than 180 employees. Plus, she’s conducted over 250 interviews this year.
We’re hiring! Join Jenni’s team as an HR Generalist. Click here to apply.
Purchasing: Ensuring Quality and Consistency
In precision manufacturing, quality starts with sourcing the right materials. The Purchasing department ensures our production teams have access to high-quality raw materials and supplies to meet exacting standards. Strong vendor relationships and effective inventory management keep operations efficient and cost-effective.
Fun Facts:
Inventory management is one of many functions this department handles. With more than 2,500 SKUs in our system, Dan Kortenber and Matt Sheehan ensure materials are always available to meet our customers' needs on time.
In his spare time, Matt referees both college and high school basketball.
Marketing: Connecting with Customers
Understanding customer needs is the first step to delivering outstanding service. Our Marketing team identifies trends, gathers feedback, and communicates the value of our products. From digital campaigns to trade shows, they ensure customers are informed, engaged, and confident in our expertise.
Fun Facts:
The Marketing team led by Carrie Fisher manages more than 150 projects at any given time, ensuring CDT stays innovative, engaged, and ahead of industry trends.
Did you know Marketing Generalist Stacy Viggiano is the wife of CDT President Nick Viggiano? In her role, she wears many hats, bringing her creativity, humor, and authenticity to the company’s communication initiatives.
IT: Empowering Precision with Technology
In today’s digital world, technology is integral to success. Our IT team ensures seamless communication, data security, and operational efficiency by managing robust networks and advanced software. Their work keeps CDT at the forefront of innovation, enabling precision and speed for our customers.
Fun Facts:
IT Director Jeremy Geier bridges the networks between our U.S. and U.K. facilities, enabling seamless and secure order processing and tracking between facilities.
Off the clock, Jeremy coaches the local, CDT-sponsored high school softball team in New Haven.
Finance: Driving Strategic Resource Management
The Finance team led by CFO Mike Brouwer ensures every resource decision is grounded in sound financial planning. They develop budgets, manage expenses, and forecast trends, allowing CDT to invest in resources needed for growth and innovation. Their expertise helps us maintain competitive pricing without compromising quality.
Fun Facts:
Did you know Accounting Manager Joseph Norris has been with CDT for 20 years? Joseph started as a part-time employee working with manual lathes on the shop floor. In 2014, he moved into a full-time role within the Electroplated team. In 2017, Joseph joined the Finance team and is instrumental with the many hats he wears.
Mike and Joseph both enjoy coaching sports outside of work.
Administration: Keeping TEAMS Running Smoothly
Behind every smooth operation is a team ensuring day-to-day activities run without a hitch. The Administration team provides essential support across departments, coordinating schedules, managing communications, and ensuring every detail is handled efficiently.
Fun Fact:
Amy Frecker at our front desk personally answers an average of 50 or more calls every day.
A Unified Effort for Superior Customer Service
Creating custom grinding tools for precision manufacturing applications is complex, but it’s made possible by the collaboration of diverse departments working toward a common goal: customer satisfaction. At Continental Diamond Tool, every team plays a important role in meeting and exceeding the demands of the industries we serve.
Whether it is our groundbreaking work in our grinding lab at CDT New Haven or our industry-leading processes in our 500-tank lab for electroplating with diamonds, it’s not just about what we make—it’s about how we work together to serve you better.
You’ll notice we share a love of teamwork and a spirit of camaraderie at CDT that extends beyond our workdays. Many of our team members coach or referee sports outside the office—be it basketball, softball, or other athletic programs—carrying forward the same principles of sportsmanship, collaboration, and high performance that we bring to serving our customers. These values are core to who we are, both on the shop floor and on the playing field.
Have questions about how we can help with your precision manufacturing needs? Contact us today to learn more about our commitment to excellence.
CDT’s Lab Evaluates Blaser Coolants in Flute Grinding Applications
Check out how we tested Blaser coolants on EVO hybrid bond wheels in CDT’s grinding lab to see which best enhances cutting, tool life, and quality in precision flute grinding.
At Continental Diamond Tool (CDT), we pride ourselves on pushing the limits of grinding technology. In one recent trial, The Grinding Chronicles team has partnered with Blaser Swisslube to test the performance of different coolants on our EVO hybrid bond grinding wheels. This experiment in CDT’s grinding lab aims to determine which coolant best enhances cutting performance, tool life, and workpiece quality in precision flute grinding applications.
Parameters for Success
Leading this effort is CDT Application Engineer Harrison Sheldon and CDT Engineering Consultant Jon VanSant, who are testing three different Blaser fluids under controlled conditions. They are measuring key parameters such as power, force, and grinding wheel wear while closely inspecting the visual quality of the workpiece for signs of burn or other surface finish issues.
“Our focus is on how the grinding wheel cuts, wears, and the resulting workpiece quality,” Jon explains. “By measuring parameters like power and force, we aim to collect data that can objectively compare the performance of each coolant under consistent conditions.”
Three representatives from Blaser joined Harrison and Jon last week at CDT’s lab: Senior Application Engineer Brett Reynolds from the New York plant, and Grinding Business Development Managers Tom Cappadona, also from New York, and Simon Stalder, representing Blaser’s headquarters in Switzerland. For this trial, Blaser has provided the coolant fluids, while CDT is supplying the EVO hybrid bond grinding wheels and the data collection equipment in the grinding lab. This setup ensures a comprehensive, scientific approach to analyzing performance with these coolants.
“When Tom approached us about this trial, we saw an opportunity to try something new with the equipment in our grinding lab,” says Harrison. “We’re excited to see how each formula stacks up to help the team at Blaser guide their customers in optimizing their process.”
Simon Stalder expressed his enthusiasm for the trial results, eager to share the findings with his engineering team in Switzerland. These results will provide valuable insights into how Blaser’s latest coolant technology enhances grinding performance and efficiency. As a global leader in metalworking fluids, Blaser delivers tailored formulas for every material, industry, and application.
Benefits of a Dynamic Testing Environment
The dynamic testing environment in CDT's grinding lab allows Harrison and Jon to adjust parameters on the fly, testing variables such as feed rate while maintaining consistent wheel speed. This enables them to evaluate the optimal feed rate range for each coolant type.
“One key advantage of running trials in the lab is the ability to collect objective data in controlled conditions,” says Jon. “Unlike in the field, where varied operator techniques can affect outcomes, our lab setting allows us to isolate variables and focus on actionable insights.”
While Blaser has come to CDT's lab primarily for the technical instrumentation and grinding know-how of our team, customers do not have to travel to take advantage of the lab’s capabilities. “CDT’s grinding lab is exceptionally flexible due to its portability. We frequently gather data directly from our customers’ processes by installing equipment at their site and analyzing it in our lab,” Harrison notes, “or we can simulate their operations on our machines and collaborate remotely to tweak their process.”
The expertise of Blaser’s application engineer, Brett Reynolds, has also been instrumental in these trials. “Brett brings a deep understanding of Blaser’s fluid formulation and their customer applications, which complements our grinding expertise,” adds Jon.
Trials on the Walter Helitronic Machine
As a 5-axis tool and cutter grinder, the Walter Helitronic is a purpose-built machine that is a centerpiece in CDT’s grinding lab and perfect for trials like this. Its versatility and precision are critical for evaluating different grinding configurations.
“The Walter machine is capable of thousands of functions, but it’s most commonly used for round cutting tools, making it perfect for flute grinding trials with our EVO Hybrid Bond fluting wheels,” Harrison says. “Its high precision, repeatability, and compatibility with advanced cooling systems make it the ideal platform for these tests.”
Jon elaborates, “The Walter allows us to make real-time adjustments to speed, feed rate, and pressure, which is essential for testing performance during these trials. Its automation and sensitive readings ensure accurate, repeatable results.”
The team at Blaser is currently reviewing the data gathered from last week’s trial and discussing how to incorporate the insights into future marketing and product development.
Accessing Our Grinding Lab Services
At CDT, we believe in the importance of real-world testing to optimize grinding processes and improve part quality. Our grinding lab is available for trials like these, whether you’re testing new grinding wheels or assessing some other metric of performance.
“Our team’s diverse areas of expertise ensures we can accommodate unique customer needs,” Harrison shares. “Whether it’s conducting tests in our lab or traveling to your site, we provide valuable solutions tailored to each challenge.”
If you’re interested in running a grinding trial with CDT, contact us with details about your process. We can recreate it in our lab or connect at your facility to gather data. From there, we develop testing parameters, share results, and make tailored recommendations for specific tools and production settings.
Learn more about Blaser Swisslube at:
Linkedin.com/company/blaser-swisslube
Youtube.com/user/blaserswisslube1