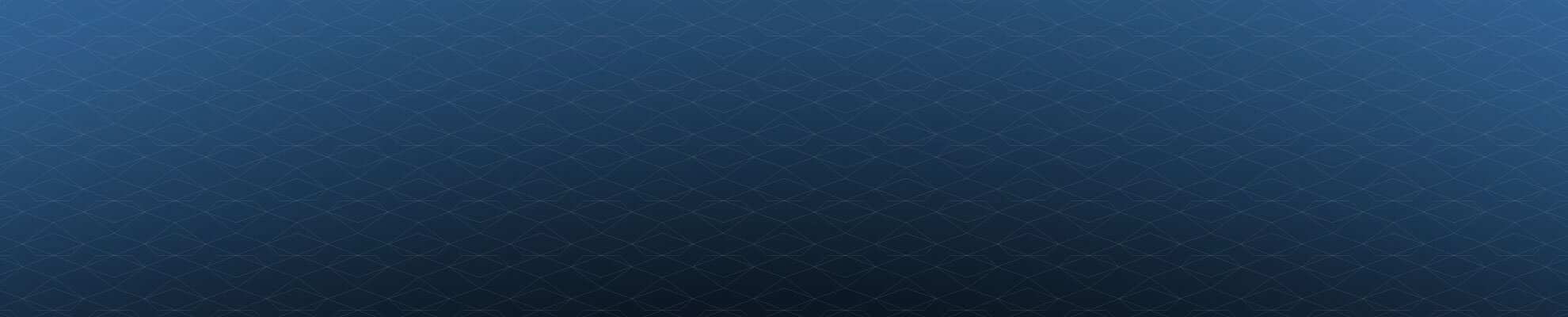
News and Resources
Browse by Category
Browse by Product
- All Dressing Products
- All Grinding Products
- CBN-Diamond Superabrasives
- Conventional Abrasives
- Diamond Lapping Compounds
- Diamond Rotary Dressers
- Diamond Stationary Dressers
- Hybrid Bond Grinding Tools
- Metal Bond Grinding Tools
- Plated Grinding Tools
- Resin Bond Grinding Tools
- Vitrified Bond Grinding Tools
How to Dress a Vitrified CBN Grinding Wheel with a Diamond Rotary Dresser
In episode 5 of The Grinding Chronicles, CDT Product Manager Troy Giacherio shares top techniques for dressing Vitrified CBN grinding wheels using Diamond Rotary Dressers. Learn how to use key parameters such as velocity ratio and overlap ratio to enhance dressing and truing operations in precision grinding.
If you work in manufacturing, particularly in the specialized area of precision grinding, it cannot be overstated the importance of wheel dressing to maintain operational efficiency and product quality. In this comprehensive guide, we will look at the best techniques for traverse dressing a vitrified cubic boron nitride (CBN) wheel using Rotary Diamond Dressers. In Episode 5 of The Grinding Chronicles, CDT Product Manager Troy Giacherio details the specific parameters and most important factors necessary for achieving peak performance in dressing and truing operations. Watch Troy’s video or read on to learn more.
The Grinding Chronicles - Episode 5
Best Techniques for Success When Dressing a Grinding Wheel
Before plunging into the specifics of dressing a Vitrified CBN wheel, it's imperative to understand the dichotomy between two fundamental processes: truing and dressing. Truing involves sculpting the shape or profile of the grinding wheel, while dressing focuses on sharpening the wheel and removing accumulated debris. While diamond rotary dressers serve both functions, understanding this distinction facilitates the implementation of effective dressing strategies.
Essential Parameters for Dressing Success
There are four key parameters to measure for optimizing the dressing of a grinding wheel:
Velocity Ratio At the heart of dressing lies the velocity ratio, calculated by dividing the velocity of the diamond roll by the velocity of the grinding wheel. This parameter holds significant importance in dressing operations. For Vitrified CBN wheels, the recommended velocity ratio stands at 0.8. Maintaining this ratio ensures that the diamond roll adeptly removes the bond material, laying bare fresh abrasives for optimal grinding performance.
Overlap Ratio The overlap ratio describes the velocity at which the diamond dresser traverses the wheel's face to sculpt its profile and hone its edge. For Vitrified Bond CBN wheels, an overlap ratio ranging between 2 to 4 is ideal. Sustaining a steady pace ensures a seamless traversal across the grinding wheel. It is important to prevent the dresser from dwelling in any single spot to guarantee uniform dressing proficiency.
Depth of Dress The depth of dress measures the extent to which the diamond roll plunges into the grinding wheel, thereby dictating the volume of material extracted per pass. When it comes to Vitrified CBN wheels, we recommend a precise depth of dress set at 0.0002 inches per pass. Adherence to this specification not only optimizes grinding efficiency and minimizes downtime, particularly in high-volume production environments, but also preserves the longevity of the grinding wheel, yielding an optimized return on investment.
Dress Interval The dress interval is defined as the frequency at which the grinding wheel needs dressing, and it is closely tied to the application at hand. Unlike their conventional abrasive counterparts, Vitrified CBN wheels do not require frequent dressing. On the contrary, it is not uncommon to grind hundreds of parts between each dressing session. However, it is important to remain vigilant. Keep an eye on the process and be prepared to adjust the dress interval if part quality diminishes.
When Should I Dress My Grinding Wheel?
Dressing frequency varies depending on several factors specific to your process. Here are two key indicators to monitor in order to assess grinding efficacy and determine when it's time to dress your grinding wheel.
Power Draw The power draw during grinding operations can be a reliable indicator for grinding wheel dressing. A drop in power draw signals that the wheel is cutting freely, with utmost efficiency, while an uptick in power suggests a looming need for dressing. Neglecting timely dressing can lead to issues such as burn or unwanted variations in surface finish. That’s why it is important to keep a close eye on power draw dynamics to prevent such issues.
Surface Finish The surface finish of machined parts relies heavily on consistently high levels of grinding performance. A well dressed wheel produces exceptional surface finishes characterized by minimal variations and unyielding consistency in part quality and dimensional accuracy. Therefore, regular dressing sessions conducted with meticulous technique are essential for maintaining superb parts quality and excellence.
Troubleshooting and Optimization
If you are still experiencing issues such as finish patterns or burn despite adhering to prescribed dressing parameters, it may be time to call in the assistance of an expert. Companies like Continental Diamond Tool have application engineers who are trained to analyze grinding processes, pinpoint underlying issues, and facilitate optimization for enhanced performance. Armed with a portable grinding lab, these experts bring their expertise on-site to meticulously evaluate coolant delivery systems, fine-tune machine settings, and traverse a gamut of other variables to resolve persistent challenges. With their help, you can galvanize productivity to unprecedented heights. If you would like help with your wheel dressing or grinding process, don't hesitate to reach out to our engineering team at TheGrindingChronicles@CDTUSA.net.
Mastering Wheel Dressing
Proper dressing of a Vitrified CBN grinding wheel with a Diamond Rotary Dresser is the key to optimal grinding performance and part quality. By incorporating the parameters and techniques we’ve outlined in this article, manufacturers can achieve reductions in downtime, extension of wheel life, and unwavering consistency in high quality results.
Additionally, by closely watching power draw and surface finish, you will know when it is time to dress before problems get out of hand. With consistent dressing, and seeking expert help when needed, companies can overcome grinding challenges and greatly improve productivity.
Whether transitioning from conventional abrasives to CBN or seeking to refine existing grinding processes, mastering proper dressing techniques with Diamond Rotary Dressers holds the key to consistent and dependable success. Check out more grinding related topics in other episodes of The Grinding Chronicles from Continental Diamond Tool.
Meet The Team Behind CDT's High Performance Resin Bond Products
Meet the skilled team driving innovation in precision grinding wheel manufacturing of CDT Resin Bond products. For over four decades, these professionals have crafted custom solutions that guarantee precision and reliability.
Behind every exceptional product is a dedicated team committed to excellence. At CDT, this is exemplified by our Resin Bond department, where talented individuals collaborate to create high-performance Resin Bond CBN and Diamond tools tailored to meet the unique needs of customers. This video and article tell the story of our remarkable team and their dedication to crafting superior products.
The Ingredients for Success in manufacturing Custom RESIN BOND Grinding Wheels
An Experienced Team
Since its launch in 1978, the Resin Bond product line has been a cornerstone of CDT's success, constituting a sizable market and just over 18% of CDT’s outgoing sales in 2023. With 40 years of experience in the industry, Resin Bond Product Line Manager Jim Fell proudly states, "We can tailor a product to anything that the customer needs, any type of specification that they need, and any type of application."
Having worked at Continental Diamond Tool for more than two decades, Resin Bond Pressing Lead Nick Rorick embodies the spirit of craftsmanship and dedication that has put CDT Resin Bond CBN and Diamond Grinding Wheels on the map. In his video interview, Rorick emphasizes, "What sets us apart is the team we have behind our products here at CDT. They put their heart into every tool they make."
Customer Focus
At CDT, customer satisfaction is our top priority. Jackson Birkenbeul, a Resin Bond Design Engineer, emphasizes the importance of addressing customer needs promptly and precisely. In the video, he remarks, "Our focus is not just on manufacturing products but on solving customer challenges." This dedication to understanding and meeting customer requirements underscores CDT's commitment to excellence and service.
Innovative Process
Using a combination of phenolic resin and CBN or Diamond superabrasive, our Resin Bond engineering and production team can design and manufacture thousands of product combinations. The production process begins with formulating a recipe that is tailored to the customer's specific application. A unique blend of bond material, abrasive, and fillers are purposefully selected to optimize grinding performance.
The custom formulation undergoes meticulous mixing in specialized tumblers before being poured and packed into mold cavities. Then, molds undergo hot pressing, where precise control over temperature and pressure ensures the creation of grinding wheels with the desired density. Finally, the wheels proceed to finishing, where they are machined and ground to achieve the intended size and geometry, allowing our Resin Bond products to be tailored to any specification required.
A Multitude of Applications
"Anything that can be cut, ground, polished, or sharpened, we can do," says Kyle Hockemeyer, CDT Pressing Tech. "In precision grinding, the consistency and repeatability of our product is one of our main goals. We strive to get a repeatable process that can be done on a regular basis to have quality, consistency, and delivery in a timely fashion."
Inside the Resin Bond department, 20+ employees work hard to make sure every order meets CDT's high standards for quality and performance. With the addition of a third shift in 2021 and an expansion in 2024 to accommodate new technology and machinery, this product line continues to grow in step with customer demand.
Putting it all together
The Resin Bond team at CDT epitomizes craftsmanship, innovation, and dedication. Their relentless pursuit of excellence and deep-seated commitment to customer satisfaction set them apart in the competitive landscape of precision grinding wheel manufacturing. As our team continues to innovate and push boundaries, customers can trust that CDT's Resin Bond products represent the pinnacle of quality, performance, and reliability.
Conventional Abrasives vs. Superabrasives
In Episode 4 of The Grinding Chronicles learn how the properties of common abrasives impact wheel life and cutting efficiency. Avoid pitfalls with industry expert Jon VanSant.
In Episode 4 of The Grinding Chronicles, Continental Diamond Tool Engineering Consultant Jon VanSant investigates the history of common abrasive materials and their key differentiating characteristics that impact wheel life, cutting performance, and efficiency. Using the wrong abrasive for your application can significantly increase your cost per part. Watch Jon’s video or read the article below to learn the differences between conventional abrasives and superabrasives.
The Grinding Chronicles - Episode 4
Understanding Abrasive Evolution
In the early 1800s, precision grinding relied on naturally occurring abrasives like emery. Fast forward to the late 19th century, and we witnessed pivotal developments with the advent of "Carborundum" or silicon-carbide by Dr. Edward Acheson in 1891, followed by the patenting of 'Alundum' or aluminum oxide by Aldus Higgins in 1904. The landscape changed once again with the introduction of synthetic diamond in 1954 and cubic boron nitride (cBN) in 1957, marking the emergence of superabrasives. Although superabrasives were first synthesized in the 1950’s, it took two decades before commercial products became available.
Distinguishing Characteristics
To understand the difference between conventional abrasives and superabrasives, let’s examine three key characteristics: hardness, thermal conductivity, and friability.
Hardness: An important consideration in abrasive selection, superabrasives like cBN and Diamond demonstrate superior hardness compared to Aluminum Oxide and Silicon Carbide. This is part of what makes superabrasives super, and makes them particularly efficient when grinding extremely hard materials.
Thermal Conductivity: Enhanced thermal conductivity facilitates efficient heat transfer during grinding operations, ensuring minimal damage to the workpiece. This is critical where surface finish is concerned.
Friability: Friability reflects the fracture or impact toughness of an abrasive and underscores another crucial aspect. Analysis reveal a substantial disparity between conventional and superabrasives, with the latter exhibiting remarkable compression fracture strength. When comparing the compression fracture strength of diamond and aluminum oxide at a particle size of 400 microns, there is a 10:1 difference between the conventional abrasive and the superabrasive.
Performance Metrics
Moving beyond physical attributes, an examination of performance metrics such as cut, wear, and dressing efficiency further demonstrates superabrasives prowess.
Cutting Efficiency: Superabrasives like Diamond and cBN require less power and force for cutting operations, ensuring efficient material removal.
Wear Resistance: Superabrasives demonstrate significantly higher wear resistance, leading to prolonged wheel life and reduced downtime when compared to conventional abrasives.
Dressing Efficiency: Superabrasives also excel when considering downtime for dressing since they maintain dressing efficiency over extended periods. In some cases, we have seen up to 20 times the parts per dress. With less frequent dressing comes more consistent performance. Plus, you’re only taking off a tenth of the material in dressing, so your wheel lasts much longer.
Cost Considerations
Superabrasives, with their many advantages, do come with a substantial up-front investment. Even so, many companies see sustainable returns.
Long-Term Value: Superabrasives offer enhanced productivity and cost-effectiveness that often results in lower cost per part over time.
Application Considerations: Recognizing that not every application warrants a superabrasive grinding wheel, factors such as machine tools, fluid compatibility, and work volume must be considered. Superabrasives are most cost effective in high volume, extremely demanding applications.
Expert Guidance
Thank you for joining us on this exploration of grinding wheel abrasives. If you would like help deciding which abrasive would work best to optimize your grinding process, don't hesitate to reach out to our engineering team at TheGrindingChronicles@CDTUSA.net. Until next time, check out additional insights and discoveries on other episodes of The Grinding Chronicles.
Streamlined Finishing and Shipping of Precision Grinding Wheels
Continental Diamond Tool ensures each grinding wheel meets exacting standards, emphasizing precision, quality, and customer satisfaction. Learn more about our meticulous processes in this article.
From aerospace components to medical devices, industries rely on a reliable supply of finely tuned machinery and tooling to achieve optimal, cost effective results. At the heart of many precision machining operations lie custom CBN and Diamond grinding wheels, meticulously crafted to exact specifications. However, the journey from concept to completion involves more than just production. It ends with two critical stages — finishing and shipping —which ensure that these essential tools reach their destinations in prime condition. This article looks at the intricacies of these processes.
Precision in Finishing
Finishing is the bridge between production and the end-user, where the grinding wheels undergo meticulous inspection and refinement. Each custom wheel is subjected to rigorous quality control measures at this final stage, along with incremental checks earlier in the production process, to ensure it meets the stringent standards set forth by the industry and the customer.
Balancing & Surface Enhancement
Surface finish plays a pivotal role in the performance of grinding wheels. Through a combination of advanced and timeless techniques in polishing, the surface is refined to minimize friction and maximize efficiency during operation. Whatever the particular grit size, bond type, or configuration, this step ensures that the wheel’s customization aligns perfectly with its intended use.
It is at this stage that our Finishing Department balances the grinding wheel, making minor modifications as needed. Balancing ensures that our tools produce high quality parts for the customer with reduced scrap, less vibration, and less wear on the spindle and machine.
"The key to working in the Finishing Department is to be a hard worker, detail-oriented, and someone who takes pride in their work," says Tony Police, CDT Finishing Tech. “In this department, we clean and polish tools to get them ready for the quality department to check and ship.”
Inspection and Quality Assurance
At CDT, every order ends with a comprehensive inspection of each grinding wheel. Highly trained technicians meticulously examine every aspect, from dimensional accuracy to surface finish, verifying that it aligns precisely with the specifications dictated by the engineer. Any deviations are promptly addressed to maintain the highest levels of precision for diamond grinding wheels.
“In the quality department, we use advanced technology to compare the tools to the print, make sure they are to spec, and exactly what the application requires,” says CDT Quality Tech Leslie Gurzynski. “At CDT, we regularly invest in new processes to ensure the best results for our customers.”
Customization and Labeling
At this final stage, the grinding wheel is either white labeled or engraved with the CDT logo. Additional labeling with essential information such as part numbers and usage instructions facilitates seamless integration into the customer’s workflow.
Efficient Shipping Solutions
With the finishing touches complete, the focus shifts to the final stage of the process – shipping. Timely and secure delivery is crucial to minimize downtime and keep operations running smoothly. Leveraging efficient shipping solutions ensures that custom precision grinding wheels reach their destination promptly and intact.
Packaging
Proper packaging is crucial to safeguarding the integrity of the grinding wheel during transit. Specialized packaging materials and techniques are employed to minimize vibration and impact, reducing the risk of damage en route. Each wheel is securely encased to withstand the rigors of transportation, providing peace of mind to both the manufacturer and the end-user. Product safety information is accessible through a QR code printed on the packaging. Dressing sticks for wheel maintenance are also routinely included when appropriate for the convenience of our customers.
Logistics Optimization
Efficient logistics management is essential to streamline the shipping process. Leveraging advanced tracking systems and strategic partnerships with reliable carriers, Continental Diamond Tool can ensure timely delivery while optimizing costs. Each month, CDT ships out more than 1,600 boxes of custom products. From domestic shipments to international exports, meticulous planning and coordination ensure that custom grinding wheels reach global destinations efficiently.
"Maximizing quality and efficiency for our customers is our primary goal," says Brad Miller, Shipping Manager at CDT. "With our move into the new building six years ago, and with each expansion, we've created more space to work and a better flow of tooling through final inspection and out the shipping doors."
Customer Support
A commitment to customer satisfaction extends through production, shipping, and beyond. Dedicated technical support teams stand ready to address any inquiries or concerns throughout the shipping process. From tracking updates to post-delivery assistance, proactive communication fosters trust and reinforces our dedication to excellence.
“If a customer faces challenges installing or adjusting the settings for a new grinding wheel, that's where our expertise comes into play,” says Blu Conrad, CDT Application Engineer. “Our application engineers don't just offer remote support; we go the extra mile by personally visiting customers' locations when needed to fine-tune their operations onsite, ensuring optimal performance and satisfaction.”
In conclusion, the finishing and shipping of custom precision grinding wheels are integral components of the manufacturing process. By upholding uncompromising standards of quality and efficiency, Continental Diamond Tool can ensure that these essential tools meet the exacting demands of modern industry. From concept to the production floor, precision drives innovation and excellence every step of the way.
To request a quote or place an order for a custom precision grinding product, please call 800-443-6629 or submit your project specifications using our website’s contact form.
Part Masking of Plated Grinding Wheels
Learn about the process of part masking in the production of plated diamond and CBN grinding wheels. This technique ensures precision and quality in precision grinding across industries like manufacturing, automotive, and aerospace. Find out the specialized skills that are required to excel in this type of work.
Part masking is a crucial technique employed in the plating process for CBN (Cubic Boron Nitride) and diamond grinding wheels. This method involves selectively covering specific areas of a metal substrate before plating to protect them from the plating solution. Part masking plays a significant role in ensuring the precision, quality, and functionality of grinding wheels used in various industries, from manufacturing to automotive and aerospace. In this article, we will delve into what part masking is, how it is done, why it is essential in the plating process, and what it takes to excel at this intricate skill.
What is Part Masking?
Part masking is the process of shielding specific areas or features of a substrate to prevent them from being plated during the plating process. It is achieved by applying a masking material to the surface of the substrate in a controlled and precise manner. The masking material can be in the form of tapes, paints, or other coatings that can resist the heat and duration of time in the plating process.
How is Part Masking Done?
The process of part masking involves several steps:
Surface Preparation
Before masking, the metal substrate is thoroughly cleaned and prepared. This step ensures that the surface is free from contaminants, oils, coolants, machining residues and oxides, which can interfere with the adhesion of the masking material.
Masking Material Selection
The choice of masking material depends on factors such as the type of substrate being plated, the plating process used, and the specific areas that need protection. Common masking materials include specialized masking tapes, latex, and resin-based coatings. Continental Diamond Tool employs all of these methods in its process.
Application of Masking Material
The masking material is applied precisely to cover the areas that should not be plated. This can be done manually or using brushes, stencils, scribes or automated equipment. For more complex patterns, careful attention is given to ensure that there are no gaps or leaks in the masking material.
Cure or Drying
Depending on the type of masking material used, it may need to be cured or allowed to dry thoroughly. This step generally takes a specific amount of time and ensures that the masking material remains intact and impermeable during the plating process.
Plating
Once the wheel has been masked and cured, the substrate is immersed in the plating bath, where the exposed areas are plated with the desired abrasive material, such as diamond or CBN particles. The masked areas remain untouched, preserving their original characteristics.
Mask Removal
After the plating process is complete, the masking material is carefully removed, revealing the plated surface underneath. This can be done through various methods, such as peeling off tapes or dissolving the masking material with solvents.
Why is Part Masking Essential?
Part masking serves several crucial purposes in the plating process for diamond and CBN grinding wheels:
Precision and Quality
Part masking ensures that the plating is applied precisely to the intended areas, maintaining the tight tolerances, quality, and accuracy essential to precision grinding.
Functionality and Performance
By protecting specific features of the grinding wheel, such as arbor holes, flanges or threaded holes, from plating, part masking helps maintain their functionality and performance, ensuring they are dimensionally fit and operate correctly.
Cost Efficiency
Masking reduces the amount of plating material used, minimizing waste and lowering production costs. It also prevents the need for costly post-plating rework to remove unwanted plating.
Customization
Part masking, applied by hand, is customizable. This allows manufacturers to create tailored, complex products to meet specific customer requirements.
What It Takes to Be Good at Part Masking
Part masking is a specialized skill that requires attention to detail, precision, and an understanding of materials and processes. Here are some key attributes and considerations for those looking to excel in this field:
Attention to Detail
Successful metal part maskers must have a keen eye for detail. Precision is paramount in this process, as even the smallest imperfections or gaps in the masking material can lead to plating errors.
Material Knowledge
Familiarity with various masking materials and their properties is essential. Different materials may be required for specific applications, and understanding their characteristics can ensure the right choice is made.
Patience and Dexterity
The application of masking material can be a delicate and time-consuming task. Patience and manual dexterity are necessary to achieve consistent and high-quality results.
Problem-Solving Skills
Maskers may encounter challenges such as complex shapes or irregular surfaces that require creative problem-solving to ensure proper masking.
Adherence to Safety Protocols
Safety is paramount when working with masking materials and plating chemicals. Understanding and following safety protocols are crucial to prevent accidents and exposure to hazardous substances.
At CDT, our masking department has almost 50 years of combined experience in this highly specialized field. The superior quality and stellar reputation of our plated products are a testament to their expertise.
If you are passionate about precision craftsmanship and believe you have the skills and attributes required for part masking, we encourage you to consider career opportunities in this field. At Continental Diamond Tool, we value skilled professionals who can contribute to our commitment to excellence.
To explore potential positions and apply for a rewarding career in electroplating or other positions in our industry, visit our careers page.
How to Order a Custom Electroplated Grinding Wheel
At CDT, we take pride in the excellence of our masking and plating departments. Part masking is an indispensable technique in the production of plated diamond and CBN grinding wheels to ensure the delivery of the very best products. It requires a unique set of skills, including attention to detail, material knowledge, patience, and problem-solving abilities. Those who excel in this field play a vital role in providing the precision, quality, and functionality of grinding wheels used across various industries.
If you are interested in ordering a custom plated grinding wheel or have any inquiries, please don't hesitate to contact our customer service department. Our team can connect you with our experienced plating engineers to start the process today.
Advantages of Using Electroplated Diamond Grinding Wheels for Precision Grinding
Say goodbye to dressing downtime and hello to faster cycle times with electroplated grinding wheels for precision industries like aerospace, automotive, medical devices, and electronics. These wheel are even more cost-effective with our Strip and Replate Program: learn more.
With precision machining and grinding, the selection of tools plays a pivotal role in determining efficiency, profitability, and overall success. Among the many options available, electroplated diamond and CBN (cubic boron nitride) wheels rank high as indispensable assets for many manufacturers worldwide. These tools offer a unique combination of advantages that contribute significantly to superior performance and cost-effectiveness. In this article, we explore four key reasons why these tools are at the forefront of precision machining and grinding.
1. Consistent Distribution of Abrasive Particles
In precision grinding, the even distribution of abrasive particles is often critical for consistency. Electroplated diamond grinding wheels excel in this aspect, ensuring a uniform dispersion of abrasive particles across their entire surface. Unlike alternative bonding methods that may result in irregular spacing of abrasive grains, electroplated tools embed diamond particles evenly in a single layer. This uniformity translates to predictably consistent grinding or cutting performance. The same is true for electroplated cbn grinding wheels.
In practical terms, this means achieving precision and accuracy in your workpiece everytime, pass after pass. Whether working with robust metals, fragile ceramics, or intricate composites, manufacturers can place their trust in electroplated grinding tools to deliver a reliable and uniform cutting or grinding action.
2. Strong Bond Between Abrasive and Substrate
Another distinguishing factor that sets electroplated diamond tools apart is the robust bond formed between the abrasive particles and the tool's substrate. During the electroplating process, diamond grains become firmly embedded within a nickel or other metallic matrix, creating a tool of exceptional durability and resilience.
This sturdy bond ensures that the diamond particles remain securely attached to the tool's surface, even when subjected to high-speed or high-pressure operations. Consequently, these tools maintain their sharpness and cutting efficiency over an extended period, eliminating the need for dressing and maximizing time between replacements. This durability translates into significant cost savings by reducing downtime and material wastage.
3. Free Cutting Action Equates to Fast Cycle Times
Electroplated diamond tools offer a "free cutting action" that speeds up the grinding and cutting process significantly. Unlike conventional tools that may generate excess heat, clog, or wear unevenly, electroplated diamond tools efficiently remove material with minimal resistance.
This means reduced cycle times for manufacturers. Jobs that used to take longer can now be completed faster and with more precision. Whether shaping aerospace components or fine-tuning medical devices, electroplated diamond tools deliver both speed and accuracy. Fast cycle times translate to increased throughput, shorter lead times, and enhanced competitiveness in today's manufacturing landscape.
4. Maintenance and Reconditioning: The Strip and Replate Program
At Continental Diamond Tool (CDT), we go above and beyond to extend the lifespan of electroplated grinding wheels through our innovative Strip and Replate Program. This program harnesses strip technology to safely remove worn-down abrasives without compromising the wheel's core. We employ a chemical solution to delicately eliminate old abrasives, preserving the integrity of the wheel's substrate. After stripping, a new layer of abrasive material is expertly applied through electroplating.
The outcome? A rejuvenated electroplated grinding wheel that performs at its best. These reconditioned wheels undergo rebalancing to ensure optimal performance during extended runs. This program not only maximizes tool lifespan but also minimizes waste, translating into cost savings and reduced downtime.
How Electroplated Grinding Wheels Yield Long-Term Cost Savings
At CDT, our electroplated grinding wheels are engineered to endure heavy usage, consistently deliver high performance, and enjoy an extra-long wheel life compared to other wheel types. This durability translates into substantial long-term cost savings — as much as 40% in some instances. Plus, the "free cutting action" of electroplated diamond tools is a powerful ally for manufacturers seeking faster cycle times without compromising quality. These tools optimize efficiency, boost productivity, and meet the precise demands of modern machining and grinding processes.
Industries Benefiting from Electroplated Grinding Tools
A wide array of industries benefit from the unique advantages that diamond plated tools offer. Here's a glimpse into some of the key sectors where these tools play a pivotal role:
Aerospace: In the aerospace industry, precision and quality are paramount. Diamond plated tools shape and finish critical components like turbine blades, engine parts, and aircraft structural elements. They deliver the precision required to ensure the safety and reliability of aircraft.
Automotive: The automotive industry relies on diamond plated tools for tasks such as sharpening cutting tools, honing engine components, and producing high-precision parts. These tools contribute to the efficiency and durability of automotive systems.
Medical Devices: The production of intricate and high-precision medical devices, including surgical instruments and implants, relies on diamond plated tools. They enable the manufacturing of components with tight tolerances and exceptional surface finishes, crucial for medical applications.
Electronics: Precision is essential in the electronics industry, where delicate components require fine grinding and cutting. Diamond plated tools play a pivotal role in shaping semiconductors, ceramic substrates, and other electronic components with microscopic precision.
Tool and Die Making: Tool and die manufacturers use diamond plated tools to create molds, dies, and precision cutting tools. These tools provide the accuracy needed to produce intricate and high-quality components.
Stone and Glass Processing: In the construction and architectural industries, diamond plated tools are used for cutting and shaping stone, glass, and composite materials. They offer the precision and control necessary for creating custom designs and finishes.
Fiberglass and Composites: Electroplated grinding tools are indispensable for shaping and refining composite materials used in many applications. From boat hulls to automotive body parts to architectural panels, their ability to provide precise shaping and surface finishing ensures the structural integrity and aesthetics of fiberglass and composite products.
The Competitive Edge of Electroplated Grinding Technology
In conclusion, electroplated grinding wheels offer an impressive array of advantages, including consistent distribution of abrasive particles, a robust bond between abrasive and substrate, fast and free cutting action, and an innovative reconditioning option with Strip and Replate. These benefits combine to deliver long-term cost savings, which establish electroplated grinding wheels as the preferred choice for precision machining across a diverse array of industries.
To harness the advantages of electroplated diamond and cbn grinding wheels for your specific machining needs and see the cost savings, consider partnering with trusted grinding wheel manufacturers like CDT, dedicated to delivering exceptional quality and performance.
Understanding Precision Polishing Film and Its Role in Precision Manufacturing
Did you know you can order Precision Polishing Film through CDT? In this article, we talk about Precision Polishing Film and its role in refining surface quality on metals, ceramics, optics, and more. Learn about its types, applications, and integration into precision manufacturing solutions.
In precision manufacturing, achieving a flawless surface finish is fundamental for product functionality and aesthetics. Precision polishing film, a specialized material used in the final polishing stages, stands as an important tool in refining and perfecting surface quality to meet rigorous industry standards.
What is a Precision Polishing Film?
At its core, precision polishing film is crafted by coating an abrasive material onto a flexible polyester substrate. This film refines surfaces and ensures precision across a variety of materials including metals, ceramics, optics, and semiconductor wafers.
3 Types of Precision Polishing Film
There exists several varieties of precision polishing film, each tailored to specific surface refinement requirements:
Mirror Film: Noted for its fine-graded abrasive grains uniformly coating the polyester film, mirror film offers superior sanding capability and durability.
Lapping Film: With micron-graded abrasive grains uniformly distributed in resin adhesive, lapping film consistently delivers accurate and high-quality finishes.
Diamond Lapping Film: The diamond abrasive in this lapping film makes it particularly suitable for precision finishing of extremely hard substances or challenging materials such as ceramic and ferrite compounds.
Broad Industry Applications
Precision polishing films are useful for many applications across diverse industries. They play an essential role in enhancing the surface of roll and shaft materials, flat displays, commutator shafts of micro motors, and magnetic heads and disks. These films are equally prevalent in the manufacture of many disc applications such as plastic lenses, optical devices, fibers, and painted surfaces. Additionally, sheet applications like print circuit boards and optical devices incorporate precision polishing film in their manufacturing processes.
Extending Beyond Our Core Specialties
While Continental Diamond Tool (CDT) is known for its high-quality, custom diamond and CBN grinding products, alongside precision diamond dressing tools, our commitment to excellence encompasses more than our specialized niche. Our expertise extends to supplying other essential grinding and polishing solutions, including precision polishing film, to address the evolving needs of our customers. This highlights our dedication to addressing a wide array of precision manufacturing requirements.
The CDT Advantage:
A Legacy of Quality: We ensure consistent, superior-grade products that adhere to stringent industry standards.
Customized Solutions: Our skilled technicians offer customized solutions, ensuring optimal performance for unique customer requirements.
Comprehensive Support: From concept to implementation, our expert team provides guidance to maximize productivity and achieve the best possible outcomes.
Expanded Offerings: Alongside our core expertise, we equip customers with grinding and polishing essentials, including precision polishing film, ensuring a comprehensive suite of tools for optimal surface refinement.
Backed by Uncompromising Quality
Our precision polishing films, like all products supplied by CDT, are made of the highest quality materials with various thicknesses available, starting at a minimum of 25 microns. The polyester film’s uniform thickness, smooth surface, and strength provides strong resistance to pulling and tearing forces, with less elasticity.
This table outlines the extensive variety of options available:
For detailed information on our precision manufacturing grinding and finishing products and their benefits to your operations, contact us today.
Mastering Precision Grinding with Diamond Rotary Dressers for Plunge Dressing
Master precision grinding with Diamond Rotary Dressers for plunge dressing. Learn how Consort Precision™ Diamond Rotary Dressers provide quicker lead times, hold tighter tolerances, and sustain higher durability in rough environments.
When it comes to precision grinding, achieving exceptional accuracy and control is paramount. One of the key techniques that enable this level of control is Plunge Dressing through the use of a precision diamond rotary dresser. In this blog, we will explore Plunge Dressing and the crucial role it plays in the high tech manufacturing industry. We will also take a step back in time to uncover the history of this essential tool.
Understanding Plunge Dressing
Plunge Dressing is a specialized method used in precision grinding requiring the tightest tolerance controls. The process involves “plunging” a precision rotary diamond dresser with the form of the finish part vertically into the grinding wheel. This approach allows for a mirror image of the part to be put into the grinding wheel which is then used to grind the finished parts to the highest levels of accuracy achievable.
The History of Plunge Dressing
Plunge Dressing, in its essence, is as old as precision grinding itself. It evolved alongside the broader history of abrasive tools and precision engineering, with the diamond rotary dresser as a key component.
The roots of Plunge Dressing can be traced back to the early days of industrialization when grinding processes were becoming essential for the production of precision components. As the manufacturing industry advanced, the need for higher precision, tight tolerances, and complex profile (geometry) control became apparent. This led to the development and refinement of techniques, including the use of the precision diamond rotary dresser or diamond dressing wheel, to enhance the grinding process.
Since 1984, Continental Diamond Tool Limited, then called Consort Precision Diamond Company, has been making precision Hand-Set “Sintered” Rotary Diamond dressers. In 1995, CDT LTD made waves with its development of an electroforming process that greatly reduced the process time for Reverse Plated Diamond Rotary Dressers. With these advances and revolutionary technology in both Sintered and Reverse Plated manufacturing methods, precision Rotary Dressers are now more affordable and accessible to a greater number of industries.
The Benefits of Plunge Dressing with a Diamond Rotary Dresser
Plunge Dressing with diamond rotary dresser, offers a range of benefits that make it a preferred choice in precision grinding:
1. Precise Profile Control: Plunge Dressing with a diamond rotary dresser enables the precise shaping of intricate profiles on workpieces. This level of control is invaluable in applications where tight tolerances and intricate shapes are required with tolerances of 1um or better.
2. Reduced Heat Buildup: The controlled plunge of the diamond rotary dresser results in precise truing and conditioning of the grinding wheel. This is especially important for materials that are sensitive to heat, helping to prevent thermal damage and maintain workpiece integrity.
4. Consistency and Quality: Plunge Dressing with a diamond rotary dresser ensures consistency in material removal, resulting in a high-quality surface finish on workpieces. This consistency is crucial for producing precise components with minimal variation.
The Mechanics of Plunge Roll Dressing
Plunge roll dressing involves a specific mechanical process. Here's a glimpse of how it works:
Preparation: To start, the diamond rotary dresser is set up and aligned with the grinding wheel.
Vertical Movement: Then the dresser is moved vertically into the spinning grinding wheel. The depth of penetration is precisely controlled to ensure the desired material removal.
Material Removal: As the diamond rotary dresser engages with the grinding wheel, it removes material from the wheel's surface. This process allows for the desired profile or shape to be formed on the wheel.
Controlled Withdrawal: After the material removal process is complete, the diamond rotary dresser is withdrawn from the grinding wheel. This is done with the same level of precision and control to maintain the desired profile.
APPLICATIONS for Plunge Dressing with a Diamond Rotary Dresser
Plunge-style diamond rotary dressers find applications in many industries, such as:
Aerospace: In the aerospace industry, where precision and tight tolerances are paramount, plunge dressing with a diamond rotary dresser is used to shape critical components for aircraft and spacecraft.
Medical Devices: Plunge-style diamond rotary dressers are essential for creating intricate and precise components in medical devices to ensure their safety and effectiveness.
Automotive: This type of diamond rotary dresser is regularly employed to craft precision parts for the automotive industry, contributing to the performance and longevity of vehicles.
IN SUMMARY
In the world of precision grinding, plunge dressing with a diamond rotary dresser stands out as a technique that empowers manufacturers to achieve the highest levels of precision and quality. Its control and consistency make it an invaluable tool for industries where tight tolerances and intricate profiles are the order of the day.
Our Consort Precision™ line of Diamond Rotary Dressers offers versatility in design, with custom plunge form dressers available in sintered or reverse plated variants. The plated plunge form rotary dressers have the extra benefit of being able to hold tighter tolerances, where as Sintered Rotary Dressers can have shorter lead times and hold up better in rough environments. Both Sintered and Reverse Plated Rotary Dressers can be manufactured and shipped from our manufacturing facilities in either North America or Europe.
The Science Behind Resin Bond Grinding Wheels: How They Work and Where They Excel
From precise tolerances to fine surface finish, explore the technology, applications, and advantages of Resin Bond superabrasive wheels for precision grinding.
In the world of machining and precision grinding, engineers and manufacturers are constantly seeking ways to enhance efficiency and finish parts to increasingly tighter tolerances. A key player in this arena is the Resin Bond superabrasive grinding wheel. This remarkable technology has revolutionized the way hard materials are shaped and finished. In this article, we will look at the science behind Resin Bond grinding wheels, understanding how they work and why they excel in various applications.
Understanding the Basics
Before we dive into the intricacies of Resin Bond grinding wheels, it is essential to understand the core fundamentals that govern their operation.
1. Resin Bond: Resin is a polymeric (plastic) material that can be formed under specific conditions. At Continental Diamond Tool, our Resin Bond products are created using phenolic and polyimide resins, which are combined with conventional abrasives, superabrasives, and metal powders to form specific grinding structures. The thermosetting resins are the bonding agent that hold the abrasive materials (typically Diamond or CBN) in place. Once blended together, wheel compositions are “hot pressed” to specific sizes & shapes in special molds, and the resins are cured. After hot pressing to near-net shape, they are machined to final dimensions and tolerances for customer use. Resin Bonds are highly regarded for their ability to provide a firm mechanical grip on abrasive particles, ensuring stability during the grinding process. It is this bonding, combined with flexibility of grinding structures, that allow for the customization required for efficient grinding of a variety of materials and applications.
2. Abrasive Material: Abrasive materials are used in grinding, cutting, and shaping processes to remove material from workpieces. They differ in terms of hardness, durability, and efficiency. Superabrasive materials are a special class of abrasive known for exceptionally high hardness, wear resistance, and cutting efficiency. The two superabrasive materials we use at Continental Diamond Tool are Diamond and Cubic Boron Nitride (CBN). Diamonds are ideal for grinding and cutting extremely hard materials like ceramics, glass, and precious stones, while CBN is used for grinding ferrous materials like steel and hardened alloys. When superabrasives are embedded in a resin matrix, it creates an incredibly effective cutting and grinding tool when compared with conventional abrasives like Aluminum Oxide and Silicon Carbide grinding wheels.
3. Wheel Structure: The arrangement of abrasive material and fillers within the resin matrix forms the wheel's abrasive surface. These abrasives can be designed in various shapes and concentrations, depending on the intended application. Variables like abrasive grain type, size, shape, concentration, bond type, porosity, wheel grade, and design are carefully engineered to determine the wheel's performance characteristics: its cutting ability, surface finish quality, heat dissipation, suitability for specific grinding applications, and more.
How It Works
Resin Bond superabrasive wheels are employed in a wide range of applications, from grinding high hardness materials to sharpening other Diamond or CBN cutting tools. For optimal efficiency, Resin Bond grinding wheels perform best with applications that are well-suited to the way these wheels interact with the workpiece.
1. Cutting Action: When a Resin Bond wheel is brought into contact with a workpiece, the Diamond or CBN abrasives on the wheel's surface come into play. Superabrasives are exceptionally hard, making them capable of cutting through even the toughest materials.
2. Heat Generation: As the wheel cuts through the workpiece, friction generates heat. Both Diamond and CBN are excellent thermal conductors, but Resin Bonds do not inherently conduct heat well. As a plastic, Resin Bond deteriorates at pretty low temperatures compared with other bonds. Its wheel performance is best when coolants and compositions are tailored for “dry grinding” applications. In applications where heat dissipation is a priority, Resin Bond formulations can be manipulated by adding conductive metals such as copper or aluminum to remove heat more efficiently.
3. Wear and Tear: Grinding forces erode equipment over time. Unlike traditional abrasive wheels that wear down quickly and require frequent dressing to stay effective, Resin Bond superabrasive wheels can be formulated to be self-dressing. As the abrasive diamonds wear, new grains are exposed, maintaining a consistent cutting edge throughout the wheel's life.
4. Edge Stability: Edge stability refers to a tool’s ability to maintain the sharpness and integrity of its cutting edge over time. The combination of the high hardness superabrasive with the strong mechanical bond of the resin binder provides excellent edge stability and sharpness, which makes for more efficient grinding. Good edge retention increases productivity and reduces cycle times through less frequent tool changes and consistent cutting performance.
5. Performance: Precision tolerances and highly controlled surface finishes are where Resin Bond Diamond and CBN wheels really shine. Their remarkable capabilities in these areas are especially crucial in industries like optics, where the tiniest imperfection can lead to significant quality issues.
The Master of Surface Finish
Here are the top 8 reasons why the unique characteristics of Resin Bond make it favored across industry applications that require fine surface finishes:
1. Uniform Abrasive Distribution: Resin Bond wheels are manufactured using a carefully controlled process that results in a uniform distribution of abrasive particles throughout the wheel. This uniformity ensures that the wheel removes material evenly across the workpiece, preventing irregularities in the surface finish.
2. Self-Dressing Properties: The self-dressing action of Resin Bond grinding wheels helps maintain a consistent cutting edge, which is essential for achieving a smooth surface finish.
3. Cooler Grinding: Diamond and CBN are already excellent conductors of heat, and resin bonds can be formulated with conductive metals to further aid in heat removal. This improved heat dissipation lessens the likelihood of thermal damage, such as metallurgical changes and micro-cracking, which negatively impact surface quality.
4. Flexibility and Conformability: Compared to Vitrified and Metal Bonds, Resin Bonds are relatively soft and flexible, which is advantageous for contour grinding and achieving intricate shapes. This flexibility allows the wheel to conform to the workpiece's surface, ensuring the consistent contact needed for a smoother finish.
5. Controlled Grit Size and Concentration: Resin Bond wheels can be precisely engineered with specific grit sizes and concentrations of abrasive particles to optimize for surface finish requirements. Finer grit sizes and lower concentrations typically produce finer surface finishes, such as those required by polishing applications.
6. Reduced Wheel Wear: As mentioned earlier, Resin Bonds wheels tend to maintain their shape and cutting efficiency over a longer period than conventional grinding wheels. This lower wear rate contributes to a consistent surface finish.
7. Minimized Wheel Loading: Resin Bond wheels are less prone to loading, which occurs when swarf or material being ground adheres to the wheel's surface. Loading can negatively impact the surface finish, but Resin Bond wheels tend to resist this issue, helping to maintain consistent performance.
8. Wide Range of Abrasive Options: Resin Bond wheels are compatible with a wide range of abrasive materials, including Diamond and CBN. By tailoring the abrasive to the specific material being ground, it further enhances fine grinding efficiency.
Areas Where Resin Bond Excels
Resin Bond superabrasive wheels are among the most popular and widely used bond types for a number of other compelling reasons.
1. Versatility: These wheels can be tailored to suit a wide variety of applications, making them indispensable in industries as diverse as automotive, aerospace, medical,and electronics manufacturing.
2. Precision: The accuracy and precision achieved with Resin Bond superabrasive wheels are unparalleled. They produce intricate shapes and finishes with exceptional consistency.
3. Longevity: Thanks to self-dressing properties, Resin Bond superabrasive wheels have a longer operational life compared to conventional abrasive wheels.
4. Reduced Waste: The minimal wear on these wheels results in less material waste, making them an eco-friendly choice for many industries.
5. Reduced Downtime: Less frequent wheel changes and dressing requirements mean reduced downtime and increased productivity for manufacturing operations. Additionally, these tools dress easily for added convenience.
6. Cost-Efficiency: Despite an initial higher cost compared to conventional counterparts, the longevity and efficiency of a Diamond or CBN Resin Bond tool often result in cost savings over time.
7. Hybrid Variants: Hybrid bonds combine characteristics of different bond types. This is especially common with Resin Bond wheels. For example, a hybrid wheel might have a blend of resin and metal bonds to balance precision with heat dissipation.
The Bottom Line
Resin Bond grinding wheels are a testament to advanced materials science and engineering precision. Their ability to cut, grind, and shape materials with unparalleled accuracy and efficiency has made them indispensable in numerous industries, especially in high-precision production grinding applications of hard materials.
These versatile grinding wheels are employed in tasks ranging from centerless and cylindrical grinding to surface and creep feed grinding. They cater to materials as challenging as tungsten carbide, ceramics, and stainless steel, where precision and surface finish are paramount. Resin Bond wheels also excel in cutoff, roll grinding, tool and cutter, saw and knife sharpening, PCD grinding, and surgical tool blade sharpening applications, showcasing their adaptability across the spectrum of manufacturing and fabrication needs. Whether it's the intricate precision required for surgical tools or the robust grinding demands of hardened steel, resin bond grinding wheels are trusted companions for achieving exceptional results.
As technology continues to advance with hybrid bond types, it is likely that Resin Bond superabrasive wheels will play an even more significant role in the quest for perfection in machining and precision grinding. Their adaptability, accuracy, and longevity make them a driving force behind innovation in manufacturing processes and a cost-efficient grinding solution for many industries around the world.
The Story Behind Our Precision Grinding Solutions at Continental Diamond Tool Ltd.
Continental Diamond Tool Limited's Diamond Rotary Dressers set industry standards with cutting-edge technology and award-winning processes. With decades of expertise and product excellence, our dressing and grinding solutions meet the demands of diverse industries worldwide. Learn more about our innovative solutions in precision grinding.
At Continental Diamond Tool Limited, our 40 years of success has been built by delivering the finest custom Diamond Rotary Dressers available in the market. Also called Diamond Rolls, these tools are used extensively in a growing number of grinding operations to primarily facilitate the transfer of highly accurate repeated configurations onto components. What makes a Consort Precision Diamond Rotary Dresser stand out can be summarized in four key aspects: technology, expertise, process, and quality or product excellence. As we have expanded into other product lines, we bring that same commitment to every precision grinding product we produce.
Cutting Edge Technology
In a plunge-style dresser the Rotary Diamond Dresser is mounted onto a spindle of a drive unit which in turn is mounted onto a slideway arrangement that allows the formed periphery of the dresser to infeed into a grinding wheel, thereby transferring the desired shape into it. The form, or configuration, can then be 'ground' on to the component. Plunge dressers are especially accurate for precision grinding as there is no lost form or geometry due to machine movements. Plus, the dressers can be held to submicron levels of accuracy.
Traverse dressing is a grinding wheel dressing technique where the diamond rotary dresser traverses across the surface of the grinding wheel to create a specific profile or shape. Traverse Disc Dressers allow you the flexibility to make profile changes or dress in completely new profiles with the same tool, reducing down time for wheel change overs or roll changes.
INDUSTRY EXPERTISE
Such Industries as the Automotive and Aerospace as well land based Turbine Engine production units employ large quantities of Rotary Diamond Dressers. Typically, within the Aero manufacturing industry, such components as Turbine Blades and Nozzle Guide Vanes as well as Flap Actuating Shafts require their intricate features to be ground with grinding wheels that have been formed with Rotary Diamond Dressers. As can be seen reference is made on our following pages to the many applications within the automotive industry.
CDT Ltd. can offer expertise in the selection of the most appropriate type of Rotary Diamond Dresser by reference to the configuration required and to the grinding machine on which it is to be used. Basically, three processes are employed. Handset Sintered, Random Set Sintered and Reverse Plated. Within each of those categories, selection of diamond type and their placement into the periphery of the Rotary Dresser, plays a major part in determining its operational life and performance. Even before its establishment in 1984, the company’s principals and a large proportion of its employees had many previous years experience in the manufacture of Rotary Diamond Dressers. Bringing with them unique knowledge of the industry, CDT Ltd. — then Consort Precision Diamond — quickly established itself with this one product into the global market of prime and subcontract component manufacturers, earning the respect of competitors and customers alike.
AWARD-WINNING PROCESSES
In respect to the Reverse Plating technique, at Continental Diamond Tool Limited we are particularly proud of the fact that we have been awarded the accolade of winning the BOOST award in the U.K. in 1995 for the design and development of a high speed plating process which dramatically reduced previous lengthy plating times. This achievement gave us a competitive edge against alternative suppliers and satisfied the reduced lead times that customers continue to demand. In the same period, we gained the S.M.A.R.T 1995 award for the development of the electroforming process as an acknowledgement of the reduction in the process time employed in the manufacture of Reverse Plated Rotary Diamond Dressers. CDT Ltd. proudly holds the ISO 9001:2015 Registration Certificate for its Quality Management Systems.
A FOCUS ON PRODUCT EXCELLENCE
The Consort Precision name has become synonymous for outstanding quality and performance in Diamond Rotary Dressers. Since 1984, we have been perfecting the design, development, manufacture, install and maintenance of this advanced dressing technology. This long history with a singular focus has given us the unique ability to provide our customers with the best solution technology can offer. We have the engineering, design, manufacturing and staff resources to supply the highest quality Diamond Rotary Dressers available on the market. Our specialized experience ensures each product we supply is the optimum choice for each individual customer, however demanding and complex the configuration. If an application calls for traverse- or plunge-style rotary dressing, Consort Precision™ Diamond Rotary Dressers are the best tool for the job.
With investment from our parent company, Continental Diamond Tool Corporation, we have expanded our facility in Kinmel Bay to manufacture a wider range of superabrasive products and better cater to a global market. In 2021, an expansion of the Plating lab more than doubled our capacity to produce the high quality tight tolerance reverse plated rotary dressers used by some of the world’s most prestigious corporations. It also paved the way for diversification into electroplated grinding wheels, which we began producing in early 2023. As CDT Ltd. continues to evolve and adapt to the ever-changing technological landscape, we remain committed to delivering innovative solutions and superior products to meet the growing demands of our customers worldwide.
Mastering Precision: How Traverse Diamond Dressing Enhances Grinding Wheel Performance
Discover how Traverse Diamond Dressing enhances grinding wheel performance, maintains precision, and reduces scrap rates. Explore applications across industries and choose the right type for your needs.
Precision in manufacturing is the key to producing high-quality components across various industries, from automotive to aerospace, and even in everyday consumer products. One crucial aspect of achieving this precision is the performance of grinding wheels. In precision grinding operations, where the tolerances can be incredibly tight, grinding wheel performance is paramount. Enter the Traverse Diamond Dresser, a type of diamond rotary dresser that plays a pivotal role in ensuring that grinding wheels are in top form. In this blog post, we will delve into the world of Traverse Disc Dressers and explore how they enhance grinding wheel performance.
The Basics of Traverse Diamond Dressing
The Traverse Disc Dresser is an indispensable wheel profiling tool in the realm of precision grinding. Also referred to as Diamond Wheel Dressers, they are designed to dress and shape profile grinding wheels to maintain an optimal condition. The dressing process involves the removal of abrasive material from the grinding wheel's surface, which can become uneven, clogged, or worn over time due to the abrasive grinding process.
Here's how Traverse Disc Dressers work their magic:
1. Material Removal: These dressers feature a wide range of diamond sizes and grades to achieve the desired dressing condition. As the rotary diamond dresser traverses across the grinding wheel's surface, it precisely and efficiently removes small amounts of abrasive material. This effectively 'cleans' the wheel, restoring its cutting ability.
2. Wheel Truing: One primary function of Traverse Disc Dressers is truing the grinding wheel. Over time, grinding wheels can develop irregularities, affecting the precision of the grinding process. The dresser ensures that the wheel runs true and maintains a consistent, flat or cylindrical shape, depending on the application.
3. Form Dressing: In precision grinding, some applications require intricate shapes or profiles to be ground onto workpieces. Traverse Disc Dressers can be employed for form dressing, which shapes the grinding wheel to match specific profiles with utmost precision.
Achieving Superior Grinding Wheel Performance
Now that we understand the role of Traverse Disc Dressers let's explore how these wheel profiling tools enhance grinding wheel performance:
1. Consistency is Key: Precision grinding demands consistency. Traverse Diamond Dressing ensures that the grinding wheel profile remains uniform in shape, minimizing variations in the workpiece's finish and dimensions. This consistency is essential for meeting tight tolerances.
2. Optimized Material Removal: Dressing the wheel not only ensures precision but also optimizes material removal rates. It enhances the wheel's cutting ability, reducing heat generation and the risk of burning the workpiece—a common issue in precision grinding.
3. Reduced Scrap Rates: With a properly dressed grinding wheel, the likelihood of producing defective or out-of-spec parts is significantly reduced. This translates to lower scrap rates and higher yields, ultimately improving the bottom line.
4. Versatility: Traverse Disc Dressers are versatile tools suitable for various grinding applications. Whether you're grinding metals, ceramics, or other materials, these dressers can be adapted to meet your specific needs.
5. Flexibility: Change parts/profile shapes frequently? Traverse Disc Dressers allow you to quickly and easily make profile changes or dress in completely new profiles without making grinding wheel changes, saving you down time for wheel change overs and/or roll changes.
Applications for Traverse Disc Dressers
Traverse Disc Dressers play a pivotal role in a multitude of precision-driven industries. These grinding wheel truers are essential for maintaining and shaping grinding wheels, ensuring that precision grinding processes yield consistent and accurate results. Here's a succinct overview of how key industries rely on Traverse Disc Dressers:
Automotive: Crucial for precision grinding in tasks like crankshaft and camshaft production, gear manufacturing, and engine component fabrication.
Aerospace: Used in grinding operations for aircraft components and jet engine parts, where precision is paramount.
Tool and Die Making: Maintains the sharpness and precision of cutting tools, including end mills, drill bits, and punches.
Medical Device Manufacturing: Ensures precision in the production of surgical instruments, orthopedic implants, and dental tools.
Bearings and Bearing Components: Shapes and maintains grinding wheels to ensure the accuracy of bearing components.
Cutting Tool Manufacturing: Essential for achieving precise tool geometries and cutting-edge profiles in tools like inserts and taps.
Oil and Gas: Involved in precision grinding for drilling equipment, pumps, and valves, vital in this sector.
Metalworking: Used in the production of gears, shafts, and machine components to meet precision requirements.
Die Casting and Foundry: Maintains and shapes grinding wheels to finish cast components with tight tolerances.
Renewable Energy: Supports precision grinding operations for components in renewable energy technologies like wind turbines and solar panels.
These industries rely on Traverse Disc Dressers for precision and consistency in their manufacturing processes, making them essential tools for achieving the highest levels of accuracy in precision grinding operations.
Types of Traverse Disc Dressers
Traverse Disc Dressers come in distinct types, each designed for specific applications. They can be made with a wide range of diamond sizes and grades, with CVD (chemical vapor deposition) stones, or a combination of the two, to achieve the desired dressing condition.
1. Electroplated: Electroplated Traverse Disc Dressers are known for their short lead times and open and aggressive structure allowing for high removal rates with similar performance at a lower cost.
2. Metal Bond: Metal bond Traverse Disc Dressers offer flexibility with a range of bond systems and abrasives to custom fit the application and provide a balance of durability and precision, making them suitable for a wide range of grinding operations.
3. Sintered: Sintered Traverse Disc Dressers offer exceptional durability and precision and are ideal for applications involving hard and abrasive materials with tight profile tolerances.
4. Reverse Plated: Reverse Plated Traverse Disc dressers stand out due to their unique construction, which allows for unmatched precision and efficiency in shaping grinding wheels. They offer benefits such as reduced dressing time, extended wheel life, improved surface finish, and versatility, making them a valuable asset for industries requiring the highest levels of accuracy in their grinding operations.
It's worth noting that CDTUSA manufactures all types of traverse dressers except Reverse Plated, which will be added to our lineup next year. CDT Limited in Europe (previously Consort Precision Diamond) specializes in Reverse Plated, as well as the other types of diamond rotary dressers. When it comes to grinding wheel truers, our dedicated teams are ready to assist you. Feel free to reach out for a free quote, and let us help you achieve precision and excellence in your grinding operations.
Understanding the Distinction Between CBN and Aluminum Oxide Abrasives
Uncover the secrets behind top-notch results in grinding and machining of tough steels and metals. Discover the unique properties of Cubic Boron Nitride (CBN) and Aluminum Oxide and learn how to choose the right abrasive for optimal efficiency and precision.
Are you ready to explore the fascinating world of abrasives? In manufacturing, we often encounter Superabrasives and Conventional abrasives. In the Superabrasives corner, we have Diamond and Cubic Boron Nitride (CBN), and their common Conventional abrasive counterparts are Silicon Carbide and Aluminum Oxide. Each serves a specific purpose. What makes CBN and Aluminum Oxide stand out is their exceptional ability to tackle those stubborn steels and metals that can't stand Carbon.
In this blog, we'll explore the properties and applications of CBN and Aluminum Oxide abrasives. Discovering their unique characteristics will help you choose the right abrasive for your specific machining needs, ensuring efficiency and top-notch results. Whether you're working with hardened steels or softer metals, the right abrasive is the key to achieving your desired outcome in grinding and machining. So, let's dive in and unlock the true potential of CBN and Aluminum Oxide abrasives.
What is CBN?
CBN is a synthetic Superabrasive known for its incredible hardness, high thermal conductivity, and thermal stability. Originally released with the trade name Borazon from GE Superabrasives, its cubic crystal lattice structure is similar to Diamond, giving it remarkable abrasive properties. With a hardness close to 10 on the Mohs scale, CBN excels in machining tough materials that require precision grinding. Its chemical composition and high thermal stability prevents chemical reactions and premature breakdown under high temperatures, when grinding ferrous metals and high-temperature alloys. What's more, because CBN doesn't react with ferrous materials, it doesn’t alter or change their properties resulting in longer life in use when ground with CBN.
CBN is a game-changer when grinding hardened ferrous alloys or super alloys that are sensitive to heat. It efficiently grinds hardened steels while maintaining accuracy and surface finish. Plus, it's a favorite for grinding ferrous metals like cast iron and stainless steel, ensuring clean and precise results without chemical alterations. CBN is a must-have tool for achieving precise and efficient outcomes in critical machining tasks.
What is Aluminum Oxide?
Aluminum Oxide, also known as alumina, is a versatile Conventional abrasive. With high hardness and toughness, it is available in various grit sizes, making it perfect for a wide range of machining and finishing applications. Though not as hard as CBN, Aluminum Oxide is fantastic for soft metals, wood, and non-ferrous materials. While it may not match the precision of Superabrasives, it's still a reliable choice for many tasks.
In the machining industry, Aluminum Oxide is the go-to for grinding soft metals like aluminum, brass, and copper. It performs beautifully with non-ferrous materials such as bronze and titanium, without causing any chemical interactions. Its role in achieving desired surface finishes across various industries, from automotive to aerospace, is unparalleled.
Key Differences Between CBN and Aluminum Oxide Abrasives
While CBN and Aluminum Oxide both play significant roles in grinding and machining operations, they have many distinct properties that set them apart.
Crystal Structure and Hardness: CBN's crystal lattice structure is similar to Diamond, resulting in exceptional hardness and wear resistance. Aluminum Oxide, while still hard, has a lower hardness than CBN, making it more suitable for soft metals and certain alloys.
Heat Resistance and Thermal Conductivity: CBN exhibits superior heat resistance and thermal conductivity compared to Aluminum Oxide, making it perfect for grinding high hardness and heat sensitive alloys.
Material Compatibility and Reactivity: Both CBN and Aluminum Oxide are chemically inert with ferrous materials whereas Diamond and Silicon Carbide are not, thus why they are the abrasives for ferrous metals.
Cost and Practicality: CBN grain costs significantly more than Aluminum Oxide grain, resulting in higher grinding wheel prices. Because of higher hardness and better thermal conductivity, CBN wheels can provide lower grinding costs in applications where high workpiece hardness and thermal properties need to be maintained. In cases of grinding soft steels and low volume production, the lower wheel price of Aluminum Oxide makes it a more competitive option.
Safety Considerations and Handling
Whether you choose CBN, Aluminum Oxide, or another solution for your abrasive, ensuring safety during grinding and finishing processes is essential. Proper machine guarding, eye and respiratory protection, proper dust/mist extraction, and careful handling and storage of abrasives are crucial to protect workers and maintain a clean and safe work environment.
Selecting the Right Abrasive for Specific Applications
Choosing the right abrasive for your specific machining needs is vital to achieving optimal results. Making an informed decision will ensure efficient, accurate, and cost-effective grinding and finishing processes. Some factors to consider include:
Workpiece Material Characteristics: Soft metals like aluminum, brass, copper, and mild steels may need moderate hardness abrasives like Aluminum Oxide to prevent excessive material removal, while harder materials like hardened steels and high-temperature alloys such as inconel and hardened Stainless Steel require abrasives with superior hardness and high thermal conductivity like CBN for precise and efficient cutting and grinding.
Machining Operations and Efficiency: Superabrasives like CBN are preferred for high-precision tasks where tight tolerances and maintaining material properties are paramount, while conventional abrasives like Aluminum Oxide offer lower cost solutions for general grinding of mild steel and soft metals.
Surface Finish and Material Removal Rates: Superabrasives like CBN excel in production applications of hardened steels and Superalloys that are sensitive to heat, , while conventional abrasives like Aluminum Oxide are effective in low volume applications and for grinding of soft metals.
Tooling and Machinery Considerations: Abrasive selection also needs to account for machinery and tooling capabilities. The truing and dressing of Superabrasive and Conventional Abrasive grinding wheels can be different and require different tools (stationary or rotary dressers of different configurations). Because of the difference in hardness between CBN and Alumina, Alumina being much lower, the amount of grinding debris resulting from wheel wear during grinding can be 100-300 x’s greater with the conventional wheel, which in turn needs to be disposed of. .
Both CBN and Aluminum Oxide abrasives offer distinct advantages in grinding and machining. Considering their unique properties with specific application requirements will lead to efficient and precise processes, ensuring optimal results and safety in the workplace. And if you ever need assistance, our grinding experts at CDT are here to help. Whether it's Superabrasives or Conventional abrasives, we can help find the perfect solution for your process.
Superabrasive Grinding Technology for the Ceramic Industry
We explore the transformative impact of custom superabrasive grinding products on the ceramics industry, highlighting the benefits they offer and the cutting-edge technologies driving these innovations.
The rapid growth of ceramic and carbide components in industries such as Automotive, Aerospace, Medical, and Electronics has created new challenges for grinding professionals. The hardness, abrasiveness, and brittle nature of ceramics and carbides make them difficult to grind efficiently. Yet advancements in superabrasive grinding technology have paved the way for improved grinding processes and reduced cycle times for those that invest in new custom technology. In this article, we explore the transformative impact of custom superabrasive grinding products on the ceramics industry, highlighting the benefits they offer and the cutting-edge technologies driving these innovations.
Overcoming Grinding Challenges in the Ceramics Industry
Ceramic and Carbide materials pose unique challenges when it comes to grinding due to their unique hardness and abrasive properties. Traditional metal bond and resin bond grinding wheels have been the go-to solution for grinding these materials. However, advancements in CNC grinding equipment and the introduction of new bond systems have revolutionized the way ceramic and carbide components are ground.
In different industries like electronics, optics, aerospace, and advanced manufacturing, people are using carbide and ceramic coatings to make components last longer and better at handling heat. Two common ways to add these coatings are HVOF (High-Velocity Oxygen Fuel), which uses high-speed flames to spray the coating onto surfaces, and HVOC (High-Velocity Oxygen-Fuel Cold Spray), which works at lower temperatures with fast-moving gas. Another method is Chemical Vapor Deposition (CVD), where a thin layer of material is deposited on a surface through chemical reactions in the vapor phase. Using CVD or HVOF/HVOC can make components longer lasting and more wear resistant.
The inclusion of carbide or ceramic layers necessitates special consideration during the grinding process because of the inherent hardness and abrasive properties of these materials. Superabrasive grinding wheels offer superior performance in grinding these materials by reducing grinding forces, lowering power consumption, and minimizing subsurface damage. These innovative grinding products are particularly effective in reducing grinding cycle times and reducing scrap, resulting in significant cost savings and enhanced productivity.
Advances in Superabrasive Grinding Technology
The advent of multi-axis CNC grinding with Rotary Dressers has automated grinding processes, increasing efficiency and accuracy. Spindle & High-Pressure Coolant systems have improved the delivery of coolant to critical grinding areas, optimizing swarf removal and improved the cooling and lubrication during the grinding process. High-speed grinding spindles enable a wider range of bond technology and wheel sizes to be used for ID and smaller part grinding.
New "Cutting Tool" designs, such as slotting, high porosity bonds, coolant holes, and CNC adaptors for improved rigidity, have improved tool life and performance. These designs enhance coolant flow, chip evacuation, and overall tool effectiveness, contributing to longer tool life and reduced downtime.
Innovative bond systems have been developed to address the unique challenges of grinding ceramic and carbide materials. These new bonds lower grinding forces, reduce power consumption, and lead to faster cycle times. They also minimize subsurface damage resulting in lower scrap rates while enhancing the quality and integrity of the finished components.
Superabrasive Grinding Products for Ceramic & Carbide Components
CDT's superabrasive solutions deliver significant benefits, including a reduction in grinding forces by 30% or more (compared with resin & metal bonds), reduction in cycle times by up to 50%, and significant reduction in scrap rates on these critical and costly components. These advancements help manufacturers optimize their grinding processes, increase productivity, and reduce costs.
Continental Diamond Tool (CDT), a leading provider of superabrasive solutions, offers a comprehensive range of grinding products designed specifically for the ceramics & carbide industries. Their products are compatible with major industry equipment manufacturers, including Studer, Kellenberger, Danobat, Walters, ANCA, Junker, Okuma, Koyo, USACH, Lapmaster, Peter Wolters, SpeedFam, Stahli, Supfina, and many more. CDT also offers advanced custom tool designs, such as cross cutters and hole drilling with flat bottom drills, to address specific grinding requirements. Their expertise extends to a wide range of equipment, including round tools for Anca, Haas, ITM, Normac, Rollomatic, Star, and Walters, as well as inserts for Agathon, Coborn, EWAG, Waida, and Wendt. Additionally, CDT has created surface grinders for Arter, BLOHM, Brown & Sharp, Chevalier, ELB, and Magerle, as well as Blanchard grinders for Blanchard, Bourn & Koch, and DCM.
Superabrasive grinding products have revolutionized the ceramics & carbide industry, overcoming the challenges presented by the high hardness and abrasive nature of these materials. With reduced grinding forces, faster cycle times, and reduced scrap rates, manufacturers can achieve greater efficiency, productivity, and cost savings. Continental Diamond Tool's advanced superabrasive solutions provide tailored grinding products for a wide range of equipment, enabling manufacturers to optimize their grinding processes and achieve exceptional results. As industries continue to evolve to use more ceramic & carbide materials, the use of superabrasive grinding products will undoubtedly play a crucial role in meeting the growing demand for efficient production of these components.
5 Common Questions About Industrial Diamonds For Grinding
All of the most commonly asked questions are answered in Continental Diamond Tool's latest blog about industrial diamond technology for grinding.
1: What are industrial diamonds, and how are they used in grinding wheels?
Industrial diamonds can be either synthetic diamond or natural diamond and are specifically processed for industrial applications, rather than for jewelry.
Industrial diamonds are used in grinding wheels as an abrasive that removes material from a workpiece through friction and cutting. When the grinding wheel rotates against the workpiece, the diamond particles (abrasives) efficiently remove small particles of the workpiece – resulting in geometry, size, and finish desired.
Because diamond is the hardest known material, grinding wheels with diamond abrasives are commonly used in hard material applications that require high precision and accuracy such as in the aerospace, automotive, medical and semiconductor industries. CDT has experience working with grinding operations in all of these areas.
2: How are industrial diamonds manufactured?
Natural diamonds have been used for a long time in industrial grinding. They are mined from the earth and transported to a plant for processing. Through a system that includes x-ray machines and hand sorting, the gem quality diamonds are separated from industrial diamonds. These small, lower-quality stones, otherwise known as ‘boart,’ can be used in equipment such as grinding wheels, drill bits, and dressing tools.
Synthetic industrial diamonds used in grinding wheels can be made in one of two ways:
High-pressure and high-temperature (HPHT)
Chemical vapor deposition (CVD)
In the HPHT method, diamond-creating materials are put under high pressures and high temperatures to make it form into a diamond. In the CVD method, diamond-creating materials are put in a vacuum chamber where carbon gasses are then added to make it form into diamond.
Whether naturally or synthetically sourced, the industrial diamonds are then crushed, milled, cut, shaped, and polished to customizable sizes and shapes. Then, the particles are bonded together to form a grinding wheel or cutting tool, typically using metal, resin, vitrified materials or electroplated in a single layer onto a metallic substrate.
3: How do the properties of industrial diamonds affect the performance of grinding wheels?
Industrial diamonds are valued for their extreme hardness, wear resistance, and thermal conductivity. All of these impact the performance of a grinding wheel.
Extreme Hardness:
Diamonds are known for their extreme hardness because they are made up of carbon atoms that are held together in a cubic crystal lattice structure. You can think of it like a brick wall, where the precise arrangement and spacing of the bricks represents the arrangement of atoms in the cubic crystal structure. Like a brick wall, diamond is strong and stable, making it difficult to break or become deformed.
Because diamond is the hardest known material, it is not readily scratched by other materials. Instead, it does the scratching. Because of the high strength of the carbon bonds, Diamond has the best wear properties of all abrasives unless chemically attacked by materials that react with carbon.
This gives grinding wheels the ability to precisely cut through and remove material from other hard substances like ceramics, glass and non-iron-containing metals with very precise geometries and dimensional tolerances.
Wear Resistance:
A diamond's wear resistance refers to its ability to maintain sharp edges and cutting ability for longer, which results in longer-lasting grinding wheels that don’t need to be replaced as often.
Diamond particles can withstand high pressures generated during the grinding process – a crucial aspect of grinding that can cause other abrasive options to break down. Whereas the wear-resistant nature of a diamond abrasive maintains a durable, precise size and finish.
Thermal Conductivity:
Diamonds have the highest thermal conductivity of any known material, which is ideal for grinding due to the heat generated by the friction that occurs during the grinding process. Heat can cause abrasive particles in the wheel to become dull and less effective at cutting, as well as cause thermal damage to your workpiece.
Diamonds can conduct heat away from the grinding area more effectively than other abrasive materials. This keeps it cooler, protecting the material being ground from thermal damage and preventing the abrasive from becoming dull.
4: What are the advantages and disadvantages of using industrial diamonds in grinding wheels compared to other abrasive materials?
Advantages:
Diamond is the hardest known material due to it’s strong covalent bonds between carbon atoms and perfect crystal symmetry. Because Diamond is harder than all other materials it is the best choice for grinding and wear resistance. Other abrasives are softer than diamond and therefore do not last nearly as long. Secondly, Diamond also has the best thermal conductivity and therefore removes/dissipates most effectively the heat generated during grinding.
All of this makes diamond an advantageous choice as an abrasive because it will provide a longer-lasting durability, an improved precision, and a better quality finish.
Disadvantages:
Because of its high hardness, it also means that diamonds can’t be easily shaped or molded into different forms. Dressing of diamond wheels is done with Diamond tools, and with Diamond on Diamond, dresser life is low when compared with other abrasive types. Secondly, Diamond grinding wheels are not recommended when grinding ferrous metals as a chemical reaction between Carbon (Diamond) and the metal is possible and results in changes of the material properties of the metal and premature wear of the Diamond grinding wheels, both of which can be detrimental. Therefore, diamond is typically suggested for use in specialized applications for grinding of hard materials such as Ceramics, Carbides, and glasses.
5: What are the latest trends and advancements in industrial diamond technology for grinding wheels?
One of the latest trends in industrial diamonds is the increasing use of synthetic or man made diamonds. Diamonds that are grown in a lab are as real as diamonds mined from the earth. They are identical to natural diamonds in every way, except that they are created in a lab and the specific material properties of the Diamond can be tailored to specific applications..
As this process has gotten more efficient, man made diamonds can now be sourced cheaper and more readily than natural diamonds. Diamond grinding products are becoming more economically viable for a growing number of industries. CDT uses both natural and synthetic diamonds in its superabrasive products.
Another advancement in industrial diamond grinding technology is the creation of hybrid bond grinding wheels. Hybrid wheels combine different types of bond to adhere the abrasive material, such as diamond, to the grinding wheel and achieve superior grinding performance.
Traditionally, diamond grinding wheels use one of a handful of bonding agents to adhere the superabrasive material to the grinding wheel. Bonding options include:
Electroplating
Resin bond
Metal bond
Vitrified bond
Each of these bonding options have different characteristics which result in different pros and cons for the grinding process. You can learn more about the different bond types here.
By combining bonds, hybrid wheels can be tailored to the needs of specific grinding applications, resulting in higher efficiency and reduced costs. CDT specializes in cutting edge, customizable hybrid bonds using diamond abrasives to provide superior results for our customers. You can learn more about our hybrid bonds here.
Industrial diamonds are a crucial component in many grinding processes, and they continue to play a vital role in the manufacturing industry. Because of their ideal thermal conductivity, wear resistance, and hardness, the technology will continue to advance to make the most use out of this favorable material. It is safe to say that industrial diamonds are not going away anytime soon, and their importance in the manufacturing industry will only continue to grow from here!
If you are wondering if diamond grinding wheels or tools would be a good fit for your specific application, contact CDT for a free quote.
CDT Expands Diamond Rotary Dresser Production
Continental Diamond Tool is proud to announce that we’re expanding our capabilities to make custom Diamond Rotary Dressers (also known as Diamond Rolls) in our dressing product line.
For companies in need of grinding wheel dressing, conditioning, and shaping, finding a high quality and cost effective supplier for custom dressing solutions is even easier!
Continental Diamond Tool is proud to announce that we’re expanding our capabilities to make custom Diamond Rotary Dressers (also known as Diamond Rolls) in our dressing product line.
Dressing tools are a necessary aspect of maintaining the natural wear and tear that occurs with superabrasive grinding wheels. When your abrasive becomes dull and ineffective due to particle buildup, it is recommended that you use diamond dressers to clear off the particles and make your grinding wheels perform like new again.
While many tool and cutter grinding shops and other manufacturing facilities use stationary dressers to get that job done, more and more industries are finding uses for diamond rotary dressers — and for good reason!
As industries work with more and more advanced and complex engineering configurations, Diamond Rolls are the clear, superior choice for these applications … but why?
Simple. Diamond Rolls:
Have precision profiles and geometry to match your specific needs
Are designed for your specific needs, surface finish, removal rates, time savings
Come in all shapes and sizes, from simple traverse dress rolls to complex profiles
Not only does it make way for excellent sharpening and fine finishes, it’s cost effective too.
CDT currently offers the following types of Diamond Rolls:
CVD dressers
Sintered Rotary Dressers
Reverse Plated Rotary Dressers
Diamond Rotary Dressers are commonly used in the following industries:
Aerospace
Automotive
Biomedical
Knives and Blades
Bearing
Whether you are in an industry that’s looking for one of the dressing products above — or if you want to work with our engineers to develop something new— CDT is excited to serve your needs with the best possible up-and-coming technology for getting the job done right.
CDT has been in the business of providing solutions for sharpening and refinishing of superabrasive grinding wheels with Stationary Diamond Dressers since our start in 1973. In 2018, we added Diamond Rolls to our dresser line through our acquisition of Consort Precision Diamond in the U.K. who joined us with a solid reputation for making major technological advancements in rotary dresser technology.
Now, after upgrades made in late 2022, Continental Diamond Tool has capabilities to produce many configurations of custom Diamond Rotary Dressers at our U.S. facility in New Haven, Indiana. Call us or complete our contact form for details.
How to Extend the Life of Your Electroplated Grinding Wheel
CDT’s “Strip and Replate” Program is designed to give our customers the highest quality grinding wheel abrasives for the longest time possible, in the most cost effective way for the customer. Learn how this process works and when you might need to do this >
CDT offers what’s called the “Strip and Replate” Program, designed to give our customers the highest quality grinding wheel abrasives for the longest time possible, in the most cost effective way for the customer (more on this in a moment)...
First, let’s cover when you’ll want to opt for this program, and how it works.
Stripping and replating a grinding wheel refers to the process of removing the old, worn-out abrasive material from the surface of a grinding wheel and replacing it with new abrasive material.
When customers opt in for this program, we work with you to create customized tooling that you will be able to use and then bring back to CDT for us to return it to “like new” condition after it begins to wear. This keeps your wheel fresh and performing at optimal levels without having to buy new.
When To Strip and Replate?
There are many reasons why you may need to replace your wheel with new abrasive, including:
The particles on the surface of your abrasive get clogged (potentially from metal shavings or debris from the grinding process)
Your wheel becomes dull from the worn out abrasive
You need to switch from grinding one material to another, and the new material requires a different type of abrasive to be put on your wheel
The grinding wheel has worn down unevenly, causing vibrations and reducing your wheel’s effectiveness
How Does The Process Work?
CDT is able to provide high quality strip and replate services through strip technology that will remove the remaining abrasive on your worn down wheel without damaging the surface finish of the core.
Electroplating involves depositing a thin layer of metal and abrasive particles onto the surface of a grinding wheel by using an electrical current in an electrolytic plating solution.
When a grinding wheel has reached its life, we remove the old abrasive material on your wheel by soaking the wheel in a chemical solution that will safely dissolve the deposited plating without damaging the integrity of the core.
Once the old deposit and abrasive have been removed, we apply a new layer of abrasive material through the electroplating process.
After the new abrasive material has been applied, the grinding wheel is re-balanced to ensure you continue to have smooth operation and optimal performance with your returned “like new” wheel.
When is An Electroplated Grinding Wheel The Best Choice?
Electroplated grinding wheels are considered the superior choice for applications that require complex shapes or geometries. Some specific applications include metal cutting tools, saw and knife sharpening, PCD grinding, and surgical tool blade sharpening – among others.
They’re used in a wide range of industries, including metalworking, woodworking, glass and ceramics, aerospace, automotive, medical, and electronics manufacturing.
Common materials that are compatible with an electroplated diamond grinding wheel include:
Cemented carbide
Glass
Ceramics
Fiberglass
Plastics
And more
Whereas common materials that are compatible with an electroplated CBN grinding wheel include:
Die steel
Hardened carbon steels
Hardened stainless steels
Alloy steels
Aerospace alloys
And more
When you add in the ability to strip and replate, it makes electroplating a superior choice in many ways:
It provides a more consistent and uniform distribution of abrasive particles on the surface of your grinding wheel, which can help ensure consistent grinding results and prevent uneven wear in the future.
Electroplating creates a strong bond between the abrasive particles and the wheel substrate, which helps prevent the abrasive from separating or shedding from your wheel during use.
It can be used to apply a wide variety of abrasive materials, including diamond, cubic boron nitride (CBN), and various types of abrasive grains – and it can be used with both brittle materials and soft metals.
Stripping and replating an electroplated grinding wheel is a relatively quick and straightforward process because they are a single layer wheel. It also allows for precise control over the thickness of the abrasive layer, making it an ideal choice for achieving any customizations you may need for your wheel.
Electroplated wheels can withstand heavy use and provide consistent grinding performance. They don’t need to be reconditioned as frequently as other types of grinding wheels, making them a more cost-effective choice in the long run.
Overall, opting for an electroplated grinding wheel to be reconditioned and used again through the CDT “Strip and Replate” Program can result in 40% more in savings, with consistent performance results, rather than opting for brand new plated products.
If you’re ready to learn how CDT can work with you for a customized electroplated grinding wheel that qualifies for our “Strip and Replate” Program, click the button below to request a quote!
The CDT technical team is ready to provide abrasive solutions to your questions that will increase your performance while reducing waste.
Meet The Next Generation In Hybrid Bond Technology: Ultra High Performance Grinding For The Cutting Tool Industry
At Continental Diamond Tool we are proud to announce that we have officially unveiled our latest breakthrough technology in hybrid bond products – the EVO Hybrid Bond.
At Continental Diamond Tool we are proud to announce that we have officially unveiled our latest breakthrough technology in hybrid bond products – the EVO Hybrid Bond – at the much anticipated Precision Machining Technology Show this past April 2023.
What is EVO Hybrid Bond?
A game-changer in the precision grinding industry, EVO is a custom-designed bond that delivers ultra-high performance results that are impossible for our competitor’s standard Resin Bond wheels to match.
This bond is a new and improved version of CDT's Resin Hybrid Bond, designed specifically to cater to the needs of Tool and Cutter Grinding.
One of the key benefits of EVO is its superior performance that helps produce high-quality cutting tools faster and more efficiently than its past versions.
The bond is uniquely formulated to achieve faster cycle times without compromising on the wheel edge, making it an ideal choice for:
Flute from solid
Regrind
Gash and end work
And relief
What are the benefits of EVO Hybrid Bond?
When you opt for CDT’s EVO Hybrid Bond technology, you can expect superior results in both form retention and surface finish because of its free cutting action.
Additionally, the EVO bond is self-sharpening. This type of technology ensures the life of your wheel is longer-lasting, as is the dressing interval.
It can also withstand much higher temperatures while still maintaining its stability, which makes high material removal rate not only possible, but incredibly precise.
Because CDT’s EVO Hybrid Bond offers excellent heat dissipation capabilities (while ensuring low and consistent power consumption) it enhances your overall efficiency and productivity of the grinding process.
It’s also a much more sustainable option. The wheel profile lends itself to a longer-lasting type of technology that reduces your grinding process costs in the long-term.
What sets EVO Hybrid Bond apart from the competition?
Beyond all of the benefits listed above, what sets EVO apart from other superabrasive grinding products is its unique blend of Resin Bond and Metal Bond.
Available exclusively through CDT, this customizable type of bond is designed specifically to deliver cutting edge results that standard wheels cannot hope to compete with.
For the high precision cutting tool industry, EVO is a long-awaited solution to many common grinding challenges.
The bond offers a faster cycle time, less dressing, and greater performance. It is an ideal solution for those looking to improve their grinding process and achieve their goals.
At CDT, we are committed to providing the latest technology solutions to help the precision cutting tool community overcome their machining challenges. EVO Hybrid Bond is a testament to our commitment, and we are confident that it will transform your grinding process and help you stay ahead of the competition.
How To Select The Right Bond Type
We go over the common bond types (Resin, Metal, Vitrified, Electroplated and Hybrid) to help you select the best bond for your project.
Congratulations! If you are on this website, you’ve probably come to the conclusion that a superabrasive grinding wheel will be the best solution to your project’s needs. If you are still considering the pros and cons of the different types of grinding products, check out this article that explains the differences between superabrasive and conventional grinding wheels.
Once you’ve decided you need a superabrasive solution for your grinding application, what’s the next step?
SELECTING YOUR BOND TYPE
The bond acts as the glue that keeps the abrasive grains in your grinding wheel connected. The bond's strength, also known as its hardness, determines how well the wheel can handle different materials.
Harder bonds are typically recommended for softer materials and vice versa. There is also the option to create custom hybrid bonds that are specially formulated to possess unique characteristics that will better support your more specific needs.
A grinding wheel expert can help you narrow down your selection, as there are many different bond types.
Let’s go over the common ones:
Resin Bond
Metal Bond
Vitrified Bond
Electroplated Bond
Hybrid Bond
RESIN BOND
Resin bonds are the most widely used bond type in superabrasive grinding wheels. Simply put, they are grinding wheels held together with a plastic bond. They are made from synthetic resins, such as phenolic or epoxy, which is used to hold the abrasive in place.
Mostly, these types of grinding wheels are formulated and blended as powders which are then cast and hot pressed in steel molds of the desired size and shape of grinding wheel desired. The specific properties of the bond are determined by the specific resin and additives to get the desired mechanical and grinding properties.
Because of Resin Bond’s resilience and toughness, these grinding wheels tend to be:
Easy to use
Versatile across a broad range of materials & applications
Relatively inexpensive when compared with other superabrasive grinding wheels
METAL BOND
Metal bonds are, as the name suggests, made from metals – such as bronze and iron. Like Resin Bond products, Metal Bond grinding wheels are blended as powders and hot pressed in high temperature alloy or graphite molds as the processing temperature is much higher than resin.
Metal bond is the hardest of the bond types. Because of this, most Metal Bond grinding wheels are made with diamond, the hardest superabrasive, and are used on especially hard materials such as glass, ceramics, and carbides. Between the inherent hardness of the bond and the hardness of the materials being ground, these wheels generate the highest grinding forces and usually require special dressing or conditioning steps during use.
Benefits of Metal Bond grinding wheels include:
Resistance to wear
Longest wheel life
VITRIFIED BOND
Vitrified (or more appropriately known as “glass” or “ceramic”) bonds are different from resin and metal bonds in that they have both a mechanical bond like the others, but also a chemical bond between the abrasive (either dIamond or CBN) and the bond itself. Most commonly, these bonds are engineered with porosity and are “cold pressed” and sintered as opposed to hot pressed.
While the actual glass/ceramic bond is technically harder than metal bonds, the porosity levels make the function better in grinding as the porosity efficiently removes grinding debris (swarf) and brings coolant into the point of grinding. Because of the porosity of these grinding wheels, they are also more readily able to be dressed and formed into specific desired geometries.
Because Vitrified bonded grinding wheels have lower grinding forces and the ability to be readily dressed with rotary dressers, this type of bond is ideal for high volume production grinding applications of hard materials that can most benefit from the:
Lower grinding forces
Faster grinding cycles
Lower scrap rates
In the case of CDT’s VIPER Vitrified Bond grinding wheels, we have enhanced the bond strength over traditional Vitrified Bonds, coupled with a porous vitrified structure, to more perfectly grind some of industry’s hardest materials like silicon carbide, aluminum oxide, glass, carbide, and others. Our VIPER Bond system provides enhanced dressability, lower grinding forces, and shorter grinding cycles over traditional Vitrified Bond systems.
ELECTROPLATED BOND
An electroplated bond is a metallic bond (typically nickel for superabrasive grinding wheels) in which a single layer of abrasive is adhered or bonded onto a metallic core through a deposition process. Like all electroplating processes, metallic material is pulled from solution and deposited onto the substrate, encapsulating the abrasive onto the substrate in the same form as the substrate.
Like the other bond types, both diamond and CBN superabrasives are used depending on the application. Because electroplating is a liquid process, complex shapes and geometries are more readily achieved and generally don’t require dressing when in use.
Another benefit to using electroplated grinding wheels (also referred to as just ‘plated grinding wheels’) is that they are single layer and used wheels are able to “stripped” or reverse plating process and the substrate/core can be reconditioned and used again resulting in potential savings of as much as 40% over new plated products.
To recap, Plated grinding wheels:
Generally don’t require dressing
Can be designed in complex shapes and geometries
Can be reconditioned and used again for cost savings over the life of the wheel
HYBRID BOND
A hybrid bond is a combination of two or more different types of bonds and/or processing methods to create a “Hybrid” that encompasses enhanced properties to achieve better performance in grinding for a specific application.
For example, resin and metal bonds have successfully been combined into a single wheel in our EVO Hybrid Bond grinding wheels designed for the cutting tool industry. In this hybrid resin/metal bond wheel, the hard metal bond is softened to make it more user friendly while maintaining long life.
New hybrid bonds and technologies continue to be developed to bring enhanced grinding performance to specific production grinding processes.
NEXT STEPS
To dig deeper into why different types of materials require different grinding solutions, check out our previous blog Why Different Materials Need Different Grinding Wheels.
Grinding is a complex process that requires a total “systems” approach. Your grinding solution needs to encompass; the grinder/machine, dressing/truing requirements, material, coolant, and the grinding wheel.
If you’re ready to move forward with a quote or investigate the advantages of a certain bond type for your specific application, contact us to speak with our team of expert engineers that will help answer your questions and get you started.
7 Reasons Why Vitrified CBN Grinding Wheels Surpass Conventional Grinding Wheels
Discover 7 reasons why CBN grinding wheels are your next game changer >
A vitrified CBN grinding wheel is a superabrasive grinding wheel made from a Cubic Boron Nitride abrasive in a porous – or “vitrified” (ceramic) – bond.
Vitrified CBN Grinding wheels are the most cost effective solution for production grinding of ferrous metals and aerospace alloys, and offer far superior performance when compared with conventional abrasive grinding wheels.
Especially for those in industries such as:
Aerospace
Automotive
Bearing
Medical
Gears
Mold & Die
Round Tools (drills, reamers, taps, etc)
Cutting Tools
So why exactly is that?
There are 7 critical reasons why making an upgrade to a CBN grinding wheel can make a huge difference in your industry.
1. 100 - 300x The LifeSpan
CBN abrasive is the second hardest material known to man and is 2 ½ times harder than Aluminum Oxide. Because of its high hardness, the CBN crystals offer 100-300 times the lifespan when compared with traditional grinding wheels.
While Vitrified CBN grinding wheels may cost up to 10 times that of a conventional wheel, the extended wheel life far exceeds the initial wheel cost, making it more cost effective. You get what you pay for – and this is definitely one of those products where you’ll quickly see the difference in its longer lasting abilities as compared to your old grinding wheels.
(We’d even argue that once you’ve used a CBN grinding wheel, it’s hard to go back – it’s just that big of a difference).
2. Reduced Thermal Damage
Because CBN abrasive has almost 50 times the thermal conductivity of conventional abrasives, it transfers the heat generated from the grinding process away from the workpiece, rather than being absorbed by the workpiece.
Combining the high thermal conductivity of CBN with the porous vitrified wheel structures, most heat is efficiently removed through the wheel and coolant, preventing heat damage to your workpiece.
With efficient removal of heat, your workpiece won’t be subject to thermal degradation or changes to the material properties – which is very important for improved wear and life of each component.
3. Optimize Your Grinding Process
With high life and improved thermal properties, Vitrified CBN can be pushed harder during grinding, and decreased grinding cycle times are able to be achieved.
As a result, the grinding process can be more readily automated. This creates less need for more grinding machines, floor space, wheel changes, waste generation, and operators – which has many advantages when it comes to your time, cost, and safety measures.
4. Customizable
Vitrified CBN grinding wheels are engineered per specific customer applications so you can achieve optimal performance.
Considerations that can be taken into account include: material being ground, grinding machine, coolant type and delivery, dressing method, stock removal, quantity of parts, etc… And aggressive, free-cutting bonds can also adapt to various spindle speeds. Which is not only convenient, but also cost effective.
5. Lights Out Operation
Vitrified CBN grinding wheels have “dressable” structures – which lend them to “lights out operation.” The grinding layer can be refreshed using a rotary, and in some cases, stationary dresser.
You’ll be able to automate every step of the manufacturing process, making Vitrified CBN grinding wheels an excellent choice for production based applications.
6. Re-Truing of Formed Profiles
Another benefit of having a “dressable” structure is that complex forms and geometries are able to be generated in Vitrified CBN grinding wheels. The profiles are able to automatically regenerate in line on the properly equipped grinder and maintain tight tolerances.
7. environmentally friendly
The use of Vitrified CBN wheels (as opposed to conventional abrasive wheels) results in significant reductions in waste generation. It decreases the amount of grinding debris (swarf) >99%.
It even allows for more recycling of the metal swarf that is generated because it is oftentimes free of grinding wheel breakdown. Many customers are able to get credit for the Environmental and waste reduction initiatives under ISO14000 and other programs.
Experience the cost effective solution for production grinding with Vitrified CBN Grinding Wheels. Contact us for your free quote.
Why Different Materials Need Different Grinding Wheels
With all of the grinding wheel options available, figuring out which one is going to be the most efficient and cost effective for your working material can feel overwhelming, but CDT is here to help.
With all of the grinding wheel options available, figuring out which one is going to be the most efficient and cost effective for your working material can feel overwhelming, to say the least.
This article will help cover the basics as to why different materials will need different grinding wheels - and how to select the appropriate abrasive type for your grinding wheel.
So why exactly do different materials require different types of grinding wheels?
It comes down to the material properties (i.e. material hardness and chemistry) and the proposed grinding process: factors like machine, coolant, dressing, stock removal, etc.
First, consider which type of abrasive will be best for your material: conventional or superabrasive?
Conventional Abrasives
Aluminum Oxide
Silicon Carbide
Aluminum oxide has a hardness of 1800 HrV and is commonly used in grinding of ferrous or other materials that are known to chemically react with carbon.
Silicon carbide has a hardness of 2800 HrV and is used on "hard" materials such as glass, ceramics and non-ferrous metals such as aluminum and copper.
Superabrasives:
Diamond
Cubic Boron Nitride (CBN)
Superabrasives are both harder (longer lasting) and have much higher thermal conductivity (remove heat of grinding more efficiently) compared to conventional abrasives.
Diamond is the hardest known substance with a hardness of 9000 HrV and is the most effective abrasive in grinding of materials that don't react with carbon such as glass, ceramics, and non-ferrous metals. It can increase wheel life by several orders of magnitude when compared with conventional wheels. Advancements in production of synthetic or man-made diamonds have brought their cost down and led to expanded use. We commonly see diamonds used for grinding tough materials such as very hard steels, cemented carbide, and aluminum oxide cutting tools.
CBN is the second hardest known material at 4500 HrV and is ideal for grinding ferrous metals and other materials that are known to react with carbon. It is commonly utilized in the grinding of high-speed steel, hardened cast iron, tool and die steel, and stainless steels. When appropriately specified and optimized, CBN can outlast conventional Aluminum Oxide wheels by a factor of up to 300:1.
NOTE: With so many benefits, you may be wondering “What type of materials cannot be ground on a grinding wheel?” Superabrasives (Diamond & CBN) are focused on hard materials. We turn to CBN for hardened ferrous alloys, stainless steel, and nickel alloys. Diamond is ideal for even harder materials such as glass, carbides, and ceramics. The harder the material, the better it is for grinding with superabrasives, which is what we customize for our clients at Continental Diamond Tool.
You often cannot justify the cost of a superabrasive grinding wheel for soft nonferrous metals (<30 HrC) like aluminum, brass, and copper. Materials with such soft properties tend to “clog'' and coat the wheel and would require continuous dressing.
Some have asked, “Can you use a superabrasive grinding wheel on wood?" Wood is a very soft, inexpensive substance and would not be well suited for superabrasive grinding. For similar reasons, we do not recommend superabrasive grinding wheels for other soft nonmetallic materials like fabric, leather, certain plastics and rubber, etc.
Now that you know the differences between Conventional and Superabrasive grinding wheels, you can see how each caters better to different materials and uses. Once you’ve narrowed down the proper abrasive type, a grinding wheel expert can help you narrow your selection further with a selection of different bond types, such as Resin Bond, Metal Bond, Vitrified Bond, and Electroplated.
The bond is what holds the wheel’s abrasive grains together. The strength of bonding of a grinding wheel is often referred to as its hardness. Generally speaking, grinding wheels with a higher grade or hardness are recommended for softer materials and vice versa. It is also now possible to combine bonds to form custom hybrid variations that have unique properties.
NOTE: You may be thinking “Why do we use hard wheels for soft materials in grinding?” This is a complicated subject with the actual grinding mechanism (chip formation) being different between ductile or soft metals and hard materials like ceramics. Grinding wheels for metals act like micro-cutting tools where metal chips are cut or torn away. The chip size and shape is dependent on the material properties.
With harder materials such as carbides and ceramics, there are brittle fractures where small chips are actually fractured away in the grinding process. The material itself is very abrasive. Because the chips in carbide and ceramics are so abrasive, softer wheels are often more efficient at removing the small abrasive chips (a.k.a. swarf).
When shopping for a grinding wheel manufacturer, it’s helpful to have some basic parameters handy to get the most accurate quote and best product for your application. For a whole list of considerations to bring with you for selecting the best grinding wheel, check out our article on How To Order Custom Grinding Wheels.
Then contact us to collaborate with our engineers, product managers, and technical sales people to go over all of these considerations with you. If you’d like, we can even come to your facility to review your process first hand and make recommendations.
When you have the optimal grinding wheel for your material, you will see the difference in speed, durability, and performance.