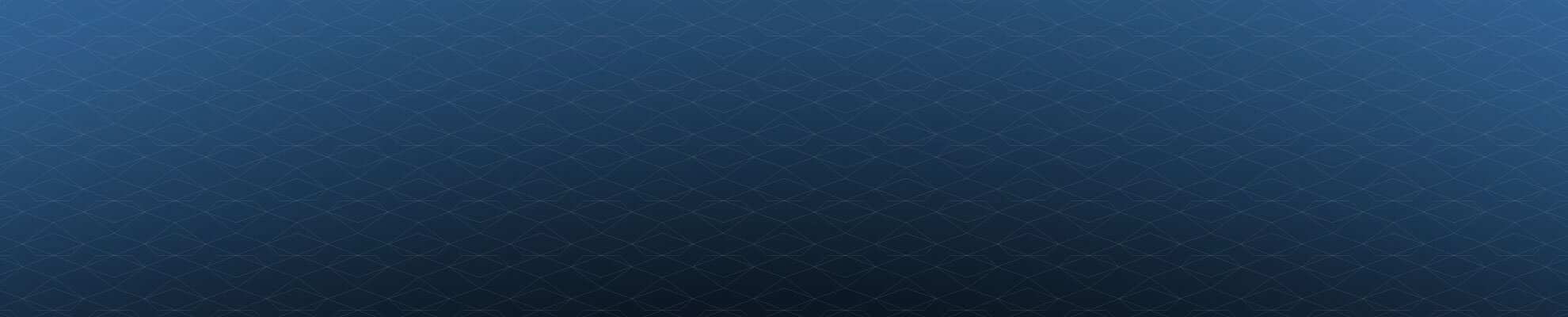
News and Resources
Browse by Category
Browse by Product
- All Dressing Products
- All Grinding Products
- CBN-Diamond Superabrasives
- Conventional Abrasives
- Diamond Lapping Compounds
- Diamond Rotary Dressers
- Diamond Stationary Dressers
- Hybrid Bond Grinding Tools
- Metal Bond Grinding Tools
- Plated Grinding Tools
- Resin Bond Grinding Tools
- Vitrified Bond Grinding Tools
Custom Rotary Diamond Dressers in as little as 4 weeks: How do we do it?
Industry-standard lead times for diamond rolls can take 8 weeks or more. If you are looking for a better, faster rotary diamond dresser alternative, we can expedite service in as little as 4 weeks. Learn how >
Since 1984, Consort Precision Diamond has supplied diamond wheel dressing products to a broad range of industries including aerospace, aircraft, automotive, blade and knife, power generation, medical, cutting tools, tool & die, saw, gear, and bearing and many other applications. What all these grinding operations have in common is that they typically require some form of wheel dressing to re-establish the wheel profile and/or recondition the wheel face.
About Wheel Dressing or Conditioning
Wheel conditioning involves the sharpening and opening of the wheel face, while also removing dull abrasives, excessive bond, and workpiece material (loading). A sharp and open wheel face will allow maximum possible material-removal rates and reduced thermal stress on the workpiece.
Consort’s rotary dressers provide the ideal profile for your desired wheel topography, with superior materials and manufacturing technology. Because your dresser is custom manufactured, demanding and complex configurations are possible.
Diamond Roll Delivery in as Little as 4 Weeks
The question then turns to delivery and lead times. In business, time is money. Industry-standard lead times for custom rotary diamond dressers can take 8 weeks or more. That’s a long time to wait for a critical part in your manufacturing process. Consort has made a reputation for fast delivery with a standard lead time of 6-8 weeks.
Need a tool in a hurry? Customers can request “Expedited Service” for custom diamond roll delivery in as little as 4 weeks. With manufacturing, delaying maintenance can really add to your costs in the long run. When a job is expedited, we work with our customers to get them their tooling as soon as possible.
We pride ourselves on prompt service and communication. At any time, you can reach out to your Consort account representative to begin an order or find out its status. If you do not have an account rep, please reach out to our customer service through our website online form or call 800-443-6629.
Lead times should not be a hurdle in the proper maintenance of your grinding equipment. If you are looking for a better, faster diamond roll supplier, let our service techs help you get the process started.
6 Common Grinding Problems and How to Solve Them
Are you experiencing these 6 common grinding problems? If so, your grinding wheel may be at fault. Learn more >
Most grinding problems affect one of two categories: either appearance of the workpiece or productivity and return on investment. After verifying that the grinding machine isn’t at fault, there is one likely culprit causing your grinding problems: your grinding wheel.
Poor surface finish, chatter, and burning all affect the appearance of your product. Productivity issues like short wheel life, slow or inefficient cutting, or the wheel not cutting at all are also costly problems to have.
Let’s take these one at a time to see how a fix to your grinding wheel can solve some of your most challenging grinding issues.
1) Poor surface finish
Why your grinding wheel may be at fault:
In the appearance category, poor finish is a common complaint when your grinding wheel isn’t optimized. Grinding is a multi-point cutting process, but broken down to the microscopic level, it has similarities to a single point operation like turning. Viewed this way, it’s easy to see how surface finish is affected by the same factors: the more material removed by each grinding point, the bigger the individual chips and the rougher the surface.
Solutions:
Select a grinding wheel with a finer grit size
Reduce the relative speed between the wheel and workpiece
Other possibilities:
If grinding wet, the coolant may not be efficiently removing chips from the workpiece or wheel interface.
It's also possible that the wheel is being dressed excessively, creating grinding points that are standing too proud of the wheel surface.
2) Chatter
Why your grinding wheel may be at fault:
Recognizable by a distinct, often audible, pattern on the workpiece, chatter has many causes. Wheel-induced chatter occurs when an out-of-true grinding wheel acts as an excitation source.
Solutions:
In this case the wheel should be trued carefully.
Also check that it isn’t slipping on its mount.
Other possibilities:
If the problem is tracked down to a vibration in the machine — possibly some kind of resonance — the solution is to vary the grinding speed. Try going 10% faster or slower to remove the forcing excitation.
A detailed discussion of chatter is available at the Abrasive Engineering Society website.
3) Burning
Why your grinding wheel may be at fault:
Machinists use the term “burning” to describe thermal damage. It can show up as cosmetic discoloration, changes in workpiece hardness, and possibly distortion-inducing internal tensile stresses. Burning can occur if the wheel is glazed or loaded, causing more rubbing and friction. This often occurs if the machinist is trying to push the wheel through the workpiece too quickly or using a wheel that’s too durable.
Solutions:
Dress the wheel with the correct dressing tool
Reduce the feed rate or the relative velocity between wheel and workpiece.
Other possibilities:
Burning is far more common when grinding dry, although can still be experienced in wet grinding if there isn't enough coolant flow to carry away the heat.
See “Burn Awareness”, originally published in Cutting Tool Engineering, December 2000, for more information.
4) Wheel life too short
Why your grinding wheel may be at fault:
This costly issue can be caused by a wheel that's either too hard or too soft for the workpiece. When this is the case, the grinding wheel loads up or wears away too quickly.
Solutions:
Try a grinding wheel manufactured with a different material that is better suited for your grinding operation.
Other possibilities:
Insufficient coolant
Dressing your grinding wheel too frequently
Wheel speed too low
5) Wheel cutting slowly
Why your grinding wheel may be at fault:
This productivity issue is usually caused by feeds and/or wheel speeds that are too low. If you are using the wrong type of grinding wheel, you may be forced to cut slowly to avoid burning, but ultimately that’s not efficient for your process.
Solution:
The solution is to find a wheel that can grind as fast as possible without burning. A grinding wheel specialists can suggest alternatives that will increase speed for your specific operation.
6) Wheel not cutting at all
Why your grinding wheel may be at fault:
Most likely, this happen when the grinding wheel is glazed by truing.
Solution:
The solution is to dress the wheel lightly until the grit opens up. For dressing advice, consult with a grinding specialist.
OUR BEST ADVICE: THINK LOGICALLY
Most grinding problems can be solved by tracing the fault back to basic principles. With all grinding applications, imagine your material being removed by individual cutting points. Thinking from this perspective, a solution usually emerges.
Also, use your resources. The grinding experts at CDT are happy to discuss your cutting and grinding issues and offer solutions that will set your manufacturing operations on track to success.
The Hardest Materials Just Became EASY
Customers report significant improvements to the grinding process and cost savings with CDT’s latest generation of Vitrified Diamond grinding wheels. Learn more »
Have you struggled to grind hard materials such as Silicon Carbide, Aluminum Oxide, Glass, Carbide, and others? With these substances, it has always been difficult to improve cycle times and reduce chipping and scrap ... until now.
Significant Gains in Grinding Performance
CDT’s latest generation of Vitrified Diamond grinding wheels combines high bond strength with porosity levels that significantly improve the grinding process. Better yet, this wheel is optimized for grinding hard, problematic materials such as Silicon Carbide, Ceramics, CMC, PCD, and more. With our VIPER™ Bond Technology, customers have reported significant improvements to the grinding process and cost savings.
*Vitrified Diamond grinding wheels with the new VIPER™ Bond Technology have been found to reduce cycle times up to 70% when compared with conventional resin bond grinding processes. Cycle times were reduced 30% or more when compared with other vitrified grinding products.
The Science Behind VIPER™ Bond Technology
Vitrified Diamond grinding wheels already take the hardest known superabrasives held mechanically and chemically in a ceramic bond to form some of the most efficient grinding products available on the market. Our custom-engineered wheels use varying concentrations, porosity levels, and bond hardness to optimize performance specific to your grinding process. The payoff? Vitrified—Improved—Performance
"With this new bond we saw cycle time reductions of 20% or more and the same amount of wear compared to our first generation vitrified wheel, which was already a vast improvement over a conventional wheel."
— Jim Elliott, Advanced Carbide
If you thought you knew what to expect from your Vitrified Diamond grinding wheel, it may be time to take another look. Contact us today to see how VIPER™ Bond Technology might improve your tool's performance.
Diamond or CBN?
Having decided to leave conventional grinding wheels in favor of superabrasives, buyers are confronted with a difficult choice between diamond or CBN grit.
Having decided to leave conventional grinding wheels in favor of superabrasives, buyers are confronted with a difficult choice: diamond or CBN abrasive?
Both are extremely hard and offer the potential for greatly improved grinding productivity, but there are differences between the two. It's important to understand these and match the abrasive to the task if peak productivity, and lowest cost-per-piece are to be achieved.
A CHEMISTRY LESSON
Diamond is a crystalline form of carbon. Under heat and pressure carbon atoms link with adjacent atoms to create the hardest known material. This makes it an ideal cutting tool, or would do but for it's rarity and price. However, in the mid 20th century scientists figured out how to manufacture diamond, and today most diamond grit used in superabrasive grinding wheels is man-made.
Unlike diamond, cubic boron nitride (CBN) doesn't exist in nature and is synthesized from boron and nitrogen. When chemically bound together these two elements behave much like carbon in that they can create an immensely strong crystal lattice structure. Of the two, diamond is considerably harder at room temperature, (knoop hardness around 7,500 versus the 4,500 of CBN,) but CBN has better thermal and chemical stability, remaining inert at temperatures up to 1,000 oC, versus the 800 oC at which diamond begins to degrade.
CHEMISTRY DETERMINES APPLICATIONS
As the harder of the two, diamond is preferred for shaping extremely hard workpiece materials such as ceramics, carbides, stone and glass. It is not however suitable for use with steels. This is because carbon and iron have a strong affinity for one another, especially at elevated temperatures. This results in rapid erosion of the diamond grit, quickly destroying the grinding wheel.
CBN is better suited to grinding applications that generate high temperatures, meaning it can be used at higher speeds. And it's unreactive nature makes it the preferred choice for grinding most steels, such as tool steel and HSS.
IMPACT ON WHEEL CONSTRUCTION
The relatively low thermal limit of diamond also affects the type of wheel construction it can be used in. Vitrified wheels are made by firing a clay mix at very high temperatures: if the mix includes a proportion of diamond grit the firing temperature must be kept below 800 oC otherwise the diamond will start to react. For this reason, CBN is more common in vitrified grinding wheels.
TAKEAWAY
Use diamond on the hardest workpiece materials, but don't let it get too hot. Use CBN on ferrous workpiece materials to avoid the chemical reaction that will quickly wear diamond.
Diamond or CBN Grit with your Vitrified Grinding Wheel?
Each type of bond, vitrified, resin, metal or plated, has distinct performance characteristics. Learn about the choice between diamond and CBN as it relates to vitrified grinding wheels.
WHY USE A VITRIFIED GRINDING WHEEL
With a very hard and porous structure, vitrified grinding wheels are a popular choice amongst high productivity applications due to the great chip clearance and excellent coolant delivery. This type of grinding wheel has an extremely low wear rate and results in a high ratio of stock removal to wheel usage. The enhanced ability to dress a vitrified wheel allows for a larger layer depth with continual renewing of the grinding layer. The customization of this type of grinding wheels allows for the wheel to meet a wide range of customer applications, using either diamond or CBN as the abrasive.
Compared to other product lines, the structure of a vitrified grinding wheel allows for no deflection as the wheel feeds into part. As the grit starts to take chips of material out of the part, the finished piece size is strongly controlled and an enhanced surface finish from any customer’s requirements. Vitrified wheels do not need to run as fast as other products in the industry and coupling that with the ability to flow coolant through the open structure, results in less heat generated and minimal thermal damage to the workpiece.
REASONS FOR AND AGAINST DIAMOND GRIT TYPE
With its exceptional hardness due to the symmetry of its structure, diamond seems the obvious choice for every grinding wheel operation. However, there are limitations on where diamond can be used in applications as it has a strong affinity for iron and hardened steel. Diamond is a pure crystal of pure carbon, and the carbon and iron molecules like to interact and bond when the heat is generated during a grind. As a result, this can potentially cause issues with the workpiece as well as increases the wear of the grinding wheel.
ARGUMENTS FOR AND AGAINST CBN
In the application where diamond cannot be used, cubic boron nitride (CBN) is the next best alternative. The two big strengths are its ability to cut at extremely high temperatures and refusal to react with iron and other hardened steels when grinding. This makes CBN ideal when grinding tools and high-speed steels. The biggest downside to CBN is that the structure is not nearly as hard as diamond, and as a result, this grit type must run at a higher speed to be able to reach the same cutting abilities as a vitrified diamond grinding. Overall, both vitrified diamond & CBN wheels are available for a wide range of applications and can yield great results on a workpiece for a customer.
Advantages of Metal Bond Grinding Wheels
Every superabrasive grinding wheel consists of diamond or CBN grit held in a supporting matrix material known as the bond. The main bonding systems are resin, vitrified, plated, and metal. Of these, metal bond grinding wheels are perhaps the best known thanks to their overall utility and the length of time they've been available.
Every superabrasive grinding wheel consists of diamond or CBN grit held in a supporting matrix material known as the “bond.” The main bonding systems are resin, vitrified, plated, and metal. Of these, metal bond grinding wheels are perhaps the best known thanks to their overall utility and the length of time they've been available.
CONSTRUCTION AND MANUFACTURE
Metal bond grinding wheels start life as a superabrasive grit mixed with a metal powder. Most often this is bronze, although other metals such as iron and nickel are sometimes used. The mixture is distributed evenly around the periphery of a metal grinding wheel form, then placed in an oven and heated to around 1,4000F (7600C.) At these temperatures the metal grains begin to melt and diffuse into one another. This creates a dense matrix that locks the abrasive grit in place more tightly than in resin or vitreous bond wheels.
STRENGTHS AND WEAKNESSES
The metal bond wheel structure offers a number of advantages.
Metal bond grinding wheels last longer than those made by other methods. This boosts productivity by cutting down on dressing frequency and wheel changes.
Complex forms can be created, and since wear rates are low they last longer than in other types of wheel.
The metal structure is impervious to attack by alkaline coolants, (unlike resin grinding wheels which are susceptible to chemical attack, especially at elevated temperatures,) so is well-suited to use with grinding fluids.
Has excellent impact resistance, (unlike a vitrified wheel,) thanks to the metal wheel form, so stands up well in interrupted cut applications.
Heat is quickly dissipated through the metal core. This makes it appropriate for high material removal rate operations like creep feed grinding, (which are also helped by the ability to use coolant.)
One weakness to be aware of with metal bonded grinding wheels is that they are not easily dressed. Unlike resin and vitrified wheels, the bond material can't be cut away to release dull grit and expose new edges.
MANY APPLICATIONS
Metal bond grinding wheels can be used on a range of materials such as carbides and tool steels. However, their main application areas are those where coolant is needed to remove heat and chips, such as grinding or cutting glass, ceramics, granite, stone and concrete. They are usually recognizable by the presence of the metal core, but the 'M' at the end of the wheel identification code should remove any doubt.
The main advantage of these wheels is their long life/low maintenance nature. This makes them ideal for use when productivity concerns are paramount. Their ability to dissipate heat and work with coolant means they are useful in situations where interface temperatures become high enough to cause burning or size control problems. They are particularly useful in creep feed and internal grinding and also find use in grinding complex forms as the shape is maintained over the course of a long production run.
SEEK ADVICE
Purchasing diamond or CBN grinding wheels is a significant investment, so it's important to select the type of construction most appropriate to the intended application. Metal bond grinding wheels are perhaps the best known type but it may be worth seeking advice from specialists at CDT before ordering.
Diamond Lapping Compounds
CDT lapping and polishing compounds are excellent for mold, die, and tool polishing.
CDT lapping and polishing compounds are excellent for mold, die, and tool polishing. These compounds also provide superior results when polishing to final tolerance of ceramic parts, tool-room use, and many other high finish and tight tolerance performance applications.
Diamond is the hardest and the most abrasive-resistant material used in nearly every type of industry. Our diamond lapping compounds use these unique characteristics to improve your finishing capabilities. You may choose to add diamond powders to the polishing paste in some instances.
Whether your job calls for high stock removal, fast polishing times, or superior finishes, you can find a compound that will help you achieve better results and a mirror finish. Both water and oil soluble compound are available in 5 and 18 gram syringes. Our syringes are disposable plastic dispensers that are convenient and safe from outside impurities.
Key features and benefits include:
Faster cut rates
High surface finish
Excellent surface tension
Quality viscosity
Low evaporation rate
Key adhesion to tools and surfaces
Easily cleans surfaces with both water and oil
Customers often ask what grit do we use for mold, die, and tool polishing? Our engineers are happy to assist you in finding the best compound for your specific application: 800-443-6629.
Since 1973, CDT has lead the field in providing technically superior precision tooling solutions to numerous industries. If you need rapid, accurate lapping, polishing and super-finishing, contact our technical team to learn more about our diamond lapping compounds.
Precision Finishing With Diamond Lapping Compounds
In many applications the finish resulting from grinding is good enough. When it isn't, the next step is lapping. As with grinding, diamond makes an excellent abrasive, but for best results needs to be selected and used appropriately.
A good quality grinding wheel on a rigid machine can produce a surface with a roughness around 0.25 microns Ra. In some applications this isn't enough; in others flatness is of greater importance than finish. In either situation the next step is to move on to lapping.
PRECISION FINISHING
In lapping an abrasive compound, composed of abrasive particles in a liquid or paste transport medium, is placed between the work piece and a lapping plate. Movement of the plate rolls the particles across the surface, removing raised peaks and flattening high regions. Depending on the work piece material, roughness numbers of under 0.30 microns Ra are achievable.
Other reasons for lapping are to bring something down to a precise and uniform final size and to produce a very flat surface. (Think of flatness as the rolling of hills and valleys, while roughness is the furrows plowed in the field.) Lapping doesn't put any stress or heat into the surface, and the low cutting forces make it a distortion-free way of finishing thin-wall parts.
LAPPING WITH DIAMOND COMPOUNDS
A number of abrasives can be used but diamond has several advantages:
highest material removal rates, by virtue of it's exceptional hardness
excellent surface finish, because the edges cut cleanly and diamond can be graded down to micron-level. (Producing a uniform, scratch-free surface demands particles of the same size: any that are larger will produce undesirable scratches.)
When lapping, standard practice is to use a cast iron lapping plate. For lapping with superabrasives (diamond or CBN) though it's recommended to use a composite metal plate such as tin, copper or cast iron.
The transport medium used in a diamond lapping compound can be either oil or water soluble. Oil soluble compounds are the most common and can be used on ceramics, carbides, cast iron and other metal surfaces.
A water soluble compound is used when the work piece is sensitive to oil. It's often employed for finishing electronic and electro-optical components and is widely used for magnetic read/write heads and semiconductor applications.
Companies like CDT supply precisely graded diamond lapping compound in syringes for easy dispensing. The coarsest grades, in the region of 40 to 90 microns, gives rapid stock removal while smaller particle sizes are used for finishing. To give one example, an application like preparing metallographic samples needs abrasives of less than two microns in size.
CHOOSE YOUR DIAMONDS CAREFULLY
In many applications the finish resulting from grinding is good enough. When it isn't, the next step is lapping. As with grinding, diamond makes an excellent abrasive, but for best results needs to be selected and used appropriately.
Understand Dresser Options To Cut Costs
Dressing is at the heart of a simple process: Use a diamond to expose fresh grit on the grinding wheel to extend its life. Yet there are dozens of different dressing tools — learn which to choose.
If you look at “Dressers “ or “Diamond Rolls” on the CDT website, it reveals several different types. Dressing is at the heart of a simple process: Use a diamond to expose fresh grit on the grinding wheel, so why so many tool options?
Focus on cost per piece
Stopping to sharpen the wheel means lost production, so it’s tempting to dress infrequently and to do it as fast as possible. Most shops know that’s a mistake, so they look for other routes to cut costs.
For some that means buying the cheapest single point dressers they can find. That’s often false economy. Instead they should try to minimize the dressing cost per work piece. That might mean buying better quality or more sophisticated dressers, which is why so many different types are offered.
Single point
The single point diamond dresser is the workhorse of grinding. It works in practically every application but is especially effective on straight wheels and for creating simple profiles. Special variants of the single point dresser are used for thread forms.
Diamonds aren’t cheap though, especially the better quality ones that better resist microcracking, so it’s important to get as much life from the dresser as possible. That means rotating the diamond regularly and changing the face exposed to the wheel to even out the wear.
Some diamond dressers are resettable, meaning the diamond can be reoriented to expose a fresh point. That adds to the cost but can mean an overall saving when compared with nonresettable dressers that are effectively throwaway items.
Multipoint dressers
In multipoint dressers, several diamond points work together to dress the grinding wheel. They work well for straight pass grinding on larger OD wheels as well as surface and centerless wheels.
A special form of the multipoint dresser is the donut cluster. These consist of a large number of diamonds set in a large crown. Good for dressing large wheels quickly, they are especially recommended for use on cylindrical grinders.
Grit dresser tools
Continuing the progression toward more dressing points, these tools use a diamond grit rather than discrete diamonds. These are long-lasting and allow for rapid dressing, making them very cost effective.
Blade dressers
Similar to a chisel in appearance, these present a line of diamond to the wheel. While they work for straight dressing, it’s more common to use them for profiles. Blade dressers come in both fixed and swivel head geometries for additional versatility.
Rotary diamond dressers
Rotary Diamond Dressers are a highly efficient and cost effective means of dressing and truing grinding wheels. Their use in achieving accurate correct form, tolerance, and condition is rapidly growing in the automotive, aerospace, power generation, machine tool and precision engineering component manufacturing.
Not an easy choice
There are several routes to minimize dressing cost per work piece and even for experienced machinists, it’s not always obvious which to take. That’s why it’s advisable to consult with experts to determine the best type of dresser for your application.
Grind Quickly And Accurately With A Vitrified Superabrasive Wheel
When high material removal and dimensional control is a concern, a vitrified wheel should be the first choice. Learn more benefits of a vitrified wheel >
High material removal rates demand a lot from the workpiece-machine-wheel system. Everything deflects under the high loads, making it difficult to achieve precise control over finished workpiece dimensions.
To combat this grinding machine manufacturers engineer-in as much rigidity as possible, but the wheel has a part to play as well. Resin-bonded wheels tend to “give” slightly under load, making it hard to meet tight tolerances whereas vitrified wheels provide much higher stiffness. This is because the Vitrified wheel is essentially composed of abrasive bound in a ceramic bond that doesn’t deflect as it contacts the workpiece, so size control is better.
VITRIFICATION BENEFITS
A vitrified superabrasive wheel begins life as Diamond or CBN grit incorporated into a specialized ceramic bond. After being formed to the required wheel shape this goes into a kiln where it’s fired at high temperature to fuse the abrasive to the bond. The superabrasive is both mechanically and chemically held.
This provides five other benefits in addition to stiffness:
Low wear rates
Thermal stability – which helps size control
Open structure enables coolant delivery to the grinding zone, keeping interface temperatures down
Oils and other fluids have no effect on wheel integrity
Dress-able, allowing precise forms and extending life
APPLICATIONS
Vitrified superabrasive wheels have a much longer life than conventional Silicon Carbide or Aluminum Oxide grinding wheels and provide exceptionally rapid material removal. This makes them attractive for high volume applications where cycle time and downtime must be minimized.
Vitrified diamond wheels are ideal for grinding PCD cutting tools, as well as carbides, cermets and ceramics. Vitrified CBN wheels are more suited for ferrous metal applications like camshaft and crankshaft grinding in the automotive industry or tool and die machining.
A further advantage of vitrified wheels is the possibility of customization to suit a specific application. Consult CDT to learn what's possible.
CAUTIONS
Glass is brittle and so is a vitrified wheel. It will break down under high pressure. This also means the wheels need to be engineered for the application.
Because of the porous structure of the Vitrified wheels, it is important to adjust the corresponding grit size to match finish when comparing/converting from conventional abrasives or Resin and Metal Bond wheels.
THE HIGH VOLUME SOLUTION
When high material removal is needed and dimensional control is a concern a vitrified wheel should be the first choice. Its high stiffness and porous structure allow rapid grinding while minimizing deflection in the workpiece-machine-wheel system. Add in long life and the result is a wheel suited to the most challenging high volume applications.
What are Metal Bond Grinding Wheels and What Benefits Do They Offer?
Extensively used in manufacturing diamond grinding wheels, metal bonds are manufactured utilizing three different processes: cold press, semi hot press and hot press modes.
Extensively used in manufacturing diamond grinding wheels, metal bonds are manufactured utilizing three different processes: cold press, semi hot press and hot press modes.
Cold press mode involves pressing the transition layer (no diamonds) and the working layer (with diamonds) of selected diamond portions to forms that on the body of the grinding wheel. These segments are then allowed to interconnect with the grinding wheel's body via slots or teeth. Finally, cold press grinding wheels are placed into sintering furnaces where they are sintered without press.
The semi hot press mode improves on the cold press mode by complementing the sintering process. While grinding wheels are sintering in a furnace, applicable molds are applied and minimal to moderate pressure is added. However, any pressure applied is significantly lower than the amount of pressure applied in hot press mode.
Hot press mode directly sinters diamond particles in molds under preset pressure levels in induction units. Diamond segments are then affixed on the grinding wheel using high frequency laser welding, high frequency welding or mosaic methods of mechanical welding.
Metal bond grinding wheels are produced when powdered metals or compounds containing cubic boron nitride or diamond are sintered on the wheel, resulting in exceptionally strong tools that maintain shape during rigorous use. In addition, metal bonding extends the life of grinding wheels by reducing the need for repeated dressings and continues being productive longer than market-brand super abrasives.
Benefits of Using Metal Bond Grinding Wheels
Because metal bond grinding wheels are sintered with cobalt, copper, mill, silver or stanum powder, they work exceptionally well on a variety of surfaces (glass, refractories, ceramics, silicon, semi-conductors and quartz).
Whether used for tool cutting, glass grinding, ceramic grinding or form cutting, metal bond grinding wheels provide the longest, most superior quality of service before any type of maintenance is needed.
Metal bond offers the ability to perform outstanding interrupted cuts while retaining the tool's original dimensions even during the most energetic grinding actions, including centerless, cylindrical, creep feed, deburring and cutoff applications.
Although resin bonds are more commonly used than vitrified or electroplated bonds, these bonds do not offer the hardness or wheel retention properties exhibited by metal bond grinding wheels.
As one of the most frequently seen machines in manufacturing plants requiring grinding applications, centerless grinders especially benefit from metal bond grinding wheels because of the slow, precise pace of material removal method demanded of these machines. Additionally, super abrasive centerless grinders necessitate powerful wheels such as metal bond grinding wheels that can effectively make predetermined alterations to products while reducing quality control issues that may arise if lesser quality wheels are used.
Continental Diamond Tool Corporation has been producing Metal Bond products since it was founded in 1973. If you are looking for a custom metal bond wheel, contact our experienced team of product engineers today.
40 Percent Improvement for Carbide Grinding with CDT Wheels on a Studer CNC Grinder
Check out how our engineers were able to add value to carbide grinding using Studer CNC grinders with a custom vitrified grinding wheel by CDT.
“Continental Diamond Tool knows grinding wheels … give them a problem and they tackle it.”
Continental Diamond Tool recently had a customer looking to replace the grinding wheel on their Studer CNC grinder. They were searching for a modern solution that would be compatible with both their newer and older CNC grinder models. With this upgrade, they hoped to reduce their cycle times and increase utilization of their capital equipment.
CDT proposed a transition to a diamond wheel for carbide grinding, and it was determined that our newly formulated vitrified diamond grinding wheel would accomplish their goals in this circumstance. Our engineers customized the core material to improve vibration damping characteristics. We also dynamically balanced the wheel allowing for improved start-up and wheel performance.
After extensive testing of the grinding wheel on their new programmable, variable speed Studers, with the same parameters as the previous competitors wheel, they slowly increased feeds until they reached the optimized 40% cycle time reduction with great success.
With the older Studers, our team ran into a complication. Because those machines use a pulley driven system, the grinders did not have the desired 6500 SFPM for vitrified diamond included. When hurdles like this arise, we meet those challenges head on. The solution to purchase a new pulley size allowed the older Studers to achieve the optimal speed for 40% cycle time efficiencies.
Besides gaining efficiency, the new wheel has extended our customers profile and form capabilities, adding Straight 1A1, Anglehead 1E1, Slotting/Groove, Face 6A2, and ID 1A8 styles. With these new capabilities our customer has been able to increase their through-put by 40% or more.
Additionally, because their old Studers are performing like new with extended capabilities, the customer will be able to delay the replacement of these old CNC grinders. At $450,000 a machine, this is a significant benefit.
Our next project will extend rotary dressing capabilities to their old Studer CNC grinders. They currently off-line dress both their current grinding wheels every other day on these older machines. Their newer Studers have rotary dressers that eliminate off-line dressing. Once rotary dressing is implemented on all their machines, it will greatly reduce their maintenance downtime.
The results from this custom project have been impressive with added value in multiple steps of the process summarized below:
· Reduced cycle times more than 40%
· Increased through-put by more than 40%
· Increased utilization of capital equipment
· Opened the door for the elimination of off line dressing
At CDT, we value our relationship with loyal customers. One of the key aspects of working with them has been our ability to expedite orders when needed and improve product performance and ultimately add value to the bottom line. When we are familiar with a company's unique process, we can often compress our four week standard lead-times to deliver in as little as one week. We can also organize blanket orders with scheduled releases.
When we asked their CFO why they chose CDT for their grinding wheels, he said, "Continental Diamond Tool knows grinding wheels, and their team is always innovating. Give them a problem and they tackle it — with excellent service, quality, and follow through."
It was a pleasure working on this project, and we're always happy to be of service!
Preparing CBN Wheels for Use
Preparing CBN wheels for use requires a bit of effort up front, but will give you long-term benefits that are immeasurable.
Superabrasive grinding wheels, such as diamond and CBN wheels require a little work and effort to set up and make them ready for use. This involves three main steps mounting, preparing (truing) and dressing the wheel so that they work as they should and give you the best possible grind. All three steps are important, but none so much as truing your CBN wheel.
What is Truing?
Truing allows for the face of the CBN wheel to be presented to the work piece properly and give you the best possible performance. After all, a wheel that is untrued can provide a surface finish, stock and removal capability that is undesirable. If you go through the truing process, and choose the right options based on your particular device and the product you are working with, you will get the highest possible performance of your grinding wheel. Additionally, the wheel life will be greatly reduced costing you much more effort and cost in the long run.
The Truing Process
The truing process occurs after you have already hand mounted your CBN wheel to the minimum runout. There are a number of techniques you can utilize to obtain the maximum truing level. Two of the most common include:
1) Multiple point (14 - 40 mesh) or impregnated (40 - 100 mesh or finer) diamond-type dressing tools.
Offers 0005" infeed for each pass (.01MM)
Not recommended for single point & cluster diamond tools
Finer mesh diamond - This technique allows better initial work piece finish
2) Truing brake or motorized dresser
Coarse grit (ranging from J to M hardness)
Silicon carbide or aluminum oxide wheel
001” Infeed per pass (.025MM)
You will apply the truing device to the wheel until contact is made with the entire face of the CBN grinding wheel. Whenever it is possible, you want to use flood coolant as this will extend the life of the CBN wheel. Heavy-duty water-soluble oils will also help add life.
It is important to remember that a resin-bonded wheel is not necessarily ready to go after it has been trued. Properly dressing it is very important as well. If you do not work through all the steps of the process, you will not get the best possible results and you may find yourself changing your wheel again much sooner than you planned to in the future.
Taking the proper preparation steps with your CBN wheels is not necessarily the easiest part of the grinding process, but it can make a big difference in the effectiveness of your wheels as well as with helping them to do their job for a longer length of time. For most factory and workshop applications, it is worth the effort and cost up front. After all, a CBN wheel is one of the most important tools you use on a daily basis, so why not take the time with the process?
Tips To Solving Wheel-Related Grinding Problems
When there are problems with a ground surface finish, when productivity is low, or if costs are too high, the fault may lie with the grinding wheel. Changing the grit, wheel feeds and speeds, or coolant application may be the solution, depending on the precise nature of the problem.
Grinding problems show up in two ways: in the appearance of the workpiece and as cost or productivity issues. After verifying that the grinding machine isn’t at fault, attention should turn to the grinding wheel.
Appearance problems divide into poor surface finish, chatter, and burning. Cost and productivity issues are short wheel life, slow cutting, and the wheel not cutting.
APPEARANCE ISSUES
Poor finish
Grinding is a multi-point cutting process, but down at the microscopic level it’s little different to a single point operation like turning. Viewed this way, it’s easy to see how surface finish is affected by the same factors: the more material removed by each grinding point, bigger the individual chips and the rougher the surface.
The solutions are:
Select a finer grit size
Reduce the relative speed of wheel and workpiece
If grinding wet, it might also be that the coolant is not removing chips from the workpiece/wheel interface. It's also possible that the wheel is being dressed excessively, creating grinding points standing too proud of the wheel surface.
Chatter
Recognizable by a distinct pattern on the workpiece, and often audible, chatter has many causes. If initiated by a vibration in the machine – possibly some kind of resonance – the solution is to vary the grinding speed. Try going 10% faster or slower to remove the forcing excitation.
Wheel-induced chatter occurs when an out-of-true grinding wheel acts as an excitation source. In this case the wheel should be trued carefully. Also check it isn’t slipping on its mount. A detailed discussion of chatter is available at the Abrasive Engineering Society website.
Burning
Machinists use this term to mean thermal damage. It can range from cosmetic discoloration to changes in workpiece hardness and possibly the creation of distortion-inducing internal tensile stresses. Burning is far more common when grinding dry, although can still be experienced in wet grinding if there isn't enough coolant flow to carry away the heat. “Burn Awareness”, originally published in Cutting Tool Engineering, December 2000, provides more information.
Burning can occur if the wheel is glazed or loaded, so there is more rubbing and hence more friction, by trying to push the wheel through the workpiece too quickly, or by using a wheel that’s too durable.
Solutions are:
Dress the wheel with a dressing stick
Reduce the feed rate or the relative velocity between wheel and workpiece.
COST AND PRODUCTIVITY ISSUES
Wheel life too short
This can be caused by:
Insufficient coolant
Dressing too often
A wheel that's either too hard or too soft for the workpiece (so it loads up or wears away too quickly)
Wheel speed too low
Slow cutting
Usually caused by feeds and/or wheel speeds that are too low, the solution is to grind as fast as possible without burning.
Wheel not cutting
This happens when the wheel is glazed by truing. The solution is to dress the wheel lightly until the grit opens up.
THINK LOGICALLY
Most grinding problems can be solved by relating the fault back to basic principles. Picture material being removed by individual cutting points and a solution usually emerges.
How to Keep your Grinding Wheels Performing Every Time
Properly dressing your grinding wheels is an important step in helping them to work as they should.
Grinding wheels are a very important tool in many factory and shop situations. They can be used for any number of projects; because of this, they tend to become something that are taken for granted. You expect that when you go to the shop that the grinding wheels will work as intended.
However, there are a number of issues that can occur that prevent the wheels from grinding as they should. While some of these problems are big and require a replacement wheel, others are reparable. One of the most common problems is a wheel that is not providing as heavy of a grind as it should.
Commonly, new wheels may not have the same grinding power as wheels that have been “broken in” and used for some time. As such, it is important to understand the concept of dressing grinding wheels.
To get the best cutting performance from your grinding wheel it is important that the wheel have a sharp abrasive grain with cutting points that are well exposed and able to connect with the piece with which you are working.
The ultra-hard abrasive crystals often used in grinding wheels will remain sharp simply through the process of grinding itself. Essentially, the wheels will slowly expose further crystals and you will not need to continuously dress the wheel. This is one of the biggest benefits of these superabrasive grinding wheels.
However, one problem is when you are working with new wheels. Usually these wheels have a smoother grinding surface. This occurs because the crystals and the surrounding bond are still flush to the edge of the cutting surface. If you try to operate a wheel without first dressing it, you will find performance is lacking. This is called “loading.” A wheel that is loaded will have poor cutting performance and may even cause some burning to your work piece.
This is where dressers come in. Diamond dressing sticks or rotary diamond dressers (also known as diamond rolls) are supplementary tools that keep your wheel operating at peak performance.
Dressing your superabrasive grinding wheel enhances grain exposure and brushes away some of the bond so that the wheel will work as it should. However, it is important that you choose the right type of dressing for your wheel to get the performance you desire. Some of the qualities you should consider with your grinding wheel dressing include:
Hand held aluminum oxide or silicon carbide stick
Soft (G, H hardness)
Fine grit (200-400 mesh)
Another strategy is to lower the RPM of the spindle, at least temporarily. This will open the wheel quicker and expose the abrasive surface for a more open surface. Then, you can increase the RPM in the future when the abrasive surface has been properly dressed and exposed.
While dressing your wheel is often something that only occurs when the wheel is new, it is possible to experience burning and poor cutting even on an older wheel. If this happens, you can simply use the same stick and technique to re-expose the surface and reopen the wheel.
As you can see, there is a lot to think about when you are first setting up your grinding wheel or if you are working with a wheel that does not seem to offer the best performance. It is possible to get the performance you desire it just takes a little work and effort up front!
Hardness Matters. Best Materials for Drilling, Cutting and Grinding
Superabrasives are split into two categories: CBN for use with ferrous material, and diamond for almost all other materials. At only half the hardness of a natural diamond, CBN is the only other material besides synthetic diamonds that is hard enough to be considered a superabrasive.
A natural diamond is the hardest material on the Knoop Hardness Scale, as is well known. It is considered a superabrasive, and has a long list of things it is regularly used to drill or otherwise shape. Glass, plastic, cemented carbide, ceramics, fiberglass, electronic components and materials, and titanium alloys are just a sampling of the things a diamond can cut. This is true whether the diamond is natural, manmade, or polysrystalline, as all three of these diamond types top the Knoop Hardness Scale. This means that even non-natural diamonds are harder than anything else except a natural one.
Right after the diamonds comes the Cubic Boron Nitride (CBN). This measures at nearly 5,000 on the Knoop Hardness Scale (compared to the 10,000 for a natural diamond, for comparison). At only half the hardness of a natural diamond, CBN is the only other material besides synthetic diamonds that is hard enough to be considered a superabrasive.
Everything else on the Knoop Hardness Scale is less hard than natural and synthetic diamonds and CBN. This means these things can cut through nearly everything else. The vast difference between the hardness of a natural diamond and the hardness of CBN shows just how relatively soft everything else on earth is in comparison to a natural diamond. If it wasn't for CBN, there would be no other super abrasive at all.
Superabrasives are split into two categories: CBN for use with ferrous material, and diamond for almost all other materials. Conventional Abrasive grinding wheels are also split into the same two categories. Silicon Carbide is known to chemically interact with ferrous materials making it less than ideal for such materials. Aluminum Oxide, despite being somewhat softer than Silicon Carbide, does not have chemical reactivity with Ferrous materials, and is therefore a better choice for these materials.
So the question becomes which is the better choice; conventional abrasive or superabrasive grinding products for your application? In general, superabrasive grinding wheels can provide 100-300 times the grinding wheel life when compared with conventional abrasives due to their higher hardness values, while only costing 10-30 times the wheel price. However, significant other variables have to be considered when determining which type of grinding wheel is best for your application. These include the machine/grinder, dressing of the grinding wheels, work piece material properties, coolant type and delivery, etc…..
Please contact one our experienced engineers to help evaluate your grinding process today to see if superabrasives are the ideal solution for your grinding application.
CDT Now Offering Same Day Shipping on Select High Performance Grinding Wheels for the Cutting Tool Industry
If you are in the cutting tool industry and are interested in gaining a competitive edge with CDT's GL™ Series grinding wheels, contact our knowledgeable team of service techs today.
Last year Continental Diamond Tool Corporation introduced its Resin Hybrid Bond — custom formulated grinding wheels with a winning combination of durability, finish, and performance.
The Resin Hybrid Series is the superior option of superabrasive diamond and CBN grinding wheels for the cutting tool industry. Using the latest Advanced Bond technology, competitive trials have proven that the bond grinds up to four times quicker without losing the wheel edge. Flute from solid, regrind, gash and end work, and relief.
Resin Hybrid Bond is not your standard “one size fits all.” This bond is tailored to specific grinding applications, providing the highest quality tool with the most efficient performance. Its unique properties offer key advantages to the CNC Tool and Cutter Grinder in many ways:
Free cutting action with superior form retention and surface finish
Self sharpening bond lengthens wheel life and dressing interval
High material removal rate with high temperature stability
Maximum heat dissipation with low and constant power consumption
Optimal wheel profile stability lowers costs due to wear
Previously cutting tool manufacturers had to commission custom-designed Resin Hybrid wheels to get all these benefits. Now CDT is stocking our most popular shapes and sizes specifically tailored to cutting tool manufacturing at affordable, off-the-shelf prices. CDT wheels are compatible with most of the cutting tool industry's leading CNC Tool and Cutter Grinder machinery.
If you are in the cutting tool industry and are interested in gaining a competitive edge with CDT's Resin Hybrid Series grinding wheels, contact our knowledgeable team of service techs today. Tell us your requirements and we will check our inventory for availability or provide you a custom quote. Wheels in stock ship the same day!
Or call 800-443-6629.
Care and Maintenance of Diamond Wheels
A few simple steps to care for and maintain your diamond wheels will allow you to get the performance and durability you expect from them.
Diamond wheels provide the maximum performance and high-speed cutting on demanding materials. Proper care and maintenance will ensure that the wheel gives the superior results for the maximum time. The steps are not difficult and well worth the effort.
Installation
Make sure that spindles, back plates and flanges are always clean before installing a new wheel. Use a dial indicator to check that the rotation of the wheel is within 0.0005 inch, 12.7 microns, of true. Tighten the flanges once the wheel is true and double-check tightness before use.
Diamond cutting wheels should only be used to make straight cuts. Twisting or jamming the wheel can cause fatigue and segment loss. Excess pressure should not be applied when making cuts.
When performing any cutting or grinding process, all work materials require firm support. Excess overhang should be avoided; even slight tilting can create an angled cut.
Feed and grinding speed
Material must be fed into the wheel at the appropriate speed. A feed rate that is too fast will cause chatter and vibration. This will result in a poor cut and possibly damage the cutting edge of the wheel.
Diamond wheels work best at speeds between 5,000 to 6,000 surface feet per minute. Running at lower speeds can lead to glazing.
Dressing
Using the wrong cutting wheel, one with a bond that is too hard for the working material, will create glazing. The easiest way to avoid this is using a blade that is matched to the material. Dressing the blade is a maintenance technique, but dressing does slow down production and reduce the life of the wheel.
Dressing a diamond wheel cleans the build up of debris from cutting operations that block the abrasive surface. The resurfacing restores the sharp abrasive edges of the diamond coating. A dressing stick, normally aluminum oxide or silicone carbide, is used to cut through or remove the debris and expose new diamond material.
Make an arrow mark on the wheel showing the rotation direction the first time and always dress the wheel with it spinning in the same direction. Dressing a wheel in both directions will destroy it.
Dressing is accomplished by simply making a straight cut through the dressing stick or bar. Cut off a thin section per pass. Only one or two cuts through the stick should be required.
If a dressing stick is not available, a section of asphalt can be used. Make a few cuts into the asphalt and the blade should be clean.
Overheating
Coolant should be used for maximum results. The coolant needs to spray to contact where the cutting wheel and material meet. A weak soluble oil solution may be used to reduce corrosion.
If dark streaks form along the sides of the cutting edge, the wheel is being overheated. Excess heat can cause the wheel to break apart. If dry cutting is being performed, allow the wheel to cool for about 10 seconds for every 30 seconds of cutting operation.
Use the right grade wheel, designed for the material to prevent injuries from reactive force or throw back. Never use a wheel that shows signs of fracture, fatigue or broken segments.
Industrial Diamond Facts
Find out about industrial diamond shapes, quality and sizes as well how they are used in industrial settings.
Diamonds are used for many industrial settings due to the fact that they are the hardest substance known. Diamonds are a crystalline form of carbon, capable of assuming a variety of shapes, sizes and qualities and are used for grinding, cutting, drilling, polishing and as an abrasive in industrial applications. Although diamonds have a high cost initially, they often cut down on the total labor cost of industrial projects due their efficiency for cutting and grinding.
SIZE AND QUALITY
Diamonds used for industrial purposes vary widely in cost which is based on two factors--size (determined by carat weight) and quality. One carat is equal to 200 milligrams of 1/5 of a gram. Each gram represents five carats. A carat is further defined as having 100 points (the smallest unit of measure in the carat system). Therefore .10 equals 1/10 of a carat, 1.5 equals 1 1/2 carats.
Diamond quality is difficult to assess, determined by highly technical factors representing the considered judgment of a trained diamond expert. For industrial purposes, the best way to judge diamond quality is by performance. The better quality a diamond is, the more structurally sound each individual crystal will be. High-quality diamonds have better shape definition, allowing for longer service and quality dressing action desired on the grinding wheel.
SHAPES
Industrial diamonds can be shaped in a variety of ways as shown below:
A Concise Guide to Single Point Diamond Dressers
Learn about diamond classifications and 10 tips for using single point diamond dressers.
Problematic grinding performance typically arises as a consequence of improper dressing. Choosing the correct diamond quality classifications greatly improves the expected quality of finished products. Moreover, the number of settable points will contribute heavily to acceptable dressing standards.
Classifications of Diamond Qualities
Grade A quality diamonds provide four+ settable points--smooth-surfaced octahedron or dodecahedron.
Grade B quality diamonds provides three+ settable points--possibility of inclusions, although they do not disturb the diamond's integrity.
Grade C quality--two+ settable points exhibiting blockish structure with superficial irregularities. This grade is the most common grade used in tool rooms.
Grade D quality--less than two settable points. Grade D's may have defects around less defined points.
Grade E quality--one settable point, "utility" grade diamond typically presenting cracks and other flaws.
Grade U quality--one settable point, "utility" grade cube-shaped diamond with an opaque surface
10 Tips For Using Single Point Diamond Dressers
1. Extend the life of a single point diamond dresser by inclining the tool at a 10 to 15 degree angle to the wheel radius. Point the tool in the rotation direction of the grinding wheel to maintain a consistently sharp point.
2. When dressing with Polycrystalline (PCD), grit, diamond single points or arbitrary stone tools, the infeed has to be .001 since a diamond dressing tool inevitably pulverizes the vitrified bond. Anything higher than .001 will cause cracking into the wheel--as much as .009 deep--that forces the bond to degenerate. In addition, gullets develop that produce loading by catching chips and overheating the wheel. Consequences of excessive infeed are chatter, bounce, bad finish and burn.
3. Sharply-tipped, crystal octahedrons should be utilized for straight dressings. For 46 grit and 60 grit wheels, crystal octahedrons shaped in a gothic style work well. Points associated with crystal octahedrons stay sharp if you turn the tool six to 12 indexes every revolution, or as necessary.
4. Make sure to use enough coolant to moderate dressing temperature, otherwise overheating occurs which may chemically transforms diamond into graphite. Diamonds will also suffer cracking if subjected to large temperature gradients.
5. The objective of dressing is to generate and expose novel, superficial cutting edges on the wheel. Single point diamond dressers achieve this objective by shattering existing gravelly grains and facilitating the emergence of desired abrasive particles. Dressing increases in-feed as well as feed and must be performed regularly to maintain optimal grain protrusion and grain edge sharpness.
6. Always begin dressing at the center of the wheel, which is the biggest diameter. Starting a dressing procedure at a wheel's side will probably result in shattering or even destroying the highest quality diamonds.
7. To prevent wheel taper, place the single point diamond dress as close as possible to the grinding area.
8. Grinding wheel grain sizes are contingent on longitudinal feeds, which significantly influences the structure of the surface of a grinding wheel. Additionally, reduced feed rates will predictably provide finer, more desirable surfaces.
9. Rotate the dresser 20 to 40 degrees in the shank if a flat appears on the diamond so that the dresser maintains an optimally conical point.
10. Avoid letting the diamond erode until the shank is visible. Doing so could allow the stone to dislodge or fall out.