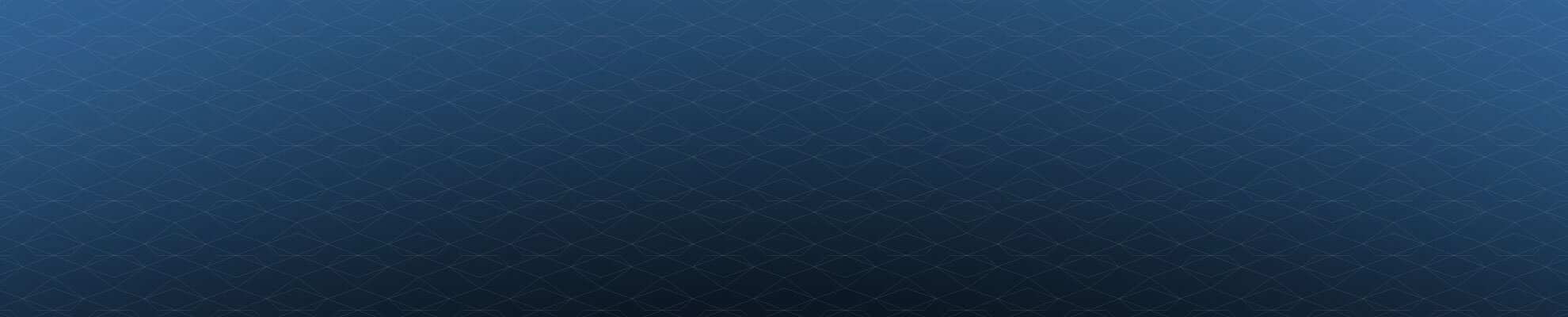
News and Resources
Browse by Category
Browse by Product
- All Dressing Products
- All Grinding Products
- CBN-Diamond Superabrasives
- Conventional Abrasives
- Diamond Lapping Compounds
- Diamond Rotary Dressers
- Diamond Stationary Dressers
- Hybrid Bond Grinding Tools
- Metal Bond Grinding Tools
- Plated Grinding Tools
- Resin Bond Grinding Tools
- Vitrified Bond Grinding Tools
Consort Precision Diamond Celebrating 5 Years With CDT
5 years ago, Continental Diamond Tool made one of our biggest leaps into providing top notch products for our customers by joining forces with our subsidiary – Consort Precision Diamond (CPD) – in the U.K. Learn more about what has been accomplished in the past 5 years >
5 years ago, Continental Diamond Tool made one of our biggest leaps into providing top notch products for our customers by joining forces with our subsidiary – Consort Precision Diamond (CPD) – in the U.K.
CPD is a leading supplier of precision Rotary Diamond Dressers for production grinding applications in aerospace, automotive, medical, tooling, etc.
CPD has and remains fully dedicated to this passion – to provide all customers with the best rotary dresser technology possible.
When it comes to Rotary Diamond Dressers, their focus is all-encompassing:
Design
Process & Product Development
Manufacture
Application Support
By teaming up with CPD, CDT has been able to bring quality rotary diamond dressers to the portfolio of superabrasive product offering, allowing for a fully integrated grinding process to the customer.
This has led to superior results for grinding wheel maintenance. The Rotary Diamond Dressers:
Can perform at high dressing speeds
Capability improvements -0.001um tolerance
Allow for more complex configurations
Improved product performance
Capacity expansions
Additional Products - CVD / Traverse disc dressers
Not only does it make way for excellent sharpening and fine finishes, it’s cost effective too.
But we’ve been up to more than just producing the highest quality rotary diamond dressers these past 5 years… All of which has had a direct, positive impact on the service you’ve come to expect with us at CDT.
More has happened over the past 5 years.
Capacity Expansion (2019/2020)
With the help of the Welch government we invested $500k into CPD.
New lathes
New grinders
New inspection lab/equipment
This improved our product quality, increased our capacity, and allowed us to hold tighter tolerances.
Major Upgrades to The Plating Lab
With the increase in demand, and our drive to supply the best of leading edge tech, we launched an upgrade to the plating lab in 2021.
This extension more than doubled our ability to produce high-quality tight tolerance reverse plated rotary dressers.
Featured In the British Chamber of Commerce Study
The British Chamber of Commerce published a case study featuring CPD and our growth in international trade.
We export to over 20 countries worldwide, including:
Europe
USA
Canada
Brazil
Mexico
China
Nominated for 2 Major Awards
CPD was nominated for the 2022 Chamber Business Awards and the WCNW Chamber Business Awards in Export & International Trade.
2x Faster Production Rate
CPD expansion was supported by the government of Wales with £200k.
This support helped protect/create new jobs and would “help fund the first phase of a five year plan that will see Consort Precision Diamond expand and increasing its head count.”
2023
CPD will be adding a new product line of electroplated grinding wheels in Q2, which will allow further expansion into the superabrasives products in the EU/UK markets.
CPD had championed so much in the past 5 years, maintaining and exceeding expectations for being the top producer of diamond rotary dressers.
Thanks for joining in the 5-year celebration with us! We expect even more great things in the coming 5 years.
To get a full look at all Consort Precision Diamond services, click here.
7 Reasons Why Vitrified CBN Grinding Wheels Surpass Conventional Grinding Wheels
Discover 7 reasons why CBN grinding wheels are your next game changer >
A vitrified CBN grinding wheel is a superabrasive grinding wheel made from a Cubic Boron Nitride abrasive in a porous – or “vitrified” (ceramic) – bond.
Vitrified CBN Grinding wheels are the most cost effective solution for production grinding of ferrous metals and aerospace alloys, and offer far superior performance when compared with conventional abrasive grinding wheels.
Especially for those in industries such as:
Aerospace
Automotive
Bearing
Medical
Gears
Mold & Die
Round Tools (drills, reamers, taps, etc)
Cutting Tools
So why exactly is that?
There are 7 critical reasons why making an upgrade to a CBN grinding wheel can make a huge difference in your industry.
1. 100 - 300x The LifeSpan
CBN abrasive is the second hardest material known to man and is 2 ½ times harder than Aluminum Oxide. Because of its high hardness, the CBN crystals offer 100-300 times the lifespan when compared with traditional grinding wheels.
While Vitrified CBN grinding wheels may cost up to 10 times that of a conventional wheel, the extended wheel life far exceeds the initial wheel cost, making it more cost effective. You get what you pay for – and this is definitely one of those products where you’ll quickly see the difference in its longer lasting abilities as compared to your old grinding wheels.
(We’d even argue that once you’ve used a CBN grinding wheel, it’s hard to go back – it’s just that big of a difference).
2. Reduced Thermal Damage
Because CBN abrasive has almost 50 times the thermal conductivity of conventional abrasives, it transfers the heat generated from the grinding process away from the workpiece, rather than being absorbed by the workpiece.
Combining the high thermal conductivity of CBN with the porous vitrified wheel structures, most heat is efficiently removed through the wheel and coolant, preventing heat damage to your workpiece.
With efficient removal of heat, your workpiece won’t be subject to thermal degradation or changes to the material properties – which is very important for improved wear and life of each component.
3. Optimize Your Grinding Process
With high life and improved thermal properties, Vitrified CBN can be pushed harder during grinding, and decreased grinding cycle times are able to be achieved.
As a result, the grinding process can be more readily automated. This creates less need for more grinding machines, floor space, wheel changes, waste generation, and operators – which has many advantages when it comes to your time, cost, and safety measures.
4. Customizable
Vitrified CBN grinding wheels are engineered per specific customer applications so you can achieve optimal performance.
Considerations that can be taken into account include: material being ground, grinding machine, coolant type and delivery, dressing method, stock removal, quantity of parts, etc… And aggressive, free-cutting bonds can also adapt to various spindle speeds. Which is not only convenient, but also cost effective.
5. Lights Out Operation
Vitrified CBN grinding wheels have “dressable” structures – which lend them to “lights out operation.” The grinding layer can be refreshed using a rotary, and in some cases, stationary dresser.
You’ll be able to automate every step of the manufacturing process, making Vitrified CBN grinding wheels an excellent choice for production based applications.
6. Re-Truing of Formed Profiles
Another benefit of having a “dressable” structure is that complex forms and geometries are able to be generated in Vitrified CBN grinding wheels. The profiles are able to automatically regenerate in line on the properly equipped grinder and maintain tight tolerances.
7. environmentally friendly
The use of Vitrified CBN wheels (as opposed to conventional abrasive wheels) results in significant reductions in waste generation. It decreases the amount of grinding debris (swarf) >99%.
It even allows for more recycling of the metal swarf that is generated because it is oftentimes free of grinding wheel breakdown. Many customers are able to get credit for the Environmental and waste reduction initiatives under ISO14000 and other programs.
Experience the cost effective solution for production grinding with Vitrified CBN Grinding Wheels. Contact us for your free quote.
Why Different Materials Need Different Grinding Wheels
With all of the grinding wheel options available, figuring out which one is going to be the most efficient and cost effective for your working material can feel overwhelming, but CDT is here to help.
With all of the grinding wheel options available, figuring out which one is going to be the most efficient and cost effective for your working material can feel overwhelming, to say the least.
This article will help cover the basics as to why different materials will need different grinding wheels - and how to select the appropriate abrasive type for your grinding wheel.
So why exactly do different materials require different types of grinding wheels?
It comes down to the material properties (i.e. material hardness and chemistry) and the proposed grinding process: factors like machine, coolant, dressing, stock removal, etc.
First, consider which type of abrasive will be best for your material: conventional or superabrasive?
Conventional Abrasives
Aluminum Oxide
Silicon Carbide
Aluminum oxide has a hardness of 1800 HrV and is commonly used in grinding of ferrous or other materials that are known to chemically react with carbon.
Silicon carbide has a hardness of 2800 HrV and is used on "hard" materials such as glass, ceramics and non-ferrous metals such as aluminum and copper.
Superabrasives:
Diamond
Cubic Boron Nitride (CBN)
Superabrasives are both harder (longer lasting) and have much higher thermal conductivity (remove heat of grinding more efficiently) compared to conventional abrasives.
Diamond is the hardest known substance with a hardness of 9000 HrV and is the most effective abrasive in grinding of materials that don't react with carbon such as glass, ceramics, and non-ferrous metals. It can increase wheel life by several orders of magnitude when compared with conventional wheels. Advancements in production of synthetic or man-made diamonds have brought their cost down and led to expanded use. We commonly see diamonds used for grinding tough materials such as very hard steels, cemented carbide, and aluminum oxide cutting tools.
CBN is the second hardest known material at 4500 HrV and is ideal for grinding ferrous metals and other materials that are known to react with carbon. It is commonly utilized in the grinding of high-speed steel, hardened cast iron, tool and die steel, and stainless steels. When appropriately specified and optimized, CBN can outlast conventional Aluminum Oxide wheels by a factor of up to 300:1.
NOTE: With so many benefits, you may be wondering “What type of materials cannot be ground on a grinding wheel?” Superabrasives (Diamond & CBN) are focused on hard materials. We turn to CBN for hardened ferrous alloys, stainless steel, and nickel alloys. Diamond is ideal for even harder materials such as glass, carbides, and ceramics. The harder the material, the better it is for grinding with superabrasives, which is what we customize for our clients at Continental Diamond Tool.
You often cannot justify the cost of a superabrasive grinding wheel for soft nonferrous metals (<30 HrC) like aluminum, brass, and copper. Materials with such soft properties tend to “clog'' and coat the wheel and would require continuous dressing.
Some have asked, “Can you use a superabrasive grinding wheel on wood?" Wood is a very soft, inexpensive substance and would not be well suited for superabrasive grinding. For similar reasons, we do not recommend superabrasive grinding wheels for other soft nonmetallic materials like fabric, leather, certain plastics and rubber, etc.
Now that you know the differences between Conventional and Superabrasive grinding wheels, you can see how each caters better to different materials and uses. Once you’ve narrowed down the proper abrasive type, a grinding wheel expert can help you narrow your selection further with a selection of different bond types, such as Resin Bond, Metal Bond, Vitrified Bond, and Electroplated.
The bond is what holds the wheel’s abrasive grains together. The strength of bonding of a grinding wheel is often referred to as its hardness. Generally speaking, grinding wheels with a higher grade or hardness are recommended for softer materials and vice versa. It is also now possible to combine bonds to form custom hybrid variations that have unique properties.
NOTE: You may be thinking “Why do we use hard wheels for soft materials in grinding?” This is a complicated subject with the actual grinding mechanism (chip formation) being different between ductile or soft metals and hard materials like ceramics. Grinding wheels for metals act like micro-cutting tools where metal chips are cut or torn away. The chip size and shape is dependent on the material properties.
With harder materials such as carbides and ceramics, there are brittle fractures where small chips are actually fractured away in the grinding process. The material itself is very abrasive. Because the chips in carbide and ceramics are so abrasive, softer wheels are often more efficient at removing the small abrasive chips (a.k.a. swarf).
When shopping for a grinding wheel manufacturer, it’s helpful to have some basic parameters handy to get the most accurate quote and best product for your application. For a whole list of considerations to bring with you for selecting the best grinding wheel, check out our article on How To Order Custom Grinding Wheels.
Then contact us to collaborate with our engineers, product managers, and technical sales people to go over all of these considerations with you. If you’d like, we can even come to your facility to review your process first hand and make recommendations.
When you have the optimal grinding wheel for your material, you will see the difference in speed, durability, and performance.
Choosing the Right Grinding Wheel
Choosing the right grinding wheel for any given project is perhaps the MOST important part of the process. Learn how to choose the right one. >
Choosing the right grinding wheel for any given project is perhaps the MOST important part of the process… But why?
It’s because choosing the WRONG grinding wheel for your material can be catastrophic for a whole host of different reasons. It can lead to:
Significant amounts of money lost
Major time delays to complete your project
Workpiece and/or machine damage resulting from running the wrong wheel or grinding process.
Alterations to workpiece properties (i.e. changes in material hardness from grinding).
That’s why it’s so important to go over your options carefully, and discuss them with your technicians and engineers to ensure your grinding wheel is going to get you the most bang for your buck, the fastest completion time possible while still providing high quality results, and will be safe for all workers involved.
So what exactly is a grinding wheel used for?
You can think of grinding wheels as really really souped up sandpaper… Just like sandpaper helps smooth a surface or remove excess wood, a grinding wheel is an abrasive that’s used to:
Remove any unnecessary material
Create a specific shape
Grind down your material
Prepare metal for proper welding
However, unlike sandpaper, grinding wheels are effective on many materials in addition to wood. Grinding wheels are most frequently used for almost any type of metal material you’re working with – and they produce results at a MUCH faster rate than precision cutting, saving you time and money. They can even be effective at grinding plastics, glass, and non-metallic materials.
How do you choose what kind of grinding wheel to use?
You should consider what type of material you have that needs to be ground.
The grinding wheel you choose needs to be made of stronger material in order to have an impact. Different grinding wheel types will produce different results.
For example, if you were choosing a knife to cut a loaf of bread… A serrated knife will produce a cleaner cut than your butter knife.
Choose the material that will give you the cleanest, smoothest outcome.
Here are some other key things to discuss with your engineers to make sure you select the best kind of grinding wheel to use for your project:
What material is being ground?
What abrasive type should be used for that material?
What size abrasive should be used (grain attribute)?
How course, medium, or fine should the abrasive material be (grit size)?
Coolant Type (if any)?
And what bond type should be used?
Our team can help you review your equipment and processes, the parts you’re looking to grind, and provide recommendations (including whether or not a custom superabrasive grinding wheel is necessary for your unique project needs).
When should you invest in a custom superabrasive grinding wheel?
Custom superabrasive wheels are usually either made with diamond or from Cubic Boron Nitride (CBN).
If your material that needs grinding is made of iron or other alloys, then a superabrasive CBN grinding wheel is your best pick. If your material is made of carbon, choosing diamond can help sharpen. Or if you have material made of granite, choosing diamond can help create a glossier finish.
Essentially, superabrasives are made from some of the hardest materials mankind can make. Traditional abrasives (such as aluminum oxide or silicon carbide) are much softer materials that can break down much quicker.
And while traditional abrasives may be less expensive, if you’re in any of the following industries, using a superabrasive will bring you the best, safest results:
Aerospace
Automotive
Medical
Electronics
Composites
Oil Industry
CDT is proud to have a strong group of engineers, product managers, and technical sales people in our back pocket who are more than happy to go over all of these considerations with you. You can come to our offices, or we can come visit your facility.
Diamond Rotary Dressers by Type
Find the perfect rotary diamond dresser for your application by considering these 5 factors. Continental Diamond Tool Limited offers decades of expertise and free consultations for customized solutions >
Industry's increasing demand for high-accuracy, high-speed production has fostered a new branch of engineering technology to ensure grinding wheels are maintained in optimum condition. Diamond Rotary Dressers are now recognised as the most efficient and economic means of dressing and truing grinding wheels to the correct form, tolerance and condition. Their use is growing rapidly in the manufacture of components for automotive, aerospace, power generation, machine tool and precision engineering industries.
Leading in innovation
At Continental Diamond Tool Limited, we have been a frontrunner for decades in innovating rotary dresser technology. As far back as 1995, as Consort Precision Diamond Company, we won industry awards for our development of the high speed plating process which dramatically reduced previous lengthy plating times and is still in use today. We proudly holds the ISO 9001:2015 Registration Certificate for its Quality Management Systems, and we are continuously innovating to increase the efficiency and cost effectiveness of this industry-changing technology.
OUR FOUR MAIN PROCESSES
There are four distinct methods we use in the manufacture of our diamond rotary dressers: reverse plated, hand-set sintered, cvd sintered, and random set sintered. Each has its own benefits, as outlined below.
Type 1 - Reverse-Plated
The High Accuracy dresser
Reverse Plated Dressers are selected where high accuracy of profile detail is required together with a correspondingly high quality surface finish on the component.
Accuracy is achieved by centrifugal dispersion of the specially selected diamonds onto the walls of a mould. These are secured by our electro-deposition process that has won acclaim through the acquisition of industry awards, thereby achieving the short lead times so often required by customers.
The electro-deposition process is stable and unaffected by shrinkage, which results in Rotary Diamond Dressers of exceptional accuracy.
Tolerance Detail
General Surface Finish Produced: 0.4uM. 16 C.L.A.
Typical Applications
Turbine Blade - Fir Tree Root Form
Cam Grinding
Bearing Industry
Ball Joints
Needle Injectors
Type 2 - Handset Sintered Dressers
A CONSORT PRECISION™ SPECIALTY
Of all the rotary dressers for which the Consort Precision name is known, Handset Sintered Dressers are our most popular type. These custom diamond rotary dressers cover many applications where robustness is required and the general tolerance is open.
As the name implies, diamonds are selected and set by hand in a mould, then secured in position by sintering in a tungsten based matrix. Allowances are made for consequential shrinkage to bring the finished dresser within specification tolerances.
Tolerance Detail
General Surface Finish Produced: 0.8uM. 32 C.L.A.
Typical Applications
Turbine Blade
Automobile Valves
Crankshafts
type 3 - CVD Sintered
THE High Performance Dresser
Our CVD sintered rotary diamond dressers have very high thermal oxidation resistance and other excellent thermal properties. CVD is perfect for secure mounting with traditional non-ferrous metal sintering. CVD sintered rotary diamond dressers can also be brazed onto a dresser body using an active braze alloy in a non-oxidizing environment.
Benefits
Highly resistant to chipping and fracture
Wears evenly over the dresser's entire length
Performs regardless of dressing orientation
Outstanding thermal stability
CVD diamond can be manufactured in a multitude of shapes, sizes, thicknesses and grades giving engineers great flexibility with this material's extreme properties.
Dimensions
Our CVD diamond dressers can be ordered in all the standard rectangular dimensions in various lengths and square, but we also specialize in supplying non-standard custom dimensions upon request.
Typical Applications
Metal matrix composites
Aluminium alloys
Glass-reinforced plastics
Carbon fibre-based materials
Plastics and rubbers
Graphite
type 4 - random set sintered
The dresser FOR QUICK DELIVERY
Random Set Sintered Dressers are most suitable where openness is required, coupled with a tight form and improved surface finish.
Very often selected diamonds are strategically placed in the mould to support the form in vulnerable areas. The remaining area is then in-filled by centrifugal dispersion of diamonds and sintered.
Random Set Sintered Dressers have the advantage that they can be delivered quickly to meet urgent customer requirements.
Tolerance Detail
General Surface Finish Produced 0.4 uM. 16 C.L.A.
Typical Applications
Automobile Valves
Turbine Root Forms
Flute Grinding
CHOOSING THE RIGHT DRESSER TYPE
Within each of these categories there are many further variables of appropriate diamonds and setting patterns to consider when ordering dressers of this type. Specialist techniques need specialist suppliers which is why we established our Consort Precision Diamond Rotary Dresser custom product line. Since 1984, we have dedicated substantial resources to developing the finest Diamond Rotary Dressers and support services available.
At Continental Diamond Tool Limited, we focus predominately on the design, development, manufacture, install and maintenance of Rotary Diamond Dressers. And we think that gives us a unique commitment to provide our customers with the best technology can offer.
If an application calls for a Diamond Rotary Dresser, Continental Diamond Tool will provide the best tool for the job. Contact us for a free consultation and quote.
How Does CDT Guarantee Grinding Wheel Performance?
Every grinding wheel purchase is backed by our Performance Payoff Guarantee. Learn how it works >
Customer satisfaction is our first priority at Continental Diamond Tool, best illustrated by our Performance Payoff Guarantee. What is that? It's our pledge to customers to guarantee a return on their investment. To summarize, if we cannot match the quality or life of your current tooling, you won’t pay a penny more than what it's worth to you. Here’s how it works:
1. Continental Diamond Tool guarantees that all of our tooling will be manufactured to the requested abrasive and dimensional specifications.
At CDT your manufacturing team will work directly with our engineers to design, test, and build tools customized to your processes in your industry. CDT will calculate the ideal abrasive size and style to meet your requirements for stock removal and surface finish while also accounting for the type of material being ground. Combine this custom grit with the best type of bond and, voilá, we have a grinding wheel design that will yield optimal performance for your operation.
Then, using state-of-the-art equipment and stringent quality control standards, we move your order into prototype and/or production to achieve some of the tightest tolerances in the industry.
2. As the customer, you define the length of time, the application requirements, and the test’s measurement for success.
With our grinding lab, we can perform remote product testing to eliminate your risk before you even have your grinding wheel in hand. Direct benefits include:
· Accelerated product development, with no conflict between product trials and actual production time.
· More savings and less risk, with optimization taking place during simulations rather than costly trials.
· Advanced innovation opportunities for exploring various product types and coolant delivery methods.
· Superior, usable data, thanks to monitoring sensors that record every aspect of each grind.
Even with simulated trials in our grinding lab, we still welcome the opportunity to put our custom superabrasive grinding wheels to the test in your live production environment. Our engineers are happy to come to your facility to aid in the setup process, compile before-and-after data, and summarize the results.
3. If we cannot match your current tooling’s quality or life, we will only charge according to its value to you, based upon the current tooling’s cost.
We would never expect our customers to settle for average or subpar performance. We believe wholeheartedly in the abilities of our team to produce superior grinding solutions for our customers. Our confidence comes from our founding principles of service, quality, dependability, and precision. However, talk is cheap, and we are a company of action. The Performance Payoff Guarantee holds us accountable to our customers. With it, you can see exactly what you are getting with your investment.
Take, for example, the experience of Jim Elliott of Advanced Carbide. After investing in a new hybrid solution for their vitrified grinding wheel, and seeing the results of their performance payoff guarantee trial, here’s what Jim had to say: “With this new bond [from CDT], we saw cycle time reductions of 20% or more, and the same amount of wear compared to our first generation vitrified wheel, which was already a vast improvement over a conventional wheel.” Click here to read more about it.
With every specialty superabrasive grinding wheel we make, we strive to improve grinding time, reduce overall tooling cost, and hit ROI out of the park.
If you have product warranty questions — or would like to request a quote — please reach out to your CDT representative, call 800-443-6629, or contact us through our online form.
What Is a Diamond Rotary Dresser?
Learn what Diamond Rotary dressers are you used for, the different types and where to purchase them. >
Grinding operations often work best with some form of wheel dressing to re-establish the wheel profile and/or recondition the wheel face. Wheel conditioning typically involves the sharpening and opening of the wheel face, while also removing dull abrasives, excessive bond, and workpiece material (loading). A sharp and open wheel face will allow maximum possible material-removal rates and reduced thermal stress on the workpiece. CDT engineers design each dresser to match your wheel topography so that it performs with superior strength and versatility. All are made with the highest quality CVD, natural diamond, synthetic diamond and combinations to maximize performance and roll life. Because they are custom manufactured, an abundance of configurations are possible.
Types of Diamond Rotary Dressers
There are two manufacturing methods for rotary dressers with several variations in setting/diamond application to best suit the customer application. Below are several examples:
1. Reverse Plated Diamond Roll
Manufactured with high accuracy molds and a tightly controlled electroplating process to deposit the nickel layer. The nickel layer holds the abrasive in place to allow for extremely complex profiles and tight tolerance work, which produce high quality surface finishes. Because of the accuracy on the front end of the process, these rolls require little to no surface conditioning, which leave sharp natural points for superior dressing, resulting in an open grinding wheel and lower grinding forces. Reverse plated rolls are ideal for continuous dress creep feed process, and complex forms like bearings, fuel injection, thread forms, and aerospace root forms.
2. Sintered Diamond Roll
Using a high temperature powdered metal process to create a tough tungsten matrix to secure the abrasive in the roll. This product is ideal for aggressive grinding and harsh working environment, while still holding tight profile tolerances and complex forms. These are all handset products, either pattern set or random set, to allow for a wide range of options on performance, surface finish, and roll life. Because of the manufacturing process, these rolls generally have shorter lead times and can usually be reworked to meet production demands. Sintered rolls are ideal for simple profile rolls to complex valve grinding assemblies.
3. Sintered CVD / Disc Dresser
These dressers use the same tough tungsten matrix as the standard Sintered rolls but are unique in the abrasive they are set with and how they are typically used. They are available using synthetic, natural, or CVD abrasive and can be set in combination to target specific performance, surface finish, and roll life. These are typically used to traverse across the grinding wheel to generate specific profiles and wheel conditions for open and free cutting grinding of the part. This style dresser is ideal for reconditioning, which can restore the roll to its original profile and tolerance in half the normal lead time and a fraction of the cost.
Where Can You Get a Diamond Rotary Dresser?
If you're looking to purchase a diamond rotary dresser, then you should know that Continental Diamond Tool Corporation is the final place to get them.
Experience
Since 1973, our family-owned company has built a reputation as a leading-edge manufacturer with a commitment to excellence.
Quality
Our engineers are highly specialized, and all our products are produced under stringent quality control standards.
Customization
We manufacture to your specific needs, providing you with specialized tools in a timely manner, with guaranteed satisfaction.
Precision
Our state-of-the-art equipment and expertise give our products some of the tightest tolerances in the industry.
Personalized Tech Support
From prototype to production, operations, or replacement tooling, our team works closely to get you the solutions you need.
Multiple Ways to Request an Estimate
Submit your project specifications and upload large files through our website: www.cdtusa.net/contact
Email details of your project with small file attachments to: info@cdtusa.net
Call our customer service team to talk through your project and discuss options: 800.443.6629
Why Choose Continental Diamond Tool?
There are a lot of reasons to consider Continental Diamond Tool, but we’ve narrowed it down to the top three reasons customers choose CDT. Check it out >
There are a lot of reasons to consider Continental Diamond Tool, but the top three reasons customers choose CDT are our high level of service, quality, and consistency.
Quality is the highest priority at CDT. We’re ISO Certified, with checks and balances in place to make sure each tool is the highest quality, every time.
Consistency means repeatability, so your tool is the same from one order to the next. You don’t deviate in your usage, so we have to nail it every time, with the tightest tolerances.
CDT has made customer service a main focus. Jeff Turner, Inside Sales, says, “It’s a priority that I take very seriously. Each customer should feel like they’re our biggest one.”
If you’re wondering why CDT, reach out to us. We will follow up so you can see if we can meet your needs, including our Grinding Lab, where we can show you first hand the benefits that you can get from our tooling.
Learn more about the reasons CDT is committed to you here:
Consort Precision Diamond Featured in British Chambers of Commerce Case Study
Consort Precision Diamond Co Ltd has been featured in a case study by the British Chambers of Commerce discussing Consort's exports strategy and more.
We are pleased to share with you that Consort Precision Diamond Co Ltd has been featured in a case study by the British Chambers of Commerce. The case study has been published on the British Chambers of Commerce website and shared on their social media channels. Here is an excerpt from the article:
The Consort team is immensely proud of their geographically-diverse portfolio of customers, with the export side of their business expanding rapidly. They currently export to over 20 countries worldwide, covering Europe, USA, Canada, South America, and the Far East.
During 2019 and 2020, their international trade accounted for 51% and 63% of their turnover respectively, and 2021 figures indicate that the export side of the business will account for 70% of their revenue. Brazil, Mexico, and USA are amongst the company’s largest markets, followed by Europe.
Click here to read the full article detailing Consort's exports strategy.
In addition, Consort is proud to have been nominated regionally in the 2022 Chamber Business Awards for their exports. We would like to congratulate the award winner, Metalfacture Ltd, who has been recognized as the British Chamber of Commerce National Global Player Export Business of the Year.
Consort has also been nominated for the WCNW Chamber Business Awards in Export & International Trade. The winner for that award will be announced at the ceremony on the 11th of November.
Consort Precision Diamond Company, a subsidiary of Continental Diamond Tool Corporation since 2018, is based in North Wales. They are a manufacturing specialist dedicated to the production of diamond rotary dressers, a complimentary product to CDT's custom diamond and CBN grinding wheels and tools.
What should you look for in a grinding wheel manufacturer?
Finding the right supplier of custom manufactured grinding wheels is crucial when your production is on the line. Here’s why you should consider trusting in CDT >
When you’re in search of a supplier of custom manufactured grinding wheels, we know you’re going to be focused on three main components: delivery, performance, and support.
At CDT, we deliver engineered solutions to help you complete your project on time. We will also meet or exceed any requirements you have for surface finish, tolerance holding, cycle time reduction, or anything else for which you are needing engineer solutions. We also provide support throughout the duration of the entire project, from beginning to end.
“We provide information and support all along the way,” says Harrison Sheldon, Application Engineer.
Watch our video to find out more about our commitment to excellence for our customers:
Top 10 Super Characteristics of Superabrasives
Here are the top 10 reasons you should consider a superabrasive solution for your precision grinding or finishing process. Check it out >
Superabrasive grinding products get their ‘super’ characteristics from the extremely hard substances used to make them. Unlike conventional grinding wheels that are created using blends of less durable abrasive grains, superabrasives use industry’s the hardest known substances to achieve their abrasive properties.
Diamond has the most extreme Knoop hardness rating around 7,000, with synthetic or manmade diamonds having a more consistent hardness than its naturally occurring counterpart. The other popular superabrasive material, cubic boron nitride (CBN), is an extremely hard synthetic grain with a Knoop rating of 4,700. Conventional grains typically range from 2,100 to 2,500.
Upfront cost for these superabrasive grinding products is very high when compared to conventional abrasives, so what makes them so valuable to many industries? The secret is in this product’s return on investment.
Here are the top 10 reasons you should consider a superabrasive solution for your precision grinding or finishing process.
10. Decreased Cost Per Part
9. Decreased Cost in Swarf Management
8. Increased Production Parts Per Dress
7. Multiple Profile Grinds Without Dress
6. Less Residual Stress or Damage to the Part
5. Increased Throughput
4. Lower Grinding Pressure
3. Higher Removal Rates
2. Improved Surface Finish
…and the number one reason superabrasive products are a ‘super’ solution to your grinding and finishing needs:
1. Lower Overall Tooling Costs
When companies add up the superior precision, efficiency, quality, and durability that comes with a superabrasive grinding wheels, superabrasive grinding wheels and tools quickly justify their upfront cost.
If you are interested in a free quote, contact our customer service team to discuss how a superabrasive solution can be used to improve your company’s bottom line.
What is the benefit of having a grinding lab on site?
Our grinding lab gives us the opportunity to work with customers to develop grinding processes that are specific to their materials, equipment, and applications. Learn more >
Here at CDT, we have a technologically advanced research and development grinding lab. This gives us the opportunity to work with customers to develop grinding processes that are specific to their materials, equipment, and applications. Our setup is unique, in that we’ve added numerous extra sensors to capture data on every element of the grinding process, to replicate what’s happening in the customer’s actual facilities.
We have a twofold product commitment to the Grinding Lab. One, we can develop processes for the customer and their specific application. Two, we can internally develop advanced new products that solve issues for customers before they are even known.
CDT’s customer service commitment includes the lab as well, inviting customers to reach out to us, to use our grinding lab to solve their grinding problems. Benefits to CDT customers include:
Faster product development
Cost savings/reduced risk
Opportunities to innovate
Valuable data
Remote product testing
Read more about these benefits here or watch clips of the Grinding Lab in action, and hear more about it from Jeff Wirth, our Engineering Manager in this video:
Why Superabrasives?
Superabrasive grinding wheels last longer, grind faster, cut cleaner, leave a better finish and create a sharper edge. The real question is—Why not?
When the material you are trying to process is either too hard or too delicate for conventional abrasives, custom superabrasive grinding tools might be the best solution.
What are Superabrasives?
The term “superabrasives” refers to a class of tools used in precision grinding for many industries. Superabrasive grinding products contain natural diamond, manmade diamond, and/or CBN — some of the hardest materials that can be made. Superabrasives are also sometimes called industrial diamonds: an industrial diamond is a non-gem quality small diamond that is for abrasives, cutting, and drilling tools. Other types of superabrasives include:
Cubic boron nitride (CBN): Usually called CBN, this is the second hardest cutting tool material after a diamond.
Polycrystalline: This is an abrasive material that has multiple collections of crystal grain structures with individual orientations.
CVD Diamond: These are synthetic diamonds made by a process known as chemical vapor deposition. CVD diamonds grow from a hydrocarbon gas mixture. They are extremely hard and have a high thermal conductivity that is five times that of copper. They also have broadband optical transparency, are chemically inert, and only reach graphitization at very high temperatures.
Nano-diamonds: These tiny diamonds are the product of a controlled explosion. They are sometimes called detonation nano-diamonds (DND) or an ultra-dispersed diamonds after how they are formed.
These abrasive materials have been labeled as superabrasive due to their extraordinary hardness, unparalleled performance, and longevity. Continental Diamond Tool uses these superabrasive materials to make custom grinding wheels and products, including plated, vitrified, resin bond, metal bond, hybrid bonds, and rotary dressers, for many complex applications.
Superabrasives vs. Conventional Abrasives
Superabrasives, whether natural or manmade, have a hardness range that distinguishes them as some of the most durable materials on Earth. Conventional abrasives are made with much softer abrasive materials that are less expensive but break down faster. The best abrasive product for your application depends on the material you are grinding and what properties you need to achieve your desired results.
Industries that Use Superabrasives
A great number of industries use superabrasive grinding wheels, and the custom-coated abrasives subsection of the abrasives industry continues to grow. Industries that regularly invest in superabrasive grinding wheels are:
Aerospace
Automotive
Medical
Electronics
Composites
Oil Industry
Advantages of Superabrasives
The advantages of superabrasive grinding wheels are more than extraordinary hardness, unparalleled performance, and longevity. These three features of superabrasives are the core of many advantages manufacturers gain by an aggregation of services that normal abrasives simply cannot deliver.
Benefits include:
Less expensive tooling and fixturing costs
More wheels on the spindle, smaller wheels, multiple operations
Less floor space needed for manufacturing
Virtual elimination of wheel wear
Automated CNC machines, less labor intensive operations requiring less training
Consistent surface speed from part to part
Better overall throughput with fewer machines needed
Improved material removal rates, lower per part abrasive costs, and higher speeds
With superabrasives, industries have been able to increase production with automated CNC equipment, compensating for a lack of available, skilled labor. With custom superabrasives that are optimized for their process, machine capabilities, and mechanization, there is less reliance on operator technique. A properly defined process, combined with automatic loaders, make for equipment that can even run itself in some cases with lights out manufacturing.
Industry Outlook
Future growth of the abrasives industries will primarily be in superabrasives. Currently, research and development of superabrasives are taking place in the following areas:
Custom designed “hard to grind” materials in an increasing number of industries
Creep or deep feed grinding
High-speed, high-performance grinding of hardened steel
Form grinding, sometimes with electroplating, in high precision, high-removal, and high-surface quality applications
CNC-control of line grinding machines
Continental Diamond Tool stays on the forefront of new abrasive technology developments in superabrasives with our state-of-the-art grinding lab focused on research and development of new hybrid bonds that take the efficiencies of superabrasives even further.
How to select the right superabrasive
CDT has a strong group of engineers, product managers, and technical sales people who can come out to your facility to review your equipment and processes, and the parts you’re looking to grind. Or, as Troy Giacherio, Product Manager for Rotary Dressers, suggests, “you can come into our facility and we’d be more than happy to have the conversation, review the whole development process, and then make our recommendations based on what we’ve seen and communicated.” Contact us for a free quote.
Learn more about superabrasive grinding solutions in this video:
How to Order Custom Grinding Wheels
Check out this guide on how to order custom grinding wheels that are a perfect fit for your operations.
Professionals in certain manufacturing industries use grinding wheels as a normal part of their abrasive cutting, grinding, and machining processes. There are numerous types of grinding wheels, as well as assorted types of abrasive materials and grains. Having and using the right tool for the job is essential, especially for precision manufacturing. It is important to determine what you need before you place an order or get a quote.
TYPES OF GRINDING WHEELS
These are only a few examples of numerous types of grinding wheels and their uses:
Centerless and feed wheels for creating extremely close tolerances on metal cylindrical parts, such as those for aircraft, automotive, and tool manufacturing
Cylindrical wheels for angular, plunge, and reverse grinding
Diamond and hybrid wheels for grinding extremely hard materials, such as carbide tips or concrete
Dish cup wheels for cutter and jig grinding
Mounted point wheels for deburring and profiling work on hard materials
Straight wheels, most commonly used for centerless, cylindrical, and surface grinding on bench and pedestal grinders
Tapered wheels for grinding gear teeth and threaded applications
TYPES OF ABRASIVES
Depending on the job you need to do and the type of grinding wheel you use, the type of abrasive you need varies. Examples of abrasives include:
Conventional: Aluminum Oxide (corundum), Ceramic, and Silicon Carbide
Superabrasive: Natural Diamond, Synthetic or Man Made Diamond, and Cubic Boron Nitride
At Continental Diamond Tool, we produce custom superabrasive grinding solutions. We can help you replace your conventional grinding wheel with the right superabrasive alternative.
ORDER GRINDING WHEELS
While some companies have local suppliers for their grinding wheels and abrasives, it's often more convenient to request a quote online, especially when you are looking to order custom grinding solutions. Here are the steps to take to order a custom grinding wheel:
Step 1
Determine the abrasive specifications required for the job. The proper grinding wheel is dependent on many factors including the grinder, coolant, material being ground, wheel dressing method, and more. To give you the best engineered solution for your grinding application, your supplier will need certain information to ensure you get the results you are looking for. Details you'll want to gather include:
Type of material: carbide, ceramics, concrete or stone, glass, or metal.
Type of grinder: manual or CNC
Type of grinding application: OD, ID, Cylindrical, Surface, Rotary Surface, Angle Head, Double Disc, Plunge, Traverse, etc.
Wheel diameter: varying from 0.008” to 40”
Thickness range: varying from 0.030” to 12”
Arbor hole size: varying from 0.040” to 20 inches
Desired finish: extra fine, fine, medium, or coarse (for minimal to heavy removal).
Coolant type
Dressing method & tools
Stock removal: If you know your selected abrasive material and required grit (varying from 20 to 8000 mesh), note that too.
Step 2
Call or use the online contact order form for your online supplier. For a custom grinding wheel, provide lots of detail about the type of tool you are using, along with its description, dimensions, and intended use. Continental Diamond Tool has a quote request form that walks you through the information we need to provide an accurate quote, and you can upload reference files if needed. Or you can always call us if you want to talk through the parameters of your project.
Step 3
At Continental Diamond Tool, we specialize in custom superabrasive grinding wheels and tools. Our team of engineers will work with you on a custom solution to your grinding needs. Depending on the nature of your project, we can run remote simulations or in-person trials and test prototypes before manufacturing the final piece. The whole process typically takes a number of weeks, but can be fast tracked if needed. At the end, our engineers will work with your team to guarantee that the grinding wheel is properly installed and performing as expected. They can also offer instruction on how to maintain your grinding wheel for ongoing high performance.
Stop getting by with a grinding wheel that isn’t optimized for the job. It's best to consult an expert to make sure your tool is a good fit for your process. In many cases, custom grinding wheels quickly pay for themselves with increased efficiency and extended tool life, and you'll see the difference to your company’s bottom line. It starts with calling 800-443-6629 or requesting a free quote online today:
CDT Launches New Website
Continental Diamond Tool is proud to announce the launch of a completely redesigned website. Check out the new features >
Continental Diamond Tool is proud to announce the launch of a completely redesigned website at cdtusa.net. The new website features expanded information about CDT products, an extensive searchable knowledge-base of articles, updated photos and videos, and a revamped mobile-friendly experience.
Pages about Metal Bond, Resin Bond, Vitrified, Plated, and Hybrid Bond grinding wheels, along with Stationary and Rotary Diamond Dressers have all been updated. We are also transitioning our downloads page to include interactive PDFs.
We hope you will check out our about section with updated historical photos that highlight our nearly 50 years in grinding wheel manufacturing and new photos of our team. We’ve also added a page about our efforts to support our local community. Customers can still find warranty, product safety, supplier terms, and a payment portal. Some major industry trade shows are coming up and you can find that information on our website, too!
Websites are a work in progress, and we will be continuously updating ours as we add new capabilities. Even as we launch this more robust site, we're already considering other features to make our service even more prompt, such as live chat, customer portal, and more. What information or functionality would you like to see? Let us know.
We look forward to sharing more great information about CDT grinding products and services and other resources for the manufacturing industries we serve. Follow us on Linked In, YouTube, Facebook or Instagram, and sign up for our mailing list for regular email updates about once a quarter.
As always, when your product application calls for a Diamond or CBN superabrasive wheel or tooling, you can contact our team and we'll be happy to assist you in any way. Enjoy!
Superabrasive Manufacturing: The Industries We Serve
Here’s a rundown of industries that are known to benefit from the toughness and precision of custom CBN and diamond grinding solutions through CDT. Check it out >
For industries that need to shape some of the world’s hardest substances like tungsten carbide, ceramics, and superalloys, only an extremely tough tool can do the job. Applications like these require grinding wheels and tools made with the most durable materials for cutting: natural or man-made diamond and cubic boron nitride (CBN).
Ironically, delicate substances like silicone also require the special characteristics that only these superabrasive materials can provide. With a wide variety of forms, grades, and bonds, CDT is proud to supply high-precision custom superabrasive grinding and finishing solutions for a variety of commercial, industrial, and military applications.
Here’s a rundown of industries that are known to benefit from the toughness and precision of custom CBN and diamond grinding solutions:
AEROSPACE & MILITARY
Top aircraft turbine manufacturers in the United States and around the world require precision plated form wheels and form mandrels in the manufacturing of turbine blades and other various engine parts. CBN grinding technology can be used for both the manufacturing of aircraft engine components and land-based turbine engine components. Efficient manufacturing needs shorter production runs and longer cycle times. Plated CBN wheels are the preferred choice for high precision form grinding applications of this nature.
CDT engineers are experienced with the demands of military and commercial aerospace applications, particularly in regard to turbine engine tooling and grinding solutions. We've even manufactured tooling for interplanetary use. As a leader in the manufacturing of diamond grinding tools for both air frame and aerostructure components, CDT is well-equipped to tackle this industry’s most challenging manufacturing needs.
For aerospace and military applications, superabrasive solutions are useful in working with:
Composites
Composite Material
Honeycomb Composites
Graphite & Kevlar
Reinforced Plastics
Titanium
AUTOMOTIVE
Over the years, CDT has proven to be a reliable partner to the automotive industry as a supplier of grinding tools for machining engine, chassis, and transmission components. We provide the continuous innovation, wide range of superabrasive capabilities, high quality standards, and delivery reliability that the automotive industry needs to stay competitive in an ever changing world.
The automotive industry uses superabrasive grinding products in the manufacture of many components such as:
Engines
Brakes
Steering, Suspension Systems
Parts
Rubber, Tires
Windshield Glass, Mirrors
Body Parts
CERAMICS
With extreme hardness that in some cases surpasses that of metals, the properties of ceramics offer unique opportunities and challenges for grinding in this industry. From circuit board parts, kitchenware, solar panels, pipes, and tubes to advanced technical ceramics and refractories, the ceramics industry manufactures a vast range of products that require the special characteristics of superabrasive wheels and tools. With our reputation for high precision diamond grinding wheels that work longer, cut faster, and are more durable, leaders in the ceramics industry regularly turn to CDT engineers to help them achieve their most demanding grinding and finishing requirements.
The ceramics industry uses superabrasive tools for the grinding and finishing of:
Glass
Brick, Refactories
Ceramics
Carbon, Graphite
Lavatory
Alumina
COMPOSITES, FIBERGLASS & PLASTICS
CDT has an electroplated process that is specially formulated for composites and provides outstanding cutting speed and efficiency. Our engineering team specializes in helping our customers create successful, cost effective solutions for their manufacturing needs. This applies to all types of composites, from FRP to fiberglass to Kevlar® aramid fiber. CDT's electroplated wheels have seen great success in all areas where composites are used, including: automotive, aerospace, sporting equipment (golf clubs, archery, bicycles, etc), wind energy, and military applications.
Many industries turn to superabrasive solutions when manufacturing requires these composite and fiber-reinforced plastic materials:
FRP Corrosive Resistant Material
Marine Fiberglass
Cultured Marble Types
Thermoset Resin Materials
Fiberglass Reinforced Plastics (FRP)
Composites
CUTTING TOOLS
For those companies involved in the manufacturing or resharpening of cutting tools, superabrasives have the strength and durability that such metal manipulation requires. Superabrasive tools that are custom designed to the required specs can reduce the cost per part, meet high-precision quality standards, and provide superior value.
Our engineering department has much experience achieving tighter tolerances and better performance, even with this industry’s extremely tough materials. A well designed custom grinding wheel can take a company to the next level, increasing efficiency while saving resources and time.
For the cutting tools industry, superabrasive tools are superior at grinding and finishing metals such as:
Carbide
High Speed Steel
FOOD PROCESSING, PAPER & CARDBOARD
Manufacturers of cutlery and hand tools turn to CDT superabrasives for many grinding applications. Cool cutting, fast stock removal, excellent finish, superior wheel life, and an attractive return-on-investment are prerequisites for success in the demanding grinding required in food processing and paper/cardboard.
Industries involving food processing, paper, and cardboard use superabrasive grinding products in applications such as:
Blade & Knife Sharpening
GEM
Precious Stone
Semi-Precious Stone
Corrugated & Flat Cutters
GEARS
CDT is a partner to the gear industry. Our areas of expertise include grinding wheels for virtually every operation needed in the production of gears and gear components. More broadly, our custom engineering department helps companies develop products that will maintain and improve production efficiencies on a continuous basis for whatever the customer’s need.
The gear industry uses superabrasive tools in the manufacture of:
Gear, Thread
Gear Guide, Bed
MEDICAL/DENTAL
From bone sawing to intravascular applications, CDT is regularly commissioned to engineer high precision tools for medical use. Our engineers understand the thorough testing and quality processes associated with medical device manufacturing . Our products are designed with exacting standards to achieve the tight tolerance demanded by this industry.
Medical and dental industry uses for superabrasive tooling include:
Prosthesis
Dental Instruments
Surgical Equipment
OIL & GAS
When the oil and gas industry has a job that calls for high precision grinding of carbide and PCD drill bits, wear parts, and gage blocks for oil and gas drill manufacturing, efficiency and effectiveness are extremely important. ID grinding is an exacting process that requires unparalleled precision for reliable, repeatable results. And, this industry’s CNC OD Grinders have their own unique challenges in these most difficult center-type grinding projects.
CDT has developed superabrasive advanced bond technology perfectly suited to all these needs of the oil industry. We also custom engineer each tool for longer tool life and a high stock removal, making it the best value in the industry.
The oil and gas industry turns to superabrasive tools for:
PCD/Carbide Grinding
I.D. / O.D. Grinding
POWER GENERATION
CDT has the capability to produce thousands of precision-built superabrasive products of high quality, performance, and repeatability for virtually every conceivable manufacturing area involved in power generation. The diversity in this industry calls for Vitrified, Resin Bond, Plated, and Metal Bond Diamond and CBN products to get the job done.
For the power generation industry, superabrasive tools are most commonly used in the manufacture of:
Wind Turbine
Gas & Steam Turbine
Marine Turbine
Blades
WOOD/SAW
CDT is experienced at supplying custom superabrasive products for the lumber and wood products industry. We provide grinding solutions for OEM manufacturers, filing rooms and service shops for their processes of manufacturing and maintaining band saws, circular saws, chippers, planers, and paper knives. All in all, our grinding wheels are designed to help our customers maintain and improve production efficiencies on a continuous basis.
Industry leaders in lumber and wood products use superabrasive tools for applications such as:
Carbide Tip Saw Blades
Band Saws
Knife Sharpening
OTHER MARKETS
Continental Diamond Tool has been providing technically superior precision tooling solutions to numerous other distinct industries since 1973. Over the years, we have witnessed more and more companies realize the productivity increases possible with the use of custom superabrasive products. With more parts processed per wheel and fewer wheel changes, many see how investing in this level of quality and durability pays off.
Along with those highlighted above, below are additional industries who have turned to CDT for superabrasive grinding solutions:
ELECTRONICS
Ferrites, Magnetics
Substrate (Ceramics, Glass, IC)
Quartz Crystal
Semiconductors
Printed Circuit Boards
OPTIC & PRECISION
Lens, Prism
Measuring Instruments
STONE
Lapidary Tools
Refractory Brick
Peek Materials
Granite
TOOL & DIE
Cemented Carbide Tool & Die
Special Steel Tool
Molding Die
Bearing
Pneumatic, Hydraulic, Valve
Jig
WIRE & CABLE
Precision Die
Top 10 Reasons to Work Third Shift at CDT
From longer weekends to higher pay, check out the top ten reasons you should apply for a third shift position at CDT.
Here at Continental Diamond Tool, we take our work seriously, but that doesn’t mean we don’t have a sense of humor! Whether you think of third shift as a “late shift” or a “late show,” there are lots of great reasons to work nights at CDT.
From longer weekends to higher pay, watch the video below to see the top ten reasons you should apply for third shift at CDT.
Drumroll please…..
6 Common Grinding Problems and How to Solve Them
We discuss six common grinding problems and offer solutions to help you solve some of your most challenging grinding issues. Check it out >
Most grinding problems affect one of two categories: either appearance of the workpiece or productivity and return on investment. After verifying that the grinding machine isn’t at fault, there is one likely culprit causing your grinding problems: your grinding wheel.
Poor surface finish, chatter, and burning all affect the appearance of your product. Productivity issues like short wheel life, slow or inefficient cutting, or the wheel not cutting at all are also costly problems to have.
Let’s take these one at a time to see how a fix to your grinding wheel can solve some of your most challenging grinding issues.
1) POOR SURFACE FINISH
WHY YOUR GRINDING WHEEL MAY BE AT FAULT:
In the appearance category, poor finish is a common complaint when your grinding wheel isn’t optimized. Grinding is a multi-point cutting process, but broken down to the microscopic level, it has similarities to a single point operation like turning. Viewed this way, it’s easy to see how surface finish is affected by the same factors: the more material removed by each grinding point, the bigger the individual chips and the rougher the surface.
SOLUTIONS:
Select a grinding wheel with a finer grit size
Reduce the relative speed between the wheel and workpiece
OTHER POSSIBILITIES:
If grinding wet, the coolant may not be efficiently removing chips from the workpiece or wheel interface.
It's also possible that the wheel is being dressed excessively, creating grinding points that are standing too proud of the wheel surface.
2) CHATTER
WHY YOUR GRINDING WHEEL MAY BE AT FAULT:
Recognizable by a distinct, often audible, pattern on the workpiece, chatter has many causes. Wheel-induced chatter occurs when an out-of-true grinding wheel acts as an excitation source.
SOLUTIONS:
In this case the wheel should be trued carefully.
Also check that it isn’t slipping on its mount.
OTHER POSSIBILITIES:
If the problem is tracked down to a vibration in the machine — possibly some kind of resonance — the solution is to vary the grinding speed. Try going 10% faster or slower to remove the forcing excitation.
A detailed discussion of chatter is available at the Abrasive Engineering Society website.
3) BURNING
WHY YOUR GRINDING WHEEL MAY BE AT FAULT:
Machinists use the term “burning” to describe thermal damage. It can show up as cosmetic discoloration, changes in workpiece hardness, and possibly distortion-inducing internal tensile stresses. Burning can occur if the wheel is glazed or loaded, causing more rubbing and friction. This often occurs if the machinist is trying to push the wheel through the workpiece too quickly or using a wheel that’s too durable.
SOLUTIONS:
Dress the wheel with the correct dressing tool
Reduce the feed rate or the relative velocity between wheel and workpiece.
OTHER POSSIBILITIES:
Burning is far more common when grinding dry, although can still be experienced in wet grinding if there isn't enough coolant flow to carry away the heat.
See “Burn Awareness”, originally published in Cutting Tool Engineering, December 2000, for more information.
4) WHEEL LIFE TOO SHORT
WHY YOUR GRINDING WHEEL MAY BE AT FAULT:
This costly issue can be caused by a wheel that's either too hard or too soft for the workpiece. When this is the case, the grinding wheel loads up or wears away too quickly.
SOLUTIONS:
Try a grinding wheel manufactured with a different material that is better suited for your grinding operation.
OTHER POSSIBILITIES:
Insufficient coolant
Dressing your grinding wheel too frequently
Wheel speed too low
5) WHEEL CUTTING SLOWLY
WHY YOUR GRINDING WHEEL MAY BE AT FAULT:
This productivity issue is usually caused by feeds and/or wheel speeds that are too low. If you are using the wrong type of grinding wheel, you may be forced to cut slowly to avoid burning, but ultimately that’s not efficient for your process.
SOLUTION:
The solution is to find a wheel that can grind as fast as possible without burning. A grinding wheel specialists can suggest alternatives that will increase speed for your specific operation.
6) WHEEL NOT CUTTING AT ALL
WHY YOUR GRINDING WHEEL MAY BE AT FAULT:
Most likely, this happen when the grinding wheel is glazed by truing.
SOLUTION:
The solution is to dress the wheel lightly until the grit opens up. For dressing advice, consult with a grinding specialist.
OUR BEST ADVICE
THINK LOGICALLY
Most grinding problems can be solved by tracing the fault back to basic principles. With all grinding applications, imagine your material being removed by individual cutting points. Thinking from this perspective, a solution usually emerges.
Also, use your resources. The grinding experts at CDT are happy to discuss your cutting and grinding issues and offer solutions that will set your manufacturing operations on track to success.
CDT Expands with New Third Shift Positions
Keeping up with increasing demand, Continental Diamond Tool is expanding third shift to some of their other departments at their primary manufacturing facility in New Haven, Indiana. Learn more >
o keep up with increasing demand, Continental Diamond Tool is expanding third shift at their primary manufacturing facility in New Haven, Indiana. CDT first started offering third shift positions in their resin department in late 2021. With success there, CDT is now making moves to build third shifts for their metal bond and vitrified departments as well.
What It’s Like to Work Third Shift at CDT
Kyle Hockemeyer, is CDT's third shift lead in the resin department. He works closely with his team to make sure the work goes smoothly and efficiently overnight. That also means hiring the kind of employees who show initiative and drive.
“With third shift, we’re looking for go-getters, self-starters, who get things going when they get here. There’s benefits to that,” he says in this video interview. Third shift regularly enjoys long weekends, with scheduled hours Monday through Thursday 8:00 pm to 6:00 am. There is also a $1.50/hr. shift premium and opportunities for overtime. Check out this video with Kyle to learn more about what it’s like to work CDT’s third shift:
Be a Part of Building This New Third Shift!
CDT currently has openings for a number of entry-level, full-time third shift positions. If you have that winning combination of “night owl” and “self-starter” and would like to join a team with similar goals, we invite you to apply to a third shift position at CDT.
CDT Grinding Lab Featured in Case Study by United Grinding
Learn about the process of acquiring the Walter, and our relationship with United Grinding. >
For many years, we planned to build an in-house R&D grinding lab, to allow us to develop new products and improve existing lines with real data and testing.
When COVID hit, we seized the opportunity to take advantage of global slowdown to expand in this new direction. After extensive research and assessment of future needs, we landed on the Walter Helitronic Power 400 for its versatility, as well as its stability and dependability, and United Grinding’s stellar reputation, service, and support.
With the Walter equipment, we are able to address customer requirements such as shorter cycle times, and keeping up with rapidly changing market conditions.
This forward thinking has been critical for post-pandemic market growth, at a time when other companies have scaled back instead.
Read more about the process of acquiring the Walter, and our relationship with United Grinding.