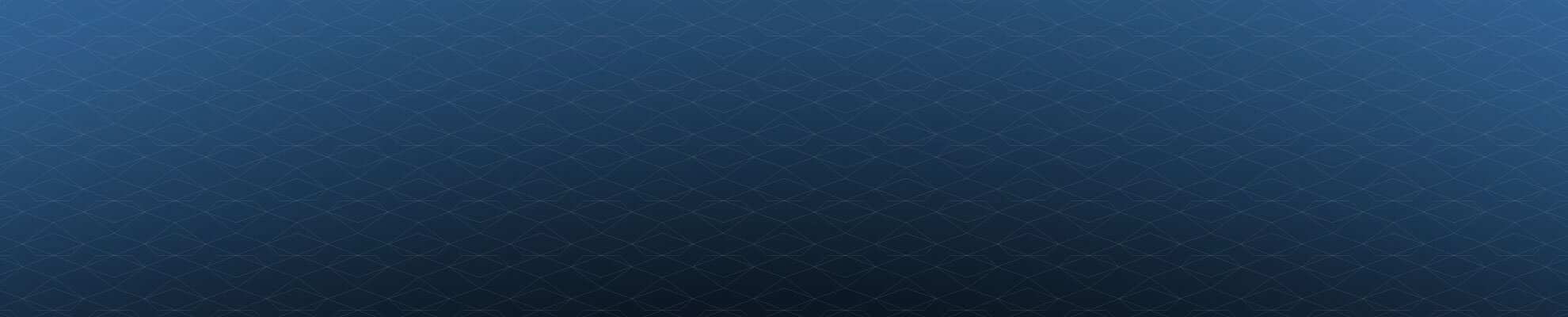
News and Resources
Browse by Category
Browse by Product
- All Dressing Products
- All Grinding Products
- CBN-Diamond Superabrasives
- Conventional Abrasives
- Diamond Lapping Compounds
- Diamond Rotary Dressers
- Diamond Stationary Dressers
- Hybrid Bond Grinding Tools
- Metal Bond Grinding Tools
- Plated Grinding Tools
- Resin Bond Grinding Tools
- Vitrified Bond Grinding Tools
Does CDT Carry Stock?
A lot of customers ask if we keep stock inventory on the shelf. Check out the answer in this article >
A lot of customers ask if we keep stock inventory on the shelf.
Because our customers’ needs are diverse, there are not a lot of common tools used across industries. Therefore, it is really most beneficial to us - and our customers - to only build custom. This gives us the flexibility to deliver exactly what the customer is looking for in a timely manner.
Customers are often surprised at how quickly and affordably we can deliver custom grinding wheels. We manage our inventory, control our overhead, and keep our costs low, so we can pass those savings on to our customers.
Watch this video to learn more.
To get started with custom superabrasive grinding wheels from CDT, contact us for a free quote.
How much does a Custom Superabrasive Grinding Wheel Cost?
We look at the 'total cost' of a custom superabrasive grinding wheel from CDT, and detail the advantages superabrasives have over conventional grinding products. Check it out >
A Look at the Bigger Picture >
As a custom-made product, the cost of a superabrasive grinding wheel can vary greatly from one design and application to the next. People may shy away from custom products because they think one of two things: it’s going to cost a lot more or it’s going to take a long time to complete. While that may be partially true on the surface, that’s not the whole picture.
In this article, we’re going to take a look at some of the factors that will help you assess the “total cost” of custom grinding products, which includes both what the product is and the value it provides over time. When taking everything into account, our clients often find that the custom grinding product that appeared to be too expensive actually has a return on investment that quickly pays for itself.
Here are 4 advantages to purchasing custom superabrasive grinding wheels from Continental Diamond Tool so you can weigh their value long-term:
1) Custom Grinding Wheel means a better fit.
With the right custom grinding wheel, customers have reported upwards of a 70% improvement in efficiency from conventional wheels. Our engineers work with you to reduce cycle times, maximize removal rates, minimize maintenance requirements, decrease material damage, and improve productivity wherever possible.
During the design phase, we can run simulations from our facility or travel to yours. We frequently visit customers to learn their machinery, materials, and processes so we can design a better grinding wheel that works for what they need. Some of our product options can be incorporated into lights out production which can be an even great boost to your company’s overall efficiency.
With each tool custom designed for your unique application, you get productivity out of your grinding wheel that you’ve likely never seen before. When you factor in these benefits, ROI skyrockets.
2) Custom Grinding Wheel means quality work.
Conventional wheels off the assembly line will never match the quality of custom grinding wheels from an experienced manufacturer. Custom grinding wheel manufacturers generally do not cut corners like you see with commodity products. At CDT, we use the best quality materials because it’s in our best interest to maintain longterm relationships with customers and the superiority of our products.
Experience can also be a factor with quality. Even within the industry of custom superabrasives, inexperienced engineers can cost you in development time, troubleshooting hassles, and subpar products. At CDT, we have almost 50 years of experience in old and new grinding technologies. And we’re always updating our quality control systems with state-of-the-art precision testing equipment to make sure you are getting the most efficiency from your custom grinding wheel investment.
3) Custom Grinding Wheel means the product will last.
Superabrasive grinding wheels are made from natural diamond, manmade diamond, and CBN —some of the strongest materials known to man. Conventional abrasives are made from materials like aluminum oxide and silicon carbide — much softer materials that break down more quickly. Depending on your application, a more durable product that you don’t have to replace as often may actually be a better investment.
Additionally, we have options with some of our superabrasive products where we can recommend dressing tools and even refinishing or replating services that can make your grinding wheels last even longer.
4) Custom Grinding Wheel means a great customer experience.
You may be wondering how great service actually saves you money. First, the customer service team at Continental Diamond Tool provides free quotes, product selection and design assistance. You don’t have to research and guess what you need. A specialist will provide product recommendations and a competitive quote for you for free.
Second, a company like CDT whom you have a personal relationship with will do everything they can to help. For example, we know that waiting on a grinding wheel order can be painful for your company’s productivity and bottom line. Delays may throw off your production calendar and anger customers. That is why we’ve taken measures — like stocking an extensive inventory of raw materials — so we can deliver your order faster than others in the industry. Additionally, once your product has been developed, a reorder can be produced and shipped much faster.
Third, service doesn’t stop at the sale. While some big name custom superabrasive and conventional wheel manufacturers have cut corners in service for better bottom lines, CDT has remained true to our founding principles. Does your grinding wheel supplier train your team on installation and maintenance? Will they come to your facility to review your machinery and processes to make sure your grinding wheel is optimized for peak performance? Do they notify you when new technology becomes available that could make your processes even more efficient? At CDT, our personal sales team and tech support are here to help you overcome the obstacles to increased productivity and success.
Learn more about superabrasives and how they differ from conventional grinding wheels in this video:
To get started with custom superabrasive grinding wheels from CDT, contact us for a free quote.
How CNC Automation at Continental Diamond Tool Benefits Customers and Employee
With CDT’s recent investment in CNC automation through robotics, they are seeing benefits to quality, speed, and employee satisfaction. Check out what this new technology means for CDT customers and employees >
Continental Diamond Tool has been in business since 1973, and in that time we’ve grown to rank among the world’s top manufacturers of Diamond and CBN wheels for drilling, cutting, and grinding applications. One key component of our growth has been our investment in innovation, both with our products and our processes. With our recent investment in CNC automation through robotics, we're seeing benefits to quality, speed, and employee satisfaction. Let’s look at what this new technology means for our customers and employees.
Quality Matters
Quality has been an area where Continental Diamond Tool has invested heavily in systems and automations that allow us to test and assure the accuracy of every product that leaves our facility. Robots take this a step further, producing consistent products with minimal, if any, defects. Robots are perfect for doing repetitive jobs with precision and efficiency.
In addition, automatic “error-proofing” is built into our robotic systems. Advanced software in robotics identifies when there is an issue in production and notifies our production team before it causes costly delays.
Reducing Lead Times
Before introducing robotic automation, at Continental Diamond Tool we struggled to reduce lead times on our custom products. Because each machine required highly skilled technicians to operate it, demand could easily exceed our available workforce during periods of peak production. Despite making every effort to expedite orders with on-hand raw materials and first-come-first-served policies, sometimes shipments wouldn’t reach customers until months after initial requests.
Now that all robotic machines can be remotely monitored, operators can observe production from start to finish on multiple machines. Lights-out production means even more efficient use of our facilities and quicker turnaround on orders. Now we've reduced lead times to mere weeks from design to delivery. Even with last minute orders, our robots extend our ability to put in overtime and keep up with unpredictable demand.
“With this tight labor market being what it is, CDT is always striving to become more efficient with what we have," says Jeff Gongaware, CDT Customer Service & Assistant Sales Manager. "It is not uncommon for me to walk through the shop at the end of the day and see the Robotic Arm machining blanks when all of the machinists are gone for the day. It is difficult to be to be more efficient than that.”
Better Service & Innovation
Our team at Continental Diamond Tool is always looking for ways to improve the customer experience. We strive to ensure that our customers receive nothing but quality products. When we implemented robotics into our machine shop, repetitive and maintenance tasks were delegated to robots. The resulting increases in efficiency and revenue has freed up both our human and capital resources for further investment in value-added services like research and development.
"Not only has robotic automation freed our team to make better use of their talents in the areas of service and creative innovation, but none of the robots have contracted COVID yet!" jokes Nick Viggiano, CDT President.
By integrating CNC automation into all phases of production, we have found we have been able to innovate more quickly while also ensuring the high quality of our parts. As a result, CDT is able to better serve our customers.
Better Job Satisfaction
An ongoing myth in manufacturing is that robots are replacing humans on the shop floor. While it’s true that robots are making many of our processes more efficient, CDT has found that automation actually makes life better for our workers. With mundane tasks being performed by robots, our employees can focus their energy elsewhere on bettering production efforts in more impactful ways.
According to CNC machinist Ron Fuller, “It has definitely improved efficiency and productivity in numbers, while also allowing me more time to focus on other projects at the same time. Prior to using the robotic arm, I was producing about 50-60 parts per day and now the arm allows me to produce 80 parts per day."
Repetitive, strenuous tasks tend to pose health and safety issues for CNC machinists and operators. By delegating these tasks to robots, there is less risk for workplace injury. And without this highly physical, repetitive work, we now find we have a wider pool of candidates who are willing and able to perform production work.
“In manufacturing in general, the pool of qualified or interested candidates is currently a bit shallow," says Kathy Fell, Human Resources Manager. "However, CDT is able to take what seems difficult and turn it into an opportunity with the idea of modifying job roles.”
For example, CDT has begun hiring recent retirees who want to reenter the workforce. They may no longer want to do heavy machining work, but with robots they can use their expertise in new ways, while working part-time schedules as productive as their full-time positions used to be.
Today CNC operators at CDT are focused on more enjoyable tasks such as programming and preparing multiple machines, designing new products, improving production strategies, and general monitoring of the production line. Robots are making the jobs of our CNC operators more rewarding, as they can produce more with less effort.
Working Smarter
To be successful in business, we have to be good stewards of our resources. By investing in CNC automation, Continental Diamond Tool is able to produce higher-quality products faster and with less waste. This equates to happier customers, greater employee satisfaction, and a stronger financial standing for us as a business. By working smarter through automation, we are all seeing the benefits.
Find New Purpose with a Part-time Job in Manufacturing — Seniors Welcome!
Though most of our employees work full-time, we have a great group of part-timers who have come out of retirement to join our team. Learn how a part-time job at CDT could benefit you >
The top thing people report missing about work after they retire is interacting with co-workers, friends, and others. Whatever stage of life you’re in, it can be difficult to find ways to make yourself feel productive and included in your community if you’re not working full-time. Working part-time has been shown to boost mental health, improve self-esteem, and provide opportunities for growth. That’s why it’s so important to know that part-time manufacturing jobs are available — seniors included!
What Part-Time Jobs in Manufacturing Are Available?
Manufacturing jobs are often classified as full-time or part-time. While part-time manufacturing jobs do exist, they’re rare. That’s because we, like many manufacturers, have crucial production periods that need to be consistently staffed and require special training. Yet at Continental Diamond Tool, we've identified several job functions that make for excellent part-time work. These part-time jobs do not require higher education or physically-demanding skills, but are still important in getting the job done.
Am I Qualified?
No matter what part-time job you’re looking for, it can be difficult to know if you have enough experience. If you’re over 50 or have been out of the workforce for awhile, you may worry that your age or work gap will count against you when applying for part-time positions in manufacturing. The fact is we like to hire employees who are over 50 to benefit from their experience and skills.
Benefits to Part-time Employment
Though most of our employees work full-time, we also have a great group of part-timers who have come out of retirement to join our team. A part-time job is a great way to maintain an active life outside of work while still being productive. Enjoy purposeful work with a team moving toward a common goal. Benefits like job flexibility, gaining experience, and staying on top of new technology can all make part-time employment attractive for those looking to supplement their income or come out of retirement. The free golf membership is also a great perk!
Benefits for part-time positions at Continental Diamond Tool include:
Paid Break
Climate Control
Golf Membership
Fitness Center
Check out this video from one of our part-time employees about coming out of retirement to join CDT:
Who Should Apply?
Seniors or anyone interested in part-time jobs with a prior history in manufacturing should consider applying. This is a great way to scale back on work while staying connected to your career as well as share the experience you've gained over the years.
At CDT, you don't have to worry about feeling out of place. We have purposefully hired a workforce diverse in age and experience. In fact, having former retirees on staff provides an opportunity for our younger workers to learn from those more experienced in production work. That's just one example of how we reward ambition at CDT — it doesn't matter if you're young or old, we want every employee to feel valued and respected here at CDT .
How to Get Started with Part-time Employment
The first step is to gather your work history and apply. You can complete our online application, email your resumé to jobs@cdtusa.net, or drop it off at our main office at 10511 Rose Avenue in New Haven, Indiana. Please note on your application or resumé that you are interested in a part-time position.
When we call you for an interview, be ready to tell us why you’re looking for a manufacturing position and discuss any relevant experience you have. Before we meet, have an idea of what your ideal job would look like: How much do you want to work? Is there a certain type of job that interests you? What experience or limitations do you have? We will talk about the part-time positions available and contact you if we think you’d be a good fit!
Pushing the Bounds in Grinding Technology
If a customer needs it, CDT makes it happen. Check out just how we accomplish this with our custom superabrasive products in our latest blog article >
In today’s competitive advanced manufacturing space, industry leaders know that staying a step ahead means continuously pushing the bounds of what’s possible. Materials are harder, tolerances are tighter, and cycle times are shorter than ever before. In this environment, precision is essential. Well designed custom tooling can provide the edge you need to make your processes that much better.
When Ray Viggiano set up shop in 1973, his philosophy was simple:
If a customer needs it,
CDT makes it happen.
Over the years, a lot has changed, but this philosophy has stayed the same. In this video, you can see Continental Diamond Tool's state-of-the-art facility. Learn how we've grown into a leading manufacturer of superabrasive grinding wheels and diamond dressers that set new standards in the industry. Watch how we have assembled the technology, materials, and expertise to tackle the toughest jobs out there with precision and excellence. And hear about our can-do culture that has been the foundation for our company's success.
At CDT, we are committed to producing grinding wheels with the highest quality, performance, and accuracy. If you need it, CDT will make it happen. To get started, call us or request a quote.
Thank You to Our Customers
We wanted to take a moment to let you know that we truly appreciate working with you, and we’re so grateful for the trust you place in us. We wish you a happy Thanksgiving and the very best throughout this holiday season.
We wanted to take a moment to let you know that we truly appreciate working with you, and we’re so grateful for the trust you place in us. We wish you a happy Thanksgiving and the very best throughout this holiday season.
If there are any last minute tools you need for 2021, or if you'd like a quote for 2022 budgeting, please don't hesitate to reach out.
We will be closed on Thursday, November 25th and Friday, November 26th to observe the Thanksgiving holiday.
Komets Fans Recruited by CDT
If you are a Komets fan looking for a career change at a team-oriented workplace with great benefits, apply now at www.CDTUSA.net/jobs. Go Komets!
With demand in superabrasive grinding wheels surging, Continental Diamond Tool is looking to grow its workforce of highly motivated, enthusiastic employees. In a stroke of inspiration, CDT management is tapping a pool of unexpected candidates with great potential — Komets hockey fans.
“When I asked my team what we’re looking for in a new hire, they told me we need go-getters, team players, who will enjoy our benefits and push the team forward,” says Nick Viggiano, CDT President. “It was obvious to me that Komets fans are the ideal pool of candidates.”
Sports lovers, and especially Komets fans, love working at CDT — the company offers employees free access to its fitness center, free golf memberships, and free access to a suite at the Coliseum for employees to share throughout the Komets season.
“At CDT, we’re in it to out hustle, out work, out-think, outplay, and outlast. Wheel, Snipe, Celly. If you get that, come on in and apply,” says HR manager Kathy Fell.
Earlier this month, the ultimate Komets fan and mascot, Icy D. Eagle, came to CDT to complete his application. His enthusiasm was not lost on CDT Quality Manager Karl Zimmerman. “When he checked me into the glass, I knew he had drive,” says Karl.
Here is a short clip from Icy’s tour of the CDT facility:
Keep an eye out for more clips of Icy’s antics at CDT on YouTube, Facebook, and at hockey games throughout the Komets season. Upcoming home dates include:
FRI, NOV 05
SAT, NOV 13
FRI, NOV 19
SAT, NOV 20
SUN, NOV 21
THU, NOV 25
FRI, DEC 3
SAT, DEC 4
FRI, DEC 17
SAT, DEC 18
SUN, DEC 19
SUN, DEC 26
MON, DEC 27
FRI, DEC 31
WED, JAN 5
SAT, JAN 8
FRI, JAN 14
SUN, JAN 16
SAT, JAN 22
WED, FEB 9
FRI, FEB 11
WED, FEB 16
FRI, FEB 18
SAT, FEB 19
SUN, FEB 20
WED, MAR 2
SAT, MAR 5
SUN MAR 13
SAT, MAR 26
SUN, MAR 27
WED, MAR 30
SAT, APR 2
WED, APR 6
FRI, APR 8
SAT, APR 16
You miss 100% of the shots you never take.
If you are a Komets fan looking for a career change at a team-oriented workplace with great benefits, apply now at www.CDTUSA.net/jobs. Go Komets!
Plated CBN for Aerospace
The mechanics of producing aircraft to safely transport people in such harsh conditions, however, is particularly challenging. The solution? Plated CBN grinding wheels.
Commercial airline travel may have taken a dramatic hit during the pandemic, but a rebound for the aerospace industry has already begun. 2021 marked the first all-civilian flight into space, and the possibilities this presents are especially exciting.
The mechanics of producing aircraft to safely transport people in such harsh conditions, however, is particularly challenging. Modern jet engines depend on superalloys to handle combustion temperatures of 1400ºC or more. These high-performance nickel-based materials have very high temperature stability, which makes machining components like turbine vanes extremely challenging. The solution is to use plated CBN wheels. Here’s why.
AEROSPACE DEMANDS
The aerospace industry asks a lot from their high-precision grinding tools. Specifically, aerospace grinding wheels must:
Remain hard at high temperatures
Be chemically inert to resist chemical reactions between grinding wheel and the nickel alloys
Provide excellent size control throughout a production run
Be available in complex forms
Not damage the workpiece – no burning or microcracking
Minimize residual stresses in the finished workpiece
Missing from this list is wheel life. While grinding wheel durability is important for Nickel based alloy grinding, it is less of a consideration for aerospace applications since their production runs are generally shorter than other industries like automotive. In this respect, plated grinding wheels provide a perfect middle ground.
Plated wheels are longer lasting than conventional abrasives, and they are capable of being refurbished through replating to extend their use. On the flip side, a plated wheel does not require the downtime for wheel dressing that a longer lasting Vitrified CBN wheel needs to maintain optimal performance. This makes plated wheels particularly well suited for applications with smaller lot sizes that don’t need an especially long life.
All of these considerations make plated CBN wheels an excellent option for aerospace applications.
ADVANTAGES OF CBN GRINDING TECHNOLOGY
As the hardest known substance, diamond might seem the obvious choice for grinding exceptionally hard materials. However, it doesn't perform so well at temperatures over 700ºC as it tends to react chemically with the material and deteriorates due to oxidation at higher temperatures. It's also vulnerable to attack by some of the chemicals found in grinding coolants, which reduces wheel life.
The alternative to diamond is Cubic Boron Nitride (CBN). This is a man-made or synthetic abrasive material that's not as hard as diamond but is harder than anything else. Unlike diamond, it retains its hardness at elevated temperatures. CBN offers superior resistance to chemical attack when grinding ferrous metal alloys. It exhibits no affinity to iron and doesn’t alter the material properties like Diamond does.
WHY PLATED WHEELS?
An electroplated grinding wheel has a single layer of superabrasive tightly bonded by a metallic layer to a solid metallic core. This has several advantages:
The bond material is below the tops of the grains, creating a free-cutting wheel that removes material rapidly with low power consumption, and helps keep interface temperatures down.
Good thermal conductivity helps take heat away from the grinding zone.
Wheel forms are readily achievable by machining needed geometries onto the metallic cores.
Worn wheels can be stripped and re-plated, making them an economical choice.
Costly dressing systems and rotary dressers aren’t needed, thus simplifying and lower capital expenditure on equipment.
THE AEROSPACE PROBLEM-SOLVER
Plated CBN grinding wheels are used extensively in aerospace. They perform well on exceptionally hard superalloys, providing high material removal rates coupled with excellent dimensional control throughout a production run.
The engineers at Continental Diamond Tool Corporation have extensive experience developing tools that can hold up to the rigorous demands of aerospace production. Contact us for a free grinding wheel analysis and quote.
Plated Diamond Rotary Dresser Operations Expanding for Increasing Demand
Always striving to stay ahead of the curve in technology, Consort Precision Diamond is excited to announce that thier newly upgraded plating lab is up and running.
Diamond Rotary Dressers are widely recognized as the most efficient, cost effective means of dressing and truing grinding wheels to the correct tolerance, form, and condition. As industry is experiencing an increasing demand for high-accuracy, high-speed production, the need for reverse plated dressers is also increasing.
Always striving to stay ahead of the curve in technology, CDT-subsidiary Consort Precision Diamond is excited to announce that our newly upgraded plating lab is up and running.
"This plating lab expansion more than doubles our capacity to produce the high quality tight tolerance reverse plated rotary dressers used by some of the most prestigious companies in the world," says Troy Giacherio, Product Manager at Consort Precision Diamond. Stephen Noakes, Production Manager, lead the team who worked on the plating lab upgrade.
Choosing the Best Diamond Rotary Dresser
There are two types of production methods for diamond rotary dressers, sintering and plating. Consort Precision Diamond specializes in the manufacture of both types.
Sintered diamond rotary dressers are suitable for large quantities of high precision machining and many types of high hardness grinding wheels.
Reverse plated diamond rotary dressers are best suited for applications where high accuracy of profile detail and a correspondingly high quality surface finish on the component are required.
Our Commitment to Excellence
If your application calls for a Diamond Rotary Dresser, Consort Precision Diamond is committed to providing you the best tool for the job. Our service techs are skilled at helping you find the correct specifications optimized for your application. Contact us today >
Consort Precision Diamond is a subsidiary of custom superabrasive grinding wheel manufacturer Continental Diamond Tool Corporation. Learn more about Consort’s products at www.consortprecision.co.uk.
Who Uses Vitrified Grinding Wheels and Why?
At CDT, our Vitrified products generally serve two distinctly different markets, Vitrified CBN and Vitrified Diamond. Learn about what makes a Vitrified wheel and the capabilities Vitrified has.
At CDT, our Vitrified products generally serve two distinctly different markets, Vitrified CBN and Vitrified Diamond. As the two hardest known materials, CBN and Diamond are referred to as superabrasives and both are excellent thermal conductors.
These abrasive properties when combined with our porous vitrified structures allow for:
longer wheel life
shorter grinding cycle times
automated grinding production capabilities with wheels dressed right on the grinder
CBN vs. Diamond
Vitrified CBN products are ideal for steel and ferrous alloy grinding applications in automotive, aerospace, medical, production tooling, etc. They are excellent thermal conductors and do not react with ferrous materials during the grinding process like diamond does.
We regularly customize Vitrified Diamond products for grinding ceramic and carbide materials used in industries such as glass, ceramics, computer chip manufacturing, thermal spray coatings, and more. Diamond is the hardest known material with the best thermal conductivity making it the best abrasive where there is no chemical reaction.
We are uniquely qualified in both types of Vitrified products because of our full range of manufacturing capabilities and technical application support. Because we handle the vitrification process entirely onsite, we have full control of the manufacturing process and a standard lead time of about 3-4 weeks — about half as long as the industry standard.
The Vitrification Process
At CDT, we use a cold press and sintered process to press near net shape with highly and tightly controlled sintering. This fuses the Vitrified/Ceramic bond together with the Diamond or CBN into a porous structure. CDT's vitrification process is unique in how our engineers have developed a series of custom bonds, formulations, and structures to offer our customers superior grinding performance when compared with off-the-shelf or other competing products.
Combining either of these two abrasives with a porous vitrified bond offers a very strong and stiff system in which the porosity brings coolant into the grinding zone. This innovation removes heat and grinding debris (or "swarf") to extend the wheel life and improve performance. CDT's Vitrified Diamond and CBN wheels generally provide 100 to 300 times the grinding wheel life and maximize the amount of material being ground compared with conventional grinding wheels.
Reducing Cycle Times
"Cycle Time" is the term used to describe the grinding process. Our porous vitrified grinding wheels offer greater efficiency through more effective coolant delivery and swarf removal. This also extends the life of the grinding wheel requiring less downtime for wheel dressing.
When compared with conventional wheels, we see an 80-90% cycle time reduction with our custom vitrified wheels. Even compared with other superabrasives such as Resin and Metal Bond Diamond and CBN wheels, we see 40-75% reductions in cycle times with vitrified wheels.
From military/defense and energy sectors to mold & die markets and everything in between, we have found unique opportunities for more efficient grinding using custom Vitrified products in many industries. Our engineers would be happy to discuss the parameters for your process and provide a free analysis and quote for a custom grinding solution that works best for your application. Contact us today >
How Has CDT Handled the 2020 Pandemic and Its Aftermath?
At CDT, we're always looking ahead. In this video, President Nick Viggiano explains how CDT has continued to provide products reliably for customers despite all the challenges of 2020.
2020 was a set back for economies across the world, but by making wise use of this time, CDT is poised to spearhead the recovery for themselves and their customers in 2021 and beyond.
“At CDT, we are always trying to look ahead and prepare for what’s around the corner,” says Nick Viggiano, President of CDT. “In 2020, during the pandemic, we had time to develop a state-of-the-art grinding lab, make improvements to our quality protocols, and upgrade our ERP systems.”
“We felt that production would go through the roof once we got past the pandemic, so we spent more on capital equipment in 2020 than any other year prior. With the explosion in growth we’ve experienced this year, we will surpass that with all the new technology we are bringing into our manufacturing facility.”
During the first half of 2021, CDT experienced major supply chain issues like much of the manufacturing sector. The purchasing team worked closely with vendors to anticipate supply bottlenecks. At the first hint of trouble, CDT ordered six month supplies and quarantined it as safety stock for key materials such as Diamond, CBN, steel, aluminum, and powders.
“We never wanted to tell a customer we couldn’t make something because we didn’t have the materials,” says Nick. “This approach opened new doors for us this year when other less-proactive manufacturers had to let their customers down. They found us, and we were more-than-willing to help!”
The labor shortage has been another source of worry for businesses. To be up 50% this year in manufacturing custom tooling has been a tough challenge for the CDT team.
“We’ve always had a family culture at our workplace that appreciates and rewards our employees’ contributions, but this year we’ve explored more unique ways to attract talent in our area,” says Nick. “We launched a video social media campaign to highlight the fun culture and unique benefits we offer such as golf memberships and fitness center. These efforts have paid off with lots of great new people joining our team while continuing to get 75-100 new applications a month.”
“CDT is growing, and I’m very proud of what this company is achieving and where we are headed!”
CDT Starting A New Third Shift
Continental Diamond Tool has experienced extensive growth in Three of their most popular product lines, and they are now adding a third shift to their schedule to increase production and continue to fulfill global orders in a competitive timeframe. Apply today >
Continental Diamond Tool Starting A New Third Shift, Now Hiring
Continental Diamond Tool has experienced extensive growth in three of their most popular product lines, and they are now adding a third shift to their schedule to increase production and continue to fulfill global orders in a competitive timeframe.
The new shift will consist of four 10-hour shifts per week, from 8 p.m. to 6 a.m. This third shift will begin as soon as the open positions are filled, which may be as soon as August. All positions are entry-level and require a high school diploma. Job training will be provided.
CDT fosters an innovative, team-oriented environment for their employees, who enjoy paid lunch breaks, competitive wages, and health insurance benefits, along with additional benefits and overtime opportunities, in a clean, climate-controlled environment.
In business since 1973, CDT is a leading producer in the global market for superabrasive grinding wheels and custom tooling. Their 128,000 sq. ft. manufacturing facility in New Haven, Indiana, utilizes the latest technology to serve numerous industries including medical, aerospace, power generation, and more.
Additional information and applications are available by calling 800-443-6629 or visiting CDTUSA.net/careers.
Not Your Standard Plating!
Continental Diamond Tool now offers a new generation plated product available on carbide, aluminum, copper, or steel substrate bodies.
Now available in Carbide, Aluminum, Copper, and Brass
Plating has traditionally been a single layer of abrasive with either CBN or diamond attached to a steel body. CDT now has a new generation of plated products available on carbide, aluminum, copper, or steel substrate bodies.
Carbide is a great option for mandrels and similar processes where extra rigidity is needed. Carbide provides superior hardness, unsurpassed corrosion resistance, and the ability to retain its strength at extreme temperatures.
Aluminum is light weight and easier to handle than steel, making it better for processes that require labor intensive lifting. There is less strain on your operator when working with this tool. The reduced weight also exerts less stress and wear on your machine, prolonging the life of spindles and spindle bearings. This material is also resistant to rust and corrosion and has a high strength-to-weight ratio.
Copper also offers great corrosion resistance, and it is also malleable. Its inherent flexibility allows it to maintain adhesion even if a substrate is bent and manipulated post plate. This feature makes it ideal for processes that need extra pliability.
Brass is a solution we also turn to for its malleability. It is also a good choice for dressers, because it will not cause sparking. Many grinding machines run oil-based coolant, and sparks can cause the oil to ignite. Brass is superior for these especially flammable conditions.
Steel substrate is still a highly durable option for aggressive grinding applications. The strength of the steel is long lasting and prevents damage to the core.
Each material has its advantages. When you talk to a CDT grinding specialist, they will gather information about your manufacturing goals and recommend the substrate that has the right features for your application. Stop trying to succeed with the same grinding tools your competitors are using and instead gain an advantage with grinding solutions that are specially design with your process in mind for optimal performance.
If you would like to see if your plated grinding wheels would work better with a different substrate — or to find out about innovations in vitrified, resin bond, or metal bond grinding wheels that may benefit you — contact us for a free quote: 800-443-6629.
Take a Tour of CDT’s Plating Department
Why Switch To A Vitrified Superabrasive Grinding Wheel?
What is a Vitrified Superabrasive Grinding Wheel and what are the benefits of using one? In this blog, you’ll learn who should switch to Vitrified >
How a grinding wheel performs is dictated as much by the bond as the abrasive. Superabrasives, which can be either diamond or cubic boron nitride (CBN) have four types of bond: metal, plated, resin and vitrified. Of these, vitrified may be the least well-known, yet it’s attracting attention, thanks to the improved performance and lower costs that it offers.
WHAT IS A VITRIFIED WHEEL?
In a vitrified wheel superabrasive grit is mixed with a type of glass or ceramic and then pressed before firing in a kiln. This creates a porous, glass-like structure that holds the grit in a rigid matrix.
Unlike a plated wheel where the abrasive is just a single layer, a vitrified wheel can have considerable depth. This means the wheel can wear and go through repeated dressing. Wear rates are very low as the vitrified bonds must fracture to release worn grit and expose fresh edges. It’s also possible to put a form into the wheel to allow grinding of complex profiles, (although this does complicate dressing.)
BENEFITS OF VITRIFIED DIAMOND AND CBN WHEELS
The open, porous structure ensures the grit stands proud of the bond surface, creating a wheel that’s described as ‘free cutting.’ This means good space for chip clearance, which:
increases material removal rate
lessens dressing frequency
reduces wear
carries coolant through the grinding zone
lowers grinding forces, thus creating less heat and less work piece damage
As an additional benefit, these last five points result in lower temperatures at the interface and reduced risk of workpiece burning in metals and less microcracking in ceramic and hard materials.
Lower temperatures help maintain control over final size, as does the very rigid nature of the wheel. With minimal wheel deflection due to grinding forces and low thermal growth very high tolerances can be maintained throughout a production run.
APPLICATIONS
High volume production are ideal applications for vitrified grinding wheels. Low wear rates, combined with a free-cutting nature and ‘dressability’ mean very high material removal rates and less downtime for wheel changes.
Vitrified cubic boron nitride grinding wheels are preferred for grinding hard ferrous workpieces like crankshafts and camshafts as well as tool steels. Vitrified diamond grinding wheels are good in non-ferrous applications such as shaping ceramics and carbides.
THE HIGH-VOLUME WHEEL
Of the four main bond types, the vitrified wheel is best suited for high volume, extended production run applications. The rigid, porous structure delivers high material removal rates and extended life, helping lower manufacturing costs.
Call the engineers at CDT at 800-443-6629 to talk over your specific application and determine if a custom vitrified grinding wheel would benefit your manufacturing process.
Is Continental Diamond Tool ISO 9001 Certified?
Continental Diamond Tool has implemented and maintains a Quality Management System that meets the requirements of ISO 9001:2015, as a manufacturer and distributor of Super Abrasive Grinding Products.
Quality Management
ISO 9001 Certification
Continental Diamond Tool Corporation in New Haven, Indiana, USA, underwent its most recent ISO audit in April 2024, conducted by IsoTec Alliance. A similar recertification audit at Continental Diamond Tool Limited in Kinmel Bay, Rhyl, U.K., was completed in February 2023 in collaboration with BM Trada. The comprehensive review covered all processes and documentation, with a particular emphasis on control plans, training records, and employee interviews across various departments. Following the rigorous four-day assessment, the auditor granted recertification for ISO 9001:2015, highlighting the company's steadfast commitment to maintaining superior quality management practices.
The ISO program mandates meticulous review of all processes, establishment of Standard Operating Procedures (SOPs), work instructions, and control plans, along with comprehensive training sessions for employees at all levels to ensure familiarity with ISO procedures. The Stage 1 audit, typically lasting one day, serves as an initial assessment by IsoTec Alliance to gauge readiness for Stage 2. Upon successful completion of Stage 1 with no issues detected, IsoTec recommends progression to Stage 2. Stage 2 entails a thorough four-day audit, during which auditors scrutinize all facets, including documentation and processes, to validate adherence to prescribed practices. This includes thorough examination of control plans, training records, and interviews with employees across various departments. Following the Stage 2 audit, a closing meeting is convened to assess the company's compliance, and if deemed satisfactory, certification for ISO 9001:2015 is granted. The official certificate is then issued to the company several days after the audit's conclusion.
Recertification audits are obligatory every three years to maintain ISO 9001:2015 status. These audits serve to ensure continued adherence to the stringent requirements outlined by the ISO program, underscoring the company's ongoing dedication to operational excellence and continual improvement.
The Evolution of Vitrified Grinding Wheels (Part 3)
In part 3 of this 3-part blog series, we explore the advantages and limitations of the Vitrified Grinding Wheel in various grinding applications.
Vitrified Superabrasive wheels use either diamond or CBN in a glassy or ceramic bond. Conventional grinding wheels use either Aluminum Oxide or Silicon Carbide, as with all grinding wheels, the bond imparts certain characteristics, making it better suited to some applications than others.
ADVANTAGES
High strength structures with porosity for clearing chips and bringing coolant to grinding zone allow for reduced grinding cycle times.
Porosity for coolant and chip removal efficiently remove heat and reduce work piece thermal damage and stresses.
Efficient chip removal reduces wheel dressing frequency thus prolonging wheel life thus lowering machine down time for wheel changes and lowering waste removal costs.
High wheel stiffness, long wheel life, and minimal heat generation allow for excellent finish and dimensional tolerancing.
Wheel specifications can be optimized for each specific application (machine, coolant, work piece, stock removal, dressing, etc…)
High product uniformity and performance allows for continuous unmanned grinding operations.
Automated dressing and wheel conditioning.
LIMITATIONS
Wheel manufacturing process controls need to be tight to ensure repeatability and product consistency (most sensitive of bond systems to process variations).
Wheel designs need to be matched to the application (i.e. solid Vitrified wheels are limited to 80m/s operation, Vit wheels with steel cores can be rated for use up to 170m/s operation).
Wheel prices may seem high when compared with conventional or other Superabrasive grinding wheel prices (need to look at all costs, not just wheel price).
Significant capital investment in terms of equipment to maximize cost benefits of higher concentration CBN and Diamond Vit wheels for high volume applications.
Generally requires knowledge of complete grinding process to maximize grinding performance. Grinding application support is necessary in many applications
Difficult to cross reference competing manufacturers wheel specifications
APPROPRIATE APPLICATIONS
Vitrified CBN grinding wheels are ideal for high volume applications where productivity is paramount such as Automotive applications like Cam & Crank shaft grinding, and Aerospace engine component grinding. Recent advances in bonds and wheel specifications has led to the development of wheel structures for use on older less suitable grinding equipment and applications like surface and cylindrical grinding in mold and die shops.
Vitrified diamond grinding wheels are most suited for grinding of very hard Ceramic and Carbide materials. Applications include grinding of PCD and PCBN cutting toolings, structural ceramic components, and Carbides.
CURRENT RESEARCH
Improved bond and wheel strength through continuing work with “Ceramic” bonds.
Abrasive grit customization for better chemical and mechanical bonding in existing and new “Ceramic” bonds.
Improved understanding and modeling of the grinding process.
STILL EVOLVING
Vitrified Diamond and CBN wheels compositions continue to evolve through the use of new chemistries and processing variables to enhance grinding wheel structures and performance. When it comes to grinding hard to grind materials, there are no better abrasives than Superabrasives; Diamond and CBN. Vitrified structures combined with Superabrasives often times allows for the best compromise between wheel life and grinding performance, thus giving the lowest overall costs in grinding.
The Evolution of Vitrified Grinding Wheels (Part 2)
We reviewed the materials of the Vitrified Grinding Wheel development in part 1 of this blog series, now we will discuss the bond. Learn more >
Any review of vitrified grinding wheel development should cover both the abrasive materials and the bond medium. Part 1 of this series addressed materials; here we turn to the bond.
THE BOND MEDIUM
Grinding wheels probably originated in ancient Egypt where they were likely cut from sandstone. They also appear in sketches by Leonardo da Vinci and it's thought Belgian gem-polishers were using a cast iron wheel impregnated with diamond powder during the late 1700's, but little else is known until the early nineteenth century.
Around this time the first solid-bonded abrasive wheels appeared. These were made in India for hand-grinding gems and used emery or corundum abrasive in a gum resin shellac binder.
Rubber bond grinding wheels were introduced around 1860, again using corundum.
The first Vitrified (glass) bond wheels were commercialized about ten years later. What are today known as Resin (plastic) bonded wheels didn't appear until 1923. Metal bonds for diamond grinding wheels weren't introduced until the early 1940's.
CREATING A VITRIFIED BOND GRINDING WHEEL
The term “Vitrified" in its simplest form means “glassy” or “glass bond." Abrasive Materials such as Aluminum Oxide, Silicon Carbide, Diamond, and CBN are mixed with glass frit (ground glass) and other ceramic materials (clays, feldspars, fluxes, etc…). More recent advances in “Vitrified” bonds has led to the development of “Ceramic” bonds. In general terms, Ceramic bonds are those in which some or all of the glass phase has been converted to a crystalline phase to enhance certain material properties (i.e. higher strengths). Blended grinding wheel compositions are then formed either by “Hot Pressing” or “Cold Pressing” processes.
In Hot Pressing, the blended wheel materials are placed into a suitable mold and simultaneously pressed and sintered (baked). In sintering, the glass & ceramic components are fused and melted together forming the hard Vitrified Bond that holds the abrasive materials in place. Because the grinding wheel is simultaneously pressed and sintered at high temperatures, mold material selection has to withstand the processing temperature. Hot Pressed Vitrified wheels usually have low porosity levels and are very different in their use applications when compared with Cold Pressed Vitrified grinding wheels.
In Cold Pressed Vitrified Products, an extra material called a binder is blended into the wheel composition. The purpose of the binder is to provide handling strength to grinding wheels that are pressed in molds at room or low temperature and then removed for subsequent and separate sintering in kilns (high temperature ovens). In the sintering process, the temporary binder is removed at a low temperature and the glass is fused together at a high temperature forming the rigid hard Vitrified bond. Cold Pressed Vitrified grinding wheels generally have high levels of porosity in their structures.
Grinding wheel properties are adjusted by varying the percentage of abrasives, size of abrasives, blends of abrasives, different bonds and bond types, manufacturing process, etc… Varying the amount of the abrasive in Superabrasive Grinding wheels is referred to as the “Concentration”. Higher Concentrations contain more material and in general provide longer grinding wheel life as there are more Diamond or CBN cutting points to remove material.
CREATING POROSITY IN VITRIFIED GRINDING WHEELS
Porosity carries coolant through the grinding zone and provides space for chip clearance. By providing space to remove grinding swarf (used grinding wheel and removed work piece material), the grinding wheels are able to grind faster, provide better surface finishes (especially if the grinding fluid is filtered to remove the debris). Because open spacing in a wheel structure brings liquid coolants to the grinding zone, they are also known to grind cooler. In so doing, Vitrified Grinding wheels can remove the heat generated during grinding much more efficiently thus allowing faster grinding cycle times and less thermal damage to sensitive materials like Steels and Aerospace Alloys.
Porosity in wheels structures can be created by a variety of methods. In cold press and sinter manufacturing, the wheels are pressed to limited densities and sintering is controlled to limit shrinkage and densification. Another method for creating porosity in grinding wheel structure is through the use of additives in the wheel compositions that are then removed in the sintering stage, thus leaving voids (porosity) where the material once resided. Additional porosity can be generated by adding constituents to wheel compositions that remain within the wheel through manufacturing but are initiated when used. For example, some wheel compositions include material that doesn’t melt in processing but is dissolved in coolant upon use (i.e. Salt). Another example of induced porosity would be the use of hollow microspheres which upon use are broken open, leaving the open void as a pore.
Stay tuned for part 3 of this series where we will explore the advantages and limitations of vitrified diamond and cbn wheels in various grinding applications.
New Master Surface Finisher at CDT
Jordan Donnelly, CDT’s Plating Research and Development Manager, has been named a Master Surface Finisher (MSF).
CDT is proud to announce that Jordan Donnelly, Plating Research and Development, has been named a Master Surface Finisher (MSF).
The MSF is the highest designation given by the National Association for Surface Finishing. Master Surface Finishers must demonstrate mastery of essential finishing processes, as well as knowledge in specialized processes and environmental stewardship.
In July 2020, Jordan Donnelly was recognized as one of the top "40 under 40" in the surface finishing industry by Products Finishing Magazine.
Excerpt from article:
"Jordan has been in the finishing industry for 15 years. He recently completed the AESF Foundation’s Certified Electroplater-Finisher program and the CAF – Airline and Aerospace certification. He is working towards Master Surface Finisher certification."
Full article: www.pfonline.com/articles/40-under-40-class-of-2020
We are proud of Jordan for his drive, determination, and dedication to his craft, and we're happy to have him on our team.
The Evolution of Vitrified Grinding Wheels (Part 1)
The vitrified bond grinding wheel first appeared 150 years ago, and continues to become ever more valuable. Learn more about the evolution >
The vitrified bond grinding wheel first appeared 150 years ago, and continues to become ever more valuable. While some products reach a kind of developmental plateau where there's no potential for further improvement, research continues to uncover ways of making vitrified wheels cut faster and last longer.
When it comes to shaping hard materials quickly, accurately, and cheaply the vitrified superabrasive grinding wheel has few rivals. Low wear, high heat stability, combined with a free-cutting nature and excellent ‘dressability’ mean very high material removal rates and less downtime.
Understanding how this tool evolved yields some fascinating insights into its use in manufacturing. This begins with an overview of grinding wheels and abrasive materials, covers the production process, and explores where the technology might be heading.
HISTORY OF GRINDING WHEELS
Any review of grinding wheel development needs to cover the two primary components: the abrasive materials and the bond medium.
ABRASIVE MATERIALS
It is thought that sandstone was the first abrasive material. Probably used for putting a sharp edge on axes, compacted quartz embedded in the rock grains proved an effective way of removing material, (much like sandpaper today.) However, as a natural material sandstone has the disadvantage that the quartz particles vary in size and shape, resulting in unpredictable performance.
An alternative material, emery, was known to the Greeks and Romans as an abrasive and is still mined on what is today the Greek island of Naxos. Emery is a form of corundum, the second hardest naturally occurring material, is the crystalline form of Aluminum Oxide containing traces of Iron, Titanium, and Chromium.
As an abrasive emery had two problems: it was expensive to extract and ship to the manufacturing centers in the UK and USA, and its performance was unpredictable due to variance in raw materials that are mined. Spotting an opportunity, entrepreneurs set about developing alternatives. The results included synthetic or manmade Silicon Carbide and synthetic Aluminum Oxide (Corundum). These materials are generally known as “Conventional Abrasives."
INTRODUCING SUPERABRASIVES
Natural Diamond, has been used for grinding since at least the seventeenth century when Belgian gem-polishers used Diamond powder embedded in cast iron. Cost and variability of natural Diamond held back wider use until the creation of synthetic Diamond changed the equation in the 1950s.
As the hardest known substance, Diamond makes an excellent abrasive in most instances. There are certain Ferrous, Cast Iron, and Aerospace alloy materials, however, that produce a chemical reaction with Diamond causing it to wear rapidly and to alter the properties of the material. To address this problem, in 1969 General Electric introduced a crystalline material they had developed with a hardness approaching that of Diamond: Cubic Boron Nitride (CBN).
Despite having a lower hardness than Diamond, CBN doesn’t react with Ferrous and Aerospace alloys when grinding and has an even higher temperature stability. Therefore, it offers better grinding performance when grinding these particularly tricky materials.
Diamond and CBN are generally known as “superabrasives" for their unique, highly effective, grinding capabilities.
In part 2 & part 3 of this series, we will look specifically at the vitrified bond medium and its advantages and limitations in various grinding applications.
Grit Size And Its Impact On The Grinding Process
Grit size only approximately correlates to surface finish: machine condition and the type of workpiece make a big difference. Learn more >
Shop for sandpaper in the hardware store and you'll see a numbering system indicating roughness. A coarse 80 grit grade removes material quickly but leaves the surface rough while a fine 400 grit won't take much off but leaves a smooth finish.
Superabrasive grinding wheels are no different. The size or coarseness, of the grit is indicated numerically in the wheel identification code, and guides the user in how that particular wheel should be used. Diamond is available in grit sizes from 40 to 8,000 mesh while CBN comes in the range of 50 to 8,000 mesh. As with sandpaper, a smaller number signifies the abrasive particles are larger.
RELATING GRIT TO SIZE
Grit numbers are derived from mesh sizes, mesh being the standard way of grading powder. The general principle is that of sieving: the finer the mesh the smaller a particle must be to pass through the gaps between the wires. Mesh size is indicated in gaps per inch, so a mesh of 16 has 16 gaps per inch.
When referring to powders mesh size is actually shown by two numbers, such as 50/60. The first number is the sieve through which most of the powder grains would pass, and the second is the mesh size that traps most of the grains. For simplicity, in the superabrasives industry the grit number refers to the larger size mesh, the one through which most particles would pass, so powder with a mesh size of 50/60 is referred to as 50 grit.
On average, in a 50 grit powder the particles are around 300 microns or 0.011 inches in diameter. That's roughly the size of grains of beach sand, although it's important to note that sieving result s in a distribution of sizes and shapes.
IMPACT ON GRINDING PERFORMANCE
As with sandpaper, larger abrasive particles, (a smaller grit number,) remove material faster but leave a coarser finish. With a finer grit, (larger number,) each particle removes less material. The removal rate will be lower but the surface finish will be smoother.
Grit size only approximately correlates to surface finish: machine condition and the type of workpiece make a big difference. Grit size, concentration, bond type plus hardness, and the grinding process (machine, wheel speed, coolant, work-piece) all greatly impact the surface finish achieved. Our engineers take all of these factors into consideration when optimizing custom grinding tools for our clients. Contact CDT for engineered superabrasive grinding solutions.