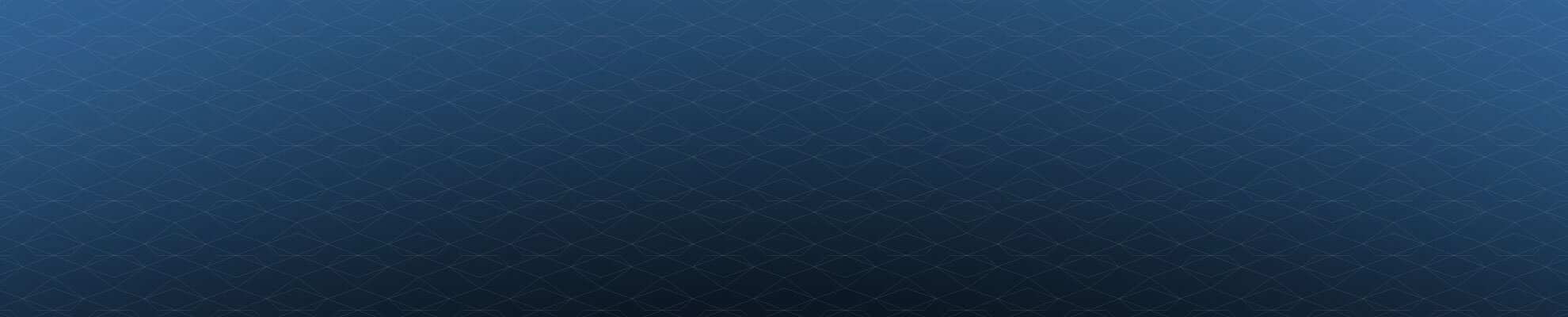
News and Resources
Browse by Category
Browse by Product
- All Dressing Products
- All Grinding Products
- CBN-Diamond Superabrasives
- Conventional Abrasives
- Diamond Lapping Compounds
- Diamond Rotary Dressers
- Diamond Stationary Dressers
- Hybrid Bond Grinding Tools
- Metal Bond Grinding Tools
- Plated Grinding Tools
- Resin Bond Grinding Tools
- Vitrified Bond Grinding Tools
5 Factors for Best Dressing Performance
Find the perfect rotary diamond dresser for your application by considering these 5 factors. Continental Diamond Tool Limited offers decades of expertise and free consultations for customized solutions >
The intricacies of selecting the ideal rotary diamond dresser for your unique application depend on many factors like tolerance, surface finish, configuration of form, grinding machine type, and grinding wheel specification. Continental Diamond Tool (CDT) has extensive experience in designing and crafting dressing solutions that perfectly suits your needs. Customization is key. Read on to discover how tailoring a diamond rotary dresser to your process can improve grinding performance.
Plunge dressing vs. Traverse dressing
Traverse dressing and plunge dressing are two methods that employ diamond rotary dressers in precision grinding applications. Each dressing technique requires a different form to serve its unique purpose.
Traverse dressers are designed to move across the surface of a grinding wheel, gradually shaping and refreshing its profile to maintain consistent performance and geometric precision. This method is ideal for applications where maintaining a constant wheel profile is crucial, such as in high-precision cylindrical grinding.
On the other hand, plunge diamond rotary dressers are employed to create specific, intricate profiles or contours in a grinding wheel. By plunging the dresser directly into the wheel, they generate complex shapes and features with precision. These dressers are particularly valuable in applications requiring customized workpiece forms, like gear grinding or aerospace components.
Both methods play a vital role in the manufacturing industry, ensuring the optimal condition and shape of grinding wheels. This, in turn, guarantees the quality and accuracy of the finished workpieces.
DIAMOND ROTARY DRESSER TYPEs
The diamonds in Diamond Rotary Dressers are what give this technology its cutting edge. There are four unique processes that can be used to adhere the diamonds to the dresser form:
REVERSE PLATED - Reverse Plated Dressers are best suited for applications where high accuracy of profile and a correspondingly high quality surface finish on the component are required.
HANDSET SINTERED - Handset Sintered Dressers are our most commonly used type of Rotary Diamond Dresser. They cover applications where robustness is required and the general tolerance is open.
CVD SINTERED - CVD Sintered Dressers are highly resistant to chipping and fracture, and they wear evenly over the dresser’s entire length. They also have outstanding thermal stability in use.
RANDOM SET SINTERED - Random Set Sintered Dressers are perfect for applications requiring openness, tight form, and improved surface finish. They can be delivered quickly to meet urgent demand.
Sometimes called Truers or Rollers, how do you know which of these will be the best diamond rotary dresser type for your application? Especially when each of these categories contain many further variables of appropriate diamonds and setting patterns.
5 factors for proper dresser selection
Proper dresser selection starts with investigating these five factors. Every well designed dressing tool must meet the specific requirements of these areas:
TOLERANCE - Tolerance refers to the allowable deviation or variation from a specified measurement or dimension in a workpiece. In the context of dressing tools, it's essential to consider the level of precision or accuracy required in the dressing process to meet the desired workpiece tolerances.
SURFACE FINISH - Surface finish pertains to the quality and texture of a workpiece's surface after the grinding or machining process. When designing a dressing tool, you need to account for the desired surface finish, which can range from rough to smooth, as it influences the choice of abrasive grains and dressing techniques.
CONFIGURATION OF FORM - Configuration of form relates to the specific shape, contour, or profile that the dressed grinding wheel should have. It encompasses the design and geometry of the wheel, which needs to be precisely replicated by the dressing tool to achieve the desired workpiece shape or finish.
GRINDING MACHINE TYPE - The type of grinding machine used in a particular application, such as cylindrical, surface, or centerless grinding, significantly impacts the dressing tool's design. Different machines require specific dressing techniques and tools to optimize performance and precision.
GRINDING WHEEL SPECIFICATION - This factor involves the characteristics and properties of the grinding wheel to be dressed. It encompasses details like wheel diameter, abrasive type, grain size, bonding material, and other specifications. The dressing tool must be compatible with these wheel specifications to ensure effective and efficient dressing.
Considering these factors when designing a dressing tool is crucial to achieving the desired precision, surface finish, and workpiece quality in various grinding applications. Correct specification involves the appropriate design, selection and placement of diamonds in a way that takes into account all the factors affecting the individual customer's application. It cannot be achieved by choosing from a small range of general purpose dresser types. Customization is required.
Our team at CDT has decades of experience in specifying and manufacturing Rotary Diamond Dressers for individual applications is second to none. Our processes are what make the Consort Precision™ Diamond Rotary Dresser truly exceptional, winning awards in the industry. We now manufacture and ship our custom diamond rotary dressers from both Europe and North America. The best part? It you costs nothing to consult with us—so contact us first to find the very best fit for your project.
Custom Rotary Diamond Dressers in as little as 4 weeks: How do we do it?
Industry-standard lead times for diamond rolls can take 8 weeks or more. If you are looking for a better, faster rotary diamond dresser alternative, we can expedite service in as little as 4 weeks. Learn how >
Since 1984, Consort Precision Diamond has supplied diamond wheel dressing products to a broad range of industries including aerospace, aircraft, automotive, blade and knife, power generation, medical, cutting tools, tool & die, saw, gear, and bearing and many other applications. What all these grinding operations have in common is that they typically require some form of wheel dressing to re-establish the wheel profile and/or recondition the wheel face.
About Wheel Dressing or Conditioning
Wheel conditioning involves the sharpening and opening of the wheel face, while also removing dull abrasives, excessive bond, and workpiece material (loading). A sharp and open wheel face will allow maximum possible material-removal rates and reduced thermal stress on the workpiece.
Consort’s rotary dressers provide the ideal profile for your desired wheel topography, with superior materials and manufacturing technology. Because your dresser is custom manufactured, demanding and complex configurations are possible.
Diamond Roll Delivery in as Little as 4 Weeks
The question then turns to delivery and lead times. In business, time is money. Industry-standard lead times for custom rotary diamond dressers can take 8 weeks or more. That’s a long time to wait for a critical part in your manufacturing process. Consort has made a reputation for fast delivery with a standard lead time of 6-8 weeks.
Need a tool in a hurry? Customers can request “Expedited Service” for custom diamond roll delivery in as little as 4 weeks. With manufacturing, delaying maintenance can really add to your costs in the long run. When a job is expedited, we work with our customers to get them their tooling as soon as possible.
We pride ourselves on prompt service and communication. At any time, you can reach out to your Consort account representative to begin an order or find out its status. If you do not have an account rep, please reach out to our customer service through our website online form or call 800-443-6629.
Lead times should not be a hurdle in the proper maintenance of your grinding equipment. If you are looking for a better, faster diamond roll supplier, let our service techs help you get the process started.
Understand Dresser Options To Cut Costs
Dressing is at the heart of a simple process: Use a diamond to expose fresh grit on the grinding wheel to extend its life. Yet there are dozens of different dressing tools — learn which to choose.
If you look at “Dressers “ or “Diamond Rolls” on the CDT website, it reveals several different types. Dressing is at the heart of a simple process: Use a diamond to expose fresh grit on the grinding wheel, so why so many tool options?
Focus on cost per piece
Stopping to sharpen the wheel means lost production, so it’s tempting to dress infrequently and to do it as fast as possible. Most shops know that’s a mistake, so they look for other routes to cut costs.
For some that means buying the cheapest single point dressers they can find. That’s often false economy. Instead they should try to minimize the dressing cost per work piece. That might mean buying better quality or more sophisticated dressers, which is why so many different types are offered.
Single point
The single point diamond dresser is the workhorse of grinding. It works in practically every application but is especially effective on straight wheels and for creating simple profiles. Special variants of the single point dresser are used for thread forms.
Diamonds aren’t cheap though, especially the better quality ones that better resist microcracking, so it’s important to get as much life from the dresser as possible. That means rotating the diamond regularly and changing the face exposed to the wheel to even out the wear.
Some diamond dressers are resettable, meaning the diamond can be reoriented to expose a fresh point. That adds to the cost but can mean an overall saving when compared with nonresettable dressers that are effectively throwaway items.
Multipoint dressers
In multipoint dressers, several diamond points work together to dress the grinding wheel. They work well for straight pass grinding on larger OD wheels as well as surface and centerless wheels.
A special form of the multipoint dresser is the donut cluster. These consist of a large number of diamonds set in a large crown. Good for dressing large wheels quickly, they are especially recommended for use on cylindrical grinders.
Grit dresser tools
Continuing the progression toward more dressing points, these tools use a diamond grit rather than discrete diamonds. These are long-lasting and allow for rapid dressing, making them very cost effective.
Blade dressers
Similar to a chisel in appearance, these present a line of diamond to the wheel. While they work for straight dressing, it’s more common to use them for profiles. Blade dressers come in both fixed and swivel head geometries for additional versatility.
Rotary diamond dressers
Rotary Diamond Dressers are a highly efficient and cost effective means of dressing and truing grinding wheels. Their use in achieving accurate correct form, tolerance, and condition is rapidly growing in the automotive, aerospace, power generation, machine tool and precision engineering component manufacturing.
Not an easy choice
There are several routes to minimize dressing cost per work piece and even for experienced machinists, it’s not always obvious which to take. That’s why it’s advisable to consult with experts to determine the best type of dresser for your application.
Supplier to Rolls Royce Creating Additional Jobs
Consort Precision Diamond, U.K. manufacturer of sophisticated cutting tools for Rolls Royce and other automotive and aerospace companies, is to create 23 new jobs. Consort is a subsidiary of Continental Diamond Tool Corp.
Consort Precision Diamond, the Continental Diamond Tool subsidiary that specializes in Rotary Diamond Dressers, was recently featured in the Daily Post in Wales. Read the article below or link to the Daily Post website here.
Supplier to Rolls Royce Creating Additional Jobs
BY OWEN HUGHES, Business Correspondent | Daily Post
A company that manufactures sophisticated cutting tools for Rolls Royce and other automotive and aerospace companies is to create 23 new jobs.
Economy Minister, Ken Skates (pictured) visited Consort Precision Diamond in Kinmel Bay, Conwy to discuss the expansion plans, which will be supported by £200k from Welsh Government.
The Minister also spoke to the company’s management team about the types of challenges they are facing in the run up to Brexit, and urged them to take advantage of the range of support offered to Welsh business to help them prepare and build resilience ahead of Brexit.
Ken Skates said: “I am delighted that the Welsh Government is supporting Conwy based Consort Precision Diamond in its plan to expand its facilities and create an additional 23 highly skilled jobs at Kinmel Bay.
“The support from Welsh Government will help fund the first phase of a five year plan that will see Consort Precision Diamond building a new premises and increasing its head count to just shy of 170.
“It was also good to speak to the company about its Brexit preparations and to ensure they are aware of, and are accessing the full range of Welsh Government support.
“Consort Precision Diamond actually exports extensively to markets outside of the EU, meaning that it is a stronger position to deal with the changes and challenges that Brexit will bring.
“I would urge any business in Wales to access our comprehensive range of exporting support and advice so they can put themselves in the strongest possible position to navigate the journey ahead.
“Of course we know that what business really needs, and continues to call for, is certainty.
“For our part we will keep pushing the UK Government to take No Deal off the table and work to secure a Brexit that protects Welsh jobs and our economy.”
Source: https://wales247.co.uk/rolls-royce-supplier-creates-23-new-jobs-with-welsh-government-support/
How to Keep your Grinding Wheels Performing Every Time
Properly dressing your grinding wheels is an important step in helping them to work as they should.
Grinding wheels are a very important tool in many factory and shop situations. They can be used for any number of projects; because of this, they tend to become something that are taken for granted. You expect that when you go to the shop that the grinding wheels will work as intended.
However, there are a number of issues that can occur that prevent the wheels from grinding as they should. While some of these problems are big and require a replacement wheel, others are reparable. One of the most common problems is a wheel that is not providing as heavy of a grind as it should.
Commonly, new wheels may not have the same grinding power as wheels that have been “broken in” and used for some time. As such, it is important to understand the concept of dressing grinding wheels.
To get the best cutting performance from your grinding wheel it is important that the wheel have a sharp abrasive grain with cutting points that are well exposed and able to connect with the piece with which you are working.
The ultra-hard abrasive crystals often used in grinding wheels will remain sharp simply through the process of grinding itself. Essentially, the wheels will slowly expose further crystals and you will not need to continuously dress the wheel. This is one of the biggest benefits of these superabrasive grinding wheels.
However, one problem is when you are working with new wheels. Usually these wheels have a smoother grinding surface. This occurs because the crystals and the surrounding bond are still flush to the edge of the cutting surface. If you try to operate a wheel without first dressing it, you will find performance is lacking. This is called “loading.” A wheel that is loaded will have poor cutting performance and may even cause some burning to your work piece.
This is where dressers come in. Diamond dressing sticks or rotary diamond dressers (also known as diamond rolls) are supplementary tools that keep your wheel operating at peak performance.
Dressing your superabrasive grinding wheel enhances grain exposure and brushes away some of the bond so that the wheel will work as it should. However, it is important that you choose the right type of dressing for your wheel to get the performance you desire. Some of the qualities you should consider with your grinding wheel dressing include:
Hand held aluminum oxide or silicon carbide stick
Soft (G, H hardness)
Fine grit (200-400 mesh)
Another strategy is to lower the RPM of the spindle, at least temporarily. This will open the wheel quicker and expose the abrasive surface for a more open surface. Then, you can increase the RPM in the future when the abrasive surface has been properly dressed and exposed.
While dressing your wheel is often something that only occurs when the wheel is new, it is possible to experience burning and poor cutting even on an older wheel. If this happens, you can simply use the same stick and technique to re-expose the surface and reopen the wheel.
As you can see, there is a lot to think about when you are first setting up your grinding wheel or if you are working with a wheel that does not seem to offer the best performance. It is possible to get the performance you desire it just takes a little work and effort up front!
The Importance of Maintaining your Grinding Wheels
Learn how to use dressing tools effectively so your grinding wheels will have a long and productive life span.
To understand how important it is to dress grinding wheels, you must first understand just how grinding wheels work. A grinding wheel is an abrasive cutting tool. It rotates quickly while in use and is very similar to a saw. However, a saw blade is only sharp along the edge. A grinding wheel has small sharp grains distributed over the surface of the wheel. Dressing grinding wheels is important maintenance.
When you press another material to the grinding wheel, its surface is gradually worn away. The results range from subtle to dramatic depending on the wheel and its intended use. Grinding wheels come in different materials. The surface material of the grinding wheel will decide what items it will work on. For example, aluminum oxide wheels work well on many steels, wrought iron, annealed malleable iron, and bronzes. Silicon carbide works well on rubber and stone.
Grinding wheels come in various shapes, including cup, dish, and cylinder shapes. The shape of the wheel typically changes over time with use. When you notice that the wheel's shape is different from that initially displayed, it’s time to discuss the matter of dressing grinding wheels. You have options available to you such as diamond dressers for grinding wheels and aluminum oxide dressing sticks. Each has its own distinctive features.
Grinding wheel dresser diamond tools are an extremely hard and efficient option. Diamonds are best known for their sparkle and elegance, but they also have a durable quality that makes them ideal for dressing tools. The hard diamonds score and reshape most dressing wheels very quickly and efficiently. A diamond dresser for grinding wheels will work with nearly any material. Choose the dresser design that’s best for your desired finish and get to work returning your grinding wheel to its former glory.
Aluminum oxide dressing sticks are a good option as well. Aluminum oxide is often used to dress tools made from diamond. The diamonds are easily sharpened with aluminum oxide. If the tool you’re working with is itself diamond, opt for this type of dressing stick to keep it maintained.
Dressers come in many shapes so you can restore any type of grinding wheel easily. A chisel dresser creates a fine contour. Plunge dressers are best for a concave radius. Grit dressers have broad even faces for fast dressing on a large surface. There’s a tool for any grinding wheel so you can always keep your surfaces in top shape. Plan to use your dressing tools often and your grinding wheels will have a long life span.
Continental Diamond Tool has acquired Consort Precision Diamond
Continental Diamond Tool Corporation (CDT), an industry leader in Diamond & CBN grinding wheels and tools, today announces their acquisition of Consort Precision Diamond Company Limited, a leading manufacturer of Rotary Diamond Dressers in the United Kingdom. You can find them exhibiting together at GrindTec 2018 this week: Hall 4, Booth 4082.
Continental Diamond Tool Corporation (CDT), an industry leader in Diamond & CBN grinding wheels and tools, today announces their acquisition of Consort Precision Diamond Company Limited, a leading manufacturer of Rotary Diamond Dressers in the United Kingdom. You can find them exhibiting together at GrindTec 2018 this week: Hall 4, Booth 4082.
About CDT
Continental Diamond Tool, a private company located in New Haven, Indiana, is a leading producer in the global market for superabrasive grinding wheels and custom tooling. For more than 40 years, they have specialized in the design, manufacture and application of diamond and CBN cutting and grinding products and services. Their Electroplated, Resin Bond, Metal Bond, Vitrified Bond, and CDT-exclusive Hybrid Bond products serve a wide range of industries, including medical, oil & gas, automotive, aerospace, cutting tools, power generation, wood & saw, electronics, and many others.
About Consort Precision
Consort Precision Diamond Company Ltd is a private company established in 1984 by its shareholders as a manufacturing facility specializing in the production of Rotary Diamond Dressers for niche grinding operations. Their highly accurate precision components are used predominantly in automotive, aerospace and land-based turbine engine production.
For information on Consort Precision Diamond's Rotary Diamond Dressers, please contact our Customer Service at 800-443-6629 or info@cdtusa.net and they can assist you with a quote.
Dressing or Truing: What’s the Difference?
Although sometimes known as conditioning, any time a grinding wheel is mounted on a machine it must be both trued and dressed to produce satisfactory work.
Any time a grinding wheel is mounted on a machine it must be trued and dressed to produce satisfactory work. These two terms are sometimes lumped together as “conditioning” but they mean different things. Inexpensive conventional abrasive wheels are relatively robust: dressing and truing can often be performed at the same time and repeated periodically. The same is not true for CBN and diamond grinding wheels.
These superabrasive grinding wheels represent a considerable investment, which should be repaid in longer life and higher productivity. However, achieving that performance demands close attention be paid to truing and dressing.
WHY TRUE A GRINDING WHEEL?
No matter how precisely manufactured, once a grinding wheel is mounted on a spindle there will be some eccentricity. Even if it's less than 0.001” it's going to affect the final size and finish of the workpiece, so to produce high-quality work the wheel must be trued.
One method of finding high spots is with a child's wax crayon. Spin up the wheel and bring in the crayon until it just touches: high spots will quickly gain a colored layer.
TRUING SUPERABRASIVE WHEELS
Conventional grinding wheels are easily trued with a diamond cutter that's harder than the wheel matrix. Diamond and CBN wheels can't be cut, and instead are effectively ground to size. While this can be done by traversing a conventional grinding wheel or sintered diamond roller across the wheel face, many machinists prefer to use a brake-controlled truing device (BCTD.)
Like the other methods, the BTCD presents an abrasive surface to the wheel, but turns more slowly. This speed differential results in a precise and controllable truing operation.
DRESS AFTERWARDS
Truing creates a smooth surface on the wheel periphery, and with no exposed grit the wheel won't cut. Dressing sharpens the wheel by removing bond material and fracturing the superabrasive grit to expose fresh edges, so dressing always follows truing.
A superabrasive grinding wheel is largely self-sharpening, although the workpiece material can cause it to dull or load-up. In such situations the grit starts to either rub against the surface or plow, (pushing material aside). Both affect surface finish, increase cutting forces and create heat, which can damage the workpiece. The solution is periodic dressing.
IMPACT OF WHEEL CONSTRUCTION
Resin and vitrified superabrasive grinding wheels have some depth to the matrix. This allows a wheel to be dressed and trued several times. However, plated and metal bond wheels have a much thinner layer of grit and can only be trued to the depth available.