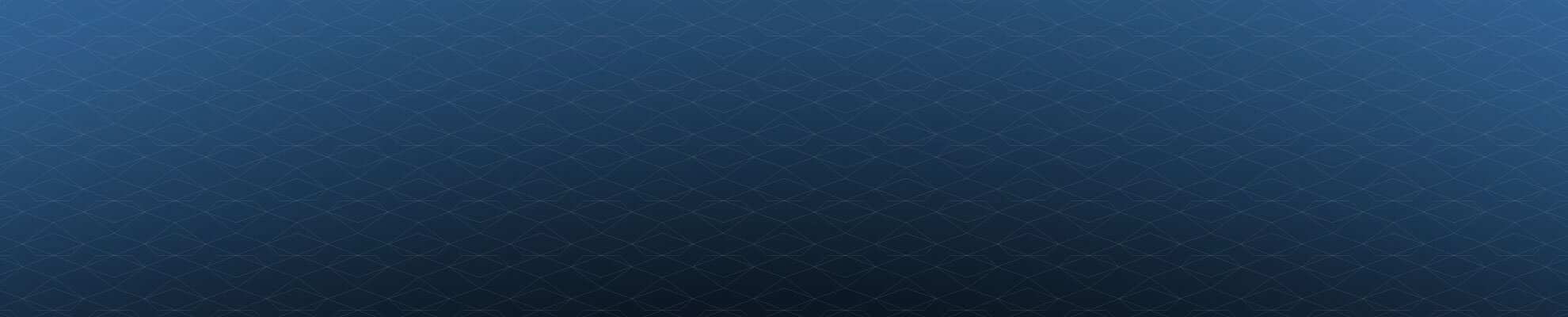
News and Resources
Browse by Category
Browse by Product
- All Dressing Products
- All Grinding Products
- CBN-Diamond Superabrasives
- Conventional Abrasives
- Diamond Lapping Compounds
- Diamond Rotary Dressers
- Diamond Stationary Dressers
- Hybrid Bond Grinding Tools
- Metal Bond Grinding Tools
- Plated Grinding Tools
- Resin Bond Grinding Tools
- Vitrified Bond Grinding Tools
True Blue Performance in Conventional Grinding
CDT demonstrated Blue Moon TZ wheels from Krebs & Riedel on the Studer S33. Learn how these grinding wheels improve form retention, power use, and grind quality.
When you’re looking for ways to improve grinding performance, the ultimate factor comes down to value: how can you get the precision and efficiency you need while managing costs? That’s where advanced conventional abrasives often excel.
With certain applications, classic abrasives like silicon carbide and aluminum oxide deliver strong results at a lower upfront investment compared to superabrasives. For shops that don’t require the extreme speeds or precision of diamond and CBN, conventional wheels remain a smart, cost-effective choice.
While these wheels haven’t changed much in a hundred years, a few innovators are pushing the boundaries with scientifically engineered abrasive grains. One next-generation solution is the Blue Moon™ TZ high-performance grinding wheel from Krebs & Riedel, designed to bring greater efficiency, precision, and consistency to your process. Watch this video or read the following article to learn more.
Features and Benefits of Blue Moon™ TZ
Continental Diamond Tool is proud to bring to its customers the Blue Moon™ TZ, which represents the next evolution in the Blue Moon product line developed by the R&D team at Krebs & Riedel. This conventional grinding wheel incorporates a precision-shaped trapezoid abrasive grain that delivers maximum performance through high cutting efficiency, low thermal load, and outstanding profile retention.
Designed to perform under long contact lengths and demanding applications, the Blue Moon TZ offers:
Very low risk of overheating while grinding
High removal rates leading to short grinding times
Self-sharpening abrasive grain for consistent performance
Extended dressing intervals for improved wheel life
Reduced cost per unit through higher efficiency
Applications range from deep pass and centerless grinding to raceway and profile grinding of large gear modules. It is a versatile solution across aerospace, automotive, agricultural engineering, wind energy, hydraulics, and bearing production.
Blue Moon TZ’s Proven Performance
At the United Grinding Precision Summit in July 2025, Continental Diamond Tool was happy to bring this innovative wheel technology to the North American market. During a live demonstration on the Studer S33 cylindrical grinder, the Blue Moon™ TZ wheel was put to the test on steel specimens commonly used for tensile strength testing. This setup allowed attendees to see first-hand how the wheel handles demanding applications such as thread grinding where precise form and surface finish are critical. As the S33 shaped these test specimens, the Blue Moon™ TZ delivered stable performance with reduced heat build-up, extended form retention, and consistent results over long grinding passes.
At the event, CDT Senior Application Engineer Paul Christy shared his perspective on why this technology stands out:
“The Precision Summit has been exciting. Many people have been asking questions, and we’ve had some great customer engagement,” says Paul. “We’re running Blue Moon technology. It has a ceramic-shaped grain, specifically formulated for the steel grinding that they were doing here.”
During his presentation, Paul emphasized that the benefits translate directly to shop-floor productivity:
“The Blue Moon technology gives us lower power consumption and better form retention. In this application, where we’re holding thread forms, the wheel provides excellent life and the consistent form retention required to grind threads.”
The Practical Advantage of conventional abrasive grinding wheels
For many manufacturers, conventional abrasives like the Blue Moon™ TZ offer a cost-effective solution with impressive productivity gains. Grinding shops benefit from high removal rates, reduced thermal load, and extended dressing intervals, all of which help shorten cycle times and improve efficiency.
At CDT, we work with customers to match the right wheel to the right process. While superabrasive wheels made of diamond or CBN deliver the highest levels of performance and longevity, there are certain applications where the cost-per-part savings of superabrasives don’t fully materialize. In these cases, conventional options like the Blue Moon™ TZ strike the right balance between performance and upfront investment.
With lower power consumption, reliable form retention, and strong economic efficiency, the Blue Moon™ TZ demonstrates just how far conventional abrasives have advanced. For applications from raceway grinding to large gear profiles, it’s a proven solution that helps manufacturers achieve results while managing costs.
See us Live at Motion + Power 2025
Manufacturers looking to explore the benefits of advanced conventional abrasives will have the opportunity to see CDT’s solutions first-hand at Motion + Power Technology Expo 2025. This event marks our first major showcase of Krebs & Riedel products since becoming their exclusive North American partner, as well as our public debut in the gear grinding market. On display will be the Blue Moon™ TZ alongside other Krebs & Riedel products and CDT’s Vitrified CBN wheels and Diamond Rotary Dressers, giving attendees a chance to see the full range of solutions we provide for gear and precision grinding applications.
Join us at Motion + Power 2025 to talk with our engineering team, see how our investment in the Burri PM550T enables precise custom profiling, and learn how CDT is helping manufacturers achieve faster turnaround, consistent results, and better overall grinding performance.
our Commitment to Excellence
At Continental Diamond Tool, we’re committed to helping customers choose the best abrasive solution—whether it’s conventional wheels like the Blue Moon™ TZ or our world-leading superabrasives—so you get the right balance of performance, precision, and long-term value.
We take pride in delivering not only advanced products but also outstanding customer service. Reach out by phone, email, or web form to learn how Blue Moon™ TZ can support your process. Contact us today.
Precision Grinding for the Semiconductor Industry
CDT’s custom wheels help grinding shops meet tight specs, reduce downtime, and machine tough materials for the components needed to make semiconductors.
From smartphones to satellites, semiconductors power modern life. But behind every microchip are precision equipment, advanced materials, and skilled technicians that make high-volume chip production possible.
For machining shops that support the semiconductor industry, quality is non-negotiable. These manufacturers play a key role in producing wafer chucks, dicing tool components, and structural parts that keep chip production running at scale. These components must hold tight tolerances and perform in high-heat, high-vacuum, and chemically aggressive environments.
At Continental Diamond Tool (CDT), our role is simple: support the grinding operations that keep this work moving. We manufacture superabrasive grinding wheels that hold spec, reduce downtime, and deliver consistent quality.
Pandemic Pressures on Semiconductor Production
The global chip shortage that began in 2020 wasn’t just a blip—it was a wake-up call. When demand for electronics surged and supply chains fell behind, everything from automotive production to medical device manufacturing slowed down.
What caused it?
Demand for electronics and cloud infrastructure spiked
Fabs, packaging plants, and ports were shut down
Capacity for advanced chips was limited and concentrated in a few regions
Some sectors canceled orders early and were left scrambling when demand came back
This perfect storm exposed just how fragile the semiconductor supply chain had become.
Semiconductors, Five Years Later: What’s Changed?
Since then, major investments have poured into rebuilding and expanding semiconductor capacity:
The CHIPS and Science Act is supporting new fabs in the United States, including Ohio, Arizona, and New York
Foundries like TSMC and Samsung are expanding beyond Asia to reduce geopolitical risk
Automakers have jumped into chip development and procurement to secure their own supply
Meanwhile, demand keeps rising—especially with the growth of AI and cloud computing. AI workloads from machine learning, real-time analytics, and generative models require advanced chips, high-bandwidth memory, and complex packaging. That demand has cascaded across industries—from data centers and robotics to autonomous vehicles and healthcare.
Meeting that demand isn’t just about making more chips. It also means meeting tighter tolerances, ensuring reliability, and reducing variation across the supply chain. While new fabs are coming online, other parts of the process—like grinding and machining—are just as critical.
Grinding shops produce the wafers, tooling, and support components that make high-performance chipmaking possible. At CDT, we manufacture grinding wheels that are built for the job.
Precision Grinding: The Quiet Backbone of Semiconductor Manufacturing
Semiconductor fabs require tools made from tough materials like tool steels, ceramics, carbides, and coated alloys. Materials are selected for their strength, stability, and ability to handle heat and wear, but that also makes them challenging to machine.
Our customers specialize in grinding tight-tolerance components using surface, OD, and ID grinding. In the semiconductor industry, this often means working at the micro level—holding tolerances within ±0.0001” and achieving mirror-like finishes with no room for error. We support this detailed work with custom-engineered wheels that are:
Built for consistency – holding form over long production runs
Aggressive yet cool-cutting – to reduce heat distortion and burn
Tailored to the material – with bond and grit combinations suited for everything from hardened steels to fragile ceramics
Tackling Tough Materials with Superabrasive Precision
Semiconductor manufacturing is performed in clean rooms under extreme conditions with high heat, vacuum environments, reactive chemicals, and intense electric fields. Tools like etchers, deposition systems, and ion implanters must operate with micron-level accuracy that stays stable under pressure.
That’s why these tools are made of materials that offer:
Thermal stability to handle high processing temperatures
Mechanical strength to hold shape
Chemical resistance to survive plasma and gas exposure
For this work, grinding wheels must be capable of shaping and controlling difficult materials like plasma-resistant ceramics, hardened tool steels, and carbide-based coatings. On top of that, shops regularly face new materials engineered to improve thermal performance, erosion resistance, and particle control.
To machine these materials effectively, you need grinding tools that stay sharp, cut clean, and hold spec. Conventional abrasives can load up, overheat, and require constant dressing in these conditions, making them ill-suited for the task. On the other hand, CDT’s diamond and CBN wheels — made with resin, vitrified, hybrid, or metal bonds — are designed to handle these jobs with ease.
And what if a customer is working with a material that’s unfamiliar? That’s when we turn to the CDT grinding lab.
Custom Superabrasive Solutions Tested In-House
CDT’s in-house grinding lab is built to help customers test materials and validate wheel performance. Whether you’re running a new material or facing a recurring problem, we can help develop the right solution.
If you’re dealing with edge burn, profile loss, or surface finish issues on brittle materials, we’ll work with you to sort it out. We regularly work with advanced ceramics, silicon carbide, coated tool steels, and other materials that are now standard in semiconductor production. We use custom wheels and a controlled testing environment with the goal to help you dial in your process faster and avoid tying up valuable time and equipment on the shop floor.
Precision That Powers Progress
From wafer chuck carriers to dicing tool components, precision grinding shops keep semiconductor chip production running at scale. It’s not the work that happens inside the cleanroom—but it’s every bit as important.
At CDT, we know what’s at stake. As the industry moves toward thinner wafers, harder materials, and tighter specs, we’re here to help grinding teams produce parts that are consistent, efficient, and competitive. Our wheels are built for performance, long life, and lower cost per part.
Ready to Tackle Your Toughest Grinding Challenge?
From plasma-resistant ceramics to hard-coated steels, we know how tough these materials can be. We work directly with grinding shops to develop the right tool for the job.
Whether you’re qualifying a new material, scaling a high-volume part, or solving a surface finish issue, CDT delivers custom-engineered grinding solutions that help you move forward. Our in-house lab takes the guesswork out of testing and speeds up production.
Reach out to see how CDT can help with your next grinding challenge.
Profile vs. Surface Finish: Identifying the Limiting Factor in Your Grinding Process
Learn how to identify whether profile or surface finish is limiting your grinding process—and how to use that insight to reduce scrap and optimize performance.
Scrap is costly—both in time and materials. If you’re looking to improve quality and reduce waste, it’s essential to identify what’s holding your process back. In Episode 12 of The Grinding Chronicles, CDT Application Engineer Blu Conrad shares how measuring profile and surface finish can help pinpoint the root cause of your quality issues. Watch the video or read on to learn how to address these limiting factors and run a more efficient grinding operation.
The Grinding Chronicles - Episode 12
Why Your Parts Are Going Out of Spec — And How to Fix It: Part 1
Efficient grinding operations—especially at scale—depend on consistency to stay competitive. When parts start falling out of spec, the impact is immediate: lost time, wasted material, and rising costs. Two of the most common culprits are profile deterioration and surface finish breakdown. But how can you tell which one is actually limiting your process?
A targeted approach to tracking part quality can reveal the answer—and help you set the ideal dressing interval for your wheel.
Profile and Surface Finish: Understanding the Distinction
In grinding, profile refers to the macro geometry your wheel produces—the shape and dimensional accuracy of the part. Surface finish, on the other hand, captures the micro-level texture or roughness on the surface. Both play a critical role in quality, but they degrade differently and can indicate different underlying problems.
Track the Right Data
One of the most effective ways to diagnose which factor is causing your parts to fail is to measure both profile and finish at regular intervals. For example, take a measurement every five or ten parts and record that data alongside the volume of material removed.
Plotting those measurements on a graph—with volume ground on the horizontal axis and profile or finish on the vertical axis—will give you a clear picture of which element goes out of tolerance first.
“Whichever set of data crosses out of tolerance first—that’s your constraint,” says Blu Conrad, Application Engineer at CDT. “That tells you where your process is breaking down and where to focus your efforts.”
If profile is causing you to fall out of spec first, your dressing interval should be set based on that. If surface finish is the issue, your remedies need to shift toward surface-related variables.
If Profile is the Problem
When profile is the limiting factor, excessive force per grit is often to blame. This can occur when the wheel-work contact length is short, meaning fewer cutting edges are engaged and each grit is doing more work. Over time, this accelerates wear and throws the wheel out of shape.
In cases like this, upgrading to a more robust grinding wheel can help. A harder abrasive or more durable bond may provide better resistance to wear and extend the life of the wheel between dressing cycles.
But before you swap out tooling, it’s important to rule out other contributors—especially coolant. Inadequate coolant flow or misaligned nozzles can rapidly accelerate wheel wear and distort profile accuracy.
“It’s not always the wheel’s fault,” Blu explains. “Sometimes just optimizing your coolant delivery can make a huge difference in how long your profile holds.”
To learn more about effective coolant application, check out The Grinding Chronicles Episode 3, where Blu breaks down four key factors—velocity, flow, line placement, and temperature—and how each one affects wheel performance and part quality.
If Surface Finish is the Issue
In some processes, the surface finish goes out of spec before the profile ever does. This points to different limitations—often related to speed, feed, wheel dressing parameters, or wheel condition.
In an upcoming video later this year, we will walk through how to predict surface finish with a simple calculation and explain what changes you can make to improve results. Subscribe to our YouTube Channel to catch the release.
Make Your Dressing Interval Work for You
Scrap is always costly—but it’s also avoidable with the right analysis. By identifying whether profile or finish is the first to fail, you gain control over your process. You can set a purposeful dressing schedule that reduces unnecessary wheel wear, increases uptime, and keeps parts in spec for longer. After all, both profile and finish will eventually degrade—it’s not a matter of if, but when—so knowing which factor breaks down first lets you plan more strategically.
Need help dialing in your own dressing interval? Contact CDT’s Application Engineering team at TheGrindingChronicles@cdtusa.net or visit cdtusa.net/the-grinding-chronicles for more grinding insights.
Check out more videos from The Grinding Chronicles and follow CDT on Linked In for the latest news in grinding technology.
Breaking from the Conventional: How Vitrified CBN Wheels Excel on Studer Equipment
Vitrified CBN wheels improve performance, reduce downtime, and enable lights-out grinding on Studer machines. Learn more in CDT’s latest blog.
At Continental Diamond Tool, we frequently manufacture Vitrified CBN wheels for widely used grinding platforms such as the Studer S33, FavoritCNC, and S131r. While many operations still rely on conventional abrasives, Vitrified Bond CBN is increasingly the go-to solution for high-precision, high-volume grinding applications—and for good reason.
If your shop is pushing for tighter tolerances, longer tool life, or lights-out production, here's why this technology may be the right move.
Why Choose Vitrified CBN?
When grinding hardened steels and other ferrous materials, Vitrified CBN (Cubic Boron Nitride) wheels offer significant advantages over traditional abrasives like aluminum oxide, which are commonly used for similar applications:
100–300× Longer Wheel Life
Vitrified CBN outlasts conventional wheels by a wide margin, reducing the frequency of wheel changes and downtime.Tighter Tolerance Control
These wheels maintain form exceptionally well, ensuring consistent part geometry even across extended production runs.Cooler, Cleaner Cutting
The vitrified bond provides superior chip clearance and heat dissipation, minimizing the risk of thermal damage and improving surface finish.Ideal for Lights-Out Operation
Extended wheel life, consistent performance, and reduced need for manual intervention make Vitrified CBN wheels a great match for automated and lights-out environments.
“If you are dressing properly with a diamond rotary dresser, your vitrified CBN wheel will last a very long time—and you’ll produce high-quality parts at a great pace with little to no variation,” says Troy Giacherio, CDT’s Product Line Manager for Rotary Dressers.
Rotary Dressing Techniques for Vitrified CBN
Dressing is essential for maintaining wheel shape and exposing fresh cutting edges—but how often and how efficiently you can dress the wheel makes a big difference in productivity.
Conventional Abrasive Wheels
These wear down quickly and require frequent dressing to restore geometry and surface integrity.Vitrified CBN Wheels
Thanks to their exceptional wear resistance, these wheels require dressing far less frequently. When dressing is needed, rotary diamond dressers are the tool of choice.
At CDT, we manufacture rotary diamond dressers tailored to your process, whether using conventional or Vitrified CBN wheels. For vitrified applications, these dressers enable precise, programmable dressing that fits seamlessly into automated processes—reducing operator time and increasing repeatability.
“If you’re transitioning from conventional abrasives to CBN—or if you’re seeing issues like burn or finish patterns—you might not be dressing your wheel correctly,” says Troy. “If your power draw starts creeping up or you see changes in surface finish, that’s your cue—it’s time to dress the wheel.”
Want to learn more about dressing Vitrified Bond CBN wheels with a rotary diamond dresser? Watch Episode 5 of The Grinding Chronicles, where Troy breaks down key dressing parameters like velocity ratio, overlap ratio, and depth of dress.
Top Signs You Should Be Using Vitrified CBN Wheels Instead of Conventional Abrasives
If your current process is held back by:
Frequent dressing and wheel changes
Inconsistent size or surface finish
Excessive heat generation
Limited machine uptime or operator availability
…it may be time to evaluate a Vitrified CBN solution. Especially when paired with capable machines like the Studer S33, FavoritCNC, and S131r, CBN technology can unlock new levels of efficiency and reliability.
“When switching from conventional wheels to vitrified CBN wheels, we’ve seen dress intervals go from a few parts to hundreds,” says Troy. “The key is balancing efficiency with consistency to get the most life out of your wheel and performance from your process.”
Whether you’re looking to reduce cost per part, improve part quality, or enable lights-out production, switching to Vitrified CBN may be the upgrade your process needs.
See CDT Wheels in Action: United Grinding Precision Summit
Curious how Vitrified CBN performs in a real-world environment?
Join us July 29–30 at the United Grinding Precision Summit, where CDT has supplied wheels on these three Studer machines: the S33, FavoritCNC, and S131r.
You’ll have the opportunity to meet our engineers, discuss dressing techniques and process parameters, and explore how customized Vitrified CBN wheels can enhance your operations.
👉 RSVP now at united.grinding.com/theprecisionsummit2025
Making the Switch from Conventional Abrasives to CBN
Ready to explore Vitrified CBN Wheels and Diamond Rotary Dressers? At CDT, our sales team includes dedicated process engineers who work directly with customers to assess grinding setups, identify improvement opportunities, and develop optimized solutions tailored to today’s most advanced platforms.
Whether you're running a Studer S33, FavoritCNC, or S131r, or comparable machines from Kellenberger, Bryant, or Okuma, CDT has the tools and technical expertise to support your production goals. We help manufacturers across industries transition from conventional abrasives to high-performance vitrified CBN—delivering better form retention, reduced dressing, and longer wheel life.
📞 Call us at 1-800-443-6629 or contact us online to get in touch with a CDT expert and find the right grinding solution for your application.
Improving Part Quality and Reducing Costs in Medical Grinding
Discover how CDT helps medical manufacturers improve part quality, reduce scrap, and cut costs with custom-engineered grinding wheel solutions.
In medical manufacturing, even small inconsistencies in components like implants, surgical tools, or drill bits can lead to costly failures and compromised safety. Precision and reliability aren't just goals—they're required for industry standards and FDA approval. Yet it’s common for manufacturers to struggle with persistent issues like inconsistent surface finishes, excessive burr formation, and unpredictable wheel performance that increase scrap and labor costs.
At Continental Diamond Tool (CDT), we understand the root causes behind these challenges and help medical manufacturers overcome them through targeted, reliable, custom engineered grinding solutions.
One of CDT’s biggest strengths is how closely our sales and engineering teams work together—often as the same people. Many of our team members serve dual roles, combining application expertise with customer-facing support, so the person helping you select your wheel also understands how to fine-tune it for maximum performance.
“The most important factor for medical suppliers is part quality,” says Blu Conrad, CDT Application Engineer who specializes in medical manufacturing support. ”When we see issues like burrs, poor finishes, or short wheel life, it’s usually a sign that there is a problem with the wheel or process set up. We can help you fix that.”
CDT’s vitrified CBN wheels provide reliable, repeatable performance when grinding complex medical components like surgical drill bits.
Is Your Grinding Process Hurting Your Productivity?
Do you face problems like:
Inconsistent surface finishes and part quality?
Excessive manual deburring labor due to excessive burr formation?
Short wheel life and frequent dressing?
Difficulties maintaining tight tolerances and precise geometries?
These problems often come down to using a grinding wheel or machine settings that are not optimized for your application. At CDT, we take a hands-on, data-driven approach to help you pick the right wheel and adjust your set up — so you can count on consistent, reliable performance that fits the way you work.
Specialized Grinding Wheels Designed for the Medical Industry
CDT specializes in designing, developing, and delivering custom-engineered diamond and cBN grinding wheels for all types of medical manufacturing. While we have seven unique product lines, there are three distinct grinding wheel types that we commonly specify for medical manufacturers:
Plated Wheels: Perfect for roughing operations, plated wheels maintain precise profiles — like those required on complex medical implants and surgical cutting tools — for the entire life of the wheel with no dressing required. We also offer a strip and replate program that reuses your wheel core and reapplies the abrasive—restoring it to like-new condition at a fraction of the cost.
Vitrified CBN Wheels: Often found in finishing operations, these wheels minimize burr formation and ensure consistent, high-quality results. Best used with machines featuring onboard wheel dressers, vitrified cBN wheels are particularly cost effective for manufacturers who are taking advantage of lights out operation. CDT also manufactures the onboard Diamond Rotary Dressers that keep these wheels efficiently grinding at peak performance.
Hybrid Bond Wheels: A variation of CDT's resin bond grinding wheels, our EVO Hybrid Bond formula provides excellent shape retention, consistent free cutting, and reduced heat buildup. We often recommend this product line for finishing medical parts on machines where operators manually dress the wheel.
“We’ve helped customers reduce cycle times by up to 20%,” recalls Blu. “And just as important, we’ve been able to significantly cut down on manual deburring labor—especially when they switch to vitrified CBN wheels paired with onboard wheel dressers that run cleaner and cooler with less downtime than manual dressing.”
Proven Solutions Across Leading Machines and Materials
CDT grinding wheels are designed to perform on leading medical manufacturing machines, including platforms from Walter, Rollomatic, Schütte, Starr, and Strausak. Whether you're a large OEM or a contract manufacturer, we tailor each wheel to your production requirements.
“Medical components are often made from stainless steels like 17-4 or 455, which can be tricky,” Blu explains. “They’re gummy and prone to burrs. That’s why we pay close attention to both the material and the machine setup when we spec a wheel.”
Our team takes material properties—such as ductility and hardness—into account when developing wheels. Stainless steels are particularly prone to heat buildup and burrs. With the right wheel and setup, we can significantly reduce these effects, helping customers reduce scrap and minimize secondary deburring processes.
Your Trusted Guide for Long-Term Success
CDT isn't just a wheel supplier; we're your strategic partner in precision grinding. Our team proactively collaborates with you from new product prototyping to established production optimization, ensuring your processes are finely tuned and continuously efficient.
We can also help you evaluate machine options—well before it's time to order your grinding wheel. “It’s more common than it should be for us to get called in after a machine is already purchased,” says Blu. “We love to be part of the conversation earlier because features like onboard dressers make a huge difference. We’ve had customers retrofit onboard dresser technology just to unlock the full performance of a vitrified CBN wheel.”
In addition, our grinding lab is a valuable resource for customers. They can safely explore the performance limits of their wheels and identify opportunities for improvement without interrupting production or incurring the cost of scrap and downtime. We also offer a portable lab to diagnose system inefficiencies directly at the production site.”
From implants to surgical tools, CDT Application Engineer Blu Conrad specializes in helping medical manufacturers improve precision, reduce scrap, and save time. Reach out today.
Why Medical Manufacturers Trust CDT
Medical manufacturers consistently choose CDT because we deliver:
Rapid turnaround and reliable lead times
Dependable quality, performance, and cost-efficiency
Hands-on technical support, troubleshooting, and training for your operators
Expert R&D engineering services focused on helping you succeed
Don’t let grinding wheel issues compromise the quality or productivity of your medical manufacturing operations. Take control of your process and partner with CDT to confidently meet your critical manufacturing goals.
Ready to transform your grinding process? Contact Blu Conrad and others on the CDT sales team today for a free consultation and quote. Call 1-800-443-6629 or visit our webform to get started.
Solving Grinding Challenges in Advanced Ceramics with Superabrasive Solutions
Discover how custom-engineered superabrasive grinding wheels improve precision, reduce scrap, and boost efficiency in advanced ceramic manufacturing.
Working with advanced ceramics? Then you know the challenges: parts that chip under pressure, tools that wear out fast, and long cycle times that slow you down.
Whether you’re machining zirconia for aerospace, silicon carbide for electronics, alumina for medical components, or glass for food and beverage applications, the goal is the same—hit tight tolerances without sacrificing efficiency.
At Continental Diamond Tool (CDT), we understand the pressure—balancing precision and productivity, maintaining a competitive edge, and ensuring employee safety and customer satisfaction through an unwavering commitment to quality and best practices.
That’s why our superabrasive grinding wheels are engineered not just to meet specs, but to solve real manufacturing challenges. Our role is to support you with tools that cut downtime, reduce scrap, and maximize productivity—because in your business, reliability is everything.
The Problem: Time, Tool Life, and Surface Integrity
Ceramic materials are notoriously hard and brittle. With the wrong grinding setup, you risk:
Microcracks and subsurface damage
Excessive wheel wear
Long grinding cycles that reduce throughput
If your process isn’t delivering the results you need, there are many variables to check out—feeds and speeds, coolant delivery, dressing frequency. But among these, one of the most powerful levers is your grinding wheel.
Not all grinding wheels are created equal. Traditional wheels that were designed for grinding metal—even some diamond and CBN options—often fall short when used on ceramics.
Metals have distinct properties that react to heat and stress very differently than ceramics, so designing a grinding wheel that is optimized specifically for the ceramic material you are grinding will set you up for the best results.
The Solution: Tackling Challenges with Advanced Bond Technologies
That’s why CDT develops advanced vitrified and hybrid bonds—engineered specifically for ceramics—to handle extreme hardness, reduce power consumption, and maintain consistent performance over time. Our engineering team has worked with leading global industries to:
Reduce grinding forces by up to 30%—less heat, less damage
Cut cycle times in half—to exceed production targets
Increase tool life up to 20x—because every wheel change costs time and money
Whether you're grinding alumina, zirconia, silicon nitride, or another ceramic, our custom bond systems help you maintain surface integrity while keeping production moving
Purpose-Built Tools for Your Machines
There are countless combinations of wheel types and machine settings that can technically get the job done—but only a wheel engineered for your application and material in mind will truly maximize output, consistency, and profitability.
CDT product engineers design custom wheels for the leading machines in your facility, including:
Round Tool grinding (e.g., Anca, Rollomatic, Star)
Surface and Blanchard grinding (e.g., Okamoto, ELB, DCM)
Cylindrical & ID grinding (e.g., Studer, Toyoda, Landis)
Double disk and fine grinding (e.g., SpeedFam, Supfina)
Need unique geometries? We engineer wheels with fluting, coolant holes, cross-cutters, and flat-bottom drills to meet your exact requirements. We’re here to help you move beyond trial-and-error to get dialed-in results from the first part to the last
Tools Built for High-Performance Lines
Your production line is fast, automated, and precise—your tooling should be too. CDT supports modern machining environments with:
Multi-axis CNC compatibility
Rotary dressers for automated operations
Through-spindle and high-pressure coolant systems
High-speed spindle compatibility for ID grinding
We don’t just supply grinding wheels—we engineer solutions that integrate seamlessly into your process. Our application engineers can work with you—on-site or remotely—using data-driven analysis to fine-tune your settings for improved performance. Click here to learn more about our portable grinding lab, designed to collect real-time data directly from your machine—right at your facility.
Risk-Free Innovation: Partner with CDT
Switching tooling vendors is a big decision—and we don’t take that lightly. That’s why CDT makes the process transparent, collaborative, and low-risk. Our engineers work closely with your team to define clear success metrics and test parameters up front, so you know exactly what to expect before making any changes.
With over 50 years of experience and more than 70,000 unique tools engineered for over 5,000 customers, we’ve seen—and solved—a wide range of grinding challenges. Whether you're facing issues with surface finish, throughput, or wheel wear, our team brings proven expertise to help you move forward with confidence.
Let’s talk about your process—and how we can help you get more from it.
Call us at 800-443-6629 or visit cdtusa.net to get started.
Ceramic Grinding: Myth vs. Reality
CDT tests the grindability of ceramic vs. metal materials. Discover how ceramics like Silicon Carbide and Quartz really perform—and why the process matters.
Metals have historically dominated manufacturing, but ceramic materials are quickly gaining traction. While many machinists are comfortable grinding metals, ceramics can be intimidating due to their reputation for being difficult to work with. But is grinding ceramics really as challenging as it's made out to be?
In Episode 11 of The Grinding Chronicles, Application Engineer Harrison Sheldon tackles this misconception head-on. Watch the video or continue reading below to discover the realities of grinding ceramics and how their performance compares to metals.
The Grinding Chronicles - Episode 11
Debunking the Myth: How Difficult is it to Grind Ceramics?
Grinding ceramics often gets labeled as difficult partly due to perception. Manufacturing operations typically have more experience with grinding metals, making ceramics seem inherently more challenging. Machinists unfamiliar with ceramics may develop misconceptions and overlook the subtle nuances involved in grinding these materials.
Ceramics possess unique properties that contribute to their perceived difficulty. Technical ceramics generally fall into three main categories: oxides (like alumina and quartz), non-oxides (like silicon carbide and boron carbide), and composites. Composites combine metals and ceramics with particulate or fiber reinforcement to create a hybrid material. Zirconia Toughened Alumina (ZTA) is a type of Ceramic Matrix Composite (CMC).
Ceramics are typically strong and hard, yet brittle, due to their strong ionic or covalent bonds. These strong bonds create a rigid atomic structure, making ceramics resistant to deformation. However, this rigidity also means ceramics cannot easily absorb impacts or distribute stresses evenly, causing them to fracture or chip under stress instead of deforming as metals typically do. This brittleness makes them more challenging to grind, as the process must carefully control forces and temperatures to prevent microscopic cracks or breakage.
The Rise of Ceramics in Manufacturing
Ceramic materials have been used by humans for thousands of years, initially for pottery, construction, and decorative purposes. However, the modern adoption of ceramics in industrial applications took off significantly during the late-20th century, particularly with advancements in superabrasive grinding wheels that can process these extra hard materials. Ceramics began to replace metals in applications demanding high-temperature stability, corrosion resistance, low weight, and excellent wear characteristics. For example, ceramic bearings in automotive turbochargers and ceramic turbine blades in aerospace engines showcase their growing importance in mission-critical, high-precision applications.
Despite their impressive capabilities, ceramics have historically seen slower adoption rates due to difficulties surrounding their machining and grinding processes. Traditional operations have hesitated to make the investment into superabrasive technology that supports ceramic grinding. However, adoption of these advanced grinding methods have greatly improved the ease and efficiency of processing ceramics has led to their expanded use within practical applications across various industries.
A Controlled Trial: Ceramics vs. Metals
To better understand ceramic grinding, CDT conducted a detailed trial comparing the grinding difficulty of various advanced ceramic materials. Four distinct ceramics were selected—Boron Carbide, Quartz, Silicon Carbide, and ZTA—and each was surface-ground using the same 240 grit vitrified diamond wheel. Sensors captured critical metrics, including power draw and cutting forces, at different feed rates to generate a series of three different material removal rates. We then aligned our findings with a similar historical study conducted on metals, allowing us to directly assess how ceramic materials measure up to metals in terms of grinding difficulty.
Understanding the Metrics
The two critical measurements taken during grinding were power draw and force. Why focus on these?
1. Power Draw: This metric directly relates to the grinding zone temperature. Elevated temperatures accelerate diamond wear, causing wheel degradation.
For example, in a practical scenario, higher temperatures can significantly shorten the life of a grinding wheel, increasing operational downtime and costs. Therefore, optimizing power draw directly contributes to maintaining productivity and profitability.
2. Cutting Forces: Excessive cutting forces can lead to machine deflection, vibrations, increased wheel wear, stress on machinery, and quality issues like cracking.
Consider a manufacturer grinding precision ceramic components for aerospace applications; excessive cutting forces could lead to subtle defects or inconsistencies that might compromise safety and performance. Managing and controlling these forces through proper grinding parameters is crucial for maintaining product integrity and consistency.
Results of the Experiment
The experiment conducted by The Grinding Chronicles team provided valuable insights into the relative difficulty of grinding ceramics compared to metals:
Specific Power: Among the ceramics tested, Boron Carbide required the most power, indicating it can be more challenging to grind, whereas Quartz needed the least.
Force: The ranking of ceramic materials was the same when evaluating the cutting force required, reaffirming the results from the specific power analysis.
Cutting Performance: In a third analysis, we combined power and force data to evaluate the overall grindability of each ceramic material. This provided a clear picture of how easy—or difficult—each one was to grind. In this cutting performance evaluation, Quartz was notably easy to grind—so much so that it hardly registered on the standard graph. This illustrates that ceramics can range from very challenging (Boron Carbide) to exceptionally easy (Quartz).
To provide additional perspective, we referenced a notable 1970s study by Dr. Richard Lindsay, which examined the relative difficulty of grinding various metals using conventional abrasives. By using a similar methodology for our experiment, we were able to overlay our ceramic grinding data onto Dr. Lindsay’s original findings to evaluate the results.
In the direct comparison, it clearly illustrates how ceramics stack up against metals in grinding difficulty. The results showed that grinding Boron Carbide with a vitrified diamond wheel was only slightly more challenging than grinding 52100 steel using conventional abrasives. Meanwhile, Zirconia Toughened Alumina (ZTA) with a vitrified diamond wheel ground as easily as cast iron with conventional abrasives.
The Key Takeaway
Not all ceramics are created equal. Similar to metals, ceramic materials vary significantly in their grindability. Misconceptions about ceramics arise mainly because machinists are generally more familiar with metals and their properties, processes, and challenges.
However, from a power and force perspective, ceramics exhibit grinding characteristics comparable to metals. Success in grinding ceramics depends heavily on understanding the optimal grinding processes, machine setups, and wheel selections tailored to each specific ceramic material.
If you're new to ceramics or struggling with grinding ceramic materials, CDT’s engineering experts are here to help. Contact us today at TheGrindingChronicles@CDTUSA.net for expert guidance.
Check out more videos from The Grinding Chronicles and follow CDT on Linked In for the latest news in grinding technology.
Tailoring Grinding Solutions for the Unique Challenges of Aerospace
From titanium to CMCs, see how Continental Diamond Tool’s grinding and dressing solutions are engineered to meet the toughest manufacturing challenges in aerospace.
In aerospace manufacturing, precision grinding is essential for producing components that must reliably perform under extreme conditions. Whether it’s turbine blades, vanes, or structural parts, these components require tight tolerances, exceptional surface finishes, and consistent performance—all while being made from some of the most challenging materials to grind, such as nickel-based superalloys, titanium, and ceramic matrix composites (CMCs).
The grinding process must balance aggressive material removal, heat management, and tool wear resistance to achieve the required part quality and efficiency. This is where electroplated grinding wheels and diamond rotary dressers provide significant advantages, offering solutions to some of the most persistent challenges in aerospace grinding.
Evolving Challenges in Aerospace Manufacturing
Aerospace manufacturers are continuously refining their production processes to meet increasing performance demands. Several industry trends are shaping the way grinding solutions must adapt:
Advanced Materials Require New Machining Strategies
The use of lightweight, high-strength materials such as carbon fiber composites, aluminum-lithium alloys, and CMCs is growing. These materials improve fuel efficiency without sacrificing structural integrity. However, their brittleness, heat sensitivity, and abrasiveness present machining challenges that require specialized grinding technology to shape them.
Additive Manufacturing Is Changing Component Design
3D-printed aerospace parts often require post-processing to achieve dimensional accuracy and surface integrity. Superabrasive grinding wheels are particularly well-suited for refining these components without inducing stress or altering their properties.
Rising Demand for High-Precision Parts
Increasing global defense spending and increased commercial air travel require manufacturers to produce high-performance components at scale, making efficient and repeatable grinding solutions more critical than ever.
Space Exploration Is Pushing Material Science Forward
New materials developed for satellite technology and space vehicles require grinding solutions that can maintain precision while working with ultra-hard alloys and ceramics, materials designed to withstand the extreme conditions of space.
With these challenges in mind, engineering the right grinding wheel is more critical than ever for ensuring part quality, process efficiency, and long-term performance in aerospace applications.
The Role of Electroplated Grinding Wheels in Aerospace
Electroplated grinding wheels offer a unique advantage in aerospace manufacturing due to their single-layer abrasive structure, aggressive cutting action, and ability to maintain form without dressing. Unlike bonded grinding wheels, where abrasive grains are embedded within a matrix, electroplated wheels expose a full layer of diamond or cBN material, ensuring sharp cutting edges and consistent performance.
How Electroplated Grinding Wheels Address Aerospace Challenges
✔ Maintaining Profile Accuracy: Electroplated wheels hold complex geometries without needing dressing, making them ideal for intricate aerospace components.
✔ High Stock Removal with Minimal Heat Generation: The open structure of electroplated wheels allows for aggressive material removal while features like coolant slots and through the wheel coolant delivery can be added to reduce heat buildup—critical when working with heat-sensitive materials like titanium.
✔ Custom-Engineered for the Application and Material: Abrasive size and type, core accuracy, and uniform plating are all critical to match unique aerospace grinding requirements.
✔ Longer Tool Life, Less Downtime: Electroplated wheels maintain their shape throughout their lifespan, eliminating the need for dressing and reducing machine downtime.
✔ Cost Savings with Strip and Replate Services: CDT offers a customized strip and replate program that allow customers to reuse the same core, reducing costs and lead times while delivering the same high-level performance. Our strip technology safely removes remaining abrasive without damaging the core and returns the tool to “like new” condition after replating. This makes it a more cost-effective and sustainable solution for aerospace manufacturers running frequent grinding operations.
"Electroplated grinding wheels are a great fit for aerospace because they are both precise and efficient. They hold intricate profiles, handle high speeds, and stand up against tough materials like nickel alloys, titanium, and ceramics — plus, with our strip and replate services, customers can extend the life of their tools and keep costs down without sacrificing performance," says Jordan Donnelly, CDT Product Line Manager for Electroplated Products.
Optimizing Grinding Performance with Diamond Rotary Dressers
Precision grinding requires continuous wheel maintenance to ensure optimal cutting efficiency and part consistency. Diamond rotary dressers are essential in aerospace manufacturing for truing and conditioning grinding wheels, ensuring the reliability and accuracy of the grinding process.
Key Benefits of Diamond Rotary Dressers in Aerospace
✔ Consistency Across High-Volume Production: Rotary dressers keep grinding wheels performing uniformly, ensuring part consistency and accuracy from the first to the last component.
✔ Reducing Cycle Times & Increasing Efficiency: Keeping wheels properly conditioned and sharp, minimizes grinding forces and allows for optimum cycle times while maintaining part quality.
✔ Application-Specific Design: Whether the application requires traverse or plunge-style dressing, CDT custom-designs each rotary dresser to specific customer needs and applications.
✔ Manufacturing Customization: Every application is different, thus requiring different solutions. CDT solves this issue by offering sintered, reverseplated, and metal bonded rotary dressers.
"Consistency is everything in aerospace manufacturing. Even the smallest deviation can throw off performance, which is why rotary dressing is so important. Our custom-engineered dressers keep grinding wheels precise and reliable, helping manufacturers get accurate, repeatable results every time," explains Troy Giacherio, CDT Product Line Manager for Diamond Rotary Dressers.
The Advantage of a Multi-Disciplinary Grinding Expertise
While electroplated grinding wheels and diamond rotary dressers provide high-performance solutions, CDT’s expertise extends beyond these technologies—allowing us to approach aerospace grinding challenges from multiple angles.
We have extensive experience working with a variety of:
Bond Types: Plated, resin bond, metal bond, vitrified bond, hybrid bond
Core Materials: Carbon fiber, ceramic, high-tensile strength steel, and many more
Diamond Patterns: Handset, random set, reverse plated, CVD-reinforced
Abrasives: Diamond, cBN, and conventional abrasive grinding solutions
This broad expertise enables CDT to study materials, test performance, and develop tailored grinding solutions that push the boundaries of what’s possible. Our dedicated grinding lab allows us to simulate real-world aerospace applications, testing how new materials react during grinding and refining wheel designs to optimize performance.
This cross-industry experience from both the product and application side fosters innovation, ensuring that we don’t just provide grinding wheels—we provide solutions tailored to the specific needs of aerospace manufacturers.
Expanding Capabilities to Better SERVE the Aerospace Industry
To address increasing global demand for aerospace products, CDT is expanding its electroplated grinding wheel production capacity with a new building that will grow its second plating line in Europe. This expansion will increase production efficiency, reduce lead times, and allow CDT to serve aerospace manufacturers at a larger scale.
"Expanding our plating facility is a big step forward. With the new electroplating line, we can speed up production and handle more capacity, getting products delivered faster. It’s all part of CDT’s commitment to innovation and supporting the growing needs of our aerospace customers," says Justin Hughes, Production Manager at CDT Ltd.
Finding the Right Grinding SolutionS for Aerospace Manufacturing
The challenges of aerospace manufacturing—tough materials, tight tolerances, and growing demand—require advanced grinding solutions that can maintain precision, minimize downtime, and innovate at speed and scale.
With specialized knowledge in electroplated diamond and cBN grinding wheels, advanced diamond rotary dresser technology, and expertise across many other grinding product types, CDT is uniquely positioned to help aerospace manufacturers optimize production processes and innovate for the future.
Contact us today to discuss how CDT’s precision grinding solutions can help optimize your aerospace manufacturing process.
Core Matters: How Different Wheel Body Materials Impact Grinding
Learn how grinding wheel core materials like steel, aluminum, and carbon fiber impact performance, precision, and cost to optimize your grinding applications.
When using superabrasive grinding wheels in precision manufacturing, selecting the right abrasive, bond type, and wheel core material is critical for optimal grinding performance and wheel life. While abrasives and bond types often take center stage, the wheel core can be equally important. The core material is the foundation that provides structural support and stability. The right core material ensures high performance while preventing machine strain, excessive grinding wheel wear, and unnecessary cost. But how do you determine the best core material for your specific needs?
In Episode 10 of The Grinding Chronicles, CDT Engineering Manager Jeff Wirth breaks down the essential properties of core materials and how they influence grinding applications. Watch the video or read the article below to learn how to choose the best option for your application.
The Grinding Chronicles - Episode 10
Selecting the Right Core Material for Grinding Wheels
The core of a superabrasive grinding wheel does more than just hold the abrasive—it directly impacts machine efficiency, grinding precision, and tool longevity. Choosing the right core material not only optimizes performance but also helps prevent unnecessary damage to the wheel, machine, and workpiece while enhancing operator safety.
Common core materials for superabrasive grinding wheels include metals—such as steel, aluminum, and copper—as well as non-metals like ceramics and resin composites. Ceramic or vitrified cores are commonly found in conventional abrasive grinding wheels and are also used in some superabrasive grinding wheels. Resin composite cores may be made from materials like bakelite, abrasive composites, or carbon fiber. Each of these materials has unique properties that affect grinding performance, and understanding their characteristics helps manufacturers make more informed decisions.
Understanding Core Material Properties
Density – Defined as mass per unit volume, density directly affects the weight of a grinding wheel. Heavier cores put added stress on machines and spindle bearings, which is why large-diameter grinding wheels are often designed with lighter core materials like carbon fiber, bakelite, or ceramic. An overly heavy wheel can reduce machine longevity, increase energy consumption, and pose handling risks for operators, making weight an important consideration for both performance and safety.
Expansion – Core materials expand due to heat and mechanical forces, which can impact grinding accuracy. Minimizing expansion is crucial for applications with tight tolerances, as it helps prevent wheel distortion and ensures consistent precision. Expansion occurs in two forms:
Mechanical Expansion: At high speeds, some core materials naturally expand due to centrifugal forces. Materials with high tensile strength resist this growth, maintaining stability and accuracy over time.
Thermal Expansion: Heat generated during grinding can cause materials to expand, leading to dimensional changes and reduced precision. Materials with low thermal expansion coefficients are essential for consistently achieving tight tolerances.
For high-speed and high-precision grinding applications, grinding wheels with cores made from high-tensile steel, carbon fiber, or vitrified ceramic often perform better. These materials minimize mechanical and/or thermal expansion, ensuring consistent performance, reduced deformation, and greater accuracy under extreme conditions.
Thermal Conductivity – This property determines how well a core material dissipates heat. Efficient heat transfer prevents thermal damage (burning) to the workpiece, improves surface quality, and extends tool life. Metal materials like Copper and Aluminum with high thermal conductivity remove heat, leading to lower wear and improved performance in high heat applications such as fluting drills.
Modulus of Elasticity (MOE) – This measurement indicates a material’s ability to resist deformation under stress. A higher MOE means the material is stiffer and less likely to flex or deform. Steel has a very high MOE. This can be beneficial for applications with high grinding forces that require tight tolerances, as a flexible core can introduce inconsistencies in grinding performance.
Comparing Core Materials: Strengths and Weaknesses
Each core material offers specific advantages and drawbacks. Here’s how some of the most common materials compare:
Steel is strong, durable, and resistant to mechanical expansion. However, its heavy weight can strain machinery.
Aluminum is lighter and often more affordable than steel, with higher thermal conductivity and resistance to corrosion. However, it has significantly higher thermal expansion compared to steel and other materials.
Copper offers excellent thermal conductivity and a high modulus of elasticity (MOE), but its weight and cost make it less suitable for large grinding wheels.
Ceramic is lightweight, cost-effective, and resistant to expansion, but low thermal conductivity and high stiffness or brittleness can be a drawback.
Resin composites, including bakelite, are affordable and lightweight. However, they lack stiffness and high thermal conductivity, making them more susceptible to expansion and heat buildup in high-force grinding applications.
Carbon fiber is ideal for demanding applications due to its high stiffness and low weight. However, it tends to trap heat and is more expensive than other materials.
Choosing the Right Core Material for Your Application
Selecting the best core material depends on several factors, including the type of grinding being performed, the machine’s limitations, and cost considerations. For example:
Flute grinding and medical drill bits operate at traditional speeds with lower grinding forces. This means that a wide variety of core materials can be used without significant performance issues. In these cases, ceramic cores are often recommended because they provide an excellent balance of cost and functionality.
High-speed applications like camshaft grinding generate significant heat and grinding forces. This makes high-stiffness materials like carbon fiber or high-tensile steel essential to be able to perform effectively and safely.
Hybrid or combination cores are an innovative solution for balancing weight, stiffness, and cost. This approach involves layering or combining different materials to optimize performance while keeping costs manageable. For instance, a steel core can be reinforced with carbon fiber to reduce weight without sacrificing strength.
Practical Considerations in Core Material Selection
Beyond material properties, cost plays a major role in selecting the right core material for grinding wheels. While core materials like carbon fiber and vitrified ceramic are both resistant to mechanical and thermal expansion and lighter weight, they come at very different price points. Once all process requirements are met, cost is usually the deciding factor, as manufacturers balance performance needs with material costs to avoid unnecessary expenses.
Budget-Friendly Options – Ceramic and resin composites provide cost-effective solutions for applications with lower grinding forces and minimal heat generation. These materials perform well in traditional grinding operations without adding unnecessary expense.
Mid-Range Solutions – Aluminum and standard steel cores offer a balance between affordability and durability. These materials are commonly used in medium-duty grinding applications where moderate strength and thermal properties are required, optimizing cost per part without sacrificing performance.
Premium Core Materials – High-tensile steel and carbon fiber provide top-tier performance, making them ideal for high-speed and high-force applications. While their higher price point increases the initial cost of the grinding wheel, their longevity and reliability often justify the investment by reducing long-term cost per part through extended tool life and efficiency gains.
When selecting a core material, it is essential to consider not just the upfront cost but also long-term savings from reduced machine wear, improved grinding efficiency, and longer tool life. CDT’s engineering team can help assess cost-effectiveness based on your specific grinding application, ensuring the best balance between performance and cost per part.
Optimize Your Grinding Wheel Performance with CDT
Choosing the right core material is critical for achieving consistent, high-performance grinding results. Whether you're working with grinding applications for heavy-duty industrial engine components or high-precision medical tool manufacturing, the engineering team at Continental Diamond Tool is ready to assist in customizing a grinding wheel with the materials that are best for your needs.
If you have questions about selecting the best core material for your specific application, CDT’s engineers are here to help. Reach out to TheGrindingChronicles@cdtusa.net for expert advice.
Check out more videos from The Grinding Chronicles and follow CDT on Linked In for the latest news in grinding technology.
The Essential Role of Diamond Grinding Wheels in Manufacturing with Composite Materials
Learn how diamond grinding wheels optimize composite material manufacturing, tackling fiber pullout, heat sensitivity, and tool longevity.
Manufacturing with composite materials presents unique challenges: differences in hardness, fiber pullout, and heat sensitivity require grinding wheels with specialized engineering to prevent defects and ensure tool longevity. Superabrasive grinding wheels, particularly those utilizing diamond abrasives, have become indispensable tools in achieving the desired quality and efficient grinding of parts made from composites.
Understanding Composites
Composites are engineered materials made by combining two or more constituent materials with distinct physical or chemical properties. The result is a material that exhibits characteristics different from the individual components, often offering enhanced strength and reduced weight. Common types of composites include:
Fiberglass: Comprising glass fibers embedded in a resin matrix, fiberglass is renowned for its versatility and is used across many sectors, from automotive components to sporting goods to garage doors.
Ceramic Matrix Composites (CMCs): These consist of ceramic fibers within a ceramic matrix, providing high-temperature stability and strength. CMCs are ideal for many aerospace applications.
Fiber Matrix Composites (FMCs): Combining fibers such as carbon or aramid with a polymer matrix, FMCs are commonly used in wind turbines and marine vessels due to their excellent strength-to-weight ratios.
The Role of Superabrasive Grinding Wheels
Manufacturing with composites presents unique challenges, primarily due to their heterogeneous nature and the abrasive characteristics of reinforcing fibers. Superabrasive grinding wheels, especially those with diamond abrasives, can be custom engineered to address these challenges effectively.
Fiberglass and FMCs: For these materials, electroplated diamond grinding wheels are an excellent choice. Plated diamond grinding wheels are widely used because they can be designed with an open structure that helps prevent issues like "loading," where softer materials can clog the wheel and lead to inefficiencies. These wheels are often employed with aggressive grit sizes ranging from 40 to 120 to ensure efficient material removal and desired surface finishes.
"Each composite material presents unique machining challenges. For example, Fiberglass and Fiber Matrix Composites can be tricky because they tend to ‘string’ if not cut properly. That’s why we often recommend a plated grinding wheel with aggressive grit—it keeps the material from gumming up and ensures a clean finish,” says Matt Harnish, CDT Sales Rep for Diamond and CBN Plated Products.
CMCs: Given their hardness and brittleness, CMCs require a more nuanced approach. While plated grinding wheels are suitable for the majority of composite grinding applications, approximately 75% of those we see at CDT, certain scenarios may benefit from metal bond or hybrid bond grinding wheels.
"Plated wheels are ideal for most composite applications because they maintain their profile and cut aggressively without excessive wear. But for Ceramic Matrix Composites, we sometimes refer customers to our metal bond or hybrid bond product lines when deeper diamond layers are needed for longevity and performance,” says Jordan Donnelly, Plated Product Line Manager.
Maintenance and Performance Considerations
Due to the variable composition in composite materials, it is common for grinding wheels to experience "loading," where debris accumulates on the wheel's surface and diminishes cutting efficiency. While plated grinding wheels typically do not require dressing, in these applications some dressing can help to restore their optimal performance and prolong their lifespan. Proper coolant application can also help to reduce the amount of debris.
"One of the biggest factors in machining composites is managing tool wear. If a wheel starts loading up, it’s not cutting efficiently. Regular dressing keeps the wheel sharp and extends its life, ensuring our customers get consistent performance,” Matt explains.
Comparative Advantages
When evaluating grinding solutions for composites, several factors come into play:
Performance: Superabrasive grinding wheels, particularly diamond-based plated wheels, offer superior cutting efficiency and precision compared to alternatives like carbide-tipped wheels.
Durability: The inherent hardness of diamond ensures a longer tool life, reducing the frequency of replacements and downtime.
Cost-Effectiveness: While the initial investment in superabrasive wheels is high, their extended lifespan and enhanced performance lead to cost savings over time, often making them more cost effective when considering cost per part.
“We switched from carbide to diamond-plated wheels over 30 years ago and have seen great results. They last much longer and aren’t that much more expensive. The savings in tool life and less downtime easily make up for the cost. Diamond’s extreme hardness, durability, and efficiency make it the best choice for grinding composites, especially with the precision we need for large-scale building construction and remodel projects,” says a longtime CDT customer.
Emerging Technologies and Industry Outlook for Composite Machining
The composite industry is continually evolving, with advancements aimed at improving manufacturing efficiency and material performance. Notable emerging technologies include:
Automated Fiber Placement (AFP): This advanced method involves the precise placement of fiber tapes onto molds, enhancing production rates and consistency in composite part fabrication.
Additive Manufacturing with Composites: The integration of 3D printing technologies allows for the creation of complex composite structures, offering design flexibility and potential material savings.
The composites industry is experiencing robust growth, with a market valuation of $99.52 billion in 2023. This trend underscores the increasing adoption of composite materials across various sectors, driven by their advantageous properties and the continuous advancements in manufacturing technologies.
CDT is well-positioned to meet the rising demand with its state-of-the-art 500-tank plating lab in the United States. We can deliver high-capacity production of high-quality, reliable superabrasive tools. Additionally, with a larger plating facility currently being built in the United Kingdom, CDT is expanding its reach to better serve the global composites market with cutting-edge grinding solutions.
In conclusion, superabrasive grinding wheels play a pivotal role in the machining and fabrication of composite materials. Their ability to deliver precision, efficiency, and longevity makes them indispensable in the ever-evolving landscape of composite manufacturing. The use of composite materials is growing, and CDT is ready. Call us today to discuss how our precision grinding solutions can enhance your production process.
Quality Assurance at Continental Diamond Tool
Discover how the quality team at Continental Diamond Tool ensures high standards through every phase, from pre-production to final inspections.
At Continental Diamond Tool (CDT), quality is more than a department—it’s the cornerstone of our commitment to customer satisfaction. The quality control process at CDT is thorough, involving more than a dozen checkpoints from pre-production to the final inspection, ensuring that every tool we deliver meets our strict standards for accuracy and durability. This dedication to quality is achieved through structured quality checks and the expertise of our team, who are driven to exceed customer expectations at every stage.
A Rigorous, Multi-Stage Quality Control Process
Every tool manufactured at CDT goes through a comprehensive quality control process that spans pre-production, in-line, and final inspections. These checkpoints serve as crucial layers of verification, allowing CDT to consistently exceed industry standards for tolerance and customer expectations.
Pre-Production Inspections
Quality assurance starts before any production begins. It kicks off in pre-production where we verify that the quality of the raw materials and components meet our exacting quality standards. It also takes place in our engineering department where we examine prototypes, samples, and drawings to confirm that our specifications align with the intended design. By identifying potential issues early, CDT reduces the chance of mishaps later in the production process.In-Line Product Inspections
Quality control ramps up once production starts. Production technicians at every stage are trained on in-line or in-process inspections to make sure the tool matches the customer’s specifications. This proactive inspection phase helps prevent errors and catches any inconsistencies before they compound through the production process.Final Inspections
The final inspection is the most familiar phase to many, taking place once production is complete. Every finished tool is thoroughly inspected to ensure it meets CDT’s rigorous standards for dimensional accuracy, durability, and aesthetic appeal. This final layer of inspection provides the highest level of assurance that every tool shipped is fully compliant with customer requirements.
The Role of Quality Professionals at CDT
The skilled professionals in CDT’s Quality Department bring nearly 150 years of combined experience to this structured approach to quality assurance. Led by Quality Manager Karl Zimmerman, the team is dedicated to upholding the high standards CDT customers expect. "We take pride in inspecting every tool that goes through our shop, across all product lines," Zimmerman says. "Our well-rounded team ensures each product is both appealing and dimensionally precise."
A critical component of CDT’s quality efforts is the final inspection, where Quality Technicians play an essential role. They not only inspect the completed products but also create inspection programs to enhance consistency and efficiency. “As a Quality Tech here at CDT, we use a variety of instruments to ensure tools meet customer specifications precisely,” says former Quality Tech Leslie Gerzinsky.
In this video, Gerzinsky highlights the importance of adaptability and attention to detail in quality control: “Working here requires a willingness to learn and an eye for detail.” This attitude is essential for CDT’s rigorous environment, where every tool is unique and every department is continuously seeking improvement. “My favorite part of the job is getting to explore different processes and technology. Working in such a supportive, family-like atmosphere really makes the difference,” she adds.
A Quality Culture Built on Continuous Improvement
Quality control at CDT is not limited to final inspections; it is a continual process starting well before production. By working closely with design and production teams, the quality department helps identify and solve potential challenges early, reducing inefficiencies and ensuring a high-quality product. This integrated approach fosters a culture of quality that permeates CDT, from the shop floor to management.
CDT invests in advanced inspection tools and software to maintain a competitive edge in precision and quality. For example, CDT has invested heavily in high-tech measuring equipment from industry leaders like Zoller and Keyence, and our quality techs are skilled in programming this state-of-the-art equipment to streamline quality checks, minimize human error, and enhance team efficiency. Continuous improvement is a guiding principle, driving the team to refine methods and implement new technologies that enhance their inspection and quality control processes. This commitment to improvement enables CDT to stay ahead of industry trends and maintain high customer satisfaction.
CDT’s culture of quality is further reinforced by the dedication of its employees, who take pride in their work and recognize their impact on CDT’s reputation and success. The supportive environment fosters a sense of ownership and collaboration, allowing the quality team to focus on producing reliable, high-performance grinding tools without compromising speed or innovation.
The Key to Customer Satisfaction
At CDT, quality assurance goes hand-in-hand with our dedication to customer satisfaction. Our multi-step inspection process is designed with our customers in mind, to ensure products that are reliable, efficient, and tailored to their needs. This customer-centric approach is key to CDT’s success, underscoring the importance of quality at every step of the process.
With a team of committed professionals and a drive for continuous improvement, CDT ensures that every tool meets the highest standards of precision, durability, and reliability. To learn more about CDT’s quality assurance process or to tour our facility firsthand, reach out to us at www.cdtusa.net/contact. Interested in a career in quality? Check out cdtusa.net/careers for a list of job openings.
Vitrified Bond for High Performance Grinding
Learn how CDT’s vitrified bond grinding wheels deliver precision, customization, and efficiency across industries. Trusted for high-performance manufacturing since 1973.
When quality and performance are crucial to your industry—whether it’s automotive, aerospace, medical, or electronics—reliable grinding solutions are essential. At Continental Diamond Tool (CDT), we understand these demands, which is why our vitrified bond product line has become a trusted choice for high precision manufacturing worldwide. Today vitrified bond wheels are fast-evolving into one of the most sought-after products in the grinding industry. They stand as a key solution across multiple markets, delivering the high performance and customizability industry leaders need to stay competitive.
Check out this video and article below to explore what makes CDT’s vitrified bond products so effective and why customers across industries trust us to meet their high-performance grinding needs.
The Rapid Growth of CDT’s Vitrified Bond Product Line
Since we introduced this product line in 2014, our vitrified bond grinding wheels have experienced remarkable growth, becoming a cornerstone of our grinding solutions. In just 10 years, our vitrified bond products have gone from being a niche offering to one of the most widely demanded solutions in our portfolio.
Jeff Wirth, Engineering Manager at CDT, reflects on this growth:
“When we first introduced vitrified bonds, we knew they had the potential to meet the demands of a growing number of applications. Today, vitrified bonds have become one of our most popular and successful product lines, offering unmatched results.”
The success of this product line can be attributed to its adaptability, customization, and superior performance, which have allowed CDT to penetrate new markets and expand its presence in existing ones. From high-volume automotive production,rapidly developing semiconductor, or high-stakes aerospace applications, the versatility and reliability of CDT’s vitrified bonds have made them an essential tool for manufacturers around the globe.
Understanding Vitrified Bonds
As Jeff Wirth explains, vitrified bonds are a key element of grinding wheel technology:
“Your bond is basically the glue that holds the materials in your grinding wheel together, and it impacts the wheel's performance. Selecting the right bond for your application is crucial for process efficiency and workpiece quality.”
Vitrified bonds, made from glass or ceramic materials, provide structural integrity and hold the diamond or CBN abrasives together in the wheel. These bonds are valued for their ability to withstand high levels of pressure and heat, making them ideal for challenging grinding operations. Plus, their porous nature allows for the free flow of coolants, reducing the risk of burning and enabling higher material removal rates.
Customizing Solutions for Every Application
One of the major drivers behind vitrified bond’s success is CDT’s expertise in customization. Each wheel is designed to meet the requirements of the customer’s process, ensuring optimal performance for their unique grinding application.
Walt Baumbach, Vitrified Product Manager, explains:
“At CDT, our vitrification process is customized to the specific needs of our customer’s application. Our structures are based on the products our customers are grinding, and we use data-driven analysis to build a structure that is superior to competitors.”
This level of customization enables CDT to craft grinding wheels that maximize efficiency and deliver superior results. From manufacturers of electronic components requiring high-volume precision grinding to medical orthopedics demanding exact tolerances, CDT’s vitrified bond products are tailored to deliver consistent and reliable performance.
The Manufacturing Process of Vitrified Grinding Wheels
At CDT, the vitrified bond manufacturing process is carefully controlled from start to finish to ensure that every product meets the highest standards of quality and performance. Craig Rorick, Production Supervisor for the Vitrified Department, elaborates on the diversity in the industries benefiting from these products: “The industries that use vitrified wheels include automotive, aerospace, medical, and ceramics. Really pretty much every industry—whether directly or indirectly—has vitrified grinding wheels connected to it.”
Here’s a closer look at the exacting manufacturing process:
Formulation: The process begins with a carefully tailored formulation or recipe, designed to meet each customer's unique grinding application. These formulations include the bond material, abrasive fillers, and other additives used to fine-tune the structure and performance of the grinding wheel.
Mixing: The dry powders, which consist of glass, ceramic, diamond or CBN, and fillers, are mixed together using a variety of proprietary techniques to create a homogeneous blend.
Molding: The mixed powder is then carefully poured and packed into the desired mold cavity. This step is crucial for ensuring uniformity and the right density for the wheel's structure.
Pressing: After molding, the material is pressed to form the wheel’s shape and density, ensuring the bond is strong and capable of handling the demands of high-production environments.
Sintering/Baking: Pressed wheels are sintered (Baked) at high temperatures in specialized kilns (ovens). This fuses the glass or ceramic bond with the abrasive materials, creating a hard, porous structure that allows for efficient grinding and coolant flow.
Assembly: Some wheels require assembly or bonding to metallic or composite components such as threaded wheel studs or cores that allow them to be mounted onto specific grinding machines. Assembly is done by a proprietary epoxy bonding procedure to ensure product integrity.
Finishing: Once the wheel has been baked and fused, it undergoes precision machining and grinding to meet the customer's exact size, geometry, and tolerance requirements.
Each of these steps ensures that CDT’s vitrified bond grinding wheels provide superior performance while handling complex grinding tasks.
Key Advantages of Vitrified Bond Grinding Tools
Vitrified bond products from CDT offer several distinct advantages, making them the ideal choice for high-production grinding applications:
High Porosity: Porous Vitrified bonds bring coolant to the grinding zone while allowing grinding swarf and debris to be removed, reducing heat buildup and minimizing the risk of burning the workpiece. This makes them well-suited for high-speed grinding operations.
Lower Grinding Forces: The structure of vitrified bonds reduces grinding forces, which allows for increased grinding speeds and improved efficiency in high-production environments.
Customization: CDT’s vitrified grinding wheels are tailored to each customer’s specific material and application, ensuring superior performance compared to standard off-the-shelf products.
High Tolerance Form Accuracy: Vitrified wheels can be profiled or shaped to meet exacting tolerances, ensuring that they provide consistent form accuracy. This makes them particularly useful for applications requiring complex geometries and precise finishes.
Vit’s Secrets to Market Success
Today, vitrified bond grinding wheels are used in some of the most demanding applications across industries. How have vitrified bond products at CDT become a cornerstone of our business? This success is driven by several key factors:
Versatility: Vitrified bond products have proven to be adaptable across a wide range of industries and applications, from grinding turbine blades in aerospace to shaping medical implants.
Precision and Efficiency: Customers rely on CDT’s vitrified bond wheels to deliver consistent, high-quality results in high-production settings, making them a critical tool in industries where precision and efficiency are paramount.
Continuous Innovation: Over the past decade, CDT has continually refined its vitrified bond technology, expanding its capabilities and offering new solutions to meet evolving industry needs.
Industries Benefiting from CDT Vitrified Bond Products
Vitrified grinding wheels are a vital tool for industries that require both reliability and precision for safety and performance. This advanced technology allows manufacturers to achieve high levels of accuracy, reduce grinding forces, and increase production efficiency with demanding specifications.
How are high-tech industries leveraging this cutting-edge technology?
Automotive: Commonly used for grinding engine components, such as camshafts and crankshafts, in high-production environments.
Aerospace: Essential for grinding turbine blades, vanes, shrouds, and other high-precision parts, where exact tolerances are required.
Medical: A key tool in manufacturing precision surgical instruments and medical implants with critical surface quality considerations.
Ceramics: Ideal for shaping and finishing hard, brittle materials like ceramics without damaging delicate components.
Semiconductors: Used in the production of electronic components to maintain quality and functionality in micro-level manufacturing.
Why Choose Vitrified Bond Products from CDT?
At CDT, we are proud of how far our vitrified bond product line has come since 2014. Today, these products are among our most widely used, trusted by industries around the globe. Here’s why customers continue to choose CDT’s vitrified bond:
- Expert Customization: Our experienced engineering team tailors every wheel for optimal performance.
- Attention to Detail: Every step of the manufacturing process is carefully controlled to ensure consistent quality and reliability.
- Reliable Delivery: We understand the importance of timely service, and our customers can trust us to deliver their products when they need them
- Application Support: CDT has made it a priority to provide our customers with access to experienced Application Engineers to provide support for your specific grinding applications.
With a decade of growth and success, CDT’s vitrified bond product line continues to push the boundaries of grinding technology. If you’re looking for custom grinding wheels, it’s very likely CDT’s vitrified bond products can offer an excellent solution for accuracy, performance, and reliability. Contact us today to learn more about how we can help you achieve your production goals.
An Essential Guide to Grinding Process Optimization for Boosting Performance in Precision Manufacturing
Optimize your grinding process with expert tips on speeds, feeds, Q-prime, and advanced bond technology to boost efficiency in precision manufacturing.
To stay competitive in precision manufacturing, grinding operations require continuous improvement in performance and efficiency. Understanding the factors that influence grinding, such as speeds, feeds, and material removal rates, can significantly impact your results. In this comprehensive guide from Continental Diamond Tool, Product Engineer Thi Dang and Engineering Consultant Jon VanSant share their expertise as they unpack the essential elements of grinding process optimization. Episode 8 of The Grinding Chronicles offers valuable insights into maximizing Q-prime, balancing G ratios, and selecting the right grinding wheel speeds. Whether you’re looking to refine your current operations or upgrade to the latest in bond technology, our engineering team’s breakdown outlines the key factors you need to consider to enhance your grinding processes. Watch the video or read on to discover practical tips and advanced strategies for getting the most out of your grinding tools.
The Grinding Chronicles - Episode 8
Unlocking the Secrets to Optimizing Your Grinding Process
In this article, you will learn the essentials for optimizing your grinding process, focusing on the metrics that matter most for achieving peak performance. From understanding the basics of speeds and feeds to exploring advanced bond technology, this guide provides actionable insights for any precision manufacturing operation. Whether you're new in the field or looking to enhance your current practices, this informative article from The Grinding Chronicles team offers valuable knowledge to help you get ahead in the industry.
Understanding the Basic METRICS in GRINDING
One of the first considerations when optimizing a grinding process is understanding the basics—speeds, feeds, and material removal rates. These elements are fundamental to the grinding process and play a crucial role in determining the efficiency and quality of the finished product.
Speeds and Feeds:
Speeds refer to the rotational speed of the grinding wheel, typically measured in surface feet per minute (SFM). Feeds, on the other hand, relate to the rate at which the workpiece is fed into the grinding wheel. Together, these parameters influence the rate of material removal, surface finish, and the overall efficiency of the grinding process.
It's essential to understand that faster isn't always better. While higher speeds can increase material removal rates, they can also lead to increased wheel wear and the potential for thermal damage to the workpiece. Therefore, finding the optimal balance between speed and feed is key to maintaining both efficiency and quality.
Material Removal Rate (Q-prime):
Q-prime, or material removal rate, is a critical measure of grinding performance. It is calculated by multiplying the depth of cut by the feed rate, resulting in the amount of material removed per unit time. Higher Q-prime values typically indicate shorter cycle times, which can significantly enhance productivity.
However, achieving high Q-prime values requires careful consideration of other factors, such as wheel wear and the quality of the finished surface. A high Q-prime might reduce cycle times, but if it leads to excessive wheel wear or poor surface quality, the overall efficiency of the process may suffer. Thus, optimizing Q-prime involves balancing it with other critical parameters, such as the G ratio.
The G Ratio:
The G ratio is another vital metric in grinding. It is defined as the volume of material removed from the workpiece divided by the volume of wheel wear. A high G ratio indicates efficient grinding, where more material is removed with less wheel wear. However, similar to Q-prime, achieving an optimal G ratio requires balancing various factors.
Maximizing Q-prime WHILE Balancing the G Ratio
Maximizing Q-prime while maintaining a high G ratio is the key to optimizing grinding processes. To achieve this balance, it’s important to consider the following:
Wheel Speed: Higher wheel speeds can lead to increased wheel wear due to elevated temperatures. Therefore, it’s crucial to find an optimal speed that maximizes material removal without excessively wearing the grinding wheel.
Coolant Delivery: Proper coolant delivery is essential in controlling the temperature during grinding. Efficient coolant systems help dissipate heat, reducing thermal damage to the workpiece and wear on the grinding wheel. This, in turn, helps maintain a high G ratio.
Machine Stiffness and Power: The stiffness of the grinding machine and the power of the spindle also play significant roles. Machines with low power or poor stiffness may limit the achievable Q-prime and G ratio, restricting the overall efficiency of the grinding process.
By carefully considering these factors, manufacturers can optimize their grinding operations to achieve both high Q-prime and G ratios, leading to improved productivity and efficiency.
The Evolution of Bond Technology
Bond technology plays a critical role in the performance of grinding wheels, particularly in their ability to achieve high Q-prime and G ratios. The history of bond technology in grinding wheels is a testament to the continuous advancements that have been made in this field.
A Look Back:
In the 1960s, phenolic resin bonds were the standard, offering Q-prime values of around three. By the 1970s, the introduction of polyimide bonds pushed Q-prime values to around five. The year 2000 marked another leap with hybrid bonds, which increased Q-prime to approximately seven.
Today, we are capable of removing material at rates between 10 and 15, thanks to the latest advancements in bond technology. This evolution highlights the importance of continuously upgrading to the latest bond technology to stay competitive in the market.
Introducing CDT's EVO Hybrid Bond:
Continental Diamond Tool has been at the forefront of these advancements with its EVO Hybrid Bond. Released earlier this year, the EVO Hybrid Bond represents a significant step forward in bond technology, offering the ability to achieve Q-prime values over 10 without compromising the G ratio.
The development of the EVO Hybrid Bond was driven by the need for a bond system that could grind aggressively while minimizing wear and maintaining excellent corner retention. This bond was also designed with thermal conductivity in mind, to transfer heat away from the part and prevent damage to the diamond, which is sensitive to high temperatures. Learn more about CDT’s EVO Hybrid Bond product here.
Practical Tips for Optimizing Your Grinding Process
Now that we’ve covered the theoretical aspects of grinding optimization, let’s look at some practical tips that can help you apply this knowledge to your operations:
Evaluate Your Current Operations: Start by assessing your current grinding processes. Measure your Q-prime and G ratio to establish a baseline. Identify areas where improvements can be made, whether in speed, feed rate, or wheel selection.
Invest in the Latest Technology: Consider upgrading to the latest bond technology, such as CDT’s EVO Hybrid Bond. Newer bonds can significantly improve your material removal rates and reduce wheel wear, leading to better overall efficiency.
Optimize Coolant Delivery: Ensure that your coolant system is operating efficiently. Proper coolant delivery is essential for controlling temperatures and reducing thermal damage, which can extend the life of your grinding wheels and improve the quality of your finished products.
Regularly Maintain Equipment: Regular maintenance of your grinding machines is crucial. Ensure that your machines are running at optimal stiffness and power to maximize performance and avoid limitations in Q-prime and G ratios.
Train Your Team: Make sure your team is trained on the latest grinding techniques and technologies. A well-informed team can make better decisions on the shop floor, leading to improved productivity and efficiency. At Continental Diamond Tool, our application engineers are here to help. We regularly connect with our customers to fine-tune their equipment and train their operators on the optimized speeds and feed rates to use with our grinding wheels.
Optimizing grinding processes is essential for staying competitive in precision manufacturing. By understanding and balancing key factors like Q-prime, G ratio, and wheel speed, manufacturers can significantly enhance their grinding operations. Continental Diamond Tool’s latest advancements, including the EVO Hybrid Bond, provide valuable tools for achieving these goals. Whether you’re looking to improve your current processes or invest in new technologies, the insights provided in this guide offer a clear path to optimizing your grinding operations. Implement these strategies to ensure your manufacturing processes are both efficient and effective, helping you to stay ahead in a demanding industry.
How to Diagnose Surface Pattern Problems in Grinding
Learn how to diagnose and fix common surface pattern problems in precision grinding with expert insights from CDT's Senior Product Engineer, Paul Christy.
Many precision grinding operations require impeccable surface finishes for both function and aesthetics. Addressing surface pattern problems is vital for ensuring the quality of the final product, eliminating waste, and controlling costs. In this detailed overview, we expand on the insights provided by Paul Christy, Senior Product Engineer at Continental Diamond Tool, as he explains how to troubleshoot and fix common causes of surface patterns. In Episode 7 of The Grinding Chronicles, Paul covers the complexities of surface patterns caused by various types of vibrations, runout, and servo system instability. Watch Paul’s video or read on to learn more about identifying and addressing these issues to optimize your grinding operations.
The Grinding Chronicles - Episode 7
Surface Pattern Troubleshooting Guide
Surface pattern problems in grinding can significantly impact the quality and precision of your workpieces. Diagnosing and resolving these issues requires a deep understanding of the underlying causes and appropriate troubleshooting techniques. This article explores common causes of surface patterns in grinding and provides expert insights into their diagnosis and elimination.
Self-Excited Vibration
One of the primary causes of surface pattern problems is self-excited vibration, which occurs at the natural frequency of the machine system. This type of vibration indicates that some component within the machine—such as the spindle, the part, or the dresser—is being excited. The resulting oscillating pattern is called chatter. Notably, this vibration only manifests when the grinding wheel and the workpiece (or the wheel and the dresser) are in contact.
Self-excited vibration results from a lack of sufficient component stiffness. The key to mitigating this issue lies in increasing the machine's stability, which requires a greater machine stiffness compared to the process stiffness. There are three main process variables that can be adjusted to help eliminate self-excited vibration:
Velocity of the Workpiece: Lowering the workpiece's speed can reduce process stiffness.
Velocity of the Grinding Wheel: Decreasing the grinding wheel's speed similarly lessens process stiffness.
Width of Contact: Reducing the contact width between the grinding wheel and the workpiece can also help.
By strategically lowering one or more of these variables, you can effectively diminish the impact of self-excited vibration.
Forced Vibration
Forced vibration occurs at a frequency corresponding to a driving force within or outside the machine. Common examples of such driving forces include unbalanced rotating bodies and pump pulsations. This type of vibration can often be diagnosed using a process of elimination. By sequentially turning on and off all rotating bodies within the machine, you can identify the source of the vibration when it ceases upon the deactivation of a specific component.
Runout
Runout is a prevalent issue in grinding due to the inherent imperfections of rotating components. It occurs when the outer surface of a rotating component does not maintain perfect concentricity with its axis or center line. Specifically, runout in a traversing diamond roll can create a pattern in the grinding wheel, which is then transferred to the workpiece. This pattern typically manifests as angled parallel lines, known as Barber Pole or Roping Patterns.
To address surface patterns caused by runout, it is essential to identify the optimal dresser and wheel RPMs. Varying the diamond roll speed during dressing can reduce the likelihood of pattern formation on the grinding wheel, preventing its transfer to the workpiece. Another effective solution is lapping the diamond roll to the machine's spindle bearings, thereby eliminating runout.
Servo System Instability
Servo system instability is another potential source of surface patterns on workpieces. The servo system controls the movement accuracy of machine components, using digital feedback to ensure precise positioning. Mechanical decoupling within components such as ball nuts, couplings, bearing support units, or scale mountings can create discord within the servo system. This results in oscillations as the system struggles to determine the correct position, leading to surface patterns on the workpiece.
Solving servo system instability typically requires sophisticated instrumentation and physics-based analysis. Iterative process changes alone are unlikely to resolve this complex issue.
Key Takeaways in Mastering Surface Finish
Diagnosing and fixing surface pattern problems in grinding necessitates a thorough understanding of the potential causes and their specific remedies. Whether dealing with self-excited vibration, forced vibration, runout, or servo system instability, targeted adjustments and precise troubleshooting are essential for maintaining the quality and precision of your grinding operations.
For more detailed information and expert guidance, refer to Episode 7 of The Grinding Chronicles, where Paul Christy shows specific measures you can take to diagnose and eliminate surface pattern problems. If you are experiencing surface patterns similar to those discussed in this article and require further assistance, do not hesitate to contact the Continental Diamond Tool engineering team at TheGrindingChronicles@cdtusa.net.
Understanding and addressing these grinding challenges will enhance your operational efficiency and ensure the superior quality of your manufactured products.
A Breakdown of the 4 Common Bond Systems in High Precision Grinding
Discover CDT's four essential bond systems for superabrasive grinding wheels: Resin, Metal, Vitrified, and Electroplated. Optimize operations with expert insights from Jeff Wirth.
If precision grinding is a critical component of your manufacturing process, understanding the bond system of your grinding wheel will help you in maintaining operational efficiency and product quality. In this detailed overview, we will explore the four most common bond systems used in superabrasive grinding wheels: Resin, Metal, Vitrified, and Electroplated. Continental Diamond Tool Engineering Manager Jeff Wirth breaks down the components of these bond systems, discussing their composition, manufacturing processes, and ideal applications in Episode 6 of The Grinding Chronicles. Watch Jeff’s video or read on to learn more about selecting the right bond to optimize your grinding operations.
The Grinding Chronicles - Episode 6
Understanding the Four Common Bond Systems
Resin Bonds
Resin bonds are plastic-based compounds typically made from phenolics or polyimides. These bonds are versatile and can be enhanced with fillers such as copper or silicon carbide to improve performance. The manufacturing process for resin bonds at CDT begins with creating a tailored formulation that includes the bond material, abrasive, and fillers. This dry powder mixture is blended in special tumblers and then carefully and uniformly packed into mold cavities. The molds undergo hot pressing, where temperature and pressure are meticulously controlled to achieve the desired density. Finally, the wheels are finished by machining and grinding them to the specified size and geometry.
Properties and Applications:
Tough and Durable: Resin bonds are fully dense and easy to use, making them suitable for a variety of grinding applications.
Versatile: They can work with nearly any material, from hard metals to softer alloys.
Enhanced Performance: Fillers like copper or silicon carbide can be added to improve heat dissipation and grinding efficiency.
Wide Range of Applications: Suitable for diverse grinding tasks, including tool and cutter grinding, centerless grinding, and surface grinding.
Metal Bonds
Metal bonds can be composed of various metals, including bronze, copper, and iron, and may sometimes be alloyed with precious metals like silver. Metal bonds are known for their hardness, toughness, and durability, making them ideal for grinding highly abrasive materials such as glass and ceramics. Although metal bonds grind more slowly than other types, they offer the longest lifespan. The manufacturing process for metal bonds at CDT is similar to that of resin bonds, involving formulation, mixing, molding, hot pressing, and finishing.
Properties and Applications:
Hardest and Toughest: Metal bonds are the most challenging to use but provide superior durability.
Long-Lasting: They offer the longest lifespan among bond types, reducing the frequency of wheel changes.
Ideal for Abrasive Materials: Best suited for grinding materials like glass, ceramics, and carbide.
Durability: Excellent for applications requiring extreme durability and extended wheel life, such as in the automotive and aerospace industries.
Vitrified Bonds
Vitrified bonds are made from glass or ceramic materials, creating a porous structure that significantly reduces grinding force. This allows for higher grinding speeds, making vitrified bonds ideal for high-production applications. These bonds offer moderate to high material removal rates and excellent form accuracy, as they can be dressed and profiled in-process using rotary dressers. The manufacturing process for vitrified wheels at CDT involves formulation, mixing, cold pressing, and a sintering (baking) process to fuse the glass or ceramic together. The final step is finishing, similar to the other bond types.
Properties and Applications:
Porous Structure: Lowers grinding force and allows increased speeds, enhancing efficiency.
High Production: Ideal for high-production applications such as automotive part manufacturing.
Moderate to High Material Removal Rates: Efficient for large-scale operations, balancing speed and precision.
High Form Accuracy: Can be dressed and profiled in-process using rotary dressers, making them suitable for precise and consistent grinding tasks.
Electroplated Bonds
Electroplated (or plated) bonds consist of a single layer of abrasive held by a nickel-based metal bond. The process begins with machining the desired wheel size and geometry onto a steel wheel core. The non-plated surfaces are masked to prevent unwanted plating. The wheel core is then placed in a bath with a nickel-based solution and the abrasive material. By applying a positive charge on one side and a negative charge on the other, nickel plating is deposited onto the wheel core, causing a single layer of abrasive to adhere. Excess abrasive is removed, and the plating process continues until the abrasive layer is encapsulated to the desired level, typically 50-100% depending on the application. Electroplated products are suitable for complex geometries and low to medium production applications due to their high material removal rates and fast grinding speeds.
Properties and Applications:
High Material Removal Rates: Provides the fastest grinding speeds, ideal for rapid material removal.
Cost-Effective: Single layer of abrasive can be stripped and replated, extending the wheel’s life.
Ideal for Complex Geometries: Precise form replication with minimal finishing, suitable for intricate designs.
Low to Medium Production: Suitable for specific applications requiring detailed shapes and efficient material removal.
Key Considerations for Selecting the Right Bond System:
Choosing the appropriate bond system for your grinding application is crucial for achieving optimal performance and quality. Each bond type offers unique properties and advantages, making them suitable for different materials and grinding conditions. By understanding the composition, manufacturing processes, and ideal applications of Resin, Metal, Vitrified, and Electroplated bonds, you can make informed decisions to enhance your grinding operations.
Factors in Bond System Selection:
Material to be Ground: The hardness and abrasiveness of the material significantly influence the choice of bond.
Grinding Speed and Efficiency: Consider whether the application requires high-speed grinding or if longevity and durability are more critical.
Application Specifics: Determine if the grinding operation involves complex geometries or requires high form accuracy.
Production Volume: High-production environments may benefit from vitrified bonds, while electroplated bonds are ideal for low to medium production with intricate details.
If you have any questions or want to learn more about which bond type would work best for your application, please reach out to our application engineers at TheGrindingChronicles@CDTUSA.net. For more industry insights and expert advice, check out these articles or watch our playlist for The Grinding Chronicles on YouTube. By leveraging the right bond system and understanding its properties, you can significantly improve your grinding efficiency, product quality, and operational cost-effectiveness.
How to Dress a Vitrified CBN Grinding Wheel with a Diamond Rotary Dresser
In episode 5 of The Grinding Chronicles, CDT Product Manager Troy Giacherio shares top techniques for dressing Vitrified CBN grinding wheels using Diamond Rotary Dressers. Learn how to use key parameters such as velocity ratio and overlap ratio to enhance dressing and truing operations in precision grinding.
If you work in manufacturing, particularly in the specialized area of precision grinding, it cannot be overstated the importance of wheel dressing to maintain operational efficiency and product quality. In this comprehensive guide, we will look at the best techniques for traverse dressing a vitrified cubic boron nitride (CBN) wheel using Rotary Diamond Dressers. In Episode 5 of The Grinding Chronicles, CDT Product Manager Troy Giacherio details the specific parameters and most important factors necessary for achieving peak performance in dressing and truing operations. Watch Troy’s video or read on to learn more.
The Grinding Chronicles - Episode 5
Best Techniques for Success When Dressing a Grinding Wheel
Before plunging into the specifics of dressing a Vitrified CBN wheel, it's imperative to understand the dichotomy between two fundamental processes: truing and dressing. Truing involves sculpting the shape or profile of the grinding wheel, while dressing focuses on sharpening the wheel and removing accumulated debris. While diamond rotary dressers serve both functions, understanding this distinction facilitates the implementation of effective dressing strategies.
Essential Parameters for Dressing Success
There are four key parameters to measure for optimizing the dressing of a grinding wheel:
Velocity Ratio At the heart of dressing lies the velocity ratio, calculated by dividing the velocity of the diamond roll by the velocity of the grinding wheel. This parameter holds significant importance in dressing operations. For Vitrified CBN wheels, the recommended velocity ratio stands at 0.8. Maintaining this ratio ensures that the diamond roll adeptly removes the bond material, laying bare fresh abrasives for optimal grinding performance.
Overlap Ratio The overlap ratio describes the velocity at which the diamond dresser traverses the wheel's face to sculpt its profile and hone its edge. For Vitrified Bond CBN wheels, an overlap ratio ranging between 2 to 4 is ideal. Sustaining a steady pace ensures a seamless traversal across the grinding wheel. It is important to prevent the dresser from dwelling in any single spot to guarantee uniform dressing proficiency.
Depth of Dress The depth of dress measures the extent to which the diamond roll plunges into the grinding wheel, thereby dictating the volume of material extracted per pass. When it comes to Vitrified CBN wheels, we recommend a precise depth of dress set at 0.0002 inches per pass. Adherence to this specification not only optimizes grinding efficiency and minimizes downtime, particularly in high-volume production environments, but also preserves the longevity of the grinding wheel, yielding an optimized return on investment.
Dress Interval The dress interval is defined as the frequency at which the grinding wheel needs dressing, and it is closely tied to the application at hand. Unlike their conventional abrasive counterparts, Vitrified CBN wheels do not require frequent dressing. On the contrary, it is not uncommon to grind hundreds of parts between each dressing session. However, it is important to remain vigilant. Keep an eye on the process and be prepared to adjust the dress interval if part quality diminishes.
When Should I Dress My Grinding Wheel?
Dressing frequency varies depending on several factors specific to your process. Here are two key indicators to monitor in order to assess grinding efficacy and determine when it's time to dress your grinding wheel.
Power Draw The power draw during grinding operations can be a reliable indicator for grinding wheel dressing. A drop in power draw signals that the wheel is cutting freely, with utmost efficiency, while an uptick in power suggests a looming need for dressing. Neglecting timely dressing can lead to issues such as burn or unwanted variations in surface finish. That’s why it is important to keep a close eye on power draw dynamics to prevent such issues.
Surface Finish The surface finish of machined parts relies heavily on consistently high levels of grinding performance. A well dressed wheel produces exceptional surface finishes characterized by minimal variations and unyielding consistency in part quality and dimensional accuracy. Therefore, regular dressing sessions conducted with meticulous technique are essential for maintaining superb parts quality and excellence.
Troubleshooting and Optimization
If you are still experiencing issues such as finish patterns or burn despite adhering to prescribed dressing parameters, it may be time to call in the assistance of an expert. Companies like Continental Diamond Tool have application engineers who are trained to analyze grinding processes, pinpoint underlying issues, and facilitate optimization for enhanced performance. Armed with a portable grinding lab, these experts bring their expertise on-site to meticulously evaluate coolant delivery systems, fine-tune machine settings, and traverse a gamut of other variables to resolve persistent challenges. With their help, you can galvanize productivity to unprecedented heights. If you would like help with your wheel dressing or grinding process, don't hesitate to reach out to our engineering team at TheGrindingChronicles@CDTUSA.net.
Mastering Wheel Dressing
Proper dressing of a Vitrified CBN grinding wheel with a Diamond Rotary Dresser is the key to optimal grinding performance and part quality. By incorporating the parameters and techniques we’ve outlined in this article, manufacturers can achieve reductions in downtime, extension of wheel life, and unwavering consistency in high quality results.
Additionally, by closely watching power draw and surface finish, you will know when it is time to dress before problems get out of hand. With consistent dressing, and seeking expert help when needed, companies can overcome grinding challenges and greatly improve productivity.
Whether transitioning from conventional abrasives to CBN or seeking to refine existing grinding processes, mastering proper dressing techniques with Diamond Rotary Dressers holds the key to consistent and dependable success. Check out more grinding related topics in other episodes of The Grinding Chronicles from Continental Diamond Tool.
Understanding the Distinction Between CBN and Aluminum Oxide Abrasives
Uncover the secrets behind top-notch results in grinding and machining of tough steels and metals. Discover the unique properties of Cubic Boron Nitride (CBN) and Aluminum Oxide and learn how to choose the right abrasive for optimal efficiency and precision.
Are you ready to explore the fascinating world of abrasives? In manufacturing, we often encounter Superabrasives and Conventional abrasives. In the Superabrasives corner, we have Diamond and Cubic Boron Nitride (CBN), and their common Conventional abrasive counterparts are Silicon Carbide and Aluminum Oxide. Each serves a specific purpose. What makes CBN and Aluminum Oxide stand out is their exceptional ability to tackle those stubborn steels and metals that can't stand Carbon.
In this blog, we'll explore the properties and applications of CBN and Aluminum Oxide abrasives. Discovering their unique characteristics will help you choose the right abrasive for your specific machining needs, ensuring efficiency and top-notch results. Whether you're working with hardened steels or softer metals, the right abrasive is the key to achieving your desired outcome in grinding and machining. So, let's dive in and unlock the true potential of CBN and Aluminum Oxide abrasives.
What is CBN?
CBN is a synthetic Superabrasive known for its incredible hardness, high thermal conductivity, and thermal stability. Originally released with the trade name Borazon from GE Superabrasives, its cubic crystal lattice structure is similar to Diamond, giving it remarkable abrasive properties. With a hardness close to 10 on the Mohs scale, CBN excels in machining tough materials that require precision grinding. Its chemical composition and high thermal stability prevents chemical reactions and premature breakdown under high temperatures, when grinding ferrous metals and high-temperature alloys. What's more, because CBN doesn't react with ferrous materials, it doesn’t alter or change their properties resulting in longer life in use when ground with CBN.
CBN is a game-changer when grinding hardened ferrous alloys or super alloys that are sensitive to heat. It efficiently grinds hardened steels while maintaining accuracy and surface finish. Plus, it's a favorite for grinding ferrous metals like cast iron and stainless steel, ensuring clean and precise results without chemical alterations. CBN is a must-have tool for achieving precise and efficient outcomes in critical machining tasks.
What is Aluminum Oxide?
Aluminum Oxide, also known as alumina, is a versatile Conventional abrasive. With high hardness and toughness, it is available in various grit sizes, making it perfect for a wide range of machining and finishing applications. Though not as hard as CBN, Aluminum Oxide is fantastic for soft metals, wood, and non-ferrous materials. While it may not match the precision of Superabrasives, it's still a reliable choice for many tasks.
In the machining industry, Aluminum Oxide is the go-to for grinding soft metals like aluminum, brass, and copper. It performs beautifully with non-ferrous materials such as bronze and titanium, without causing any chemical interactions. Its role in achieving desired surface finishes across various industries, from automotive to aerospace, is unparalleled.
Key Differences Between CBN and Aluminum Oxide Abrasives
While CBN and Aluminum Oxide both play significant roles in grinding and machining operations, they have many distinct properties that set them apart.
Crystal Structure and Hardness: CBN's crystal lattice structure is similar to Diamond, resulting in exceptional hardness and wear resistance. Aluminum Oxide, while still hard, has a lower hardness than CBN, making it more suitable for soft metals and certain alloys.
Heat Resistance and Thermal Conductivity: CBN exhibits superior heat resistance and thermal conductivity compared to Aluminum Oxide, making it perfect for grinding high hardness and heat sensitive alloys.
Material Compatibility and Reactivity: Both CBN and Aluminum Oxide are chemically inert with ferrous materials whereas Diamond and Silicon Carbide are not, thus why they are the abrasives for ferrous metals.
Cost and Practicality: CBN grain costs significantly more than Aluminum Oxide grain, resulting in higher grinding wheel prices. Because of higher hardness and better thermal conductivity, CBN wheels can provide lower grinding costs in applications where high workpiece hardness and thermal properties need to be maintained. In cases of grinding soft steels and low volume production, the lower wheel price of Aluminum Oxide makes it a more competitive option.
Safety Considerations and Handling
Whether you choose CBN, Aluminum Oxide, or another solution for your abrasive, ensuring safety during grinding and finishing processes is essential. Proper machine guarding, eye and respiratory protection, proper dust/mist extraction, and careful handling and storage of abrasives are crucial to protect workers and maintain a clean and safe work environment.
Selecting the Right Abrasive for Specific Applications
Choosing the right abrasive for your specific machining needs is vital to achieving optimal results. Making an informed decision will ensure efficient, accurate, and cost-effective grinding and finishing processes. Some factors to consider include:
Workpiece Material Characteristics: Soft metals like aluminum, brass, copper, and mild steels may need moderate hardness abrasives like Aluminum Oxide to prevent excessive material removal, while harder materials like hardened steels and high-temperature alloys such as inconel and hardened Stainless Steel require abrasives with superior hardness and high thermal conductivity like CBN for precise and efficient cutting and grinding.
Machining Operations and Efficiency: Superabrasives like CBN are preferred for high-precision tasks where tight tolerances and maintaining material properties are paramount, while conventional abrasives like Aluminum Oxide offer lower cost solutions for general grinding of mild steel and soft metals.
Surface Finish and Material Removal Rates: Superabrasives like CBN excel in production applications of hardened steels and Superalloys that are sensitive to heat, , while conventional abrasives like Aluminum Oxide are effective in low volume applications and for grinding of soft metals.
Tooling and Machinery Considerations: Abrasive selection also needs to account for machinery and tooling capabilities. The truing and dressing of Superabrasive and Conventional Abrasive grinding wheels can be different and require different tools (stationary or rotary dressers of different configurations). Because of the difference in hardness between CBN and Alumina, Alumina being much lower, the amount of grinding debris resulting from wheel wear during grinding can be 100-300 x’s greater with the conventional wheel, which in turn needs to be disposed of. .
Both CBN and Aluminum Oxide abrasives offer distinct advantages in grinding and machining. Considering their unique properties with specific application requirements will lead to efficient and precise processes, ensuring optimal results and safety in the workplace. And if you ever need assistance, our grinding experts at CDT are here to help. Whether it's Superabrasives or Conventional abrasives, we can help find the perfect solution for your process.
Superabrasive Grinding Technology for the Ceramic Industry
We explore the transformative impact of custom superabrasive grinding products on the ceramics industry, highlighting the benefits they offer and the cutting-edge technologies driving these innovations.
The rapid growth of ceramic and carbide components in industries such as Automotive, Aerospace, Medical, and Electronics has created new challenges for grinding professionals. The hardness, abrasiveness, and brittle nature of ceramics and carbides make them difficult to grind efficiently. Yet advancements in superabrasive grinding technology have paved the way for improved grinding processes and reduced cycle times for those that invest in new custom technology. In this article, we explore the transformative impact of custom superabrasive grinding products on the ceramics industry, highlighting the benefits they offer and the cutting-edge technologies driving these innovations.
Overcoming Grinding Challenges in the Ceramics Industry
Ceramic and Carbide materials pose unique challenges when it comes to grinding due to their unique hardness and abrasive properties. Traditional metal bond and resin bond grinding wheels have been the go-to solution for grinding these materials. However, advancements in CNC grinding equipment and the introduction of new bond systems have revolutionized the way ceramic and carbide components are ground.
In different industries like electronics, optics, aerospace, and advanced manufacturing, people are using carbide and ceramic coatings to make components last longer and better at handling heat. Two common ways to add these coatings are HVOF (High-Velocity Oxygen Fuel), which uses high-speed flames to spray the coating onto surfaces, and HVOC (High-Velocity Oxygen-Fuel Cold Spray), which works at lower temperatures with fast-moving gas. Another method is Chemical Vapor Deposition (CVD), where a thin layer of material is deposited on a surface through chemical reactions in the vapor phase. Using CVD or HVOF/HVOC can make components longer lasting and more wear resistant.
The inclusion of carbide or ceramic layers necessitates special consideration during the grinding process because of the inherent hardness and abrasive properties of these materials. Superabrasive grinding wheels offer superior performance in grinding these materials by reducing grinding forces, lowering power consumption, and minimizing subsurface damage. These innovative grinding products are particularly effective in reducing grinding cycle times and reducing scrap, resulting in significant cost savings and enhanced productivity.
Advances in Superabrasive Grinding Technology
The advent of multi-axis CNC grinding with Rotary Dressers has automated grinding processes, increasing efficiency and accuracy. Spindle & High-Pressure Coolant systems have improved the delivery of coolant to critical grinding areas, optimizing swarf removal and improved the cooling and lubrication during the grinding process. High-speed grinding spindles enable a wider range of bond technology and wheel sizes to be used for ID and smaller part grinding.
New "Cutting Tool" designs, such as slotting, high porosity bonds, coolant holes, and CNC adaptors for improved rigidity, have improved tool life and performance. These designs enhance coolant flow, chip evacuation, and overall tool effectiveness, contributing to longer tool life and reduced downtime.
Innovative bond systems have been developed to address the unique challenges of grinding ceramic and carbide materials. These new bonds lower grinding forces, reduce power consumption, and lead to faster cycle times. They also minimize subsurface damage resulting in lower scrap rates while enhancing the quality and integrity of the finished components.
Superabrasive Grinding Products for Ceramic & Carbide Components
CDT's superabrasive solutions deliver significant benefits, including a reduction in grinding forces by 30% or more (compared with resin & metal bonds), reduction in cycle times by up to 50%, and significant reduction in scrap rates on these critical and costly components. These advancements help manufacturers optimize their grinding processes, increase productivity, and reduce costs.
Continental Diamond Tool (CDT), a leading provider of superabrasive solutions, offers a comprehensive range of grinding products designed specifically for the ceramics & carbide industries. Their products are compatible with major industry equipment manufacturers, including Studer, Kellenberger, Danobat, Walters, ANCA, Junker, Okuma, Koyo, USACH, Lapmaster, Peter Wolters, SpeedFam, Stahli, Supfina, and many more. CDT also offers advanced custom tool designs, such as cross cutters and hole drilling with flat bottom drills, to address specific grinding requirements. Their expertise extends to a wide range of equipment, including round tools for Anca, Haas, ITM, Normac, Rollomatic, Star, and Walters, as well as inserts for Agathon, Coborn, EWAG, Waida, and Wendt. Additionally, CDT has created surface grinders for Arter, BLOHM, Brown & Sharp, Chevalier, ELB, and Magerle, as well as Blanchard grinders for Blanchard, Bourn & Koch, and DCM.
Superabrasive grinding products have revolutionized the ceramics & carbide industry, overcoming the challenges presented by the high hardness and abrasive nature of these materials. With reduced grinding forces, faster cycle times, and reduced scrap rates, manufacturers can achieve greater efficiency, productivity, and cost savings. Continental Diamond Tool's advanced superabrasive solutions provide tailored grinding products for a wide range of equipment, enabling manufacturers to optimize their grinding processes and achieve exceptional results. As industries continue to evolve to use more ceramic & carbide materials, the use of superabrasive grinding products will undoubtedly play a crucial role in meeting the growing demand for efficient production of these components.
7 Reasons Why Vitrified CBN Grinding Wheels Surpass Conventional Grinding Wheels
Discover 7 reasons why CBN grinding wheels are your next game changer >
A vitrified CBN grinding wheel is a superabrasive grinding wheel made from a Cubic Boron Nitride abrasive in a porous – or “vitrified” (ceramic) – bond.
Vitrified CBN Grinding wheels are the most cost effective solution for production grinding of ferrous metals and aerospace alloys, and offer far superior performance when compared with conventional abrasive grinding wheels.
Especially for those in industries such as:
Aerospace
Automotive
Bearing
Medical
Gears
Mold & Die
Round Tools (drills, reamers, taps, etc)
Cutting Tools
So why exactly is that?
There are 7 critical reasons why making an upgrade to a CBN grinding wheel can make a huge difference in your industry.
1. 100 - 300x The LifeSpan
CBN abrasive is the second hardest material known to man and is 2 ½ times harder than Aluminum Oxide. Because of its high hardness, the CBN crystals offer 100-300 times the lifespan when compared with traditional grinding wheels.
While Vitrified CBN grinding wheels may cost up to 10 times that of a conventional wheel, the extended wheel life far exceeds the initial wheel cost, making it more cost effective. You get what you pay for – and this is definitely one of those products where you’ll quickly see the difference in its longer lasting abilities as compared to your old grinding wheels.
(We’d even argue that once you’ve used a CBN grinding wheel, it’s hard to go back – it’s just that big of a difference).
2. Reduced Thermal Damage
Because CBN abrasive has almost 50 times the thermal conductivity of conventional abrasives, it transfers the heat generated from the grinding process away from the workpiece, rather than being absorbed by the workpiece.
Combining the high thermal conductivity of CBN with the porous vitrified wheel structures, most heat is efficiently removed through the wheel and coolant, preventing heat damage to your workpiece.
With efficient removal of heat, your workpiece won’t be subject to thermal degradation or changes to the material properties – which is very important for improved wear and life of each component.
3. Optimize Your Grinding Process
With high life and improved thermal properties, Vitrified CBN can be pushed harder during grinding, and decreased grinding cycle times are able to be achieved.
As a result, the grinding process can be more readily automated. This creates less need for more grinding machines, floor space, wheel changes, waste generation, and operators – which has many advantages when it comes to your time, cost, and safety measures.
4. Customizable
Vitrified CBN grinding wheels are engineered per specific customer applications so you can achieve optimal performance.
Considerations that can be taken into account include: material being ground, grinding machine, coolant type and delivery, dressing method, stock removal, quantity of parts, etc… And aggressive, free-cutting bonds can also adapt to various spindle speeds. Which is not only convenient, but also cost effective.
5. Lights Out Operation
Vitrified CBN grinding wheels have “dressable” structures – which lend them to “lights out operation.” The grinding layer can be refreshed using a rotary, and in some cases, stationary dresser.
You’ll be able to automate every step of the manufacturing process, making Vitrified CBN grinding wheels an excellent choice for production based applications.
6. Re-Truing of Formed Profiles
Another benefit of having a “dressable” structure is that complex forms and geometries are able to be generated in Vitrified CBN grinding wheels. The profiles are able to automatically regenerate in line on the properly equipped grinder and maintain tight tolerances.
7. environmentally friendly
The use of Vitrified CBN wheels (as opposed to conventional abrasive wheels) results in significant reductions in waste generation. It decreases the amount of grinding debris (swarf) >99%.
It even allows for more recycling of the metal swarf that is generated because it is oftentimes free of grinding wheel breakdown. Many customers are able to get credit for the Environmental and waste reduction initiatives under ISO14000 and other programs.
Experience the cost effective solution for production grinding with Vitrified CBN Grinding Wheels. Contact us for your free quote.
Who Uses Vitrified Grinding Wheels and Why?
At CDT, our Vitrified products generally serve two distinctly different markets, Vitrified CBN and Vitrified Diamond. Learn about what makes a Vitrified wheel and the capabilities Vitrified has.
At CDT, our Vitrified products generally serve two distinctly different markets, Vitrified CBN and Vitrified Diamond. As the two hardest known materials, CBN and Diamond are referred to as superabrasives and both are excellent thermal conductors.
These abrasive properties when combined with our porous vitrified structures allow for:
longer wheel life
shorter grinding cycle times
automated grinding production capabilities with wheels dressed right on the grinder
CBN vs. Diamond
Vitrified CBN products are ideal for steel and ferrous alloy grinding applications in automotive, aerospace, medical, production tooling, etc. They are excellent thermal conductors and do not react with ferrous materials during the grinding process like diamond does.
We regularly customize Vitrified Diamond products for grinding ceramic and carbide materials used in industries such as glass, ceramics, computer chip manufacturing, thermal spray coatings, and more. Diamond is the hardest known material with the best thermal conductivity making it the best abrasive where there is no chemical reaction.
We are uniquely qualified in both types of Vitrified products because of our full range of manufacturing capabilities and technical application support. Because we handle the vitrification process entirely onsite, we have full control of the manufacturing process and a standard lead time of about 3-4 weeks — about half as long as the industry standard.
The Vitrification Process
At CDT, we use a cold press and sintered process to press near net shape with highly and tightly controlled sintering. This fuses the Vitrified/Ceramic bond together with the Diamond or CBN into a porous structure. CDT's vitrification process is unique in how our engineers have developed a series of custom bonds, formulations, and structures to offer our customers superior grinding performance when compared with off-the-shelf or other competing products.
Combining either of these two abrasives with a porous vitrified bond offers a very strong and stiff system in which the porosity brings coolant into the grinding zone. This innovation removes heat and grinding debris (or "swarf") to extend the wheel life and improve performance. CDT's Vitrified Diamond and CBN wheels generally provide 100 to 300 times the grinding wheel life and maximize the amount of material being ground compared with conventional grinding wheels.
Reducing Cycle Times
"Cycle Time" is the term used to describe the grinding process. Our porous vitrified grinding wheels offer greater efficiency through more effective coolant delivery and swarf removal. This also extends the life of the grinding wheel requiring less downtime for wheel dressing.
When compared with conventional wheels, we see an 80-90% cycle time reduction with our custom vitrified wheels. Even compared with other superabrasives such as Resin and Metal Bond Diamond and CBN wheels, we see 40-75% reductions in cycle times with vitrified wheels.
From military/defense and energy sectors to mold & die markets and everything in between, we have found unique opportunities for more efficient grinding using custom Vitrified products in many industries. Our engineers would be happy to discuss the parameters for your process and provide a free analysis and quote for a custom grinding solution that works best for your application. Contact us today >